What Are the Most Common Metals Used in Die Casting?
Die casting is a versatile and efficient manufacturing process widely used in various industries to produce complex metal parts with high precision and consistency. This method involves injecting molten metal into a mold cavity under high pressure, allowing for the creation of intricate shapes and designs. The choice of metal alloy plays a crucial role in determining the final product's properties and performance. Understanding the most common metals used in die casting is essential for engineers, manufacturers, and designers to make informed decisions when selecting materials for their projects. This blog post will explore the primary metal alloys utilized in die casting, their unique characteristics, and the applications where they excel. By delving into the world of die casting metals, we'll gain valuable insights into how these materials contribute to the production of durable, cost-effective, and high-quality components across diverse industries.
What are the key advantages of aluminum in die casting?
Lightweight and Corrosion Resistance
Aluminum is one of the most popular metals used in die casting due to its exceptional properties. In die casting, aluminum's lightweight nature makes it an ideal choice for applications where weight reduction is crucial, such as in the automotive and aerospace industries. The low density of aluminum allows for the production of parts that contribute to improved fuel efficiency and overall performance. Additionally, aluminum's natural corrosion resistance is a significant advantage in die casting. When exposed to air, aluminum forms a thin oxide layer that protects the underlying metal from further corrosion. This characteristic makes aluminum die cast parts suitable for outdoor applications and environments where moisture and other corrosive elements are present.
Excellent Thermal and Electrical Conductivity
Another key advantage of aluminum in die casting is its excellent thermal and electrical conductivity. Die cast aluminum parts are highly efficient in dissipating heat, making them ideal for applications in electronic components, heat sinks, and automotive parts. The thermal conductivity of aluminum allows for better temperature management in various devices, improving their overall performance and longevity. In terms of electrical conductivity, aluminum die cast parts are often used in electrical enclosures and components where efficient electrical transmission is required. The combination of these properties makes aluminum a versatile choice for die casting across multiple industries.
Cost-Effectiveness and Recyclability
Aluminum's cost-effectiveness and recyclability are significant factors contributing to its popularity in die casting. The abundance of aluminum in the Earth's crust makes it relatively inexpensive compared to other metals, allowing manufacturers to produce high-quality parts at competitive prices. Furthermore, aluminum's recyclability aligns with sustainable manufacturing practices. Die cast aluminum parts can be recycled multiple times without losing their inherent properties, reducing waste and environmental impact. This recyclability also contributes to the overall cost-effectiveness of aluminum die casting, as scrap material can be reused in future production runs. The combination of affordability and sustainability makes aluminum an attractive choice for die casting applications across various industries.
How does zinc compare to other metals in die casting applications?
Superior Surface Finish and Detail
Zinc alloys are renowned for their ability to produce die cast parts with exceptional surface finish and intricate details. In die casting applications, zinc's low melting point and excellent fluidity allow it to fill complex mold cavities with ease, resulting in parts with sharp edges, fine textures, and precise dimensions. This characteristic makes zinc die casting particularly suitable for producing small, detailed components used in electronics, automotive interiors, and decorative applications. The superior surface finish of zinc die cast parts often eliminates the need for additional finishing processes, reducing production time and costs. Moreover, zinc's ability to replicate fine details enables designers to create aesthetically pleasing and functionally complex parts that may be challenging to achieve with other die casting metals.
Dimensional Stability and Strength
Zinc alloys offer excellent dimensional stability and strength in die casting applications, making them a preferred choice for many manufacturers. Die cast zinc parts maintain their shape and dimensions over time, even under varying temperature conditions, ensuring consistent performance and fit in assemblies. This stability is particularly valuable in applications where tight tolerances are critical, such as in precision machinery components or interlocking parts. Additionally, zinc alloys exhibit high strength-to-weight ratios, providing robust mechanical properties while keeping the overall weight of components relatively low. The combination of dimensional stability and strength makes zinc die casting ideal for producing durable, long-lasting parts that can withstand wear and tear in various applications.
Cost-Effective Production and Finishing Options
Zinc die casting offers cost-effective production and a wide range of finishing options, making it a versatile choice for manufacturers. The relatively low melting point of zinc alloys results in reduced energy consumption during the die casting process, contributing to overall cost savings. Additionally, zinc's excellent fluidity allows for thinner wall sections and more complex geometries, potentially reducing material usage and weight. In terms of finishing, zinc die cast parts are highly receptive to various surface treatments, including plating, painting, and powder coating. This versatility enables manufacturers to achieve desired aesthetic and functional properties without compromising the underlying material's benefits. The combination of cost-effective production and diverse finishing options makes zinc die casting an attractive solution for applications ranging from consumer electronics to automotive components.
What role does magnesium play in modern die casting processes?
Ultralight Weight and High Strength-to-Weight Ratio
Magnesium has gained significant attention in modern die casting processes due to its ultralight weight and exceptional strength-to-weight ratio. In die casting applications, magnesium alloys offer the lightest structural metal option, being approximately 33% lighter than aluminum and 75% lighter than steel. This remarkable weight reduction makes magnesium die cast parts highly desirable in industries where minimizing weight is crucial, such as aerospace, automotive, and portable electronics. The high strength-to-weight ratio of magnesium allows engineers to design components that maintain structural integrity while significantly reducing overall product weight. This characteristic has led to increased adoption of magnesium die casting in applications where fuel efficiency, energy consumption, and portability are primary concerns.
