Sand Casting – Process, Sand Properties, Pros & Cons
Sand casting is a versatile and widely used manufacturing process that has been employed for centuries to create complex metal parts. This method involves pouring molten metal into a sand mold, allowing it to solidify, and then breaking away the sand to reveal the finished product. The process is known for its flexibility, cost-effectiveness, and ability to produce both small and large components. In this comprehensive exploration of sand casting, we will delve into the intricate details of the process, examine the crucial properties of sand used in mold-making, and weigh the advantages and disadvantages of this time-honored technique. Understanding the nuances of sand casting is essential for manufacturers, engineers, and anyone involved in the production of metal components, as it offers unique capabilities and challenges that can significantly impact product quality and production efficiency.
What are the key steps in the sand casting process?
Pattern Making
The sand casting process begins with the creation of a pattern, which is a replica of the desired final product. This pattern is typically made from wood, metal, or plastic and serves as the template for shaping the sand mold. In sand casting, the pattern is crucial as it determines the final shape and dimensions of the cast part. The pattern maker must consider factors such as shrinkage allowance, draft angles, and core prints to ensure the final cast product meets specifications. Advanced techniques in pattern making, such as 3D printing, have revolutionized this step, allowing for more complex and precise patterns to be created quickly and cost-effectively.
Mold Preparation
Once the pattern is ready, the next step in sand casting is mold preparation. This involves packing sand around the pattern in a two-part mold, typically consisting of a cope (top half) and drag (bottom half). The sand used in this process is specially formulated to maintain its shape and withstand the high temperatures of molten metal. Binders and additives are often mixed with the sand to improve its properties. The mold cavity is created by carefully removing the pattern, leaving an exact negative of the desired part. For more complex parts, cores made of sand or other materials may be inserted into the mold to create internal cavities or features that cannot be formed by the pattern alone.
Pouring and Solidification
The final major step in the sand casting process is pouring the molten metal into the prepared mold and allowing it to solidify. This stage requires precise control of metal temperature, pouring rate, and cooling conditions to ensure the quality of the final product. The molten metal is typically poured through a gating system that includes a pouring basin, sprue, runners, and ingates, designed to control the flow of metal and minimize turbulence. As the metal cools and solidifies, it takes on the shape of the mold cavity. The solidification process is critical, as it affects the microstructure and properties of the cast part. Controlled cooling rates can be employed to achieve desired material properties. Once the metal has fully solidified, the sand mold is broken away, and the cast part is removed for finishing operations.
How do sand properties affect the quality of sand casting?
Grain Size and Distribution
The grain size and distribution of sand used in sand casting play a crucial role in determining the quality of the final product. Finer sand grains generally produce smoother surface finishes on the cast parts but may reduce permeability, potentially leading to gas defects. Conversely, coarser sand grains improve permeability but can result in rougher surface finishes. A well-balanced distribution of grain sizes is often ideal, as it allows for good compaction while maintaining adequate permeability. The choice of grain size and distribution in sand casting depends on factors such as the complexity of the part, the metal being cast, and the desired surface finish. Advanced sand casting operations often use computer-controlled sand mixing systems to achieve optimal grain size distributions for specific applications.
Permeability and Strength
Permeability and strength are two critical properties of sand in the casting process. Permeability refers to the ability of the sand to allow gases to escape as molten metal is poured into the mold. Adequate permeability is essential to prevent gas-related defects such as porosity or blowholes in the cast part. The strength of the sand mold is equally important, as it must withstand the pressure of the molten metal without deforming or collapsing. Binders and additives are often used to enhance both permeability and strength. For instance, clay binders can increase the strength of green sand molds, while organic binders are commonly used in chemically bonded sand systems. Balancing these properties is a key challenge in sand casting, as increasing strength often comes at the cost of reduced permeability, and vice versa.
Thermal Properties
The thermal properties of sand, including its heat capacity and thermal conductivity, significantly influence the solidification process in sand casting. These properties affect how quickly heat is transferred from the molten metal to the mold and, consequently, the cooling rate of the cast part. Proper control of thermal properties is essential for achieving desired microstructures and mechanical properties in the final product. For example, rapid cooling can lead to finer grain structures and higher strength, while slower cooling may be preferred for improved ductility. Sand additives such as iron oxide or chromite sand can be used to modify the thermal properties of the mold. In some cases, chill blocks or cooling fins may be incorporated into the mold design to control local cooling rates. Understanding and manipulating the thermal properties of sand in casting is crucial for producing high-quality parts with consistent properties.
What are the advantages and limitations of sand casting compared to other casting methods?
