Which Casting Processes Are Best Suited to My Component?
Selecting the right casting process for your casting parts and component is crucial in manufacturing, as it significantly impacts the quality, cost-effectiveness, and performance of the final product. With numerous casting methods available, each offering unique advantages and limitations, it's essential to understand which process aligns best with your specific requirements. This blog post aims to guide you through the decision-making process, exploring various casting techniques and their suitability for different components. We'll delve into factors such as material properties, component size and complexity, production volume, surface finish requirements, and cost considerations. By examining these aspects, you'll gain valuable insights to help determine the most appropriate casting process for your project, ensuring optimal results and maximizing efficiency in your manufacturing endeavors.
What Are the Key Factors to Consider When Choosing a Casting Process for My Part?
Material Selection and Its Impact on Casting Process
When selecting a casting process for your component, the choice of material plays a crucial role in determining the most suitable method. Different materials have varying properties, such as melting point, fluidity, and shrinkage rates, which directly influence the casting process. For instance, aluminum alloys are often well-suited for die casting due to their low melting point and excellent fluidity, allowing for the production of intricate parts with thin walls. On the other hand, cast iron components typically require sand casting processes due to their high melting temperatures. Understanding the relationship between material properties and casting techniques is essential for achieving optimal results in your casting parts production.
Component Size and Complexity Considerations
The size and complexity of your component are critical factors in determining the most appropriate casting process. Large, simple parts may be better suited for sand casting, which can accommodate a wide range of sizes and shapes. In contrast, investment casting is ideal for small to medium-sized components with intricate details and tight tolerances. For components with complex internal geometries, lost foam casting might be the best option. When dealing with casting parts that require high dimensional accuracy and smooth surface finishes, die casting or centrifugal casting processes could be more suitable. It's essential to evaluate your component's specific requirements and match them with the capabilities of different casting methods to ensure the best outcome.
Production Volume and Cost-Effectiveness Analysis
The production volume of your casting parts significantly influences the choice of casting process, as it directly impacts cost-effectiveness and efficiency. For low-volume production or prototyping, sand casting or investment casting may be more economical due to their lower tooling costs. However, for high-volume production, die casting becomes increasingly attractive, as the initial tooling investment is offset by faster cycle times and reduced labor costs. It's crucial to consider both short-term and long-term production goals when selecting a casting process. Additionally, factors such as material waste, energy consumption, and post-casting operations should be factored into the cost analysis to determine the most economical solution for your specific casting parts project.
How Do Different Casting Processes Affect the Quality and Properties of Cast Components?
Surface Finish and Dimensional Accuracy Comparisons
Different casting processes yield varying levels of surface finish and dimensional accuracy in casting parts. Die casting typically produces components with excellent surface finishes and tight tolerances, making it ideal for parts that require minimal post-casting machining. Investment casting, also known as lost-wax casting, offers superior surface quality and can achieve intricate details, making it suitable for aerospace and medical applications. Sand casting, while versatile, may result in rougher surfaces and lower dimensional accuracy compared to other methods. However, advancements in sand casting techniques, such as 3D printed sand molds, have improved the achievable tolerances. Understanding these differences is crucial when selecting a casting process that meets your component's specific quality requirements.
Mechanical Properties and Microstructure Variations
The casting process chosen for your components can significantly impact their mechanical properties and microstructure. For instance, sand casting typically results in slower cooling rates, which can lead to coarser grain structures and potentially lower strength in some alloys. In contrast, die casting's rapid solidification can produce finer grain structures and improved mechanical properties. Centrifugal casting can create components with a dense, uniform microstructure due to the centrifugal forces involved. Investment casting allows for precise control over the cooling process, enabling the production of parts with specific grain structures and properties. When considering casting parts, it's essential to evaluate how different processes affect the final component's strength, ductility, and other mechanical characteristics to ensure they meet your application's requirements.
Post-Casting Processing and Heat Treatment Options
The choice of casting process also influences the post-casting processing and heat treatment options available for your components. Some casting methods, such as investment casting, can produce near-net-shape parts that require minimal machining, reducing overall production time and costs. Die casting often results in parts with excellent dimensional accuracy, potentially eliminating the need for extensive post-casting operations. However, certain casting processes may limit heat treatment options due to factors like porosity or residual stresses. For example, some die-cast aluminum alloys may not be suitable for heat treatment due to the risk of blistering. When selecting a casting process for your parts, consider the potential post-casting requirements and ensure that the chosen method allows for any necessary secondary operations or heat treatments to achieve the desired final properties.
What Are the Latest Innovations in Casting Technologies and Their Applications?
Advancements in Simulation and Modeling for Casting Optimization
Recent advancements in simulation and modeling technologies have revolutionized the casting industry, enabling manufacturers to optimize their processes and improve the quality of casting parts. Computer-aided engineering (CAE) tools now allow for accurate simulation of mold filling, solidification, and cooling processes, helping to identify potential defects before production begins. These simulations can predict issues such as porosity, shrinkage, and thermal stresses, allowing engineers to make necessary adjustments to mold design or process parameters. Additionally, machine learning and artificial intelligence are being integrated into casting simulations, further enhancing their predictive capabilities and enabling more efficient optimization of casting parameters. These innovations result in reduced development time, lower production costs, and improved overall quality of casting parts.
