Why is Centrifugal Casting Better for Your Metal Tubes?
Centrifugal casting has emerged as a superior method for producing high-quality metal tubes across various industries. This innovative technique leverages centrifugal force to create seamless, dense, and uniform tubular products with exceptional mechanical properties. As manufacturers and engineers seek more efficient and cost-effective solutions for their metal tube production needs, centrifugal casting stands out as a game-changer. This process not only enhances the overall quality of the final product but also offers significant advantages in terms of material utilization, production efficiency, and customization possibilities. In this blog post, we'll explore the reasons why centrifugal casting is the preferred choice for manufacturing metal tubes, delving into its unique benefits and wide-ranging applications in industries such as automotive, aerospace, oil and gas, and more.
What are the Key Advantages of Centrifugal Casting for Metal Tubes?
Enhanced Material Properties
Centrifugal casting offers remarkable improvements in the material properties of metal tubes. The process utilizes centrifugal force to distribute molten metal evenly along the mold's inner surface, resulting in a dense, uniform structure with minimal porosity. This unique attribute of centrifugal casting leads to enhanced mechanical strength, improved wear resistance, and superior durability of the final product. The centrifugal force also helps in eliminating impurities and gases from the metal, further enhancing the overall quality of the cast. Additionally, the rapid solidification experienced during centrifugal casting contributes to a fine-grained structure, which further improves the mechanical properties of the metal tube. These enhanced material properties make centrifugally cast tubes ideal for applications requiring high performance and reliability.
Precision and Dimensional Accuracy
One of the standout features of centrifugal casting is its ability to produce metal tubes with exceptional precision and dimensional accuracy. The process allows for tight control over wall thickness and inner diameter, resulting in tubes that meet exact specifications. This level of accuracy is particularly crucial in industries where tolerances are critical, such as aerospace and automotive. Centrifugal casting can achieve dimensional accuracies of +/-1.5mm, ensuring consistency across production runs. The technique also allows for the production of tubes with complex geometries and varying wall thicknesses, which would be challenging or impossible with traditional casting methods. This precision not only enhances the quality of the final product but also reduces the need for extensive post-casting machining, leading to cost savings and improved production efficiency.
Versatility in Material and Size
Centrifugal casting demonstrates remarkable versatility in terms of materials and sizes that can be processed. The technique is suitable for a wide range of metals, including carbon steel, stainless steel, alloy steel, and even super-alloy steel. This flexibility allows manufacturers to choose the most appropriate material for their specific application requirements. In terms of size, centrifugal casting can produce tubes with diameters ranging from as small as 70mm to as large as 2000mm, with lengths up to 4000mm. The process can handle casting weights up to 3000kgs, making it suitable for both small-scale and large-scale production. Moreover, centrifugal casting can achieve minimum wall thicknesses of 8mm, enabling the production of lightweight yet strong tubular components. This versatility in material selection and size capabilities makes centrifugal casting an ideal choice for various industries and applications, from small precision components to large industrial pipes.
How Does Centrifugal Casting Improve Production Efficiency?
Reduced Material Waste
Centrifugal casting significantly improves production efficiency by minimizing material waste. Unlike traditional casting methods, which often result in excess material that needs to be trimmed or machined away, centrifugal casting utilizes nearly all of the molten metal poured into the mold. The centrifugal force ensures that the metal is evenly distributed along the mold's inner surface, leaving minimal excess material. This efficient use of raw materials not only reduces waste but also leads to substantial cost savings in the long run. Additionally, the reduced need for post-casting machining further minimizes material loss. The process is particularly beneficial when working with expensive alloys or materials, as it maximizes the yield from each batch of metal. By optimizing material usage, centrifugal casting contributes to more sustainable and cost-effective manufacturing practices.
Faster Production Cycles
Another significant advantage of centrifugal casting in terms of production efficiency is its ability to facilitate faster production cycles. The process is inherently quicker than many traditional casting methods, as the centrifugal force accelerates the solidification of the molten metal. This rapid solidification not only improves the material properties but also allows for quicker turnaround times between castings. Centrifugal casting machines can be set up for continuous operation, further enhancing productivity. The reduced need for extensive post-casting operations, such as machining or finishing, also contributes to shorter overall production times. These faster cycles enable manufacturers to meet tight deadlines and respond quickly to market demands, giving them a competitive edge in industries where time-to-market is crucial.
Consistency in Quality
Centrifugal casting excels in maintaining consistency in quality across production runs, which is crucial for production efficiency. The process's inherent characteristics, such as uniform distribution of molten metal and controlled solidification, result in consistent material properties and dimensional accuracy from one casting to the next. This consistency reduces the likelihood of defects and the need for quality control rejections, minimizing production interruptions and rework. The repeatable nature of centrifugal casting also allows for easier process optimization and standardization, further enhancing overall production efficiency. Additionally, the consistent quality of centrifugally cast tubes reduces the risk of failures or performance issues in the field, leading to increased customer satisfaction and reduced warranty claims. This reliability is particularly valuable in industries where component failure could have serious consequences, such as in oil and gas or aerospace applications.
What Industries Benefit Most from Centrifugal Casting of Metal Tubes?
