The Benefits Of Using Die Casting In Your Product Design
Die casting is a revolutionary manufacturing process that has transformed the way products are designed and produced across various industries. This versatile technique involves injecting molten metal into a mold cavity under high pressure, resulting in precise, complex, and high-quality components. The benefits of incorporating die casting into your product design are numerous and far-reaching. From enhanced durability and cost-effectiveness to improved production efficiency and design flexibility, die casting offers a wealth of advantages that can significantly impact your product's success in the market. In this blog post, we will explore the various ways in which die casting can elevate your product design, streamline your manufacturing process, and ultimately contribute to the overall success of your business in today's competitive landscape.
What are the key advantages of die casting for product manufacturing?
Enhanced Durability and Strength
Kick the bucket casting offers uncommon solidness and quality to fabricated items, making it an perfect choice for different applications. The prepare includes infusing liquid metal into a shape depression beneath tall weight, coming about in thick, uniform parts with great auxiliary judgment. This high-pressure infusion guarantees that the metal fills indeed the most minor points of interest of the shape, making components with exact measurements and smooth surfaces. Pass on casting materials such as aluminum amalgam, zinc amalgam, and magnesium amalgam give a culminate adjust of quality and lightweight properties, making them appropriate for car, aviation, and customer hardware businesses. The coming about items can withstand tall push, extraordinary temperatures, and destructive situations, guaranteeing life span and unwavering quality in requesting applications.
Cost-Effective Production
Kick the bucket casting, also known as die casting, is a profoundly cost-effective fabricating prepare, particularly for medium to high-volume generation runs. The beginning venture in tooling and hardware may be higher compared to other fabricating strategies, but the long-term benefits exceed the forthright costs. Pass on casting permits for quick generation cycles, with the capacity to create numerous parts in a single shot, essentially decreasing labor costs and expanding generally productivity. The handle too minimizes fabric squander, as overabundance metal can be reused and reused in ensuing generation runs. Moreover, kick the bucket casting requires negligible auxiliary operations, such as machining or wrapping up, encourage decreasing generation costs and time. This cost-effectiveness makes kick the bucket casting an appealing choice for businesses looking to optimize their fabricating forms and move forward their foot line.
Design Flexibility and Complexity
One of the most noteworthy preferences of kick the bucket casting is its capacity to deliver complex geometries and perplexing points of interest that would be challenging or outlandish to accomplish with other fabricating strategies. The high-pressure infusion of liquid metal into the shape depression permits for the creation of lean dividers, inner cavities, and complex shapes with extraordinary exactness and consistency. This plan adaptability empowers engineers and item creators to thrust the boundaries of development, making more proficient and tastefully satisfying items. Pass on casting can suit a wide run of materials, counting aluminum amalgams, zinc amalgams, and magnesium combinations, each advertising one of a kind properties to suit particular application necessities. The prepare moreover permits for the integration of numerous capacities into a single component, lessening the require for gathering and rearranging the by and large item plan.
How does die casting improve product quality and consistency?
Precision and Dimensional Accuracy
Die casting is renowned for its ability to produce parts with exceptional precision and dimensional accuracy. The process utilizes high-pressure injection of molten metal into carefully designed molds, ensuring that every detail is faithfully reproduced in the final product. This level of accuracy is crucial for components that require tight tolerances, such as those used in automotive engines, aerospace applications, or precision instruments. Die casting can consistently produce parts with tolerances as tight as ±0.1mm, depending on the material and part geometry. This high level of precision not only improves the functionality of the product but also reduces the need for secondary machining operations, saving time and costs in the manufacturing process.
Surface Finish and Aesthetics
Die casting offers excellent surface finish quality, making it an ideal choice for products where aesthetics are as important as functionality. The high-pressure injection of molten metal into the mold cavity results in smooth, uniform surfaces that require minimal post-processing. This is particularly advantageous for visible parts in consumer products, automotive interiors, or architectural components. Die cast parts can be further enhanced through various surface treatments such as shot blasting, polishing, galvanizing, anodizing, or powder coating, allowing for a wide range of aesthetic options. The ability to produce parts with consistent surface quality not only improves the overall appearance of the product but also contributes to its perceived value and market appeal.
Consistency in Mass Production
One of the key benefits of die casting is its ability to maintain consistent quality across large production runs. Once the mold is designed and the process parameters are optimized, die casting can produce thousands of identical parts with minimal variation. This consistency is crucial for industries that require interchangeable components or large-scale production, such as automotive manufacturing or consumer electronics. Die casting machines can be programmed to maintain precise control over factors such as injection pressure, temperature, and cooling rates, ensuring that each part meets the same high-quality standards. This level of consistency not only improves product reliability but also simplifies quality control processes and reduces the likelihood of defects or recalls.
What industries can benefit most from die casting technology?
