What is the coating process in investment casting?
The coating process in investment casting is a crucial step that involves applying multiple layers of ceramic slurry to a wax pattern to create a robust and heat-resistant mold. This intricate procedure is essential for producing high-quality, complex metal components with exceptional surface finish and dimensional accuracy. The process begins with dipping the wax pattern into a ceramic slurry, followed by the application of stucco particles to enhance the mold's strength. Multiple layers are applied, each allowed to dry before the next is added, resulting in a thick, durable shell capable of withstanding high temperatures during the casting process. The coating process is critical in determining the final quality of the cast product, influencing factors such as surface finish, dimensional accuracy, and overall structural integrity. Understanding and optimizing this process is key to achieving superior results in investment casting applications across various industries.
What are the key steps in the investment casting coating process?
Preparation of ceramic slurry
The preparation of ceramic slurry is a critical initial step in the investment casting coating process. This slurry, typically composed of fine refractory materials such as silica, zircon, or alumina, mixed with a binder system, forms the foundation of the mold. The composition and properties of the slurry are carefully controlled to ensure optimal viscosity, adherence, and thermal resistance. In investment casting, the choice of slurry materials depends on factors such as the metal being cast, the desired surface finish, and the complexity of the part. For instance, when casting super-alloys or high-temperature materials, specialized slurries with enhanced thermal stability may be used. The preparation process involves precise mixing and aging of the slurry to achieve the right consistency and particle distribution, which directly impacts the quality of the final casting.
Dipping and stuccoing
The dipping and stuccoing phase is where the wax pattern begins its transformation into a ceramic mold. In this stage of investment casting, the pattern is carefully dipped into the prepared ceramic slurry, ensuring even coverage. Immediately after dipping, while the slurry is still wet, the pattern is coated with stucco particles. These particles, which can be fine sand or other refractory materials, adhere to the wet slurry, creating a rough surface that enhances the bonding of subsequent layers. This process is repeated several times, with each layer being allowed to dry before the next is applied. The number of layers and the drying time between them vary depending on the size and complexity of the part being cast. In advanced investment casting processes, automated dipping systems may be employed to ensure consistency and efficiency, especially for large-scale production.
Drying and hardening
The drying and hardening stage is crucial for developing the strength and integrity of the ceramic shell in investment casting. After each layer of slurry and stucco is applied, it must be thoroughly dried before the next layer can be added. This drying process typically occurs in a controlled environment where temperature and humidity are carefully regulated to prevent cracking or warping of the shell. For more complex or larger castings, specialized drying rooms or chambers may be used to ensure uniform drying. Once all layers have been applied and dried, the entire mold undergoes a hardening process. This often involves firing the shell at high temperatures to remove any remaining moisture and to sinter the ceramic particles, creating a strong, cohesive structure. The hardening process is critical in investment casting as it determines the shell's ability to withstand the high temperatures and pressures of the metal pouring stage, directly impacting the quality and accuracy of the final cast product.
How does the coating material affect the quality of investment casting?
Impact on surface finish
The choice of coating material in investment casting has a profound impact on the surface finish of the final product. Different ceramic slurries and stucco materials can produce varying degrees of smoothness or texture on the cast surface. For instance, finer particles in the slurry typically result in a smoother finish, which is desirable for many precision components. In investment casting, the primary layer, often called the face coat, is particularly crucial as it directly contacts the molten metal and determines the surface quality of the casting. Advanced ceramic materials, such as zircon or alumina-based slurries, are often used for high-end applications requiring exceptional surface finish. The consistency and application technique of the coating also play a vital role; uneven application can lead to surface defects in the final casting. Furthermore, the interaction between the coating material and the molten metal during pouring can affect the surface characteristics, making the selection of compatible materials essential for achieving the desired finish in investment casting.
