What's the Difference Between Gravity Cast and Low Pressure Cast?
When it comes to metal casting processes, two popular methods stand out: gravity casting and low pressure casting. Both techniques are widely used in manufacturing various components, but they differ significantly in their approach and outcomes. Gravity casting, as the name suggests, relies on the natural force of gravity to fill molds with molten metal, resulting in a simple yet effective process. On the other hand, low pressure casting utilizes controlled pressure to force molten metal into molds, offering unique advantages in terms of precision and efficiency. Understanding the distinctions between these two methods is crucial for manufacturers and engineers to make informed decisions about which process best suits their specific needs. In this blog, we'll delve into the intricacies of gravity casting and low pressure casting, exploring their characteristics, benefits, and applications to help you grasp the fundamental differences between these two important casting techniques.
What are the key advantages of gravity casting over other methods?
Cost-effectiveness of gravity casting
Gravity casting offers significant cost advantages compared to other casting methods. The process requires minimal equipment and setup, making it an economical choice for many manufacturers. Gravity casting utilizes simple molds and relies on the natural force of gravity to fill them, eliminating the need for complex machinery or pressurized systems. This simplicity translates to lower initial investment costs and reduced maintenance expenses. Additionally, gravity casting allows for the production of a wide range of part sizes, from small components weighing as little as 0.1 kg to larger parts up to 100 kg, providing versatility in manufacturing capabilities. The cost-effectiveness of gravity casting makes it an attractive option for producing aluminum zinc alloy and Si aluminum alloy parts, particularly when aiming for an annual output of around 200 tons.
Versatility in material selection
One of the key advantages of gravity casting is its versatility in material selection. This method is particularly well-suited for casting a variety of alloys, including aluminum zinc alloys and Si aluminum alloys. The gravity casting process allows for excellent control over the solidification of these materials, resulting in high-quality castings with desirable mechanical properties. This versatility extends to the production of complex geometries and thin-walled components, making gravity casting an ideal choice for a wide range of applications. Furthermore, the process accommodates various surface finishes, such as shot blasting, polishing, powder coating, and painting, enhancing the aesthetic and functional qualities of the final products.
Reduced porosity and improved mechanical properties
Gravity casting offers significant benefits in terms of reduced porosity and improved mechanical properties of the final castings. The natural flow of molten metal under gravity helps to minimize air entrapment and gas porosity, resulting in denser and more structurally sound components. This reduction in porosity leads to enhanced mechanical properties, including improved strength, ductility, and fatigue resistance. For aluminum zinc alloy and Si aluminum alloy parts, gravity casting can produce castings with excellent dimensional accuracy and surface finish. The process allows for controlled solidification, which contributes to the formation of fine-grained structures and uniform distribution of alloying elements, further enhancing the mechanical properties of the cast components.
How does the low pressure casting process differ from gravity casting?
Pressure application in low pressure casting
The primary difference between low pressure casting and gravity casting lies in the application of pressure during the mold filling process. In low pressure casting, a controlled pressure is applied to force the molten metal into the mold cavity, typically using compressed air or inert gas. This pressure, usually ranging from 0.3 to 1.5 bar, is maintained throughout the solidification process. In contrast, gravity casting relies solely on the weight of the molten metal to fill the mold. The pressure application in low pressure casting offers several advantages, including improved mold filling, especially for complex geometries and thin-walled sections. This pressure-assisted process can be particularly beneficial when casting aluminum zinc alloys and Si aluminum alloys, as it helps to overcome the limitations of gravity casting in certain challenging designs.
Mold design and orientation
Low pressure casting and gravity casting differ significantly in terms of mold design and orientation. In gravity casting, the mold is typically oriented vertically, with the sprue and gating system designed to allow the molten metal to flow downward under the force of gravity. This vertical orientation can sometimes lead to challenges in filling thin sections or intricate details at the top of the casting. Low pressure casting, on the other hand, often utilizes a more flexible mold orientation. The molds can be positioned horizontally or at various angles, as the pressure applied to the molten metal ensures complete filling regardless of orientation. This flexibility in mold design allows for more complex part geometries and improved consistency in wall thickness, particularly beneficial for aluminum zinc alloy and Si aluminum alloy components weighing between 0.1 and 100 kg.
Solidification control and cooling rate
The control over solidification and cooling rate is another area where low pressure casting differs from gravity casting. In gravity casting, the solidification process is primarily influenced by the natural heat transfer from the molten metal to the mold and surrounding environment. While this can be adequate for many applications, it may lead to challenges in controlling the solidification of complex geometries or large castings. Low pressure casting offers enhanced control over the solidification process through the maintained pressure and the ability to manipulate the pressure during cooling. This control allows for more uniform solidification, reduced shrinkage porosity, and improved mechanical properties in the final castings. For aluminum zinc alloy and Si aluminum alloy parts, this enhanced solidification control can result in finer grain structures and more consistent properties across different sections of the casting, contributing to the overall quality and performance of the components.
What are the specific applications where gravity casting excels?