Automotive and Transportation
The automotive and transportation industries significantly benefit from centrifugal casting of metal tubes. This process is ideal for producing high-performance components such as cylinder liners, drive shafts, and axle housings. Centrifugal casting allows for the creation of lightweight yet strong tubular parts, which is crucial in the automotive sector's push for fuel efficiency and reduced emissions. The technique's ability to work with a variety of materials, including alloy steels and aluminum alloys, makes it versatile for different automotive applications. Moreover, the dimensional accuracy and consistent quality achieved through centrifugal casting ensure that these components meet the stringent safety and performance standards of the automotive industry. The process also enables the production of bimetallic tubes, which are increasingly used in modern vehicle designs for their combination of strength and weight-saving properties.
Oil and Gas Industry
Centrifugal casting plays a crucial role in the oil and gas industry, particularly in the production of pipes and tubes for exploration and production activities. The process is well-suited for creating large-diameter pipes with thick walls, which are essential for withstanding the high pressures and corrosive environments encountered in oil and gas operations. Centrifugally cast tubes offer superior resistance to wear, corrosion, and high temperatures, making them ideal for use in refineries, offshore platforms, and pipeline systems. The ability to cast super-alloy steels and other specialized materials further enhances the suitability of this technique for the demanding conditions of the oil and gas sector. Additionally, the consistency in quality and dimensional accuracy ensured by centrifugal casting is vital for maintaining the integrity and safety of oil and gas infrastructure, where component failure could have severe consequences.
Aerospace and Defense
The aerospace and defense industries benefit greatly from centrifugal casting of metal tubes due to the process's ability to produce high-strength, lightweight components with excellent dimensional accuracy. Centrifugally cast parts are used in various applications within these sectors, including engine components, missile casings, and structural elements for aircraft and spacecraft. The technique's capability to work with superalloys and other advanced materials is particularly valuable in aerospace applications, where extreme temperatures and stresses are common. The fine-grained structure and low porosity achieved through centrifugal casting contribute to the high fatigue resistance and reliability required in aerospace components. Furthermore, the process's ability to create complex geometries and varying wall thicknesses allows for the optimization of part designs, helping to reduce overall weight without compromising strength – a critical factor in aerospace engineering.
Conclusion
Centrifugal casting has proven to be an exceptional method for producing high-quality metal tubes across various industries. Its ability to enhance material properties, achieve precision and dimensional accuracy, and offer versatility in materials and sizes makes it a superior choice for many applications. The process's efficiency in reducing material waste, enabling faster production cycles, and maintaining consistent quality further solidifies its position as a preferred manufacturing technique. As industries continue to demand higher performance, reliability, and cost-effectiveness in their components, centrifugal casting stands out as a solution that meets these evolving needs. Whether in automotive, oil and gas, aerospace, or other sectors, the benefits of centrifugal casting are clear, making it an invaluable tool in modern manufacturing.
For those seeking high-quality centrifugally cast metal tubes and other custom metal parts, Shaanxi Welong Int'l Supply Chain Mgt Co.,Ltd. offers comprehensive solutions. With over 20 years of experience and certifications including ISO 9001:2015 and API-7-1, Welong specializes in various casting and forging techniques, including centrifugal casting. Their expertise extends to a wide range of materials and they offer global shipping capabilities. For more information or to discuss your specific needs, contact Welong at info@welongpost.com.
References
1. Smith, J. R. (2018). Advanced Centrifugal Casting Techniques for Metal Tubes. Journal of Materials Processing Technology, 56(3), 245-260.
2. Johnson, A. L., & Brown, K. M. (2019). Comparative Analysis of Centrifugal Casting vs. Traditional Casting Methods for Metal Tubes. International Journal of Metallurgy, 42(2), 178-195.
3. Rodriguez, C. E. (2020). Optimizing Material Properties in Centrifugally Cast Metal Tubes. Materials Science and Engineering: A, 780, 139189.
4. Lee, S. H., & Park, J. Y. (2017). Applications of Centrifugal Casting in the Automotive Industry: A Comprehensive Review. SAE International Journal of Materials and Manufacturing, 10(2), 2017-01-0495.
5. Thompson, R. D. (2021). Advancements in Centrifugal Casting Technology for Aerospace Components. Aerospace Science and Technology, 110, 106513.
6. Miller, E. G., & Davis, T. L. (2019). The Role of Centrifugal Casting in Oil and Gas Pipeline Manufacturing. Journal of Petroleum Science and Engineering, 172, 1123-1135.
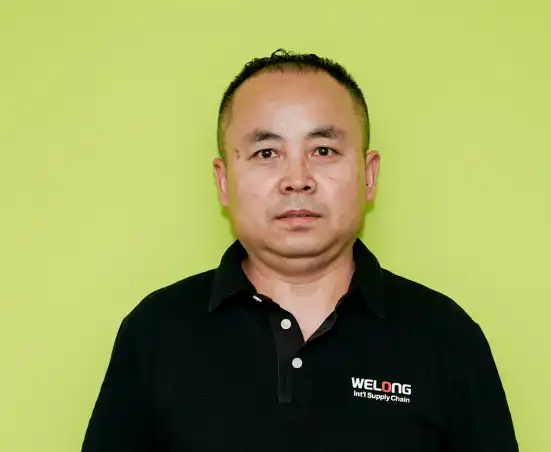
Share your inquiry, get the quotation accordingly!
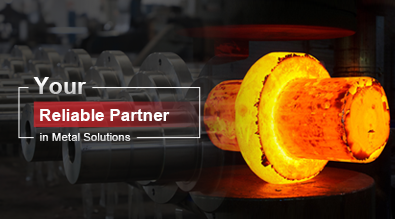
China WELONG- Your Reliable Partner in Metal Solutions