11 Different Types of Casting Processes
Casting is a fundamental manufacturing process that has been used for thousands of years to create complex shapes and structures from molten materials. In today's modern manufacturing landscape, there are numerous casting processes available, each with its own unique advantages and applications. This article explores 11 different types of casting processes, shedding light on their characteristics, benefits, and ideal use cases. From traditional sand casting to advanced investment casting and everything in between, we'll delve into the intricacies of these methods, highlighting how they contribute to the production of high-quality casting parts. Whether you're a seasoned manufacturing professional or simply curious about the world of casting, this comprehensive guide will provide valuable insights into the diverse range of techniques used to shape molten materials into finished products. Join us as we embark on a journey through the fascinating world of casting processes and discover how they continue to shape our modern world.
What are the key factors to consider when choosing a casting process for producing casting parts?
Material Selection
When it comes to choosing a casting process for producing casting parts, material selection is a crucial factor that cannot be overlooked. The type of material used in casting significantly influences the final product's properties, performance, and overall quality. Different casting processes are better suited for specific materials, so it's essential to consider the material's melting point, fluidity, and chemical composition. For instance, sand casting is ideal for materials with high melting points, such as iron and steel, while die casting is more suitable for non-ferrous metals like aluminum and zinc. Additionally, the material's shrinkage rate during solidification must be taken into account to ensure dimensional accuracy in the final casting parts. Some materials may require special treatments or additives to improve their castability, which can impact the choice of casting process. Ultimately, selecting the right material and corresponding casting process is crucial for achieving the desired mechanical properties, surface finish, and overall performance of the casting parts.
Production Volume
Production volume is another critical factor to consider when selecting a casting process for producing casting parts. The anticipated quantity of parts to be manufactured directly influences the choice of casting method, as different processes are more economical and efficient at various production scales. For low-volume production or prototyping, processes like investment casting or 3D printed sand molds may be more suitable due to their flexibility and lower tooling costs. On the other hand, high-volume production often benefits from processes like die casting or permanent mold casting, which offer faster cycle times and better repeatability. It's important to note that some casting processes have higher initial setup costs but become more cost-effective as production volumes increase. For instance, while die casting requires significant upfront investment in tooling, it becomes highly economical for large-scale production of casting parts. Manufacturers must carefully evaluate their production requirements and future demand forecasts to choose a casting process that balances initial costs, production efficiency, and long-term scalability for their specific casting parts needs.
Geometric Complexity
The geometric complexity of the desired casting parts plays a significant role in determining the most suitable casting process. Different casting methods have varying capabilities when it comes to reproducing intricate details, undercuts, and complex shapes. For instance, investment casting excels at producing highly detailed and complex casting parts with excellent surface finishes, making it ideal for aerospace and medical components. Sand casting, while more versatile, may struggle with very fine details but can accommodate large and complex shapes. Lost foam casting is particularly adept at creating intricate internal passages and cavities that would be difficult or impossible to achieve with other methods. When dealing with casting parts that have thin walls or require high dimensional accuracy, processes like die casting or centrifugal casting may be more appropriate. It's crucial to consider not only the complexity of the part itself but also any post-casting machining requirements, as some processes can produce near-net-shape parts that require minimal finishing. By carefully evaluating the geometric complexity of the casting parts, manufacturers can select a casting process that best balances the desired level of detail with production efficiency and cost-effectiveness.
How do different casting processes impact the quality and properties of casting parts?
Surface Finish and Dimensional Accuracy
The choice of casting process significantly influences the surface finish and dimensional accuracy of casting parts. Different methods offer varying levels of precision and surface quality, which can impact the final product's appearance, functionality, and potential need for post-processing. For example, investment casting is renowned for its ability to produce casting parts with excellent surface finishes and tight tolerances, often requiring minimal additional machining. This makes it ideal for applications in aerospace and medical industries where precision is paramount. On the other hand, sand casting, while versatile, typically results in a rougher surface finish and may have lower dimensional accuracy due to the nature of the sand mold. Die casting can achieve good surface finishes and tight tolerances, especially for smaller parts, but may face challenges with larger components due to potential shrinkage issues. Centrifugal casting is particularly effective for producing cylindrical casting parts with uniform wall thickness and good dimensional stability. The impact of the casting process on surface finish and dimensional accuracy must be carefully considered, as it directly affects the quality, functionality, and potential post-processing requirements of the final casting parts.
