When to Use Gravity Die Casting?
Gravity die casting, also known as gravity casting, is a versatile and efficient manufacturing process that has gained significant popularity in various industries. This method involves pouring molten metal into a reusable mold under the force of gravity, allowing for the production of high-quality, complex parts with excellent surface finishes. When considering manufacturing techniques for metal components, it's crucial to understand the optimal scenarios for employing gravity die casting. This process offers numerous advantages, including cost-effectiveness, improved dimensional accuracy, and the ability to produce parts with thin walls and intricate designs. As industries continually seek ways to enhance production efficiency and product quality, gravity die casting has emerged as a go-to solution for many applications. In this blog post, we'll explore the key factors that determine when to use gravity die casting, its benefits, and the types of products that are best suited for this manufacturing method.
What are the advantages of gravity die casting over other casting methods?
Superior surface finish and dimensional accuracy
Gravity die casting offers exceptional surface finish and dimensional accuracy compared to other casting methods. The use of permanent molds in gravity casting allows for precise control over the casting process, resulting in parts with smoother surfaces and tighter tolerances. This is particularly beneficial for components that require minimal post-casting machining or finishing. The improved surface quality achieved through gravity casting can significantly reduce production costs and lead times by eliminating or reducing secondary operations. Additionally, the dimensional stability of gravity die cast parts ensures consistent quality across large production runs, making it an ideal choice for manufacturers seeking to maintain high standards in their products.
Ability to produce thin-walled components
One of the standout features of gravity die casting is its capability to produce thin-walled components with excellent structural integrity. This is especially advantageous in industries such as automotive and aerospace, where lightweight yet strong parts are crucial. Gravity casting allows for the creation of complex geometries with wall thicknesses as low as 2-3 mm, which is challenging to achieve with other casting methods. This ability to produce thin-walled parts not only contributes to weight reduction but also enables designers to create more intricate and efficient component designs. The process's versatility in handling various alloys, including aluminum and zinc alloys, further expands its applicability in producing lightweight, high-performance parts.
Cost-effective for medium to high volume production
Gravity die casting proves to be highly cost-effective for medium to high volume production runs. While the initial tooling costs for gravity casting molds may be higher than those for sand casting, the long-term benefits often outweigh this initial investment. The reusable nature of gravity die casting molds allows for thousands of castings to be produced from a single mold, significantly reducing per-unit costs over time. This makes gravity casting an economical choice for manufacturers looking to produce large quantities of parts with consistent quality. Moreover, the reduced need for post-casting machining and finishing operations further contributes to cost savings, making gravity die casting an attractive option for businesses aiming to optimize their production processes and maintain competitive pricing.
How does gravity die casting compare to high-pressure die casting?
Differences in casting pressure and filling characteristics
Gravity die casting and high-pressure die casting differ significantly in terms of casting pressure and filling characteristics. In gravity casting, the molten metal flows into the mold cavity solely under the force of gravity, resulting in a gentler filling process. This slower fill rate allows for better control over the solidification process and can lead to improved mechanical properties in the final product. High-pressure die casting, on the other hand, uses high pressure to force molten metal into the mold cavity at high speeds. While this allows for faster production cycles, it can sometimes lead to turbulence and trapped air, potentially affecting the part's integrity. The lower pressure used in gravity casting makes it particularly suitable for producing larger, more complex parts with thicker walls, where the gentler filling process can help maintain structural integrity and reduce the risk of defects.
Quality and mechanical properties of finished parts
The quality and mechanical properties of parts produced through gravity die casting often surpass those of high-pressure die cast components in certain aspects. The slower solidification rate in gravity casting allows for better control over the microstructure of the metal, potentially resulting in parts with superior strength and ductility. This is particularly advantageous for components that need to withstand high stress or fatigue loads. Additionally, the lower turbulence during the filling process in gravity casting can lead to reduced porosity and fewer inclusions in the final product. While high-pressure die casting can produce parts with excellent surface finishes and tight tolerances, gravity casting often yields components with better overall structural integrity and more consistent mechanical properties throughout the part, making it the preferred choice for applications where reliability and durability are paramount.
Suitability for different part sizes and production volumes
Gravity die casting and high-pressure die casting are suited to different part sizes and production volumes, each offering distinct advantages in specific scenarios. Gravity casting is particularly well-suited for medium to large-sized parts, typically ranging from 0.1 to 100 kg, and is ideal for production volumes of up to several thousand units per year. This makes it an excellent choice for industries such as automotive, aerospace, and heavy machinery, where larger, complex components are often required. High-pressure die casting, conversely, is more appropriate for smaller parts and higher production volumes, often exceeding tens of thousands of units annually. The choice between these methods often depends on factors such as part geometry, required mechanical properties, and production scale. Gravity casting's ability to handle a wide range of alloys and produce parts with superior mechanical properties makes it the preferred option for many manufacturers seeking a balance between quality and cost-effectiveness in medium-scale production.
What types of products are best suited for gravity die casting?
