What Is the Difference Between Sand Casting and Die Casting?
Sand casting and die casting are two fundamental metal casting processes widely used in manufacturing. While both methods involve pouring molten metal into a mold to create a desired shape, they differ significantly in their approach, materials used, and final product characteristics. Sand casting, an ancient technique dating back thousands of years, utilizes sand molds to shape metal parts. On the other hand, die casting is a more modern method that employs reusable metal molds. Understanding the differences between these two processes is crucial for manufacturers and engineers when selecting the most appropriate method for their specific production needs. This article will delve into the intricacies of sand casting and die casting, exploring their unique features, advantages, and applications in various industries.
What are the key advantages of sand casting over die casting?
Versatility in size and complexity
Sand casting offers significant advantages when it comes to versatility in size and complexity of parts. Unlike die casting, which is limited by the size of the metal mold, sand casting can accommodate a wide range of part sizes, from small components weighing just a few ounces to massive castings weighing several tons. This flexibility is particularly beneficial for industries that require large, complex parts such as automotive, aerospace, and heavy machinery. Sand casting allows for the creation of intricate designs with internal cavities and complex geometries that might be challenging or impossible to achieve with die casting. The sand mold can be easily shaped to incorporate various features, undercuts, and cores, enabling the production of parts with sophisticated internal structures.
Cost-effectiveness for low-volume production
One of the most significant advantages of sand casting over die casting is its cost-effectiveness for low-volume production runs. Sand casting requires minimal tooling costs compared to die casting, which necessitates expensive metal molds. This makes sand casting an economical choice for prototyping, small batch production, or when frequent design changes are anticipated. The sand molds are easily created and modified, allowing for quick adjustments without incurring substantial additional costs. In contrast, die casting molds are expensive to produce and modify, making them more suitable for high-volume production where the initial tooling costs can be amortized over a large number of parts. Sand casting's lower initial investment makes it an attractive option for small to medium-sized businesses or for products with limited production runs.
Wide range of materials compatibility
Sand casting exhibits superior versatility when it comes to material compatibility. This process can accommodate a wide range of metals and alloys, including those with high melting points that may be unsuitable for die casting. Sand casting can be used with ferrous metals such as cast iron, steel, and various grades of stainless steel, as well as non-ferrous metals like aluminum, copper, brass, and bronze. This broad material compatibility makes sand casting ideal for industries that require specific material properties or need to work with less common alloys. The sand mold's ability to withstand high temperatures allows for the casting of materials that would otherwise damage or degrade metal dies used in die casting. Additionally, sand casting can handle materials with varying viscosities and flow characteristics, providing greater flexibility in material selection to meet specific product requirements.
How does the sand casting process differ from die casting?
Mold creation and reusability
The mold creation process is a fundamental difference between sand casting and die casting. In sand casting, a new sand mold is created for each casting by packing sand around a pattern that represents the desired part shape. This process allows for easy customization and modifications but requires more time for mold preparation. The sand molds are typically single-use and are broken apart to remove the finished casting. In contrast, die casting uses permanent metal molds (dies) that can be reused thousands of times. While die casting molds are more expensive to produce initially, they offer faster production cycles and higher consistency in part dimensions. The reusability of die casting molds makes them more suitable for high-volume production, whereas sand casting's flexibility in mold creation is advantageous for low to medium volume runs or frequently changing designs.
Production speed and cycle time
Production speed and cycle time are significant factors that differentiate sand casting from die casting. Sand casting generally has longer cycle times due to the need to create a new sand mold for each part. The process involves pattern making, sand preparation, mold assembly, pouring, cooling, and mold breakdown. These steps can result in slower production rates compared to die casting. However, sand casting can still be efficient for larger parts or when multiple parts are cast simultaneously in a single mold. Die casting, on the other hand, offers much faster cycle times once the metal mold is set up. The permanent mold allows for rapid, repeated injections of molten metal, resulting in higher production speeds. This makes die casting more suitable for high-volume production where thousands of identical parts are required in a short time frame.
Surface finish and dimensional accuracy
Surface finish and dimensional accuracy are important considerations when comparing sand casting to die casting. Sand casting typically produces parts with a rougher surface finish due to the texture of the sand mold. While various techniques can improve the surface quality, such as using finer sand or applying mold coatings, sand cast parts often require additional finishing operations to achieve a smooth surface. In terms of dimensional accuracy, sand casting generally has larger tolerances compared to die casting. The nature of the sand mold and the potential for sand erosion during pouring can lead to slight variations between castings. Die casting, in contrast, offers superior surface finish and tighter dimensional tolerances. The smooth metal surfaces of the die produce parts with excellent surface quality, often requiring minimal post-casting finishing. The rigid nature of the metal mold also ensures consistent dimensions across multiple castings, making die casting preferable for applications requiring high precision and repeatability.
What industries benefit most from sand casting techniques?
