The 3 Types of Sand Used for Sand Casting
Sand casting is a versatile and widely used manufacturing process that has been employed for centuries to create complex metal parts. At the heart of this process lies the crucial element of sand, which serves as the mold material. The choice of sand type plays a pivotal role in determining the quality, accuracy, and surface finish of the final cast product. In this comprehensive exploration, we will delve into the three primary types of sand used in sand casting: silica sand, chromite sand, and zircon sand. Each of these sand types possesses unique properties and characteristics that make them suitable for different casting applications. Understanding the distinctions between these sand varieties is essential for foundry professionals and engineers alike, as it enables them to select the most appropriate sand for their specific casting requirements. By examining the properties, advantages, and limitations of each sand type, we can gain valuable insights into how they influence the sand casting process and the resulting cast products.
What are the key properties of silica sand in sand casting?
Composition and characteristics of silica sand
Silica sand, also known as quartz sand, is the most commonly used type of sand in sand casting processes. Its composition primarily consists of silicon dioxide (SiO2), which gives it unique properties that make it ideal for many casting applications. The grains of silica sand are typically angular or sub-angular in shape, providing good interlocking capabilities when compacted. This characteristic is crucial in sand casting, as it helps maintain the integrity of the mold during the pouring of molten metal. Silica sand also exhibits excellent thermal stability, with a high melting point of around 1,700°C (3,092°F), which allows it to withstand the extreme temperatures involved in metal casting without significant degradation.
Advantages of using silica sand in sand casting
One of the primary advantages of using silica sand in sand casting is its widespread availability and relatively low cost compared to other sand types. This makes it an economical choice for foundries, especially for large-scale production. Silica sand also offers good permeability, which is essential for allowing gases to escape during the casting process, reducing the likelihood of defects in the final product. Its high thermal conductivity helps in rapidly dissipating heat from the molten metal, promoting faster solidification and potentially improving the mechanical properties of the cast part. Additionally, silica sand can be easily reclaimed and reused multiple times, further enhancing its cost-effectiveness in sand casting operations.
Limitations and considerations when using silica sand
Despite its many advantages, silica sand does have some limitations that need to be considered in sand casting applications. One of the primary concerns is its tendency to expand when heated, which can lead to dimensional inaccuracies in the cast product if not properly managed. This expansion is due to the transformation of quartz at high temperatures, a phenomenon known as "silica inversion." To mitigate this issue, foundries often employ additives or binders to control the expansion of silica sand. Another consideration is the potential health hazard posed by respirable silica dust, which can cause lung diseases such as silicosis. Proper safety measures and dust control systems are essential when working with silica sand in sand casting operations to protect workers' health and ensure compliance with occupational safety regulations.
How does chromite sand enhance the sand casting process?
Composition and unique properties of chromite sand
Chromite sand is a specialized type of sand used in sand casting, particularly for applications requiring higher thermal stability and improved surface finish. Composed primarily of chromium oxide (Cr2O3) and iron oxide (FeO), chromite sand offers distinct advantages over silica sand in certain casting scenarios. The grains of chromite sand are typically more rounded and have a higher specific gravity compared to silica sand, which contributes to its excellent flowability and compactability in mold-making. These properties are crucial in sand casting, as they allow for the creation of intricate mold details and smooth surfaces on the cast product. Chromite sand also exhibits exceptional thermal stability, with a melting point exceeding 2,000°C (3,632°F), making it suitable for casting high-temperature alloys.
Benefits of chromite sand in high-temperature casting
One of the primary benefits of using chromite sand in sand casting is its superior performance in high-temperature applications. Unlike silica sand, chromite sand does not undergo significant volume changes when exposed to extreme heat, resulting in improved dimensional accuracy of the cast parts. This characteristic is particularly valuable when casting alloys with high melting points, such as stainless steel or heat-resistant alloys. The high thermal conductivity of chromite sand also promotes rapid heat dissipation, which can lead to improved solidification rates and enhanced mechanical properties of the cast product. Additionally, chromite sand's resistance to metal penetration helps prevent defects such as veining and metal penetration, resulting in smoother cast surfaces and reduced need for post-casting finishing operations.
Challenges and considerations in using chromite sand
While chromite sand offers numerous advantages in sand casting, there are some challenges and considerations to keep in mind. The most significant drawback is its higher cost compared to silica sand, which can impact the overall economics of the casting process, especially for large-scale production. The higher density of chromite sand also means that more energy is required for sand handling and reclamation processes. Furthermore, the availability of high-quality chromite sand may be limited in some regions, potentially leading to supply chain challenges for foundries. When using chromite sand in sand casting, it's essential to optimize the sand-to-metal ratio and adjust molding parameters to account for its unique properties. Proper sand management and reclamation practices are also crucial to maximize the economic benefits of using chromite sand in casting operations.
What role does zircon sand play in precision sand casting?
Characteristics and composition of zircon sand
Zircon sand, composed primarily of zirconium silicate (ZrSiO4), is a specialized sand type that plays a crucial role in precision sand casting applications. Known for its exceptional refractoriness and chemical inertness, zircon sand offers unique properties that make it invaluable for casting complex and high-quality metal components. The grains of zircon sand are typically more spherical and have a higher specific gravity compared to both silica and chromite sands. This characteristic contributes to its excellent flowability and compactability, allowing for the creation of intricate mold details and smooth surfaces in sand casting processes. Zircon sand also boasts a high melting point of around 2,200°C (3,992°F), making it suitable for casting a wide range of alloys, including those with high melting temperatures.
