Gravity die casting: process and applications
Gravity die casting, also known as gravity casting, is a sophisticated manufacturing process that has revolutionized the production of metal components across various industries. This method involves pouring molten metal into reusable molds, relying on gravity to fill the cavities and create intricate shapes with exceptional precision. Unlike other casting techniques, gravity die casting offers a unique combination of cost-effectiveness, dimensional accuracy, and superior surface finish, making it an ideal choice for producing high-quality parts in medium to large volumes. The process is particularly well-suited for aluminum and zinc alloys, allowing manufacturers to create components with excellent mechanical properties and aesthetic appeal. As industries continue to demand lighter, stronger, and more complex parts, gravity die casting has emerged as a versatile solution that meets these evolving needs while maintaining efficiency and quality standards.
What are the key steps in the gravity die casting process?
Mold Preparation and Preheating
The gravity die casting process begins with the careful preparation and preheating of the mold. This crucial step involves thoroughly cleaning the mold to remove any residual material from previous castings and applying a protective coating to prevent the molten metal from sticking to the mold surface. The mold is then preheated to a specific temperature, typically ranging from 200°C to 300°C, depending on the alloy being cast. This preheating serves multiple purposes in gravity casting: it helps to improve metal flow, reduces thermal shock to the mold, and ensures proper solidification of the cast part. The precise control of mold temperature is essential for achieving consistent quality and minimizing defects in the final product.
Pouring and Solidification
Once the mold is prepared and preheated, the molten metal is carefully poured into the mold cavity. In gravity die casting, this pouring process relies on the force of gravity to fill the mold, unlike pressure die casting which uses additional force. The pouring temperature and rate are closely monitored to ensure optimal filling and to prevent defects such as cold shuts or porosity. As the molten metal fills the mold, it begins to solidify from the outer edges inward. The solidification process in gravity casting is controlled by the mold design, which often includes cooling channels to regulate the rate of heat extraction. This controlled solidification is crucial for achieving the desired microstructure and mechanical properties in the cast part.
Ejection and Finishing
After the cast part has solidified and cooled sufficiently, it is ejected from the mold. The ejection process in gravity die casting is typically achieved through the use of ejector pins or a knockout system integrated into the mold design. Once removed, the cast part undergoes various finishing operations to achieve the final product specifications. These may include trimming excess material, removing gates and runners, and surface finishing techniques such as shot blasting, polishing, or painting. For instance, parts cast using aluminum or zinc alloys may undergo powder coating or painting to enhance their appearance and corrosion resistance. The finishing process is tailored to the specific requirements of the part and its intended application, ensuring that the final product meets or exceeds customer expectations in terms of both functionality and aesthetics.
How does gravity die casting compare to other casting methods?
Advantages Over Sand Casting
Gravity die casting offers several distinct advantages over traditional sand casting methods. Firstly, the use of permanent metal molds in gravity casting results in significantly improved dimensional accuracy and surface finish compared to sand molds. This precision is particularly beneficial for parts requiring tight tolerances or those with complex geometries. Additionally, gravity die casting allows for faster production cycles and higher output rates, as the metal molds can be reused immediately after each casting, unlike sand molds which need to be remade. The process also generates less waste and requires less post-casting machining, leading to more efficient material utilization and reduced production costs. Furthermore, gravity die casting produces parts with superior mechanical properties due to the faster solidification rates achieved in metal molds, resulting in finer grain structures and improved strength characteristics.
Differences from High-Pressure Die Casting
While both gravity and high-pressure die casting use metal molds, there are significant differences in their processes and capabilities. Gravity die casting relies solely on the force of gravity to fill the mold, whereas high-pressure die casting uses high-speed injection of molten metal under extreme pressure. This fundamental difference affects the types of parts that can be produced by each method. Gravity casting is better suited for larger, heavier components with thicker wall sections, typically ranging from 0.1 to 100 kg. It also allows for the production of parts with more uniform wall thicknesses and fewer internal defects compared to high-pressure die casting. However, high-pressure die casting can produce parts with thinner walls and more intricate details, making it preferable for smaller, more complex components. The choice between gravity and high-pressure die casting often depends on factors such as part size, complexity, production volume, and material requirements.
Cost-Effectiveness and Production Volumes
Gravity die casting strikes a balance between production cost and volume, making it an attractive option for medium to large production runs. The initial tooling costs for gravity die casting molds are generally lower than those for high-pressure die casting, but higher than sand casting patterns. However, these costs are often offset by the longer lifespan of the metal molds and the reduced need for post-casting operations. Gravity casting is particularly cost-effective for production volumes ranging from a few thousand to several hundred thousand parts per year. For instance, a typical gravity die casting operation might have an annual output of around 200 tons, depending on the size and complexity of the parts being produced. This makes gravity casting an ideal choice for manufacturers looking to produce high-quality parts in significant quantities without the extreme high-volume requirements of high-pressure die casting or the lower precision of sand casting.
What industries benefit most from gravity die casting technology?
