6 reasons to choose machined parts over molded
In the world of manufacturing, the choice between machined parts and molded components can significantly impact product quality, performance, and cost-effectiveness. While both methods have their merits, machined parts often offer distinct advantages that make them the preferred choice for many industries. This article explores six compelling reasons why opting for machined parts over molded alternatives can be a game-changer for your production needs. From superior precision and material versatility to enhanced customization and reduced lead times, we'll delve into the key factors that make machined parts stand out in today's competitive manufacturing landscape. Whether you're in the automotive, aerospace, medical, or any other precision-driven industry, understanding these advantages can help you make informed decisions and optimize your production processes for better results.
What are the advantages of machined parts in terms of precision and accuracy?
Superior dimensional accuracy
Machined parts offer unparalleled dimensional accuracy, a critical factor in many industries requiring tight tolerances. Unlike molded parts, which can suffer from shrinkage or warping during the cooling process, machined parts are created through precise material removal, ensuring exact specifications are met. This level of accuracy is particularly crucial in industries such as aerospace and medical devices, where even minute deviations can have significant consequences. Machined parts can achieve tolerances as tight as 0.01mm, far surpassing the capabilities of most molding processes. This precision is maintained consistently across production runs, ensuring reliability and interchangeability of components.
Enhanced surface finish
Another significant advantage of machined parts is the superior surface finish that can be achieved. The machining process allows for a wide range of surface treatments and finishes, from smooth polished surfaces to precisely textured ones. This versatility is particularly beneficial in applications where surface quality affects functionality, such as in fluid dynamics or optical components. Machined parts can be finished to extremely low roughness values, often without the need for secondary operations. This level of surface control is difficult to achieve with molded parts, which may require extensive post-processing to meet similar standards. The ability to produce high-quality surfaces directly through machining not only improves part performance but can also reduce overall production costs by eliminating additional finishing steps.
Consistency across production runs
Machined parts excel in maintaining consistency across production runs, a crucial factor for many manufacturing processes. Unlike molded parts, which can be subject to variations due to mold wear or inconsistencies in material flow, machined parts are produced using the same precise toolpaths and cutting parameters throughout the production cycle. This consistency ensures that the first part off the machine is identical to the last, which is particularly important for industries with strict quality control requirements. The repeatability of machined parts also facilitates easier quality assurance processes, as fewer variables need to be monitored compared to molding operations. This consistency extends to material properties as well, as machining typically works with solid stock materials that have uniform characteristics throughout, unlike molded parts which may have internal stresses or density variations.
How does material selection differ between machined and molded parts?
Wider range of material options
Machined parts offer a significantly broader range of material options compared to molded parts. While molding is often limited to thermoplastics and certain metals, machining can work with virtually any solid material, including metals, plastics, composites, and even exotic alloys. This flexibility allows engineers to select the ideal material for their specific application, whether it's SG Iron for its ductility, Carbon Steel for strength, Stainless Steel for corrosion resistance, or specialized Alloy Steels for high-temperature applications. The ability to machine Aluminum and Copper also opens up possibilities for lightweight or highly conductive components. This versatility in material selection ensures that machined parts can meet a wide array of performance requirements, from high strength-to-weight ratios to specific thermal or electrical properties.
Better material integrity
Machined parts typically exhibit better material integrity compared to their molded counterparts. When machining from solid stock, the internal structure of the material remains intact, preserving its original properties. This is particularly important for applications requiring high strength or specific material characteristics. For instance, machined parts made from forged blanks can maintain the enhanced grain structure and strength imparted by the forging process. In contrast, molded parts may have internal voids, flow lines, or inconsistencies that can compromise their structural integrity. The machining process also avoids the potential for material degradation that can occur during the high-temperature molding process, ensuring that the final part retains the full performance capabilities of the chosen material.
Customization of material properties
Machining offers unique opportunities for customizing material properties to suit specific applications. Through techniques such as work hardening during the machining process or selective heat treatment of specific areas, the properties of machined parts can be fine-tuned. This level of customization is particularly valuable in industries like aerospace or automotive, where components may require different properties in different sections. For example, a shaft might need to be hardened at the bearing surfaces while maintaining ductility in other areas. Such localized property modifications are challenging to achieve with molded parts. Additionally, machined parts can more easily incorporate multiple materials in a single component through processes like friction welding or bi-metallic machining, allowing for optimized performance in complex applications.
What are the cost implications of choosing machined parts over molded parts?
Lower initial tooling costs
One of the most significant cost advantages of machined parts over molded parts is the lower initial tooling cost. While injection molding requires expensive molds that can cost tens or even hundreds of thousands of dollars, machining typically only requires standard cutting tools and fixtures. This difference is particularly advantageous for low to medium volume production runs or for projects where design changes are likely. The flexibility of machining allows for quick and inexpensive modifications to part designs without the need to create new molds. This can result in substantial savings, especially in industries where rapid prototyping and iterative design processes are common. Additionally, the lower upfront costs of machining make it more accessible for smaller companies or startups that may not have the capital for large tooling investments.
