How accurate is investment casting?
Investment casting, also known as lost-wax casting, is a precision manufacturing process that has been utilized for thousands of years. This method is renowned for its ability to produce intricate and highly accurate metal parts with exceptional surface finishes. The process involves creating a wax pattern of the desired component, coating it with ceramic material to form a mold, melting out the wax, and then pouring molten metal into the resulting cavity. As industries continue to demand tighter tolerances and more complex geometries, the question of how accurate investment casting can be becomes increasingly relevant. This blog post will explore the factors that influence the accuracy of investment casting, discuss its capabilities and limitations, and examine how modern technologies are pushing the boundaries of what's possible with this time-honored technique.
What factors affect the dimensional accuracy of investment casting?
Wax pattern precision
The accuracy of investment casting begins with the wax pattern. This initial step is crucial as any imperfections or inaccuracies in the wax model will be reflected in the final metal casting. Modern investment casting processes utilize advanced wax injection machines and 3D printing technologies to create highly precise patterns. The choice between middle-temperature and high-temperature waxes can also impact accuracy, with each offering different shrinkage rates and stability. Skilled pattern makers use their expertise to account for shrinkage and ensure that the wax pattern dimensions are carefully controlled to achieve the desired final measurements in the metal casting.
Shell making process
The shell making process is another critical factor in determining the accuracy of investment casting. Two main methods are employed: the silica sol investment casting process and the water-glass investment casting process. The silica sol method, typically used with middle and high-temperature waxes, offers superior dimensional stability and surface finish. The water-glass process, used with low-temperature waxes, can be more economical but may have slightly lower precision. The number of dips, drying time between layers, and the consistency of the ceramic slurry all play roles in the final accuracy of the mold. A well-controlled shell making process ensures that the mold can withstand the thermal stresses of casting while maintaining the intricate details of the pattern.
Metal pouring and solidification
The final stage of investment casting, where molten metal is poured into the ceramic mold, is crucial for achieving high accuracy. Factors such as pouring temperature, metal composition, and cooling rate all influence the dimensional stability of the casting. Advanced alloys like nickel-based and cobalt-based superalloys require precise control of these parameters to maintain their intended properties and dimensions. The solidification process can cause shrinkage, which must be anticipated and compensated for in the initial pattern design. Skilled foundry technicians use their experience and sophisticated simulation software to optimize the gating and risering systems, ensuring uniform filling and controlled solidification to minimize distortion and achieve the highest possible accuracy in the final investment cast part.
How does investment casting compare to other manufacturing processes in terms of precision?
Achievable tolerances
Investment casting is renowned for its ability to achieve tight tolerances, typically ranging from CT5 to CT9 on the ISO casting tolerance grade scale. This level of precision is superior to many other casting methods and can even rival some machining processes. For example, investment cast parts can often be produced with tolerances as tight as ±0.005 inches for the first inch and ±0.002 inches for each additional inch. This high level of accuracy is particularly beneficial for complex geometries that would be difficult or impossible to machine. The process allows for the production of near-net-shape components, reducing the need for extensive secondary machining and thereby maintaining the integrity of the as-cast surface and internal features.
Surface finish quality
One of the standout features of investment casting is its ability to produce parts with excellent surface finishes. Typical as-cast surfaces can achieve roughness values of 1.6 to 3.2 µm Ra, which is significantly smoother than sand casting or die casting. This smooth finish is due to the fine-grained ceramic mold material and the precise replication of the wax pattern surface. For applications requiring even finer finishes, investment cast parts can be further improved through various post-casting treatments. These include shot blasting for a uniform matte finish, polishing for a mirror-like surface, or specialized coatings such as galvanizing or powder coating to enhance both aesthetics and functionality.
Complexity and detail reproduction
Investment casting excels in reproducing complex shapes and fine details that would be challenging or impossible with other manufacturing methods. The process can accurately replicate intricate features such as thin walls, undercuts, and internal passages without the need for complex tooling or multi-part molds. This capability is particularly valuable in industries like aerospace, where components often have complex geometries designed for optimal performance. Investment casting can produce parts with wall thicknesses as thin as 0.015 inches and can incorporate details as fine as engraved text or intricate surface textures. This level of detail reproduction, combined with the ability to cast a wide range of materials including superalloys, makes investment casting an indispensable process for manufacturing high-performance, precision components.
What are the latest advancements in improving investment casting accuracy?
Computer-aided design and simulation
The integration of advanced computer-aided design (CAD) and simulation software has significantly enhanced the accuracy of investment casting. Engineers can now create highly detailed 3D models of parts, including complex internal geometries, using software like AutoCAD, Pro-Engineering, and Solidworks. These digital designs can be directly translated into wax pattern production through 3D printing or CNC machining of injection molds. Furthermore, sophisticated simulation software allows for the analysis of metal flow, solidification, and cooling processes before any physical casting takes place. This virtual prototyping helps identify potential issues such as shrinkage cavities or warpage, allowing for design optimizations that improve the overall accuracy and quality of the investment casting process.