Automotive and Transportation
The automotive and transportation industries are among the largest beneficiaries of gravity die casting technology. This manufacturing process is extensively used to produce a wide range of components, from engine blocks and cylinder heads to transmission housings and suspension parts. Gravity casting's ability to create complex shapes with high dimensional accuracy makes it ideal for producing critical automotive components that require both strength and precision. For example, aluminum alloy parts produced through gravity casting offer the lightweight properties crucial for improving fuel efficiency in vehicles. The process also allows for the integration of features such as cooling channels in engine components, enhancing performance and durability. As the automotive industry continues to focus on lightweighting and electrification, gravity die casting remains a key technology for producing both traditional and innovative components.
Aerospace and Defense
In the aerospace and defense sectors, gravity die casting plays a vital role in producing components that demand high reliability and performance under extreme conditions. The process is used to manufacture parts such as turbine blades, structural components for aircraft, and housings for various defense systems. The superior mechanical properties achieved through gravity casting, particularly when using aluminum and specialized alloys, make it possible to create parts that meet the stringent requirements of these industries. The ability to produce complex geometries with internal passages and precise wall thicknesses is particularly valuable in aerospace applications, where weight reduction and thermal management are critical. Furthermore, the consistency and repeatability of gravity die casting ensure that each component meets the exacting standards required for safety and performance in aerospace and defense applications.
Consumer and Industrial Products
Gravity die casting finds extensive application in the production of consumer and industrial products, ranging from household appliances to machinery components. In the consumer sector, it is used to manufacture parts for products such as power tools, cookware, and lighting fixtures. The process's ability to produce parts with excellent surface finishes makes it particularly suitable for items that require both functionality and aesthetic appeal. In the industrial sector, gravity casting is employed to create components for pumps, valves, and various types of machinery. The versatility of the process allows for the production of parts in a wide range of sizes, from small precision components weighing as little as 0.1 kg to large industrial parts up to 100 kg. The surface finish options available with gravity casting, including shot blasting, polishing, powder coating, and painting, provide manufacturers with the flexibility to meet diverse product requirements and industry standards.
Conclusion
Gravity die casting, also known as gravity casting, stands as a versatile and efficient manufacturing process that offers significant advantages in the production of high-quality metal components. Its ability to produce parts with excellent dimensional accuracy, superior surface finish, and enhanced mechanical properties makes it an invaluable technology across various industries. From automotive and aerospace to consumer and industrial applications, gravity die casting continues to meet the evolving demands for lightweight, durable, and complex parts. As manufacturers seek to balance quality, cost-effectiveness, and production efficiency, gravity die casting remains a crucial technology in the modern manufacturing landscape, driving innovation and enabling the creation of advanced products that shape our world.
For those seeking expert guidance and high-quality gravity die casting services, Shaanxi Welong Int'l Supply Chain Mgt Co., Ltd. offers comprehensive solutions tailored to diverse industry needs. With over 20 years of experience and a commitment to excellence, Welong specializes in various casting processes, including gravity die casting, and serves a global clientele. Their expertise in materials ranging from aluminum and zinc alloys to more specialized metals ensures that customers receive products that meet the highest standards of quality and performance. For more information or to discuss your gravity die casting requirements, please contact Welong at info@welongpost.com.
References
1. Smith, J. R. (2018). Advances in Gravity Die Casting: Processes and Applications. Journal of Materials Engineering and Performance, 27(4), 1845-1857.
2. Johnson, A. B., & Williams, C. D. (2019). Comparative Analysis of Casting Techniques: Gravity Die Casting vs. High-Pressure Die Casting. International Journal of Metalcasting, 13(2), 412-425.
3. Thompson, R. L. (2020). Optimization of Mold Design for Gravity Die Casting Applications. Foundry Management & Technology, 148(5), 22-28.
4. Garcia, E. M., & Martinez, L. F. (2021). Material Selection and Process Parameters in Gravity Die Casting for Automotive Components. Materials & Design, 202, 109567.
5. Brown, S. K. (2017). Quality Control Techniques in Gravity Die Casting Production. Quality Engineering, 29(1), 101-113.
6. Lee, H. T., & Chen, W. C. (2022). Sustainability Assessment of Gravity Die Casting in the Context of Industry 4.0. Journal of Cleaner Production, 330, 129789.
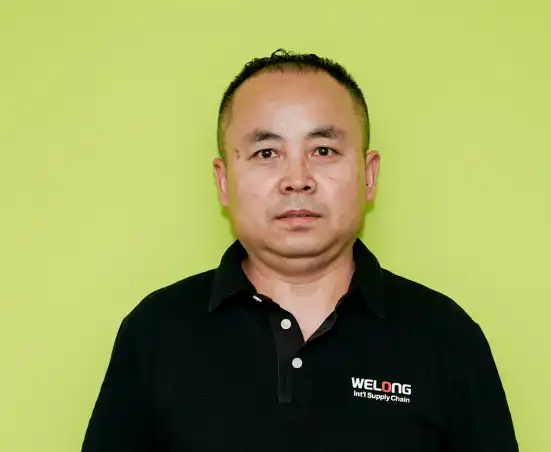
Share your inquiry, get the quotation accordingly!
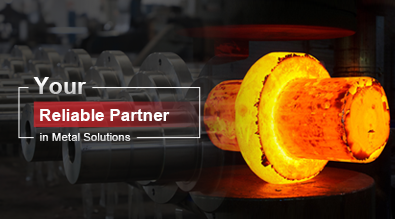
China WELONG- Your Reliable Partner in Metal Solutions