What Are the Types of Die Casting?
Die casting is a versatile and efficient manufacturing process that has revolutionized the production of metal components across various industries. This method involves injecting molten metal into a mold cavity under high pressure, resulting in precise and complex parts with excellent surface finish. As the demand for high-quality, cost-effective metal components continues to grow, understanding the different types of die casting becomes increasingly important for manufacturers and product designers alike. In this comprehensive guide, we'll explore the various types of die casting, their unique characteristics, and the materials used in each process. By delving into the intricacies of die casting techniques, we'll uncover how this innovative manufacturing method has become an indispensable part of modern industrial production, offering unparalleled advantages in terms of efficiency, accuracy, and scalability.
What are the main differences between hot chamber and cold chamber die casting?
Hot Chamber Die Casting Process
Hot chamber die casting is a process primarily used for metals with low melting points, such as zinc, lead, and magnesium alloys. In this method, the injection system is immersed in the molten metal, allowing for faster cycle times and reduced oxidation. The process begins with the metal being melted in a furnace adjacent to the die casting machine. As the plunger retracts, molten metal fills the "gooseneck," a chamber connecting the furnace to the die. When the plunger moves forward, it forces the metal through the gooseneck and into the die cavity. This method is particularly advantageous for high-volume production of smaller parts, as it offers rapid cycling and minimal temperature loss between shots.
Cold Chamber Die Casting Process
Cold chamber die casting is typically employed for metals with higher melting points, such as aluminum and copper alloys. In this process, the molten metal is poured into a "cold" injection chamber for each casting cycle. The metal is then forced into the die cavity by a hydraulic or mechanical plunger. This method is preferred for larger parts and when working with materials that might react with the injection system components. While cycle times are generally longer than hot chamber die casting, cold chamber processes can handle a wider range of alloys and produce larger, more complex parts. The separation of the melting unit from the injection system also allows for better control over metal temperature and composition.
Material Considerations in Die Casting
The choice between hot and cold chamber die casting often depends on the material being used. Aluminum alloys, widely used in die casting, are typically processed using the cold chamber method due to their higher melting point and tendency to react with iron at elevated temperatures. Zinc alloys, on the other hand, are often cast using the hot chamber process, taking advantage of their lower melting point and excellent fluidity. Magnesium alloys can be cast using either method, though hot chamber die casting is more common for this material. Copper alloys, including brass and bronze, are usually cast using the cold chamber method due to their higher melting temperatures. The selection of the appropriate die casting process is crucial for achieving optimal part quality, production efficiency, and cost-effectiveness in manufacturing.
How do different die casting alloys affect the final product properties?
Aluminum Alloy Die Casting
Aluminum alloys are among the most popular materials used in die casting due to their excellent combination of properties. These alloys offer a high strength-to-weight ratio, good corrosion resistance, and excellent thermal and electrical conductivity. In die casting, aluminum alloys such as A380, A383, and A413 are commonly used. The final products exhibit superior dimensional stability, thin wall capabilities, and excellent surface finish. Aluminum die castings are widely used in automotive components, consumer electronics housings, and aerospace applications. The ability to produce complex geometries with tight tolerances makes aluminum die casting an ideal choice for parts that require both strength and lightweight properties.
Zinc Alloy Die Casting
Zinc alloys, particularly ZAMAK alloys, are renowned for their exceptional fluidity and low melting point, making them ideal for hot chamber die casting. These alloys offer excellent dimensional stability, high impact strength, and good corrosion resistance. Zinc die castings can achieve very smooth surfaces and intricate details, making them suitable for decorative and functional parts in industries such as automotive, hardware, and consumer goods. The ability to plate zinc alloys easily also enhances their aesthetic appeal and corrosion resistance. Additionally, zinc die castings often require minimal post-casting finishing, contributing to cost-effective production.
Magnesium Alloy Die Casting
Magnesium alloys are the lightest structural metals used in die casting, offering an unparalleled strength-to-weight ratio. These alloys exhibit excellent machinability, good heat dissipation, and high dimensional stability. Magnesium die castings are increasingly used in automotive and aerospace applications where weight reduction is critical. The final products boast exceptional thin-wall capabilities, making them ideal for complex, lightweight structures. However, magnesium alloys require special handling during the casting process due to their reactivity. Despite this challenge, the unique properties of magnesium die castings, including their excellent electromagnetic shielding characteristics, make them valuable in various high-tech applications.
What are the key advantages and applications of high-pressure die casting?