Versatility and Cost-Effectiveness
Sand casting is renowned for its versatility and cost-effectiveness, making it a popular choice across various industries. One of the primary advantages of sand casting is its ability to produce parts of virtually any size, from small components weighing a few grams to massive castings weighing several tons. This flexibility is unmatched by many other casting processes. Additionally, sand casting can accommodate a wide range of metals and alloys, including iron, steel, aluminum, copper, and various alloys, offering broad material selection for different applications. The process is particularly cost-effective for low to medium production volumes, as the tooling costs are relatively low compared to other casting methods like die casting. The reusability of sand in the process further contributes to its cost-effectiveness. However, for very high volume production, other methods may become more economical due to their faster cycle times.
Surface Finish and Dimensional Accuracy
While sand casting offers many advantages, it does have limitations in terms of surface finish and dimensional accuracy compared to some other casting methods. The nature of the sand mold typically results in a rougher surface finish than processes like investment casting or die casting. This can necessitate additional finishing operations, increasing production time and cost. The dimensional accuracy of sand castings is generally lower than that of more precise methods, with typical tolerances ranging from CT8 to CT13 depending on whether the mold is made by machine or hand. This level of accuracy is sufficient for many applications but may not meet the requirements for parts with very tight tolerances. However, advancements in sand casting technology, such as the use of 3D printed sand molds and computer-controlled molding machines, are continually improving the achievable surface finish and dimensional accuracy in sand casting.
Production Speed and Complexity
Sand casting offers a balance between production speed and the ability to create complex geometries. While it may not be as fast as high-volume processes like die casting, sand casting can still achieve respectable production rates, with some facilities capable of producing hundreds of tons per month. The process is particularly well-suited for creating parts with intricate internal cavities or complex external features, which can be challenging or impossible to produce with other methods. The use of cores in sand casting allows for the creation of hollow sections and undercuts that would be difficult to achieve otherwise. However, there are limitations to the complexity of parts that can be produced, particularly in terms of very thin sections or extremely fine details. The production speed of sand casting can also be a limitation for very high volume requirements, where automated processes like die casting may be more suitable. Despite these constraints, the flexibility of sand casting in terms of part size, material options, and geometric complexity continues to make it a valuable manufacturing process across numerous industries.
Conclusion
Sand casting remains a cornerstone of modern manufacturing, offering a unique combination of versatility, cost-effectiveness, and the ability to produce complex parts in a wide range of sizes and materials. While it faces challenges in terms of surface finish and dimensional accuracy compared to some newer technologies, ongoing advancements continue to improve these aspects. The process's adaptability to various production volumes and its relatively low tooling costs make it an attractive option for many applications. As the industry evolves, sand casting is likely to remain a vital manufacturing method, particularly when balanced with other casting techniques to meet diverse production needs.
For expert sand casting services and a wide range of metal manufacturing solutions, consider Shaanxi Welong Int'l Supply Chain Mgt Co.,Ltd. With over 20 years of experience and certifications including ISO 9001:2015 and API-7-1, Welong specializes in customized metal parts for various industries. Their capabilities extend beyond sand casting to include forging, investment casting, centrifugal casting, and machining. With a global customer base and a commitment to quality and innovation, Welong is dedicated to helping customers succeed. For more information or inquiries, contact them at info@welongpost.com.
References
1. Brown, J.R. (2017). "Foseco Ferrous Foundryman's Handbook", Butterworth-Heinemann.
2. Campbell, J. (2015). "Complete Casting Handbook: Metal Casting Processes, Techniques and Design", Butterworth-Heinemann.
3. Beeley, P.R. (2001). "Foundry Technology", Butterworth-Heinemann.
4. Jain, P.L. (2003). "Principles of Foundry Technology", Tata McGraw-Hill Education.
5. American Foundry Society. (2019). "Casting Source Directory", AFS.
6. Groover, M.P. (2010). "Fundamentals of Modern Manufacturing: Materials, Processes, and Systems", John Wiley & Sons.
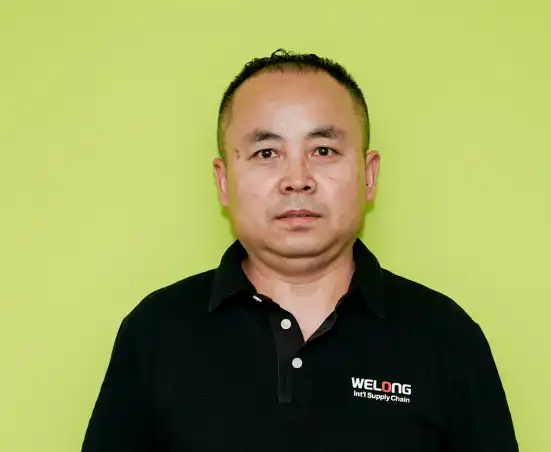
Share your inquiry, get the quotation accordingly!
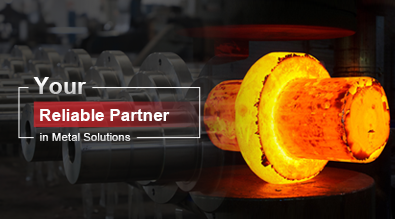
China WELONG- Your Reliable Partner in Metal Solutions