Mechanical Properties
The mechanical properties of casting parts are significantly influenced by the chosen casting process. Different methods can result in varying grain structures, porosity levels, and overall material integrity, which in turn affect the strength, ductility, and other mechanical characteristics of the final product. For instance, sand casting often produces parts with good mechanical properties due to its slower cooling rate, which allows for a more uniform grain structure. However, it may also result in some porosity, which can be addressed through proper gating and risering design. Investment casting can achieve excellent mechanical properties, particularly for complex geometries, due to its ability to control solidification and minimize defects. Die casting, while offering high production rates, may sometimes result in casting parts with slightly lower mechanical properties due to the rapid solidification and potential for trapped gases. Centrifugal casting is particularly effective for producing parts with high density and uniform properties, especially for cylindrical components. Some processes, like squeeze casting, can enhance the mechanical properties of casting parts by applying high pressure during solidification, resulting in a finer grain structure and reduced porosity. Understanding how different casting processes impact mechanical properties is crucial for selecting the most appropriate method to meet the specific requirements of the casting parts in their intended application.
Internal Defects and Porosity
The occurrence of internal defects and porosity in casting parts is heavily influenced by the chosen casting process. These imperfections can significantly impact the mechanical properties, reliability, and overall quality of the final product. Sand casting, while versatile, may be prone to gas porosity and shrinkage defects if proper venting and feeding systems are not implemented. Investment casting generally offers good control over internal defects due to its precise wax pattern and ceramic shell mold, resulting in casting parts with minimal porosity. However, it may still face challenges with shrinkage in thicker sections. Die casting can produce parts with low porosity due to the high pressure applied during casting, but trapped gases can sometimes lead to blistering or internal voids. Centrifugal casting is particularly effective at reducing porosity and segregation in cylindrical parts due to the centrifugal force pushing impurities towards the inner surface. Some advanced processes, like vacuum-assisted casting or hot isostatic pressing (HIP), can be employed to further reduce porosity and improve the internal integrity of casting parts. The choice of casting process must take into account the acceptable levels of internal defects and porosity for the specific application of the casting parts, as these factors directly influence the component's performance and lifespan.
What are the latest advancements and trends in casting processes for producing high-quality casting parts?
3D Printing in Casting
The integration of 3D printing technology into casting processes has revolutionized the production of high-quality casting parts. This innovative approach, often referred to as 3D printed sand casting or rapid casting, combines the flexibility of additive manufacturing with traditional casting techniques. By using 3D printed molds or patterns, manufacturers can significantly reduce lead times and tooling costs, especially for complex or low-volume casting parts. The process allows for the creation of intricate internal geometries and complex cores that would be challenging or impossible to produce using conventional methods. 3D printed sand molds offer excellent dimensional accuracy and surface finish, resulting in casting parts with improved quality and reduced need for post-processing. Additionally, this technology enables rapid prototyping and design iterations, accelerating the product development cycle for casting parts. Some advanced applications even involve directly 3D printing wax patterns for investment casting, further streamlining the process. As 3D printing technology continues to advance, it is expected to play an increasingly significant role in the casting industry, offering new possibilities for producing high-quality, complex casting parts with greater efficiency and cost-effectiveness.
Simulation and Optimization Software
The development and widespread adoption of advanced simulation and optimization software have significantly enhanced the casting process for producing high-quality casting parts. These sophisticated tools allow engineers and manufacturers to virtually model and analyze the entire casting process before any physical production takes place. By simulating factors such as mold filling, solidification, and cooling, potential issues such as porosity, shrinkage, and thermal stresses can be identified and addressed in the design phase. This proactive approach greatly reduces the need for costly trial-and-error methods and minimizes defects in the final casting parts. Furthermore, these software solutions can optimize gating and risering systems, improving yield and reducing material waste. Some advanced programs even incorporate machine learning algorithms to continually refine and improve casting parameters based on historical data and real-time feedback. The use of simulation and optimization software not only enhances the quality of casting parts but also significantly reduces development time and production costs. As these tools become more sophisticated and user-friendly, they are expected to become an indispensable part of the casting process, enabling manufacturers to consistently produce high-quality casting parts with improved efficiency and reliability.