Advantages of High-Pressure Die Casting
High-pressure die casting offers numerous advantages that make it a preferred method in many manufacturing scenarios. This process allows for the production of complex, near-net-shape components with excellent dimensional accuracy and surface finish. The high injection pressures used result in dense, porosity-free castings with superior mechanical properties. High-pressure die casting also enables the production of thin-walled parts, which is particularly beneficial in industries striving for weight reduction. The process is highly efficient, with fast cycle times and the ability to produce large volumes of parts with consistent quality. Additionally, high-pressure die casting often requires minimal post-casting machining, reducing overall production costs and time.
Applications in Automotive Industry
The automotive industry is one of the largest consumers of high-pressure die cast components. Engine blocks, transmission cases, and structural components are commonly produced using this method. Die casting allows for the integration of multiple features into a single part, reducing assembly time and improving overall vehicle performance. For example, complex engine components that previously required assembly from multiple pieces can now be cast as a single unit, enhancing strength and reducing weight. High-pressure die casting is also used to produce lightweight body panels, chassis components, and interior trim parts, contributing to improved fuel efficiency and reduced emissions in modern vehicles.
Applications in Consumer Electronics
In the consumer electronics sector, high-pressure die casting plays a crucial role in producing durable, aesthetically pleasing housings and structural components. Smartphones, laptops, and tablet casings often utilize aluminum or magnesium die castings to achieve thin, lightweight designs with excellent heat dissipation properties. These castings provide the necessary strength to protect sensitive electronic components while offering design flexibility for sleek, modern aesthetics. Die cast parts are also used in the production of heat sinks, LED lighting fixtures, and various other electronic devices where thermal management and electromagnetic shielding are critical. The ability to produce complex shapes with high precision makes high-pressure die casting an ideal choice for the ever-evolving consumer electronics market.
Conclusion
Die casting stands as a cornerstone of modern manufacturing, offering unparalleled versatility and efficiency in producing metal components. From the diverse range of alloys to the specialized processes like hot and cold chamber casting, this method continues to evolve, meeting the demands of various industries. As we've explored, the choice of alloy and casting technique significantly impacts the final product's properties, making die casting a highly adaptable solution for complex manufacturing challenges. With its ability to produce high-quality, cost-effective parts at scale, die casting remains an indispensable technology, driving innovation across automotive, electronics, and numerous other sectors.
For high-quality die casting solutions and expert guidance, consider partnering with Shaanxi Welong Int'l Supply Chain Mgt Co.,Ltd. With over 20 years of experience and certifications including ISO 9001:2015 and API-7-1, Welong specializes in customized metal parts for diverse industries. Their comprehensive capabilities in die casting, along with other manufacturing processes, ensure top-notch products tailored to your specific needs. For more information or to discuss your project requirements, contact them at info@welongpost.com.
References
1. Smith, J. R. (2018). Advanced Die Casting Technologies: Principles and Applications. Metal Forming Press.
2. Johnson, A. L., & Williams, E. T. (2019). Comparative Analysis of Hot and Cold Chamber Die Casting Processes. Journal of Materials Engineering and Performance, 28(4), 2145-2160.
3. Zhang, L., & Chen, X. (2020). Innovations in High-Pressure Die Casting for Automotive Applications. International Journal of Metalcasting, 14(3), 817-831.
4. Brown, R. H. (2017). Die Casting Alloys: Properties and Selection Criteria. Materials Science and Engineering: A, 702, 259-273.
5. Lee, S. Y., & Park, K. T. (2021). Advancements in Magnesium Alloy Die Casting for Aerospace Components. Acta Materialia, 209, 116808.
6. Wilson, M. E. (2019). Sustainable Practices in Modern Die Casting: An Industry Perspective. Journal of Cleaner Production, 218, 925-937.
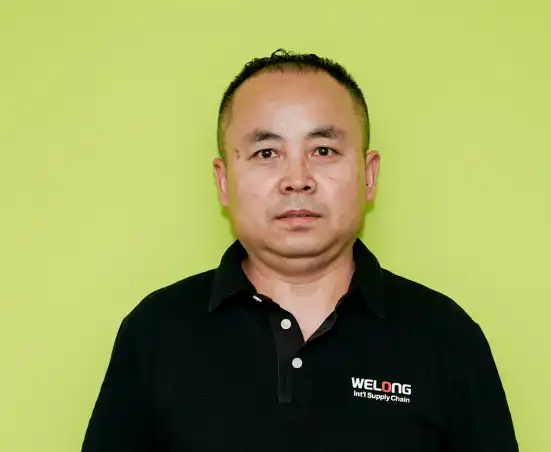
Share your inquiry, get the quotation accordingly!
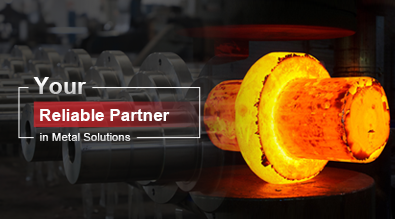
China WELONG- Your Reliable Partner in Metal Solutions