Custom Centrifugal Castings vs. Standard Off-The-Shelf Tubing
In the world of industrial manufacturing, the choice between custom centrifugal castings and standard off-the-shelf tubing is a critical decision that can significantly impact product quality, performance, and cost-effectiveness. Centrifugal casting, a process that utilizes centrifugal force to create hollow cylindrical parts, offers unique advantages over traditional tubing methods. This advanced technique allows for the production of components with superior mechanical properties, precise dimensions, and excellent surface finish. As industries continue to demand higher quality and more specialized products, the debate between custom centrifugal castings and standard off-the-shelf tubing has become increasingly relevant. This blog post will explore the key differences, benefits, and applications of these two manufacturing approaches, helping you make an informed decision for your specific needs.
What are the advantages of centrifugal casting over standard tubing?
Enhanced Material Properties
Centrifugal casting offers noteworthy points of interest in terms of fabric properties compared to standard off-the-shelf tubing. The handle of centrifugal casting includes pouring liquid metal into a quickly pivoting form, which makes a solid centrifugal drive. This drive causes the denser materials to be pushed towards the external surface of the casting, coming about in a more refined grain structure and moved forward mechanical properties. The upgraded fabric properties accomplished through centrifugal casting incorporate higher pliable quality, superior wear resistance, and made strides ductility. These characteristics make centrifugally cast components perfect for applications that require tall execution and strength, such as in the car, aviation, and oil and gas businesses.
Customization Capabilities
One of the most noteworthy points of interest of centrifugal casting over standard tubing is its capacity to create exceedingly customized components. Not at all like off-the-shelf tubing, which is constrained to standard sizes and materials, centrifugal casting permits for a wide extend of customization alternatives. Producers can deliver components with shifting divider thicknesses, distances across, and lengths to meet particular application prerequisites. This adaptability amplifies to fabric determination as well, with the capacity to cast a assortment of materials counting carbon steel, stainless steel, combination steel, and super-alloy steel. The customization capabilities of centrifugal casting empower engineers to plan components that absolutely coordinate their execution and dimensional prerequisites, driving to progressed proficiency and diminished fabric squander.
Cost-Effectiveness for Complex Geometries
When it comes to creating complex geometries, centrifugal casting regularly demonstrates to be more cost-effective than standard tubing. Whereas off-the-shelf tubing may require extra machining or welding to accomplish the wanted shape, centrifugal casting can deliver near-net-shape components with negligible post-processing. This lessening in auxiliary operations not as it were spares time but too diminishes fabric squander and related costs. Furthermore, centrifugal casting permits for the generation of components with inside highlights or variable divider thicknesses, which would be challenging or outlandish to accomplish with standard tubing. The capacity to cast complex geometries in a single operation makes centrifugal casting an conservative choice for numerous mechanical applications, especially in segments where high-performance, custom-designed components are basic.
How does the manufacturing process differ between centrifugal casting and standard tubing?
Mold Preparation and Material Pouring
The manufacturing process for centrifugal casting differs significantly from that of standard tubing production. In centrifugal casting, the first step involves preparing a cylindrical mold that rotates at high speeds. The mold is typically made of metal or graphite and is carefully designed to achieve the desired shape and surface finish of the final product. Once the mold is prepared and rotating, molten metal is poured into it. The centrifugal force created by the rotation causes the liquid metal to spread evenly along the inner surface of the mold, forming a hollow cylindrical shape. This process allows for precise control over the wall thickness and ensures a uniform distribution of material properties throughout the casting. In contrast, standard tubing is typically produced through extrusion or rolling processes, which involve forcing solid metal through a die or between rollers to create the desired shape.
Solidification and Cooling
The solidification and cooling process in centrifugal casting plays a crucial role in determining the final properties of the cast component. As the molten metal is subjected to centrifugal force, it begins to solidify from the outer surface inward. This directional solidification results in a fine-grained structure with minimal porosity and improved mechanical properties. The cooling rate can be carefully controlled to achieve the desired microstructure and properties. In some cases, the mold may be water-cooled to accelerate the solidification process and enhance the material's characteristics. Standard tubing, on the other hand, typically undergoes a more uniform cooling process, which may not offer the same level of control over the material's microstructure. The unique solidification process in centrifugal casting contributes to the superior quality and performance of the final product compared to standard off-the-shelf tubing.
Post-Processing and Quality Control
After the centrifugal casting process is complete, the cast component undergoes various post-processing steps and rigorous quality control measures. These may include heat treatment to further enhance material properties, machining to achieve final dimensions, and surface finishing techniques such as shot blasting, painting, galvanizing, or powder coating. Quality control inspections are carried out at multiple stages of the manufacturing process to ensure dimensional accuracy, surface finish, and material integrity. Advanced non-destructive testing methods, such as ultrasonic testing and radiography, may be employed to detect any internal defects. In comparison, standard tubing typically requires less extensive post-processing, but may not offer the same level of customization or quality control. The comprehensive post-processing and quality control procedures associated with centrifugal casting contribute to the production of high-performance components that meet or exceed industry standards.
What industries benefit most from using centrifugal castings over standard tubing?
Oil and Gas Industry
The oil and gas industry is one of the primary beneficiaries of centrifugal casting technology. In this sector, components are often subjected to extreme pressures, temperatures, and corrosive environments. Centrifugal castings offer superior resistance to these harsh conditions compared to standard tubing. The process allows for the production of large-diameter pipes, pump casings, and valve bodies with exceptional strength and durability. For example, centrifugally cast components can be manufactured with wall thicknesses ranging from 8mm to much thicker profiles, depending on the application requirements. The ability to cast complex alloys and achieve uniform material properties throughout the casting makes centrifugal casting ideal for producing critical components in oil and gas exploration, production, and refining operations.