Advanced Materials and Alloys
The development and application of advanced materials and alloys represent a significant trend in the casting industry, driving the production of high-performance casting parts. Manufacturers are increasingly exploring new metal compositions and alloys that offer superior mechanical properties, corrosion resistance, and thermal stability. For instance, high-strength aluminum alloys are being developed for lightweight automotive and aerospace casting parts, while advanced stainless steel grades are being formulated for demanding chemical and marine applications. The use of metal matrix composites (MMCs) in casting is also gaining traction, allowing for the creation of parts with tailored properties that combine the strengths of different materials. Additionally, the casting of traditionally difficult-to-cast materials, such as titanium alloys and superalloys, is becoming more feasible through advancements in casting technologies and material science. These advanced materials often require specialized casting processes and parameters, driving innovation in casting techniques and equipment. As the demand for high-performance casting parts continues to grow across various industries, the development and implementation of advanced materials and alloys will play a crucial role in pushing the boundaries of what can be achieved through casting processes.
Conclusion
In conclusion, the world of casting processes is diverse and continually evolving, offering a wide range of options for producing high-quality casting parts. From traditional methods like sand casting to advanced techniques such as 3D printed molds and simulation-driven optimization, each process has its unique advantages and applications. The choice of casting method depends on various factors, including material properties, production volume, geometric complexity, and desired quality characteristics. As technology continues to advance, we can expect further innovations in casting processes, materials, and quality control methods. These developments will undoubtedly lead to the production of even more sophisticated, efficient, and high-performance casting parts, meeting the ever-increasing demands of various industries and applications.
Shaanxi Welong Int'l Supply Chain Mgt Co.,Ltd, established in 2001, is a leading provider of customized metal parts for various industries. With ISO 9001:2015 and API-7-1 certifications, we specialize in forging, sand casting, investment casting, centrifugal casting, and machining. Our expertise covers a wide range of materials, including iron, steel, stainless steel, aluminum, copper, zinc, and various alloys. Our experienced team offers cost-saving solutions, quality control, and timely delivery worldwide. With a track record of serving over 100 customers in more than 20 countries, we are committed to being a leader in international supply chain management and advancing China's intelligent manufacturing capabilities. Choose Welong for high-quality casting parts and exceptional service. Contact us at info@welongpost.com to discuss your casting needs.
References
1. Campbell, J. (2015). Complete Casting Handbook: Metal Casting Processes, Techniques and Design. Butterworth-Heinemann.
2. Beeley, P. (2001). Foundry Technology. Butterworth-Heinemann.
3. Brown, J. R. (1999). Foseco Ferrous Foundryman's Handbook. Butterworth-Heinemann.
4. Sahoo, M., & Sahu, S. (2014). Principles of Metal Casting. McGraw-Hill Education.
5. Upadhyaya, G. S. (2002). Powder Metallurgy Technology. Cambridge International Science Publishing.
6. Kalpakjian, S., & Schmid, S. R. (2014). Manufacturing Engineering and Technology. Pearson.
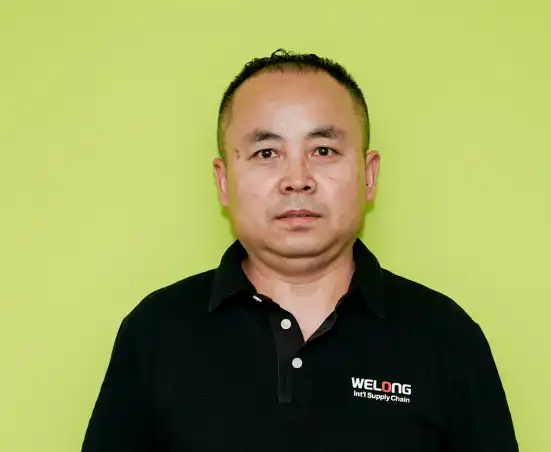
Share your inquiry, get the quotation accordingly!
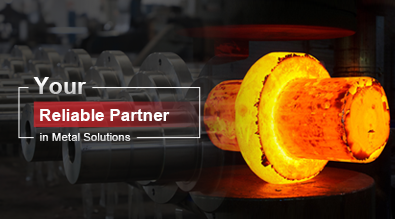
China WELONG- Your Reliable Partner in Metal Solutions