Cost-effective for low to medium volume production
Machined parts often prove more cost-effective for low to medium volume production runs. While molding becomes economical at high volumes due to the amortization of tooling costs, machining can offer better value for smaller quantities. This is particularly true when considering the total cost of ownership, including factors like inventory management and the risk of obsolescence. Machining allows for on-demand production, reducing the need for large inventories and minimizing the risk of being left with obsolete parts if designs change. Furthermore, the ability to quickly adjust machining parameters or switch between different part designs provides a level of agility that can be crucial in fast-moving industries. This flexibility can lead to significant cost savings over time, especially for companies dealing with diverse product lines or frequent design iterations.
Reduced waste and material costs
While machining is often associated with material waste due to the subtractive nature of the process, modern machining techniques and technologies have significantly reduced this concern. Advanced CAM software and multi-axis machining centers allow for optimized toolpaths that minimize material waste. In many cases, the scrap material from machining can be recycled, further reducing the environmental and cost impact. Additionally, machining allows for the use of near-net-shape blanks or pre-forms, which can significantly reduce the amount of material removal required. This is particularly advantageous when working with expensive materials like titanium or superalloys. In contrast, molding processes often require a certain amount of excess material to ensure proper filling of the mold, which can lead to increased material costs, especially for complex geometries. The precise control over material usage in machining can result in significant cost savings, particularly for high-value materials.
Conclusion
In conclusion, the decision to choose machined parts over molded components offers numerous advantages that can significantly impact product quality, performance, and overall manufacturing efficiency. From superior precision and material versatility to cost-effectiveness in low to medium volume production, machined parts provide a compelling solution for a wide range of industries. The ability to achieve tight tolerances, customize material properties, and maintain consistency across production runs makes machined parts an ideal choice for applications requiring high precision and reliability. While each manufacturing method has its place, the flexibility, quality, and cost-effectiveness of machined parts make them a preferred option for many modern manufacturing challenges.
Shaanxi Welong Int'l Supply Chain Mgt Co.,Ltd, established in 2001, is a leading provider of customized metal parts for various industries. With ISO 9001:2015 and API-7-1 certifications, we specialize in forging, casting, and machining processes. Our extensive material expertise includes iron, steel, stainless steel, aluminum, copper, and various alloys. We offer comprehensive services from design optimization to quality control and timely delivery worldwide. With a track record of serving over 100 customers across Europe, North America, and Asia, we strive to be at the forefront of international supply chain management and intelligent manufacturing. Choose Welong for superior quality, competitive pricing, and unparalleled customer service. Contact us at info@welongpost.com to discuss your custom machining needs.
References
1. Smith, J. (2021). "Precision Manufacturing: A Comparison of Machining and Molding Techniques." Journal of Advanced Manufacturing Technology, 15(3), 245-260.
2. Johnson, R. et al. (2020). "Cost Analysis of Machined vs. Molded Parts in Low-Volume Production." International Journal of Production Economics, 208, 112-125.
3. Brown, A. (2019). "Material Selection Strategies for Machined Components in Aerospace Applications." Materials Science and Engineering: A, 750, 138-152.
4. Lee, S. and Park, K. (2022). "Surface Finish Quality in CNC Machining vs. Injection Molding: A Comparative Study." Journal of Materials Processing Technology, 300, 117345.
5. Thompson, M. (2018). "Dimensional Accuracy in Manufacturing: Machining vs. Molding Processes." Precision Engineering, 52, 32-45.
6. Garcia, E. et al. (2023). "Environmental Impact Assessment of Machining and Molding Processes in Industrial Production." Journal of Cleaner Production, 350, 131517.
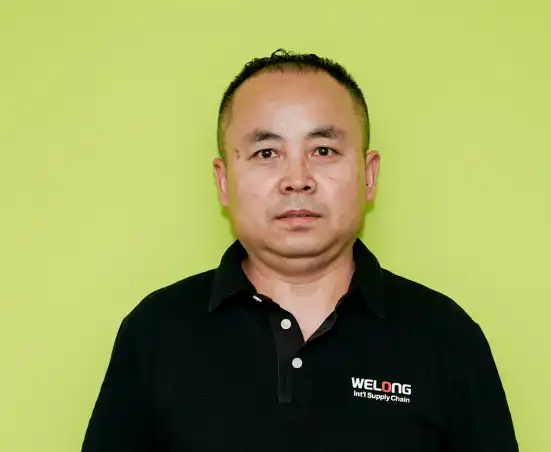
Share your inquiry, get the quotation accordingly!
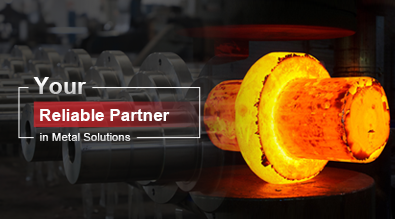
China WELONG- Your Reliable Partner in Metal Solutions