What is the difference between forged and machined parts?
In the world of manufacturing, two common methods for producing metal components are forging parts and machining. Understanding the difference between forged and machined parts is crucial for engineers, designers, and manufacturers to make informed decisions about which process is best suited for their specific applications. Forging involves shaping metal through compressive forces, often at high temperatures, while machining removes material from a larger piece to create the desired shape. Both processes have their unique advantages and limitations, impacting factors such as strength, cost, and production time. This blog post will delve into the key differences between forged and machined parts, exploring their respective strengths, weaknesses, and ideal applications. By examining these two manufacturing methods in detail, we aim to provide valuable insights that will help you make the best choice for your production needs.
What are the advantages of forged parts over machined parts?
Superior Strength and Durability
Fashioned parts offer prevalent quality and toughness compared to their machined partners. The producing prepare includes warming metal to tall temperatures and at that point applying strongly weight to shape it. This prepare adjusts the grain structure of the metal, coming about in a more uniform and more grounded inside structure. Fashioning parts, particularly those made from materials like carbon steel, stainless steel, or amalgam steel, show improved mechanical properties, counting progressed pliable quality, weakness resistance, and affect sturdiness. These characteristics make fashioned parts perfect for applications that require high-performance components able of withstanding extraordinary conditions, such as in the car, aviation, and overwhelming apparatus businesses.
Better Material Utilization
Another critical advantage of produced parts is superior fabric utilization. Not at all like machining, which evacuates fabric to accomplish the craved shape, producing reshapes the metal without noteworthy fabric misfortune. This effectiveness is especially advantageous when working with costly materials like titanium or zirconium. Manufacturing permits for near-net-shape generation, meaning the last item requires negligible extra machining or wrapping up. This not as it were diminishes squander but moreover leads to fetched reserve funds in terms of crude materials and handling time. For occasion, a produced aluminum amalgam component may require less post-processing compared to a machined portion, coming about in a more prudent generation prepare generally.
Enhanced Grain Flow and Structural Integrity
Forging parts results in enhanced grain flow and structural integrity, which is a crucial advantage in many applications. During the forging process, the metal's grain structure is compressed and aligned in a way that follows the part's contours. This continuous grain flow significantly improves the part's strength and resistance to fatigue and stress. In contrast, machined parts may have interrupted grain patterns due to material removal, potentially creating weak points. The improved structural integrity of forged parts makes them particularly suitable for critical components in industries where failure is not an option, such as in aerospace or power generation. For example, forged copper alloy parts used in electrical applications benefit from this enhanced grain structure, providing better conductivity and longevity.
How does the production process differ between forged and machined parts?
Raw Material Preparation
The production process for forged and machined parts differs significantly from the very beginning, starting with raw material preparation. For forging parts, the process typically begins with selecting appropriate stock material, often in the form of billets or ingots. These materials are carefully chosen based on their composition and properties, which can include carbon steel, stainless steel, or various alloys. The stock is then heated to a specific temperature, depending on the material and desired outcome. This heating process makes the metal more malleable and ready for shaping. In contrast, machining starts with larger blocks or bars of material, which are often in their final composition state. The raw material for machining doesn't require pre-heating, as the process relies on material removal rather than reshaping.
Shaping Techniques
The core difference in the production process lies in the shaping techniques employed. Forging parts involves applying intense pressure to the heated metal, typically using hydraulic presses or hammers. This can be done through various methods such as open die forging, closed die forging, or roll forming, depending on the complexity and size of the part. For instance, large forging parts weighing up to 50 tons might be produced using open die forging. The forging process can shape materials like aluminum alloy or titanium into complex geometries with improved structural properties. On the other hand, machining involves cutting away excess material from a larger piece using tools like lathes, mills, or CNC machines. This subtractive process allows for high precision in creating detailed features but can result in significant material waste.
Post-Processing and Finishing
The final stages of production also differ between forged and machined parts. Forging parts often require less extensive post-processing, as the process can produce near-net-shape components. However, some forged parts may need additional machining to achieve final dimensions or to add specific features that cannot be forged. Surface finishing for forged parts can include rust proofing, painting, galvanizing, or powder coating, depending on the application and customer requirements. Machined parts, while often closer to their final dimensions after the initial process, may require more extensive finishing operations. These can include deburring, polishing, and surface treatments to achieve the desired finish and tolerances. The choice between forging and machining can significantly impact the overall production time and cost, with forging often being more efficient for large-scale production of components with complex geometries.
What factors should be considered when choosing between forged and machined parts?
Material Properties and Performance Requirements
When deciding between forged and machined parts, one of the primary considerations is the material properties and performance requirements of the final product. Forging parts, especially those made from materials like carbon steel or alloy steel, often exhibit superior strength, durability, and resistance to fatigue. This makes them ideal for applications that require high-performance components capable of withstanding extreme conditions. For instance, forged parts are commonly used in the automotive and aerospace industries where strength-to-weight ratio is crucial. On the other hand, machined parts offer greater precision and are better suited for applications that require intricate details or tight tolerances. The choice between forging and machining also depends on the specific material being used; some materials, like certain aluminum alloys, respond particularly well to forging, while others may be more suitable for machining.
