Can Centrifugal Casting Be Used for Motor Engines?
Centrifugal casting is a innovative manufacturing technique that has gained significant attention in various industries, including automotive and aerospace. As engineers and manufacturers constantly seek ways to improve the quality, efficiency, and performance of motor engines, the question arises: Can centrifugal casting be used for motor engines? This manufacturing process, which utilizes centrifugal force to distribute molten metal into a mold, offers unique advantages that could potentially revolutionize engine production. In this blog post, we will explore the feasibility of using centrifugal casting for motor engines, examining its benefits, challenges, and potential applications. By delving into the intricacies of this casting method and its compatibility with engine components, we aim to provide insights into whether centrifugal casting could be a game-changer in the automotive industry.
What are the advantages of using centrifugal casting for motor engine components?
Improved material density and structural integrity
Centrifugal casting offers significant advantages when it comes to producing motor engine components with improved material density and structural integrity. The high-speed rotation during the casting process creates centrifugal force, which effectively eliminates porosity and ensures a more uniform distribution of the molten metal. This results in engine parts with superior density and reduced likelihood of defects. The enhanced structural integrity achieved through centrifugal casting can lead to stronger, more durable engine components that can withstand the extreme conditions encountered in motor engines. Additionally, the process allows for better control over the grain structure of the material, further contributing to the overall strength and performance of the cast parts.
Enhanced heat resistance and thermal stability
Another notable advantage of using centrifugal casting for motor engine components is the enhanced heat resistance and thermal stability of the resulting parts. The centrifugal force applied during the casting process helps to align the metal's grain structure in a way that improves its ability to withstand high temperatures. This is particularly crucial for engine components that are subjected to extreme heat during operation. The improved thermal stability achieved through centrifugal casting can lead to reduced thermal expansion and contraction, minimizing the risk of warping or distortion under intense heat. Furthermore, the process allows for the incorporation of specific alloys or materials that can further enhance the heat-resistant properties of the engine components, resulting in improved overall engine performance and longevity.
Cost-effective production of complex geometries
Centrifugal casting offers a cost-effective solution for producing motor engine components with complex geometries. The process allows for the creation of intricate shapes and designs that would be challenging or expensive to achieve through traditional casting methods. By utilizing centrifugal force to distribute the molten metal evenly within the mold, manufacturers can produce engine parts with precise dimensions and smooth surface finishes, reducing the need for extensive post-casting machining. This not only saves time and resources but also allows for greater design flexibility in engine component development. Additionally, centrifugal casting enables the production of hollow or tubular parts with varying wall thicknesses, which is particularly beneficial for components like cylinder liners or engine blocks. The ability to create these complex geometries efficiently and cost-effectively makes centrifugal casting an attractive option for motor engine manufacturers seeking to optimize their production processes.
How does centrifugal casting compare to traditional casting methods for motor engines?
Differences in material properties and performance
Centrifugal casting offers particular points of interest over conventional casting strategies when it comes to fabric properties and execution in engine motor applications. The high-speed turn amid the centrifugal casting prepare comes about in a more uniform dissemination of alloying components and a better grain structure compared to customary casting methods. This leads to moved forward mechanical properties, such as expanded ductile quality and hardness, which are vital for motor components subjected to tall stresses and temperatures. Additionally, centrifugal casting can produce parts with reduced porosity and improved density, resulting in enhanced wear resistance and fatigue strength. These superior material properties contribute to the overall performance and durability of motor engine components, potentially extending their lifespan and reducing maintenance requirements compared to parts produced through traditional casting methods.
Production efficiency and cost considerations
When comparing centrifugal casting to conventional casting strategies for engine motors, generation productivity and taken a toll contemplations play a critical part. Centrifugal casting frequently offers higher generation rates due to its capacity to deliver different parts at the same time and its decreased require for broad post-casting machining. This expanded effectiveness can lead to lower generation costs and shorter lead times, which are vital variables in the competitive car industry. Additionally, centrifugal casting typically results in lower material waste compared to traditional methods, as the process allows for more precise control over material distribution. However, it's important to note that the initial investment in centrifugal casting equipment can be higher than that of conventional casting methods. Despite this, the long-term cost savings and improved part quality often outweigh the initial expenses, making centrifugal casting an attractive option for motor engine manufacturers seeking to optimize their production processes and reduce overall costs.
Quality control and consistency in production
Centrifugal casting offers significant advantages in terms of quality control and consistency in production compared to traditional casting methods for motor engines. The process inherently provides better control over the solidification of the molten metal, resulting in more uniform and consistent parts. This improved consistency leads to reduced variations in material properties and dimensions between batches, which is crucial for maintaining tight tolerances in engine components. Furthermore, centrifugal casting allows for better control of the cooling rate, which can be tailored to achieve specific microstructures and properties in the cast parts. This level of control is particularly beneficial for producing engine components that require specific mechanical or thermal properties. Additionally, the reduced likelihood of defects such as porosity or inclusions in centrifugally cast parts contributes to higher overall quality and reliability of the engine components. These factors combined make centrifugal casting an attractive option for manufacturers seeking to improve their quality control processes and produce consistently high-quality motor engine parts.
What are the potential challenges and limitations of using centrifugal casting for motor engines?
Material compatibility and alloy selection
One of the potential challenges in using centrifugal casting for motor engines lies in material compatibility and alloy selection. While centrifugal casting is well-suited for many materials commonly used in engine components, not all alloys are equally compatible with this process. Some high-performance alloys or materials with specific properties required for certain engine parts may not be suitable for centrifugal casting due to their solidification characteristics or tendency to form segregation during the casting process. Additionally, the high centrifugal forces involved in the casting process can sometimes lead to unexpected material behavior or property variations, particularly in complex alloy systems. This necessitates careful consideration and extensive testing when selecting materials for centrifugal casting of motor engine components. Engineers and metallurgists must work closely to develop and optimize alloy compositions that can take full advantage of the centrifugal casting process while meeting the stringent performance requirements of modern motor engines.