Automotive components manufacturing
Gravity casting excels in the production of various automotive components, making it a preferred choice for many manufacturers in the industry. The process is particularly well-suited for casting engine blocks, cylinder heads, transmission housings, and other structural parts that require good mechanical properties and dimensional accuracy. Gravity casting's ability to produce components weighing between 0.1 and 100 kg makes it versatile enough to handle a wide range of automotive parts. The use of aluminum zinc alloys and Si aluminum alloys in gravity casting allows for the production of lightweight yet strong components, contributing to improved fuel efficiency and performance in vehicles. Additionally, the surface finish options available with gravity casting, such as shot blasting, polishing, powder coating, and painting, enable the production of aesthetically pleasing and corrosion-resistant automotive parts.
Aerospace industry applications
The aerospace industry greatly benefits from gravity casting, particularly in the production of critical components that require high strength-to-weight ratios and excellent mechanical properties. Gravity casting is often employed to manufacture aircraft engine parts, structural components, and landing gear elements. The process's ability to work with aluminum zinc alloys and Si aluminum alloys is particularly advantageous in aerospace applications, where weight reduction is crucial. Gravity casting allows for the production of complex geometries with thin walls and intricate internal features, which are often required in aerospace components. The controlled solidification in gravity casting results in fine-grained structures and uniform distribution of alloying elements, contributing to the enhanced fatigue resistance and reliability of the cast parts. With an annual output capacity of around 200 tons, gravity casting can meet the demanding production requirements of the aerospace industry while maintaining high quality standards.
Industrial machinery and equipment
Gravity casting finds extensive application in the manufacturing of industrial machinery and equipment components. The process is ideal for producing large, complex parts with high dimensional accuracy and excellent surface finish. Gravity casting is commonly used to manufacture pump housings, valve bodies, gearbox casings, and various other machinery components. The ability to cast parts weighing up to 100 kg makes gravity casting suitable for a wide range of industrial applications. The use of aluminum zinc alloys and Si aluminum alloys in gravity casting allows for the production of corrosion-resistant and durable components that can withstand harsh industrial environments. The versatility of gravity casting in terms of surface finishes, including shot blasting, polishing, powder coating, and painting, enables manufacturers to meet diverse aesthetic and functional requirements for industrial machinery parts. The cost-effectiveness and efficiency of gravity casting, coupled with its ability to produce high-quality components, make it an excellent choice for the industrial machinery and equipment sector.
Conclusion
In conclusion, both gravity casting and low pressure casting offer unique advantages in metal component manufacturing. Gravity casting excels in cost-effectiveness, versatility, and reduced porosity, making it ideal for automotive, aerospace, and industrial applications. Low pressure casting provides enhanced control over mold filling and solidification, allowing for more complex geometries and improved consistency. The choice between these methods depends on specific project requirements, including material selection, part complexity, and production volume. As technology advances, both techniques continue to evolve, offering manufacturers increasingly efficient and precise casting solutions for a wide range of industries.
For expert guidance on selecting the most suitable casting method for your project, contact Shaanxi Welong Int'l Supply Chain Mgt Co.,Ltd. With over 20 years of experience in metal parts manufacturing and a commitment to quality and innovation, Welong can help you achieve optimal results in your casting needs. Reach out to us at info@welongpost.com to learn more about our comprehensive range of casting services and how we can support your manufacturing goals.
References
1. Campbell, J. (2015). Complete Casting Handbook: Metal Casting Processes, Techniques and Design. Butterworth-Heinemann.
2. Zolotorevsky, V. S., Belov, N. A., & Glazoff, M. V. (2007). Casting Aluminum Alloys. Elsevier Science.
3. Brown, J. R. (1999). Foseco Non-Ferrous Foundryman's Handbook. Butterworth-Heinemann.
4. Kaufman, J. G., & Rooy, E. L. (2004). Aluminum Alloy Castings: Properties, Processes, and Applications. ASM International.
5. Mitra, R. (2016). Microstructure and Mechanical Behavior of Cast Magnesium Alloys. Springer International Publishing.
6. Street, A. (2017). The Diecasting Book. CreateSpace Independent Publishing Platform.
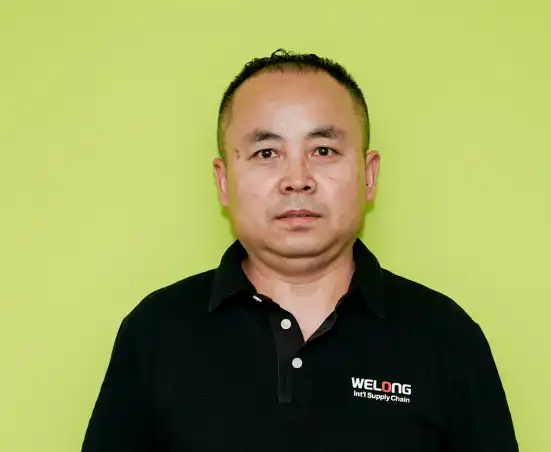
Share your inquiry, get the quotation accordingly!
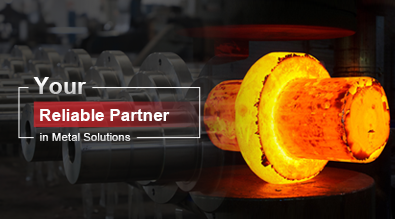
China WELONG- Your Reliable Partner in Metal Solutions