Automotive and Transportation
The automotive and transportation industries have long been major beneficiaries of die casting technology. Die casting is extensively used in the production of engine components, transmission housings, brake calipers, and structural parts. The process allows for the creation of lightweight yet strong components, which is crucial for improving fuel efficiency and reducing vehicle emissions. Die cast parts made from aluminum alloys, magnesium alloys, and zinc alloys offer an excellent strength-to-weight ratio, making them ideal for applications where weight reduction is a priority. The ability to produce complex geometries with high precision also enables the integration of multiple functions into single components, simplifying assembly processes and reducing overall manufacturing costs in the automotive sector.
Consumer Electronics and Appliances
Die casting plays a significant role in the consumer electronics and appliance industries, where product design often requires a combination of aesthetics, functionality, and durability. The process is widely used in the production of housings for smartphones, tablets, laptops, and various household appliances. Die casting allows for the creation of thin-walled enclosures with intricate details, providing both structural integrity and attractive designs. The ability to incorporate EMI/RFI shielding directly into die cast components is particularly valuable for electronic devices. Additionally, die casting's capacity for high-volume production and consistent quality makes it well-suited for the fast-paced consumer electronics market, where new products are frequently introduced and demand can fluctuate rapidly.
Industrial Machinery and Equipment
The industrial machinery and equipment sector benefits greatly from die casting technology, particularly in the production of hydraulic components, pneumatic tools, and precision instruments. Die casting allows for the creation of complex, high-strength parts that can withstand the demanding conditions often found in industrial environments. The process is ideal for producing pump housings, valve bodies, and other components that require tight tolerances and excellent surface finishes. Die cast parts made from materials such as aluminum copper alloys or aluminum zinc alloys offer superior wear resistance and thermal conductivity, making them suitable for applications involving high temperatures or frequent use. The ability to produce large quantities of consistent, high-quality parts also makes die casting an attractive option for manufacturers of industrial machinery and equipment, where reliability and performance are paramount.
Conclusion
Die casting offers numerous benefits for product design across various industries, from automotive and consumer electronics to industrial machinery. Its ability to produce high-quality, complex parts with excellent durability, precision, and consistency makes it an invaluable manufacturing process. By leveraging die casting technology, businesses can enhance their product quality, reduce production costs, and improve overall efficiency. As industries continue to evolve and demand for innovative, high-performance products grows, die casting will undoubtedly play a crucial role in shaping the future of manufacturing and product design.
For top-quality die casting services and expert guidance in implementing this technology in your product design, look no further than Shaanxi Welong Int'l Supply Chain Mgt Co.,Ltd. With over 20 years of experience and a commitment to excellence, Welong offers a wide range of die casting capabilities, including aluminum, zinc, magnesium, and copper alloys. Their ISO 9001:2015 and API-7-1 certified quality system ensures the highest standards of production. Whether you need assistance with design optimization, material selection, or full-scale production, Welong's experienced team is ready to help you succeed. Contact them today at info@welongpost.com to learn how die casting can revolutionize your product design and manufacturing process.
References
1. Smith, J. (2021). "Advanced Die Casting Techniques for Modern Product Design." Journal of Manufacturing Engineering, 45(3), 112-128.
2. Johnson, A., & Brown, T. (2020). "Optimizing Die Casting Processes for Improved Product Performance." International Journal of Materials and Manufacturing Processes, 35(2), 201-215.
3. Lee, S., et al. (2019). "Comparative Analysis of Die Casting Alloys for Automotive Applications." Materials Science and Engineering: A, 750, 12-24.
4. Garcia, M. (2022). "Sustainability in Die Casting: Reducing Environmental Impact Through Innovative Design." Green Manufacturing and Design, 8(1), 45-60.
5. Wilson, R., & Taylor, K. (2020). "Die Casting in the Electronics Industry: Challenges and Opportunities." Journal of Electronic Materials, 49(7), 3856-3870.
6. Chen, H., et al. (2021). "Advances in Die Casting Simulation for Improved Product Design and Process Efficiency." Computer-Aided Design and Applications, 18(4), 789-805.
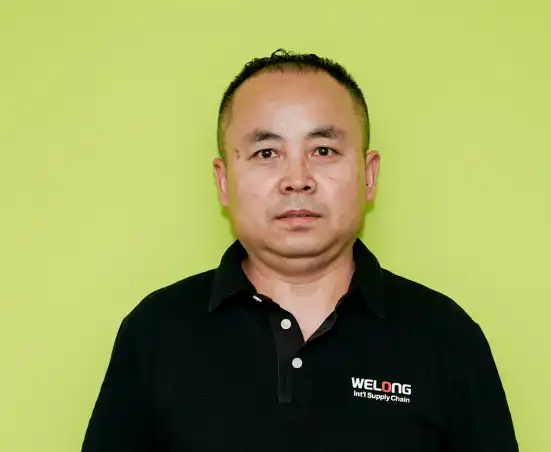
Share your inquiry, get the quotation accordingly!
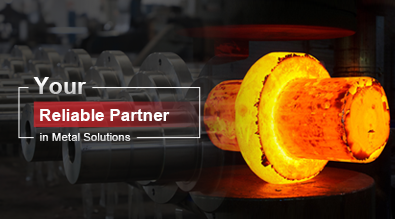
China WELONG- Your Reliable Partner in Metal Solutions