Influence on dimensional accuracy
The coating material's properties significantly influence the dimensional accuracy of investment castings. The thermal expansion and contraction characteristics of the ceramic shell during the casting process directly affect the final dimensions of the part. In investment casting, materials with low thermal expansion coefficients are often preferred to minimize dimensional changes during heating and cooling. The thickness and uniformity of the coating layers also play a crucial role; inconsistent application can lead to variations in wall thickness, resulting in dimensional inaccuracies. Additionally, the permeability of the coating material affects how gases escape during the casting process, which can impact the internal dimensions and surface quality of complex parts. Advanced investment casting techniques may employ specialized additives in the coating material to enhance dimensional stability, particularly for parts with tight tolerances. The choice of coating material must balance the need for strength and thermal resistance with the requirement for dimensional accuracy, making it a critical consideration in the investment casting process.
Effect on casting defects
The coating material used in investment casting plays a crucial role in preventing or mitigating various casting defects. The permeability and thermal properties of the ceramic shell directly affect how gases and heat are managed during the casting process. For instance, a coating with insufficient permeability can trap gases, leading to porosity or gas-related defects in the final casting. Conversely, a highly permeable coating may result in metal penetration defects. In investment casting, the thermal shock resistance of the coating material is particularly important to prevent cracking of the mold during metal pouring, which can cause leaks or inclusions in the casting. The reactivity of the coating material with the molten metal is another critical factor; incompatible materials can lead to chemical reactions that affect the surface quality or composition of the casting. Advanced coating materials and techniques in investment casting often focus on optimizing these properties to minimize defects, especially for complex parts or when working with reactive metals like titanium or super-alloys.
What are the advanced techniques in investment casting coating?
Automated dipping systems
Automated dipping systems represent a significant advancement in the investment casting coating process. These systems utilize robotic arms or programmable machines to precisely control the dipping of wax patterns into ceramic slurry. In investment casting, this automation ensures consistent coating thickness and coverage, which is crucial for maintaining uniform wall thickness in the final cast product. The automated process can be programmed to adjust dipping speed, depth, and duration based on the specific requirements of different parts, allowing for greater precision and repeatability than manual methods. This is particularly beneficial for large-scale production or when dealing with complex geometries that require careful handling. Advanced automated systems in investment casting may also incorporate sensors to monitor slurry viscosity and temperature, automatically adjusting parameters to maintain optimal coating conditions. This level of control not only enhances the quality of the castings but also improves efficiency and reduces labor costs in the investment casting process.
Specialized coating materials
The development of specialized coating materials has significantly advanced the capabilities of investment casting. These materials are engineered to meet specific performance requirements, such as enhanced thermal resistance, improved surface finish, or compatibility with challenging alloys. For instance, zircon-based slurries are often used in investment casting of super-alloys due to their excellent thermal stability and resistance to metal penetration. Nano-particle reinforced coatings are another innovation, offering improved strength and surface finish to the ceramic shell. Some specialized coatings incorporate additives that enhance the shell's collapsibility after casting, facilitating easier removal of the ceramic material from complex internal cavities. In high-precision investment casting, coatings with carefully controlled particle size distributions are used to achieve extremely smooth surface finishes. Additionally, environmentally friendly water-based binder systems are being developed as alternatives to traditional silica-based systems, addressing both environmental concerns and potentially improving casting quality. These specialized materials enable investment casting to meet increasingly demanding specifications across various industries, from aerospace to medical devices.
Advanced drying techniques
Advanced drying techniques have revolutionized the coating process in investment casting, significantly improving efficiency and quality. One such innovation is the use of environmentally controlled drying rooms, where temperature, humidity, and air flow are precisely regulated to ensure optimal drying conditions for each layer of the ceramic shell. This controlled environment prevents premature cracking or warping of the shell, a common issue in traditional air-drying methods. In some investment casting facilities, infrared drying systems are employed to accelerate the drying process without compromising shell integrity. These systems provide uniform heat distribution, reducing drying times while maintaining consistent quality. Another advanced technique is the use of microwave drying, which can rapidly and uniformly dry ceramic shells from the inside out, particularly effective for thick-walled or complex molds. Some investment casting processes incorporate fluidized bed drying, where the coated patterns are suspended in a stream of temperature-controlled air, ensuring even drying and preventing sagging or deformation. These advanced drying techniques not only enhance the quality of the ceramic shell but also significantly reduce production times in investment casting, enabling faster turnaround and increased productivity.
