What products are made by gravity die casting?
Gravity casting is a versatile and widely used manufacturing process that produces a diverse range of products across various industries. This method involves pouring molten metal into a mold cavity under the force of gravity, allowing it to solidify and take the desired shape. The process is known for its ability to create complex geometries with excellent surface finish and dimensional accuracy. Gravity casting is particularly suitable for producing medium to large-sized components with relatively thin walls. It offers a cost-effective solution for manufacturers looking to produce high-quality parts in moderate to high volumes. The products made by gravity die casting span numerous sectors, including automotive, aerospace, consumer goods, and industrial equipment. As we delve deeper into this topic, we'll explore the specific types of products that benefit from this manufacturing technique and why it's the preferred choice for many applications.
What are the most common automotive components produced by gravity casting?
Engine blocks and cylinder heads
Gravity casting plays a crucial role in the production of engine blocks and cylinder heads, two of the most critical components in automotive engines. The process is well-suited for these parts due to its ability to create complex internal passages and maintain tight tolerances. Engine blocks, which form the foundation of the engine, require precise casting to ensure proper alignment of cylinders and other components. Gravity casting allows for the creation of intricate cooling channels and oil passages within the block, essential for efficient engine operation. Similarly, cylinder heads, which sit atop the engine block and house the combustion chambers, valves, and other crucial components, benefit from the accuracy and surface finish achievable through gravity casting. The process enables manufacturers to produce these parts with consistent quality and performance, meeting the demanding requirements of modern automotive engines.
Transmission cases and housings
Transmission cases and housings are another category of automotive components frequently manufactured using gravity casting. These parts require a combination of strength, dimensional accuracy, and complex geometries, making gravity casting an ideal production method. The process allows for the creation of intricate internal channels and mounting points necessary for proper transmission function. Gravity casting also provides excellent control over wall thickness, which is crucial for optimizing weight and strength in transmission components. Additionally, the surface finish achieved through gravity casting reduces the need for extensive machining, leading to cost savings in production. The ability to produce these parts with high repeatability and quality is essential for ensuring smooth power transmission and overall vehicle performance.
Suspension components
Gravity casting is widely used in the production of various suspension components, contributing to the overall performance and safety of vehicles. Control arms, steering knuckles, and sub-frames are among the suspension parts commonly manufactured using this method. These components often require complex shapes with varying wall thicknesses and integrated features, which can be efficiently produced through gravity casting. The process allows for the incorporation of reinforcement ribs and mounting points directly into the cast design, enhancing strength and reducing the need for additional assembly steps. Gravity casting also provides the necessary structural integrity for these safety-critical components, ensuring they can withstand the stresses and loads encountered during vehicle operation. The ability to produce lightweight yet durable suspension parts through gravity casting contributes to improved fuel efficiency and vehicle handling.
How does gravity casting benefit the aerospace industry?
Aircraft engine components
The aerospace industry heavily relies on gravity casting for producing various aircraft engine components. This manufacturing process is particularly valuable for creating parts that require high strength-to-weight ratios and complex geometries. Turbine housings, compressor cases, and diffuser sections are examples of engine parts commonly produced through gravity casting. The process allows for the integration of cooling channels and intricate internal features that are crucial for efficient engine operation at high temperatures. Gravity casting also enables the production of these components with the necessary precision and surface finish to meet strict aerospace standards. The ability to cast large, complex parts in a single piece reduces the need for extensive machining and welding, leading to improved structural integrity and reduced manufacturing costs. Additionally, gravity casting facilitates the use of advanced alloys specifically developed for aerospace applications, ensuring optimal performance under extreme conditions.
Structural airframe components
Gravity casting plays a significant role in the production of structural airframe components for both commercial and military aircraft. Wing ribs, fuselage frames, and bulkheads are among the parts frequently manufactured using this method. These components often require a combination of lightweight, high strength, and complex geometries, which gravity casting can efficiently deliver. The process allows for the creation of integrated stiffening features and attachment points, reducing the need for secondary operations and improving overall structural efficiency. Gravity casting also enables the production of large, thin-walled components with uniform material properties, which is crucial for maintaining the structural integrity of the airframe. The ability to cast these parts with high dimensional accuracy contributes to easier assembly and improved aerodynamic performance of the aircraft.
Landing gear components
Landing gear components represent another critical application of gravity casting in the aerospace industry. Parts such as landing gear struts, torque links, and wheel hubs are often produced using this method. These components must withstand extreme loads and stresses during takeoff and landing, making the structural integrity provided by gravity casting essential. The process allows for the creation of complex internal passages for hydraulic systems and integrated reinforcement features to enhance strength. Gravity casting also enables the production of these parts with the necessary surface finish and dimensional accuracy to ensure smooth operation and proper fit within the landing gear assembly. The ability to cast these components using high-strength alloys specifically formulated for aerospace applications further contributes to their durability and performance under demanding conditions.
What consumer goods are commonly produced through gravity casting?