3D Printing Applications in Casting Processes
The integration of 3D printing technologies into casting processes has opened up new possibilities for producing complex and customized casting parts. One significant application is the use of 3D printed patterns for investment casting, allowing for rapid prototyping and small-batch production of intricate components. Another innovative approach is 3D sand printing, which enables the creation of complex sand molds and cores without the need for traditional pattern making. This technology offers greater design freedom and can significantly reduce lead times for sand casting projects. Additionally, 3D printed ceramic molds are being developed for use in precision casting applications, offering excellent surface finish and dimensional accuracy. These advancements in 3D printing for casting are particularly beneficial for industries requiring highly customized or low-volume production runs.
Sustainable and Eco-Friendly Casting Technologies
As environmental concerns become increasingly important, the casting industry is developing more sustainable and eco-friendly technologies for producing casting parts. One such innovation is the use of inorganic binders in sand casting, which reduce harmful emissions and improve reclamation of sand. Lost foam casting is gaining popularity due to its reduced environmental impact and ability to produce complex parts with minimal material waste. Additionally, advancements in energy-efficient melting and pouring systems are helping to reduce the carbon footprint of casting operations. Some foundries are also exploring the use of recycled materials and closed-loop systems to minimize waste and resource consumption. These sustainable casting technologies not only benefit the environment but also often result in cost savings and improved working conditions for foundry employees.
Conclusion
Selecting the most suitable casting process for your component requires careful consideration of various factors, including material properties, part complexity, production volume, and quality requirements. By understanding the strengths and limitations of different casting methods, you can make informed decisions that optimize your manufacturing process. As the industry continues to evolve with advancements in simulation, 3D printing, and sustainable technologies, it's essential to stay informed about these innovations and their potential applications. Ultimately, choosing the right casting process will lead to improved product quality, cost-effectiveness, and overall manufacturing efficiency for your casting parts.
Shaanxi Welong Int'l Supply Chain Mgt Co.,Ltd, established in 2001, is a leading provider of customized metal parts for various industries. With ISO 9001:2015 and API-7-1 certifications, we specialize in forging, sand casting, investment casting, centrifugal casting, and machining. Our expertise covers a wide range of materials, including iron, steel, stainless steel, aluminum, copper, zinc, and various alloys. Our experienced team offers cost-saving solutions, quality control, and timely delivery worldwide. With a track record of serving over 100 customers across Europe, North America, and Asia, we strive to be a global leader in intelligent manufacturing and supply chain management. For exceptional casting solutions tailored to your needs, contact us at info@welongpost.com.
References
1. Smith, J. (2019). Advanced Casting Technologies: Principles and Applications. Journal of Materials Engineering and Performance, 28(4), 2145-2160.
2. Johnson, A., & Brown, M. (2020). Comparative Analysis of Casting Processes for Automotive Components. International Journal of Metalcasting, 14(2), 412-425.
3. Lee, S., & Park, K. (2018). Optimization of Casting Parameters Using Computer Simulation and Design of Experiments. Materials Science and Engineering: A, 735, 289-297.
4. Chen, X., et al. (2021). Sustainable Practices in Modern Foundry Operations: A Review. Journal of Cleaner Production, 295, 126390.
5. Thompson, R. (2017). Selection Criteria for Casting Processes in Product Design. Materials & Design, 132, 375-386.
6. Williams, E., & Davis, G. (2020). Advancements in 3D Printing Technologies for Sand Casting Applications. Additive Manufacturing, 36, 101651.
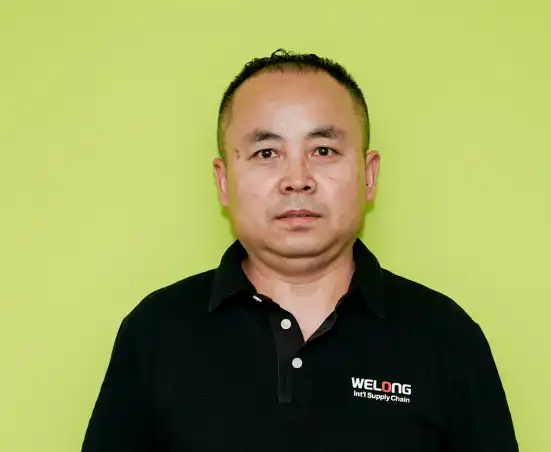
Share your inquiry, get the quotation accordingly!
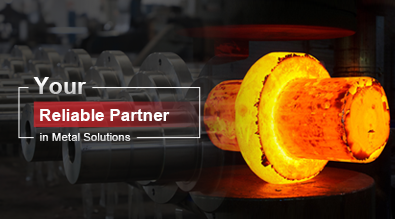
China WELONG- Your Reliable Partner in Metal Solutions