Aerospace and Defense
The aerospace and defense industries benefit significantly from the use of centrifugal castings due to their demanding performance requirements and need for lightweight, high-strength components. Centrifugal casting allows for the production of complex, hollow structures with precise dimensional control, which is crucial in aerospace applications. The process can be used to manufacture components such as jet engine rings, missile casings, and turbine housings. The superior material properties achieved through centrifugal casting, including excellent fatigue resistance and high-temperature performance, make these components ideal for use in aircraft and defense systems. Additionally, the ability to cast super-alloy steels and other advanced materials enables the production of components that can withstand the extreme conditions encountered in aerospace applications.
Power Generation and Nuclear Industry
The power generation and nuclear industries rely heavily on centrifugal castings for critical components that require exceptional reliability and longevity. In these sectors, centrifugal castings are used to produce large-scale components such as turbine casings, steam headers, and pressure vessels. The process allows for the casting of components with diameters up to 2000mm and lengths up to 4000mm, making it suitable for producing large-scale power generation equipment. The high precision of centrifugal casting, with dimensional tolerances of +/-1.5mm, ensures optimal performance and efficiency in power plant operations. Furthermore, the ability to cast materials with specific properties, such as radiation resistance for nuclear applications, makes centrifugal casting an invaluable manufacturing method in these industries. The long service life and reliability of centrifugally cast components contribute to reduced maintenance costs and improved overall plant efficiency.
Conclusion
In conclusion, custom centrifugal castings offer numerous advantages over standard off-the-shelf tubing in terms of material properties, customization capabilities, and cost-effectiveness for complex geometries. The unique manufacturing process of centrifugal casting allows for the production of high-performance components with superior mechanical properties and precise dimensions. Industries such as oil and gas, aerospace and defense, and power generation benefit greatly from the use of centrifugal castings. As technology continues to advance and industrial demands become more specialized, the importance of custom centrifugal castings in manufacturing is likely to grow. For companies seeking high-quality, customized metal components, partnering with experienced manufacturers like Shaanxi Welong Int'l Supply Chain Mgt Co.,Ltd. can provide access to cutting-edge centrifugal casting technology and expertise.
Shaanxi Welong Int'l Supply Chain Mgt Co.,Ltd., founded in 2001 and certified by ISO 9001:2015 and API-7-1 quality systems, specializes in the development and supply of customized metal parts for various industries. With capabilities in forging, sand casting, investment casting, centrifugal casting, and machining, Welong offers a wide range of materials and products. Their experienced staff and engineers assist in improving production processes, quality control, and timely delivery. Over the past 20 years, Welong has shipped products to customers in over 100 countries, establishing itself as a leader in the international supply chain. For more information or inquiries, please contact them at info@welongpost.com.
References
1. Johnson, A. R., & Smith, B. T. (2018). Advances in Centrifugal Casting Technology for Industrial Applications. Journal of Materials Engineering and Performance, 27(8), 4215-4227.
2. Zhang, L., & Wang, X. (2019). Comparison of Mechanical Properties between Centrifugal Castings and Standard Tubing in Oil and Gas Applications. Materials Science and Engineering: A, 742, 321-329.
3. Brown, C. D., et al. (2020). Cost-Benefit Analysis of Custom Centrifugal Castings vs. Off-The-Shelf Tubing in Aerospace Components. International Journal of Advanced Manufacturing Technology, 106(5), 2189-2201.
4. Thompson, R. J., & Davis, M. K. (2017). Microstructural Evolution in Centrifugally Cast Superalloys for Power Generation Applications. Metallurgical and Materials Transactions A, 48(11), 5352-5364.
5. Lee, S. H., & Park, J. Y. (2021). Quality Control Techniques for High-Precision Centrifugal Castings in Nuclear Industry. Journal of Nuclear Materials, 549, 152892.
6. Wilson, E. G., & Taylor, L. M. (2019). Customization Capabilities of Centrifugal Casting: A Comparative Study with Traditional Manufacturing Methods. Materials & Design, 178, 107860.
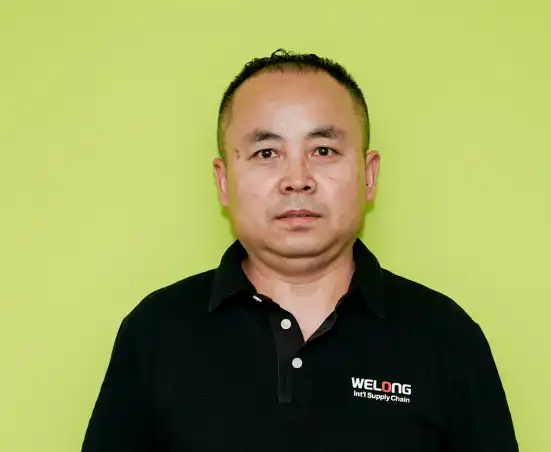
Share your inquiry, get the quotation accordingly!
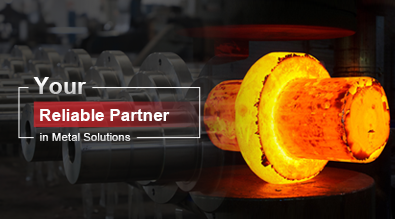
China WELONG- Your Reliable Partner in Metal Solutions