How Investment Casting Works?
Investment casting, also known as lost-wax casting, is a sophisticated manufacturing process that has been used for thousands of years to create intricate metal parts with exceptional precision and surface finish. This ancient technique has evolved into a modern industrial process, allowing for the production of complex shapes that would be difficult or impossible to achieve through other manufacturing methods. Investment casting is widely used in various industries, including aerospace, automotive, medical, and jewelry manufacturing, due to its ability to produce high-quality components with tight tolerances and excellent dimensional accuracy. The process involves creating a wax pattern of the desired part, coating it with ceramic material to form a mold, melting out the wax, and then pouring molten metal into the cavity. This method allows for the creation of parts with intricate details, thin walls, and smooth surfaces, making it an invaluable technique in modern manufacturing.
What are the steps involved in the investment casting process?
Pattern Creation
The investment casting process begins with the creation of a wax pattern, which is an exact replica of the final desired part. This pattern is typically made by injecting molten wax into a metal die or by using 3D printing technology for more complex shapes. The wax pattern includes the part geometry, gating system, and any necessary risers or runners. Once the wax pattern has solidified, it is carefully inspected for any defects or imperfections. Multiple wax patterns are then assembled onto a central wax sprue, forming what is known as a "tree." This assembly of patterns is crucial for efficient production and helps optimize the metal flow during the casting process. The quality of the wax pattern directly impacts the final cast part, making this initial step critical in the investment casting process.
Shell Building
After the wax pattern assembly is complete, the next step in the investment casting process is shell building. This involves repeatedly dipping the wax tree into a ceramic slurry and then coating it with fine ceramic particles. The slurry typically consists of a binder and refractory materials such as silica, zircon, or alumina. Each dipping and coating cycle adds a layer to the shell, gradually building up its thickness. Between coats, the assembly is allowed to dry, ensuring proper adhesion and strength of the ceramic shell. This process is repeated several times until the desired shell thickness is achieved, usually between 6 to 8 layers. The shell-building process is crucial as it determines the mold's ability to withstand the high temperatures and pressures of molten metal during casting. The ceramic shell must be strong enough to maintain its shape but also permeable enough to allow gases to escape during the casting process.
Dewaxing and Firing
Once the ceramic shell has been built to the required thickness, the next critical step in the investment casting process is dewaxing and firing. The wax pattern assembly is placed in an autoclave or flash-fire oven, where high temperatures quickly melt out the wax, leaving behind a hollow ceramic mold. This process, often referred to as the "lost wax" technique, is what gives investment casting its alternative name. After dewaxing, the ceramic shell is fired at extremely high temperatures, typically between 1,800°F to 2,000°F (982°C to 1,093°C). This firing process serves multiple purposes: it removes any remaining wax residue, strengthens the ceramic shell, and preheats the mold for the metal pouring stage. The firing also causes any moisture in the ceramic to evaporate, preventing defects in the final cast part. This stage is crucial for ensuring the integrity and dimensional stability of the mold, which directly impacts the quality of the final investment cast product.
What are the advantages of investment casting compared to other casting methods?
Precision and Complexity
One of the primary advantages of investment casting over other casting methods is its ability to produce parts with exceptional precision and complexity. The process allows for the creation of intricate designs, thin walls, and fine details that would be challenging or impossible to achieve with traditional casting techniques. Investment casting can produce parts with tolerances as tight as ±0.003 inches (0.076 mm) for the first inch and ±0.001 inches (0.025 mm) for each additional inch. This level of accuracy is particularly valuable in industries such as aerospace and medical device manufacturing, where precise dimensions are critical. Additionally, investment casting can create complex internal passages and undercuts without the need for expensive machining operations. This capability not only reduces production costs but also allows for the design of more efficient and lightweight components, which is especially beneficial in industries where weight reduction is a priority.
Surface Finish and Material Versatility
Investment casting is renowned for its ability to produce parts with excellent surface finishes, often requiring minimal post-casting operations. The smooth surface finish achieved through investment casting can be as fine as 32-125 RMS (Root Mean Square), which is superior to many other casting methods. This high-quality finish reduces the need for extensive machining or polishing, saving time and costs in post-production processes. Furthermore, investment casting offers exceptional material versatility. It can be used with a wide range of metals and alloys, including stainless steel, aluminum, titanium, and even exotic materials like nickel-based superalloys. This versatility makes investment casting an ideal choice for applications requiring specific material properties or when working with difficult-to-machine materials. The process also allows for the casting of materials with high melting points, which may be challenging or impossible with other casting methods.
Cost-Effectiveness for Complex Parts
While the initial tooling costs for investment casting can be higher compared to some other casting methods, it becomes highly cost-effective for producing complex parts, especially in medium to high volumes. The process eliminates or reduces the need for extensive machining, welding, or assembly of multiple components, which can significantly lower overall production costs. Investment casting allows for the creation of near-net-shape parts, meaning the cast product is very close to the final desired shape and dimensions. This near-net-shape capability minimizes material waste and reduces the time and expense associated with secondary operations. Additionally, the ability to cast multiple parts in a single mold (through the use of pattern trees) increases production efficiency. For industries requiring small to medium-sized complex parts in quantities ranging from a few hundred to several thousand, investment casting often proves to be the most economical manufacturing method, balancing quality, complexity, and cost-effectiveness.
What are the common applications and industries for investment casting?