Advantages of zircon sand in producing high-quality castings
One of the primary advantages of using zircon sand in sand casting is its ability to produce castings with superior surface finish and dimensional accuracy. The high thermal stability of zircon sand minimizes expansion-related defects, resulting in castings with tighter tolerances and reduced need for post-casting machining. Its excellent refractoriness allows for the casting of high-temperature alloys without the risk of sand fusion or metal penetration, which can lead to surface defects. Zircon sand's low thermal expansion coefficient also contributes to improved dimensional stability of the mold during the casting process. Additionally, the chemical inertness of zircon sand makes it resistant to reaction with most molten metals, reducing the likelihood of metal-mold interactions that can compromise casting quality. These properties make zircon sand particularly valuable in the production of precision components for industries such as aerospace, automotive, and medical devices.
Economic considerations and specialized applications of zircon sand
While zircon sand offers numerous benefits in sand casting, its use is often limited by economic considerations. The cost of zircon sand is significantly higher than that of silica or chromite sand, which can impact the overall production costs, especially for large castings or high-volume production runs. As a result, zircon sand is typically reserved for specialized applications where its unique properties provide substantial advantages that justify the additional expense. These applications often include the casting of thin-walled components, parts with intricate details, or those requiring exceptional surface finish and dimensional accuracy. To optimize the use of zircon sand in sand casting, foundries may employ techniques such as facing sands, where a thin layer of zircon sand is used on the mold surface, backed by less expensive sand types. This approach allows for the benefits of zircon sand while minimizing overall material costs in the sand casting process.
Conclusion
In conclusion, the choice of sand type in sand casting plays a crucial role in determining the quality, accuracy, and efficiency of the casting process. Silica sand remains the most widely used option due to its availability and cost-effectiveness, while chromite and zircon sands offer specialized properties for high-temperature and precision casting applications, respectively. Each sand type has its unique advantages and limitations, and the selection depends on factors such as the alloy being cast, required surface finish, dimensional accuracy, and economic considerations. By understanding the characteristics of these three sand types, foundry professionals can make informed decisions to optimize their sand casting processes and produce high-quality metal components tailored to specific industry requirements.
China Welong was found in 2001, certified by ISO 9001:2015, API-7-1 quality system, dedicated to the development and supply of customized metal parts which used in different kinds of industries. Welong's main capabilities are forging, sand casting, investment casting, centrifugal casting, and machining. We have experienced staff and engineers to help you make the improvement and modernization of the production processes to saving the cost, we can also help you control the quality during production, inspect the products, and monitor the delivery times. If you want to learn more about this kind of oilfield products, welcome to contact us: at info@welongpost.com.
References
1. Brown, J. R. (2000). Foseco Ferrous Foundryman's Handbook. Butterworth-Heinemann.
2. Beeley, P. (2001). Foundry Technology. Butterworth-Heinemann.
3. Campbell, J. (2003). Castings. Butterworth-Heinemann.
4. American Foundry Society. (2015). Mold & Core Test Handbook. AFS.
5. Jain, P. L. (2003). Principles of Foundry Technology. Tata McGraw-Hill Education.
6. Srinivasan, M. (2004). Science and Technology of Casting Processes. InTech.
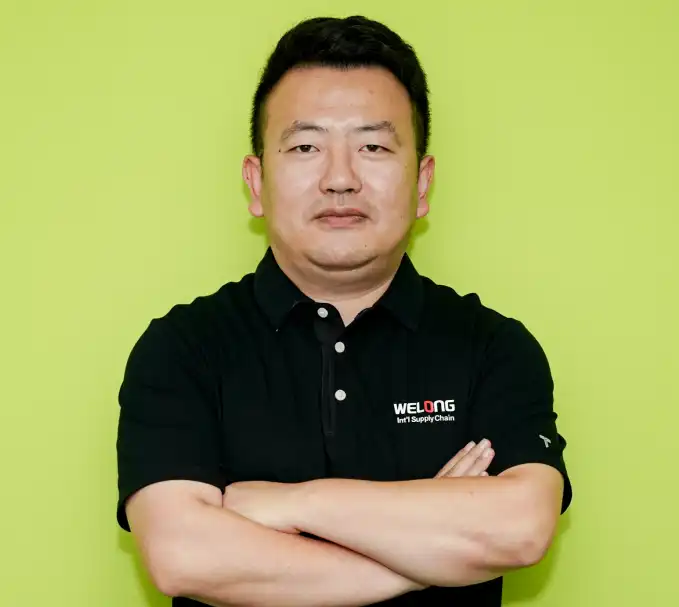
Share your inquiry, get the quotation accordingly!
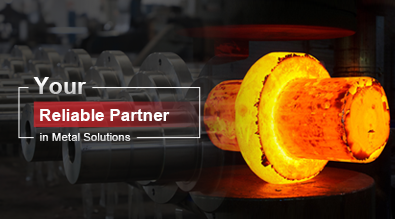
China WELONG- Your Reliable Partner in Metal Solutions