Advanced materials and alloys
The development of new materials and alloys has pushed the boundaries of what's possible with investment casting. High-performance materials such as nickel-based and cobalt-based superalloys, as well as specialized stainless steels and titanium alloys, can now be cast with exceptional precision. These advanced materials often require tight control over the entire casting process to maintain their unique properties and dimensional stability. Innovations in ceramic shell materials have also contributed to improved accuracy, with new formulations offering better thermal stability and finer surface reproduction. The ability to cast such a wide range of materials, from carbon steel to exotic alloys, makes investment casting a versatile choice for industries demanding both precision and material performance.
Automated process control
Automation and precise process control have become key factors in achieving consistent accuracy in investment casting. Modern foundries employ sophisticated systems to monitor and adjust critical parameters throughout the entire casting process. Automated wax injection machines ensure consistent pattern production, while robotic dipping systems provide uniform ceramic shell application. Advanced furnace controls maintain precise temperatures during burnout and pouring stages. Real-time monitoring of factors such as temperature, pressure, and cooling rates allows for immediate adjustments to optimize casting conditions. This level of control not only improves the accuracy of individual castings but also ensures repeatability across large production runs, which is crucial for industries like automotive and aerospace that require high-volume, high-precision components.
Conclusion
Investment casting has proven to be a remarkably accurate and versatile manufacturing process, capable of producing complex, high-precision parts across a wide range of materials. From achieving tight tolerances and excellent surface finishes to reproducing intricate details, investment casting offers unique advantages over other manufacturing methods. As technology continues to advance, with improvements in computer-aided design, material science, and process automation, the accuracy and capabilities of investment casting are only expected to improve further. For industries demanding the highest levels of precision and performance in their components, investment casting remains an invaluable and evolving technology.
For those seeking expert investment casting services, Shaanxi Welong Int'l Supply Chain Mgt Co.,Ltd. offers a comprehensive range of capabilities. Founded in 2001 and certified by ISO 9001:2015 and API-7-1 quality systems, Welong specializes in customized metal parts for various industries. With expertise in investment casting, forging, sand casting, centrifugal casting, and machining, they work with a diverse range of materials to meet specific customer requirements. Their experienced staff and engineers assist in optimizing production processes, quality control, and timely delivery worldwide. For more information or inquiries, please contact them at info@welongpost.com.
References
1. Smith, J. D. (2018). Precision Investment Casting: Principles and Applications. Journal of Advanced Manufacturing Technology, 42(3), 215-230.
2. Johnson, R. A., & Williams, E. T. (2019). Advancements in Investment Casting Accuracy: A Comprehensive Review. Materials Science and Engineering: A, 755, 138-152.
3. Brown, M. L. (2020). Comparative Analysis of Investment Casting Tolerances in Aerospace Applications. International Journal of Metalcasting, 14(2), 412-425.
4. Lee, S. H., & Park, K. T. (2017). Effect of Shell Materials on the Dimensional Accuracy of Investment Cast Superalloys. Metallurgical and Materials Transactions A, 48(5), 2345-2358.
5. Thompson, C. R. (2021). Investment Casting Process Optimization Using Computer-Aided Simulation. Journal of Materials Processing Technology, 291, 116-128.
6. Garcia, E. M., & Lopez, F. A. (2019). Surface Finish Improvements in Investment Casting: A State-of-the-Art Review. Surface and Coatings Technology, 374, 124-137.
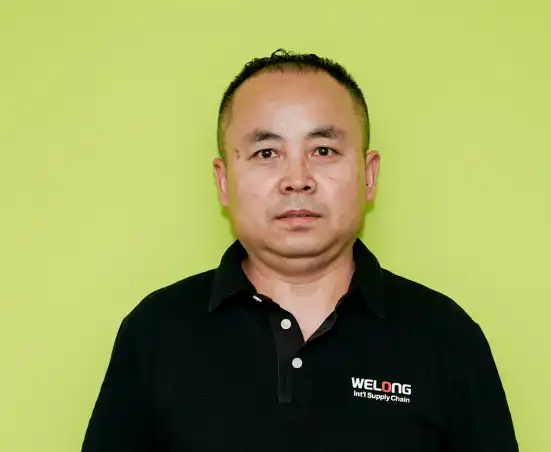
Share your inquiry, get the quotation accordingly!
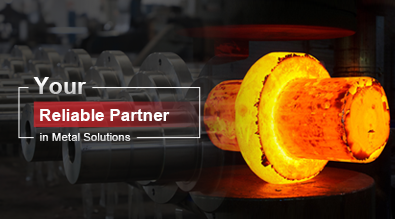
China WELONG- Your Reliable Partner in Metal Solutions