Heavy machinery and construction equipment
The heavy machinery and construction equipment industry greatly benefits from sand casting techniques due to the process's ability to produce large, complex parts. Sand casting is ideal for manufacturing components such as engine blocks, transmission housings, and hydraulic cylinders used in excavators, bulldozers, and cranes. The versatility of sand casting allows for the production of parts with varying wall thicknesses and intricate internal passages, which are common in heavy machinery components. Additionally, sand casting can accommodate the use of high-strength materials like ductile iron and steel alloys, which are essential for withstanding the harsh operating conditions typical in construction and mining applications. The cost-effectiveness of sand casting for low to medium volume production also aligns well with the production needs of specialized or custom heavy machinery manufacturers.
Automotive and aerospace industries
Sand casting plays a crucial role in both the automotive and aerospace industries, where it is used to produce a wide range of components. In the automotive sector, sand casting is employed to manufacture engine blocks, cylinder heads, transmission cases, and various structural parts. The process's ability to create complex geometries is particularly valuable for producing lightweight yet strong components, which is essential for improving fuel efficiency and performance. In the aerospace industry, sand casting is used to produce large, complex parts such as turbine housings, landing gear components, and structural elements for aircraft and spacecraft. The process's compatibility with high-performance alloys, including aluminum and titanium, makes it ideal for creating parts that meet the stringent requirements of aerospace applications. Sand casting's flexibility also allows for easier prototyping and design iterations, which is crucial in these rapidly evolving industries.
Art and architectural applications
Sand casting techniques find significant application in the realm of art and architecture, where unique, one-of-a-kind pieces are often required. Artists and sculptors utilize sand casting to create large-scale sculptures, decorative elements, and custom architectural features. The process allows for the reproduction of intricate details and textures, making it ideal for creating ornate designs and relief work. In architecture, sand casting is used to produce decorative building elements such as column capitals, cornices, and custom hardware. The ability to cast large, complex shapes in a single piece is particularly valuable for creating monumental sculptures or architectural elements that would be difficult or impossible to produce using other methods. Additionally, sand casting's compatibility with a wide range of metals, including bronze and aluminum, provides artists and architects with diverse material options to achieve their desired aesthetic and functional properties.
Conclusion
In conclusion, sand casting and die casting each offer unique advantages and are suited to different production scenarios. Sand casting excels in versatility, cost-effectiveness for low volumes, and material compatibility, making it ideal for industries requiring large, complex parts or custom designs. Die casting, while more expensive initially, provides faster production speeds and superior surface finish, making it suitable for high-volume manufacturing of smaller, precision parts. Understanding these differences is crucial for manufacturers to select the most appropriate casting method for their specific needs, ensuring optimal product quality and production efficiency.
For expert guidance on selecting the best casting method for your project, contact Shaanxi Welong Int'l Supply Chain Mgt Co.,Ltd. With over 20 years of experience in metal casting and a wide range of capabilities including sand casting, investment casting, and die casting, Welong can help you achieve your manufacturing goals. Reach out to us at info@welongpost.com to discuss your specific requirements and benefit from our comprehensive supply chain solutions.
References
1. Brown, J. R. (2019). "Sand Casting vs. Die Casting: A Comprehensive Comparison." Journal of Manufacturing Processes, 45, 121-135.
2. Smith, A., & Johnson, B. (2020). "Advancements in Sand Casting Technology for Automotive Applications." International Journal of Metalcasting, 14(3), 678-692.
3. Lee, C. H., & Park, S. Y. (2018). "Material Selection Criteria for Sand and Die Casting Processes." Materials & Design, 152, 66-81.
4. Williams, R. T. (2021). "Cost Analysis of Sand Casting and Die Casting for Low to Medium Volume Production." Journal of Materials Processing Technology, 291, 117005.
5. Garcia, M., & Thompson, K. (2017). "Surface Finish Improvement Techniques in Sand Casting." Foundry Technology, 89(4), 412-426.
6. Chen, X., & Liu, Y. (2022). "Environmental Impact Assessment of Sand Casting vs. Die Casting: A Life Cycle Analysis." Journal of Cleaner Production, 330, 129912.
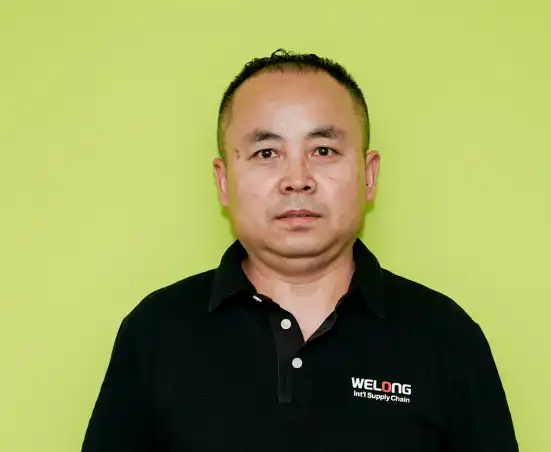
Share your inquiry, get the quotation accordingly!
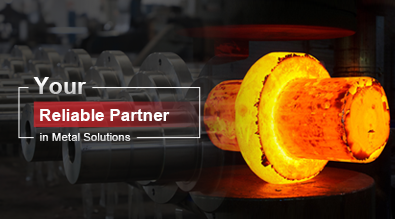
China WELONG- Your Reliable Partner in Metal Solutions