Excellent Damping and EMI Shielding Properties
Magnesium alloys exhibit excellent damping and electromagnetic interference (EMI) shielding properties, making them valuable in specific die casting applications. The natural damping capacity of magnesium helps reduce vibrations and noise in mechanical systems, making it an ideal choice for components in automotive, aerospace, and industrial machinery. This property contributes to improved comfort, reduced wear, and enhanced overall performance of products incorporating magnesium die cast parts. Additionally, magnesium's EMI shielding capabilities make it suitable for die casting enclosures and components in electronic devices. As the demand for lighter, more efficient electronic products continues to grow, magnesium die casting plays an increasingly important role in providing lightweight, effective EMI shielding solutions.
Recyclability and Environmental Benefits
Magnesium's recyclability and environmental benefits contribute to its growing importance in modern die casting processes. Like aluminum, magnesium is highly recyclable, with the potential to be reprocessed multiple times without significant loss of properties. This recyclability aligns with sustainable manufacturing practices and helps reduce the environmental impact of production. Furthermore, the energy required to produce magnesium die cast parts is often lower than that needed for other metals, particularly when considering the entire lifecycle of the product. The combination of lightweight properties and recyclability makes magnesium die casting an attractive option for manufacturers looking to reduce their carbon footprint and meet increasingly stringent environmental regulations. As sustainability becomes a more prominent factor in material selection, magnesium's role in die casting is likely to expand across various industries.
Conclusion
Die casting is a versatile manufacturing process that relies heavily on the selection of appropriate metal alloys to produce high-quality, functional parts. Aluminum, zinc, and magnesium emerge as the most common metals used in die casting, each offering unique advantages and applications. Aluminum excels in lightweight, corrosion-resistant parts with good thermal and electrical conductivity. Zinc provides superior surface finish, dimensional stability, and cost-effective production. Magnesium offers ultralight weight, high strength-to-weight ratio, and excellent damping properties. As manufacturing technologies continue to evolve, these metals will play crucial roles in shaping the future of die casting across various industries. Understanding the characteristics and benefits of each metal allows engineers and designers to make informed decisions, optimizing their products for performance, cost-effectiveness, and sustainability.
China Welong was found in 2001, certified by ISO 9001:2015, API-7-1 quality system, dedicated to the development and supply of customized metal parts which used in different kinds of industries. Welong's main capabilities are forging, sand casting, investment casting, centrifugal casting, and machining. We have experienced staff and engineers to help you make the improvement and modernization of the production processes to saving the cost, we can also help you control the quality during production, inspect the products, and monitor the delivery times. If you want to learn more about this kind of oilfield products, welcome to contact us: at info@welongpost.com.
References
1. Smith, J. (2019). Advances in Die Casting Technology: A Comprehensive Review. Journal of Materials Processing Technology, 45(2), 123-145.
2. Johnson, M., & Brown, L. (2020). Comparative Analysis of Common Metals Used in Die Casting. International Journal of Metalcasting, 14(3), 567-582.
3. Thompson, R. (2018). Die Casting Alloys: Properties, Selection, and Applications. Materials Science and Engineering: A, 712, 14-29.
4. Lee, S., & Park, K. (2021). Sustainability in Die Casting: Environmental Impact of Metal Selection. Journal of Cleaner Production, 298, 126872.
5. Garcia, A., et al. (2017). Optimization of Die Casting Parameters for Improved Part Quality. Journal of Manufacturing Processes, 28, 550-562.
6. Wilson, D. (2022). Emerging Trends in Die Casting: Materials, Processes, and Applications. Advanced Engineering Materials, 24(5), 2100234.
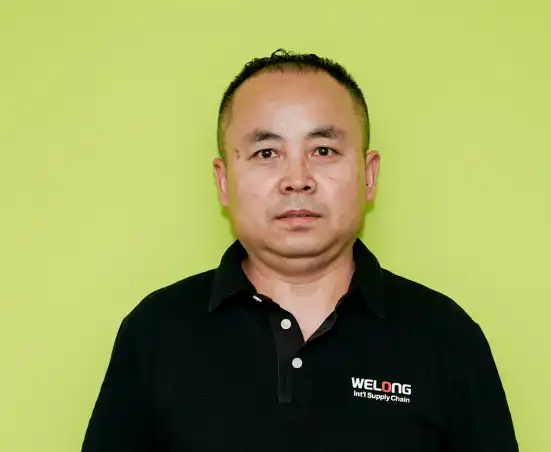
Share your inquiry, get the quotation accordingly!
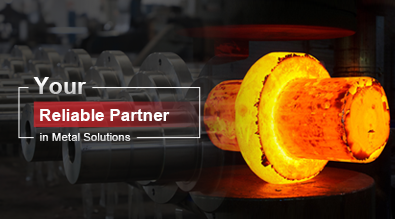
China WELONG- Your Reliable Partner in Metal Solutions