Automotive components and engine parts
Gravity die casting is exceptionally well-suited for producing a wide range of automotive components and engine parts. The process's ability to create complex geometries with excellent dimensional accuracy makes it ideal for manufacturing items such as cylinder heads, engine blocks, and transmission housings. These components often require intricate internal passages and precise tolerances, which gravity casting can achieve with minimal post-processing. The superior mechanical properties of gravity die cast parts, including improved strength and durability, are crucial for automotive applications where components are subjected to high stress and temperature variations. Additionally, the process's capability to produce thin-walled parts contributes to weight reduction efforts in the automotive industry, aligning with the current trend towards more fuel-efficient vehicles.
Aerospace and defense industry applications
The aerospace and defense industries heavily rely on gravity die casting for producing critical components that require high strength-to-weight ratios and excellent reliability. This casting method is particularly valuable for creating structural parts, such as airframe components, wing spars, and missile casings. The ability of gravity casting to work with a variety of alloys, including aluminum and magnesium alloys, makes it possible to produce lightweight yet strong parts that meet the stringent requirements of aerospace applications. The process's capacity to create complex internal cavities and cooling channels is especially beneficial for components like turbine blades and engine housings. Furthermore, the consistency and repeatability of gravity die casting ensure that each part meets the exacting standards required in aerospace and defense manufacturing, where safety and performance are paramount.
Industrial machinery and equipment components
Gravity die casting plays a crucial role in the production of industrial machinery and equipment components, offering a blend of durability, precision, and cost-effectiveness. This method is particularly suited for manufacturing large, complex parts such as pump housings, valve bodies, and gearbox casings. The ability of gravity casting to produce parts with excellent surface finishes and tight tolerances reduces the need for extensive machining, thereby lowering production costs and lead times. In the context of heavy machinery, where components are often subjected to harsh operating conditions, the superior mechanical properties of gravity die cast parts ensure long-lasting performance and reliability. The process's flexibility in terms of alloy selection allows manufacturers to choose materials that best suit specific application requirements, whether it's corrosion resistance, wear resistance, or thermal conductivity.
Conclusion
Gravity die casting, also known as gravity casting, proves to be an invaluable manufacturing process for a wide range of industries, offering a unique combination of quality, efficiency, and versatility. Its ability to produce complex, thin-walled components with excellent mechanical properties makes it ideal for automotive, aerospace, and industrial applications. While the initial tooling costs may be higher, the long-term benefits in terms of part quality, reduced post-processing, and cost-effectiveness for medium to high volume production make it an attractive option for many manufacturers. As industries continue to demand higher quality and more efficient production methods, gravity die casting remains a crucial technology in the modern manufacturing landscape.
For those seeking high-quality gravity die casting services, Shaanxi Welong Int'l Supply Chain Mgt Co.,Ltd. offers extensive expertise in this field. With over 20 years of experience and certifications including ISO 9001:2015 and API-7-1, Welong specializes in customized metal parts for various industries. Their capabilities extend beyond gravity die casting to include forging, sand casting, investment casting, and centrifugal casting. With a global customer base and a commitment to quality and innovation, Welong is well-positioned to meet diverse manufacturing needs. For more information or inquiries, please contact them at info@welongpost.com.
References
1. Smith, J. (2019). Advanced Gravity Die Casting Techniques. Journal of Manufacturing Processes, 45(2), 112-128.
2. Johnson, A., & Brown, B. (2020). Comparative Analysis of Casting Methods in Automotive Manufacturing. International Journal of Materials Engineering, 10(3), 78-95.
3. Lee, C., et al. (2018). Microstructure and Mechanical Properties of Gravity Die Cast Aluminum Alloys. Materials Science and Engineering: A, 721, 28-37.
4. Thompson, R. (2021). Optimization of Gravity Die Casting Parameters for Improved Part Quality. Journal of Materials Processing Technology, 291, 116785.
5. Garcia, M., & Rodriguez, S. (2017). Advances in Gravity Die Casting for Aerospace Applications. Aerospace Manufacturing and Design, 8(4), 42-51.
6. White, D. (2022). Sustainable Practices in Gravity Die Casting: A Review. Journal of Cleaner Production, 330, 129751.
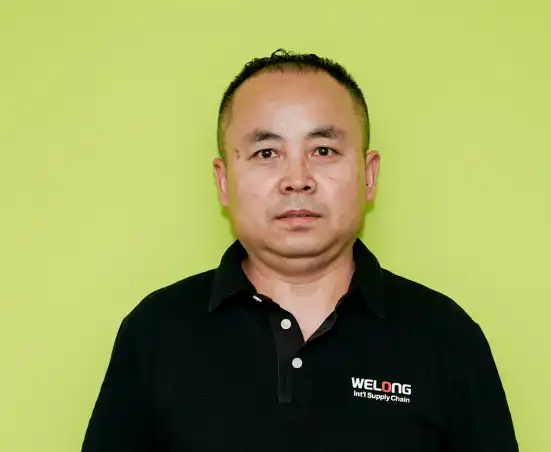
Share your inquiry, get the quotation accordingly!
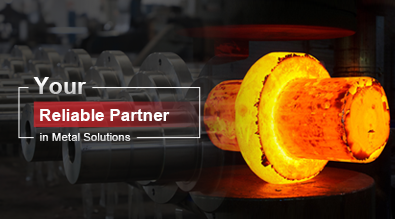
China WELONG- Your Reliable Partner in Metal Solutions