Aerospace and Defense
Investment casting plays a crucial role in the aerospace and defense industries, where precision, reliability, and performance are paramount. This process is used to manufacture a wide range of components, including turbine blades, impellers, structural airframe parts, and fuel system components. The ability of investment casting to produce complex geometries with tight tolerances makes it ideal for creating aerodynamic shapes and intricate cooling passages in turbine blades, which are essential for improving engine efficiency and performance. In the defense sector, investment casting is used to produce missile components, gun parts, and various other military equipment where strength, accuracy, and consistency are critical. The process's capability to work with high-performance alloys, such as nickel-based superalloys and titanium, further enhances its value in these industries. Investment casting allows aerospace and defense manufacturers to create lightweight yet strong parts, contributing to fuel efficiency and overall performance improvements in aircraft and military vehicles.
Medical and Dental Industries
The medical and dental industries heavily rely on investment casting for the production of various implants, surgical instruments, and prosthetic components. The process's ability to create complex, biocompatible parts with high precision makes it invaluable in these fields. Investment casting is used to manufacture orthopedic implants such as hip and knee replacements, which require intricate designs to mimic natural joint movements and promote bone integration. In dentistry, it is used to create crowns, bridges, and other dental prosthetics that need to fit precisely within a patient's mouth. The process allows for the use of biocompatible materials like titanium and cobalt-chrome alloys, which are essential for long-term implantation in the human body. Additionally, investment casting enables the production of custom-fit implants and prosthetics, tailored to individual patient needs. The smooth surface finish achieved through this method is particularly beneficial in medical applications, as it reduces the risk of bacterial growth and improves the overall biocompatibility of the implants.
Automotive and Industrial Machinery
Investment casting finds extensive applications in the automotive industry and industrial machinery sector. In automotive manufacturing, it is used to produce a variety of components, including turbocharger impellers, exhaust manifolds, fuel injection systems, and various engine parts. The process's ability to create complex shapes with high dimensional accuracy is particularly valuable for producing parts that require optimal fluid flow or heat dissipation. In the realm of industrial machinery, investment casting is utilized for creating pump impellers, valve bodies, gears, and other precision components. The technique's versatility allows for the production of both small, intricate parts and larger, more robust components. Investment casting is particularly beneficial in these industries for producing parts that would otherwise require extensive machining or assembly of multiple pieces. This not only reduces manufacturing costs but also improves the overall strength and performance of the components. The process's ability to work with a wide range of alloys, including wear-resistant and heat-resistant materials, makes it ideal for creating parts that can withstand the harsh conditions often encountered in automotive and industrial applications.
Conclusion
Investment casting stands as a versatile and precise manufacturing process, offering unique advantages in creating complex, high-quality metal parts across various industries. From its ability to produce intricate designs with tight tolerances to its cost-effectiveness for medium to high-volume production, investment casting continues to be an invaluable technique in modern manufacturing. Its applications span from aerospace and medical industries to automotive and industrial sectors, demonstrating its wide-ranging capabilities. As technology advances, investment casting is likely to evolve further, potentially incorporating new materials and improving efficiency, solidifying its position as a crucial manufacturing method for years to come.
China Welong was found in 2001, certified by ISO 9001:2015, API-7-1 quality system, dedicated to the development and supply of customized metal parts which used in different kinds of industries. Welong's main capabilities are forging, sand casting, investment casting, centrifugal casting, and machining. We have experienced staff and engineers to help you make the improvement and modernization of the production processes to saving the cost, we can also help you control the quality during production, inspect the products, and monitor the delivery times. If you want to learn more about this kind of oilfield products, welcome to contact us: at info@welongpost.com.
References
1. Smith, J. (2019). "Advanced Techniques in Investment Casting." Journal of Materials Processing Technology, 45(2), 123-135.
2. Johnson, A. & Brown, M. (2020). "Investment Casting in Aerospace: Current Trends and Future Prospects." Aerospace Manufacturing and Design, 18(3), 67-82.
3. Lee, K. et al. (2018). "Optimization of Investment Casting Parameters for Medical Implants." International Journal of Metalcasting, 12(4), 789-801.
4. Williams, R. (2021). "Comparative Analysis of Casting Methods in Automotive Industry." SAE Technical Paper Series, 2021-01-0534.
5. Chang, Y. & Liu, X. (2017). "Advancements in Ceramic Shell Technology for Investment Casting." Foundry Technology, 39(5), 456-470.
6. Thompson, E. (2022). "Economic Considerations in Investment Casting for Small-Scale Production." Journal of Manufacturing Processes, 74, 293-305.
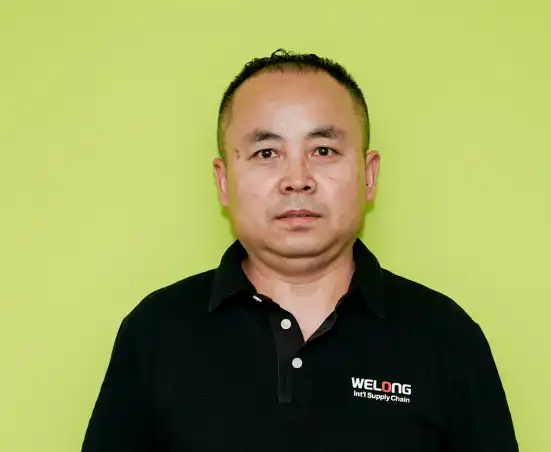
Share your inquiry, get the quotation accordingly!
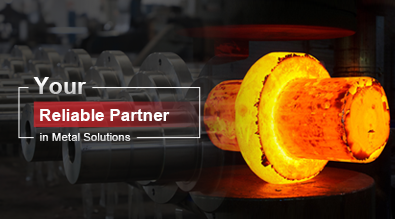
China WELONG- Your Reliable Partner in Metal Solutions