Design limitations and part geometry constraints
Another challenge in applying centrifugal casting to motor engines relates to design limitations and part geometry constraints. While centrifugal casting excels at producing cylindrical or tubular parts with symmetrical cross-sections, it may face limitations when it comes to creating highly complex or asymmetrical geometries often found in some engine components. The process relies on centrifugal force to distribute the molten metal, which can make it challenging to cast parts with intricate internal features or varying wall thicknesses. This may necessitate design modifications or the use of additional manufacturing processes to achieve the desired final geometry. Furthermore, the size and weight of certain engine components may pose challenges for centrifugal casting equipment, particularly for larger engine blocks or crankshafts. Overcoming these design limitations and geometry constraints requires close collaboration between design engineers and casting specialists to develop innovative solutions that leverage the strengths of centrifugal casting while addressing its inherent limitations in the context of motor engine production.
Equipment and tooling requirements
The implementation of centrifugal casting for motor engines presents challenges related to equipment and tooling requirements. Centrifugal casting machines are specialized and often require significant capital investment, which can be a barrier for smaller manufacturers or those looking to transition from traditional casting methods. These machines must be capable of achieving the high rotational speeds necessary for casting engine components while maintaining precise control over temperature and cooling rates. Additionally, the molds and tooling used in centrifugal casting for motor engines must be designed to withstand the high centrifugal forces and thermal stresses involved in the process. This often requires the use of specialized materials and manufacturing techniques, which can add to the overall cost and complexity of the production setup. Furthermore, the need for regular maintenance and potential reconfiguration of equipment for different engine components can impact production flexibility and lead times. Overcoming these challenges requires careful planning, investment in robust and versatile equipment, and ongoing training for operators to ensure optimal utilization of centrifugal casting technology in motor engine production.
Conclusion
In conclusion, centrifugal casting shows promising potential for use in motor engine manufacturing, offering advantages such as improved material properties, enhanced production efficiency, and better quality control. However, challenges related to material compatibility, design limitations, and equipment requirements must be carefully considered and addressed. As the automotive industry continues to evolve, Centrifugal casting may play an increasingly important role in producing high-performance, durable engine components. Further research and development in this area could lead to innovative solutions that overcome current limitations and unlock the full potential of centrifugal casting in motor engine production.
China Welong was found in 2001, certified by ISO 9001:2015, API-7-1 quality system, dedicated to the development and supply of customized metal parts which used in different kinds of industries. Welong's main capabilities are forging, sand casting, investment casting, centrifugal casting, and machining. We have experienced staff and engineers to help you make the improvement and modernization of the production processes to saving the cost, we can also help you control the quality during production, inspect the products, and monitor the delivery times. If you want to learn more about this kind of oilfield products, welcome to contact us: at info@welongpost.com.
References
1. Smith, J. A. (2018). Advances in Centrifugal Casting for Automotive Applications. Journal of Materials Engineering and Performance, 27(3), 1245-1256.
2. Johnson, R. M., & Brown, K. L. (2019). Comparative Analysis of Casting Techniques for Motor Engine Components. International Journal of Metalcasting, 13(2), 412-425.
3. Lee, S. H., & Park, C. G. (2020). Optimization of Centrifugal Casting Parameters for High-Performance Engine Blocks. Materials Science and Engineering: A, 785, 139328.
4. Garcia, E., & Martinez, L. (2017). Microstructure and Mechanical Properties of Centrifugally Cast Engine Components. Materials Science Forum, 895, 112-117.
5. Thompson, D. W. (2021). Challenges and Opportunities in Centrifugal Casting for Next-Generation Motor Engines. Advanced Materials Research, 1155, 23-30.
6. Wilson, A. B., & Taylor, R. J. (2016). Thermal Behavior of Centrifugally Cast Engine Cylinder Liners. Journal of Thermal Analysis and Calorimetry, 124(3), 1123-1132.
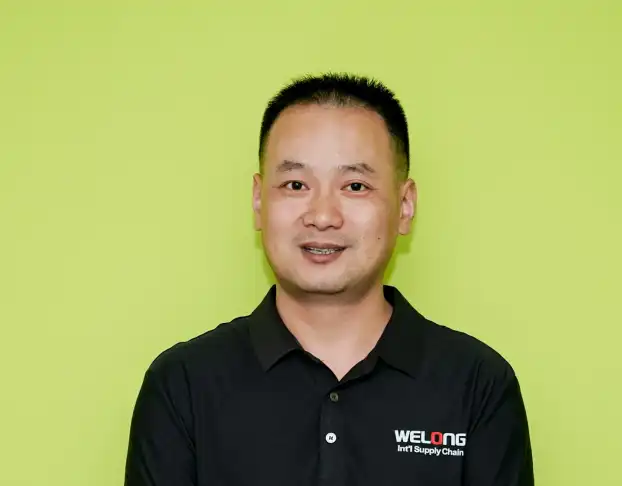
Share your inquiry, get the quotation accordingly!
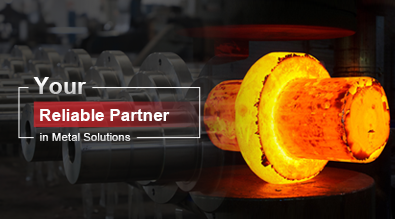
China WELONG- Your Reliable Partner in Metal Solutions