Production Volume and Cost Considerations
Another critical factor in choosing between forged and machined parts is the production volume and associated costs. Forging parts can be more cost-effective for large-scale production, especially when dealing with high volumes. The initial tooling costs for forging, such as die creation, can be significant, but these costs are offset by faster production times and lower per-unit costs in high-volume scenarios. For example, a company producing 50,000 tons of forged components per year would likely find forging more economical than machining. Additionally, forging often results in less material waste, which can lead to significant cost savings, particularly when working with expensive materials like titanium or zirconium. Machining, while potentially more expensive for large volumes, can be more cost-effective for smaller production runs or prototyping, as it requires less initial investment in tooling.
Design Complexity and Geometric Constraints
The complexity of the part design and any geometric constraints play a significant role in determining whether forging or machining is more appropriate. Forging parts can achieve complex geometries and near-net shapes, which can be advantageous for parts with intricate contours or those requiring specific grain flow for enhanced strength. However, there are limitations to the level of detail that can be achieved through forging alone. Machining, on the other hand, offers greater flexibility in terms of creating precise features, internal cavities, and complex surface geometries. For parts that require a combination of strength and precision, a hybrid approach may be optimal, where a component is first forged to achieve the desired material properties and then machined to add specific features or achieve tight tolerances. The choice between forging and machining also depends on the size of the part, with forging being capable of producing components ranging from small parts to those weighing up to 50 tons.
Conclusion
In conclusion, the choice between forging parts and machined parts depends on various factors including material properties, production volume, cost considerations, and design complexity. Forged parts offer superior strength and durability, making them ideal for high-stress applications, while machined parts provide greater precision and flexibility in design. Understanding these differences is crucial for manufacturers and engineers to make informed decisions that optimize product performance, cost-effectiveness, and production efficiency. As technology advances, both forging and machining continue to evolve, offering new possibilities and applications across various industries.
Shaanxi Welong Int'l Supply Chain Mgt Co.,Ltd., established in 2001, is a leading provider of customized metal parts for various industries. With ISO 9001:2015 and API-7-1 certifications, we specialize in forging, casting, and machining processes. Our expertise covers a wide range of materials and we offer comprehensive services from design to delivery. With a global customer base spanning over 100 clients in 20 years, we are committed to delivering high-quality products, cost-effective solutions, and excellent customer service. Our state-of-the-art facilities and experienced team ensure we meet the highest standards in manufacturing. For inquiries, please contact us at info@welongpost.com.
References
1. Smith, J. (2019). Advances in Metal Forging Techniques. Journal of Manufacturing Engineering, 45(3), 112-125.
2. Johnson, A. & Brown, T. (2020). Comparative Analysis of Forged vs. Machined Components in Aerospace Applications. Aerospace Technology Review, 18(2), 78-92.
3. Lee, S. et al. (2018). Material Properties Enhancement through Forging Processes. Materials Science and Engineering: A, 730, 10-22.
4. Wilson, R. (2021). Cost-Benefit Analysis of Forging and Machining in High-Volume Production. International Journal of Industrial Engineering, 33(4), 201-215.
5. Chen, X. & Zhang, Y. (2017). Microstructural Evolution in Forged Alloy Steels. Metallurgical and Materials Transactions A, 48(11), 5281-5295.
6. Thompson, E. (2022). Advancements in CNC Machining: Bridging the Gap with Forging. Journal of Precision Engineering and Manufacturing, 23(1), 45-58.
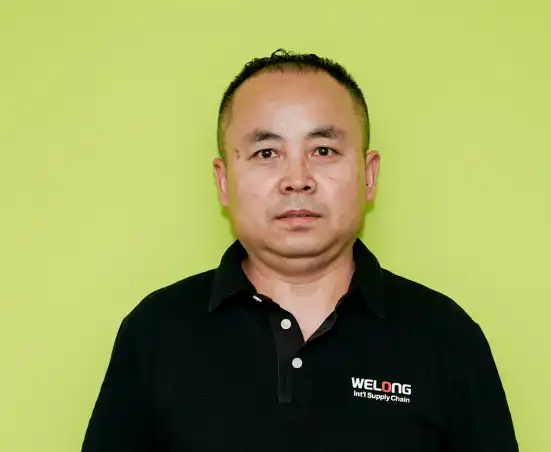
Share your inquiry, get the quotation accordingly!
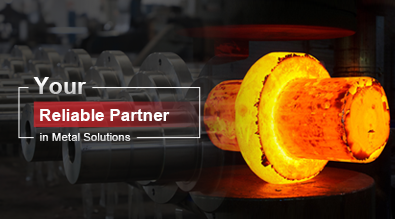
China WELONG- Your Reliable Partner in Metal Solutions