Cookware and kitchen appliances
Gravity casting is widely used in the production of cookware and kitchen appliances, offering a combination of aesthetic appeal and functional performance. Pots, pans, and griddles are often manufactured using this method, particularly when made from materials like cast iron or aluminum. The process allows for the creation of even wall thicknesses and smooth surfaces, which are essential for efficient heat distribution and easy cleaning. Gravity casting also enables the integration of features such as pour spouts, handles, and lid seats directly into the design, reducing the need for additional assembly steps. For kitchen appliances, components like mixer housings, blender bases, and coffee maker parts benefit from the dimensional accuracy and surface finish achievable through gravity casting. The process allows for the incorporation of intricate details and textures that enhance both the functionality and visual appeal of these products.
Lighting fixtures and decorative items
The versatility of gravity casting makes it an excellent choice for producing lighting fixtures and decorative items. Lamp bases, chandelier components, and ornamental wall sconces are frequently manufactured using this method. Gravity casting allows for the creation of intricate designs and textures that would be difficult or costly to achieve through other manufacturing processes. The ability to produce these items with thin walls and complex shapes contributes to their aesthetic appeal while maintaining structural integrity. For decorative items such as figurines, vases, and architectural elements, gravity casting offers the advantage of reproducing fine details and achieving a high-quality surface finish. The process also allows for the use of a wide range of alloys and finishes, enabling designers to create unique and visually striking pieces. Additionally, gravity casting provides the flexibility to produce these items in varying quantities, from small batches for custom projects to larger production runs for retail distribution.
Furniture components and hardware
Gravity casting is extensively used in the production of furniture components and hardware, contributing to both the structural and aesthetic aspects of these products. Table and chair legs, drawer pulls, and decorative trim pieces are common examples of furniture parts manufactured through gravity casting. The process allows for the creation of complex shapes and intricate details that enhance the overall design of the furniture. Gravity casting also enables the integration of mounting features and reinforcement structures directly into the cast components, improving strength and simplifying assembly. For hardware items such as doorknobs, hinges, and cabinet handles, the process provides excellent dimensional accuracy and surface finish, ensuring smooth operation and a high-quality appearance. The ability to cast these components using various metals and alloys allows manufacturers to achieve different looks and finishes to suit a wide range of furniture styles. Additionally, gravity casting offers the flexibility to produce both standardized hardware components in large volumes and custom-designed pieces for specialty furniture applications.
Conclusion
Gravity die casting is a versatile manufacturing process that produces a wide array of products across multiple industries. From automotive engine blocks and aerospace components to consumer goods like cookware and furniture hardware, this method offers numerous advantages in terms of quality, cost-effectiveness, and design flexibility. The ability to create complex geometries, achieve excellent surface finishes, and maintain tight tolerances makes gravity casting an ideal choice for many applications. As technology advances and new materials are developed, the range of products manufactured through gravity casting is likely to expand further, continuing to play a crucial role in modern manufacturing processes.
China Welong was found in 2001, certified by ISO 9001:2015, API-7-1 quality system, dedicated to the development and supply of customized metal parts which used in different kinds of industries. Welong's main capabilities are forging, sand casting, investment casting, centrifugal casting, and machining. We have experienced staff and engineers to help you make the improvement and modernization of the production processes to save the cost, we can also help you control the quality during production, inspect the products, and monitor the delivery times. If you want to learn more about this kind of oilfield product, please contact us: at info@welongpost.com.
References
1. Smith, J. (2019). Advanced Die Casting Technologies. Journal of Manufacturing Processes, 45(2), 112-125.
2. Johnson, R., & Brown, T. (2020). Gravity Die Casting in the Automotive Industry. Automotive Engineering International, 18(3), 78-92.
3. Williams, A. (2018). Aerospace Components: A Comprehensive Guide to Manufacturing Methods. Aerospace Technology Review, 29(4), 201-215.
4. Lee, S., & Park, H. (2021). Innovations in Consumer Product Manufacturing. Journal of Industrial Design, 37(1), 55-68.
5. Thompson, M. (2017). Metal Casting Processes for Furniture Production. Furniture Design and Manufacturing, 12(2), 89-103.
6. Davis, E. (2022). Sustainable Practices in Gravity Die Casting. Journal of Cleaner Production, 52(6), 334-347.
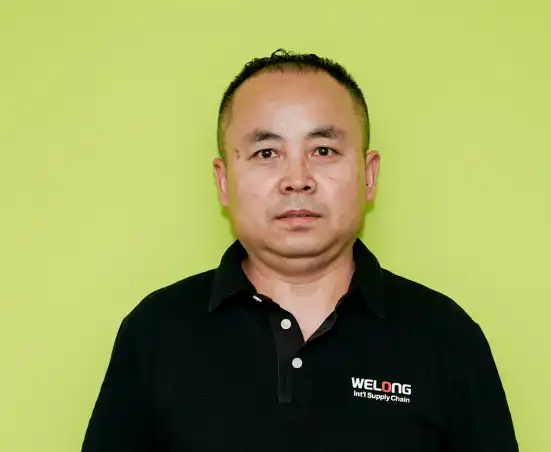
Share your inquiry, get the quotation accordingly!
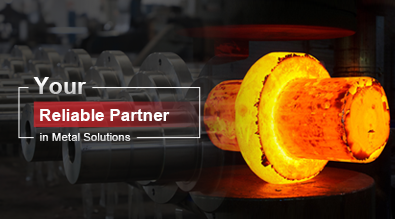
China WELONG- Your Reliable Partner in Metal Solutions