Conclusion
The coating process in investment casting is a critical component that significantly influences the quality, accuracy, and efficiency of the final cast products. From the preparation of ceramic slurries to advanced drying techniques, each step in the process plays a vital role in achieving superior results. As technology advances, innovations in automated systems, specialized materials, and controlled environments continue to enhance the capabilities of investment casting, making it an increasingly versatile and precise manufacturing method. These advancements not only improve product quality but also offer greater flexibility in design and material selection, positioning investment casting as a key technology in modern manufacturing across various industries.
For expert guidance and high-quality investment casting solutions, consider partnering with Shaanxi Welong Int'l Supply Chain Mgt Co.,Ltd. With over 20 years of experience and certifications including ISO 9001:2015 and API-7-1, Welong specializes in customized metal parts for diverse industries. Their comprehensive capabilities include investment casting, forging, sand casting, centrifugal casting, and machining, with a wide range of materials and finishing options available. Welong's commitment to quality, efficiency, and customer satisfaction makes them a leading choice in the global supply chain. For more information, contact them at info@welongpost.com.
References
1. Johnson, A. B., & Smith, C. D. (2018). Advancements in Ceramic Shell Technology for Investment Casting. Journal of Materials Processing Technology, 256, 103-112.
2. Zhang, Y., & Liu, X. (2019). Influence of Coating Materials on the Surface Quality of Investment Cast Components. International Journal of Cast Metals Research, 32(4), 197-205.
3. Brown, R. T., & Davis, E. F. (2020). Automated Dipping Systems in Modern Investment Casting: A Comprehensive Review. Foundry Technology International, 43(2), 78-89.
4. Lee, S. H., & Park, J. W. (2017). Analysis of Drying Techniques in Investment Casting Processes. Journal of Manufacturing Science and Engineering, 139(6), 061010.
5. Thompson, K. L., & Wilson, M. R. (2021). Specialized Coating Materials for High-Performance Investment Castings. Advanced Materials and Processes, 179(3), 24-31.
6. Garcia, R. A., & Martinez, L. O. (2019). Dimensional Accuracy in Investment Casting: The Role of Shell Materials and Process Parameters. Materials & Design, 168, 107638.
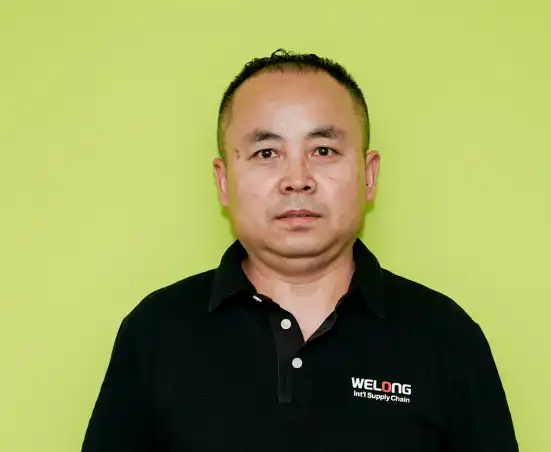
Share your inquiry, get the quotation accordingly!
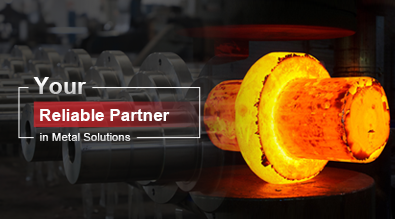
China WELONG- Your Reliable Partner in Metal Solutions