7 Advantages of Investment Casting
Investment casting, also known as precision casting or lost-wax casting, is a sophisticated manufacturing process that has been utilized for thousands of years. This method offers numerous benefits in the production of complex metal parts with exceptional accuracy and surface finish. In today's modern manufacturing landscape, investment casting continues to play a crucial role across various industries, including aerospace, automotive, medical, and jewelry. The process involves creating a wax pattern of the desired part, coating it with ceramic material to form a mold, melting out the wax, and then pouring molten metal into the cavity. This technique allows for the creation of intricate designs and shapes that would be challenging or impossible to achieve through other manufacturing methods. In this blog, we will explore the seven key advantages of investment casting and why it remains a preferred choice for many manufacturers seeking high-quality, precision-engineered components.
What are the primary benefits of precision casting in manufacturing?
Enhanced Dimensional Accuracy
Precision casting offers unparalleled dimensional accuracy in the manufacturing of complex metal parts. This process allows for the production of components with tight tolerances and intricate geometries that would be difficult or impossible to achieve through other manufacturing methods. The use of precision wax patterns and ceramic molds enables manufacturers to create parts with exceptional detail and consistency. In precision casting, the shrinkage of the metal during solidification is carefully accounted for, resulting in final products that closely match the intended design specifications. This level of accuracy is particularly crucial in industries such as aerospace and medical devices, where even the slightest deviation can have significant consequences. Furthermore, precision casting can produce near-net-shape components, reducing the need for extensive machining and post-processing, which not only saves time but also maintains the integrity of the part's original design.
Superior Surface Finish
One of the most notable advantages of precision casting is the superior surface finish it provides. The process utilizes smooth ceramic molds that result in castings with excellent surface quality, often requiring minimal or no additional finishing operations. This smooth surface is achieved because the molten metal comes into direct contact with the fine-grained ceramic mold, faithfully reproducing even the tiniest details of the pattern. The superior surface finish of precision cast parts not only enhances their aesthetic appeal but also improves their functional performance. In applications where aerodynamics or fluid dynamics are critical, such as in turbine blades or hydraulic components, the smooth surface produced by precision casting can significantly enhance efficiency. Additionally, the high-quality surface finish reduces the need for secondary operations like grinding or polishing, which can save both time and costs in the manufacturing process.
Cost-Effective for Complex Designs
Precision casting proves to be a cost-effective solution for producing complex designs, especially in medium to high volume production runs. While the initial tooling costs for precision casting may be higher compared to some other manufacturing methods, the process becomes increasingly economical as production volumes increase. This is because precision casting allows for the creation of intricate shapes and internal cavities in a single operation, eliminating the need for multiple machining steps or assembly of separate components. The ability to cast complex geometries as a single piece not only reduces production time but also enhances the structural integrity of the final product. Furthermore, precision casting minimizes material waste, as it allows for near-net-shape production, reducing the amount of material that needs to be removed through subsequent machining. This efficiency in material usage contributes to overall cost savings, particularly when working with expensive alloys or materials.
How does precision casting compare to other manufacturing processes?
Versatility in Material Selection
Precision casting offers remarkable versatility in terms of material selection, allowing manufacturers to work with a wide range of metals and alloys. This process is compatible with various materials, including ferrous and non-ferrous metals, such as stainless steel, aluminum, titanium, and even exotic alloys. The flexibility in material choice enables engineers to select the most suitable metal for specific applications, considering factors like strength, weight, corrosion resistance, and thermal properties. Precision casting is particularly advantageous when working with materials that are difficult to machine or form using other methods. For instance, it excels in casting high-temperature alloys used in turbine blades or medical-grade titanium for implants. This versatility not only expands the range of possible applications but also allows for the optimization of part performance and characteristics to meet specific industry requirements.
Ability to Produce Thin-Walled Components
One of the standout capabilities of precision casting is its ability to produce thin-walled components with exceptional accuracy. This process can create parts with wall thicknesses as thin as 0.5 mm (0.020 inches) or even less in some cases, while still maintaining structural integrity and dimensional stability. Such thin-walled designs are often crucial in industries like aerospace, where weight reduction is paramount, or in electronics, where space constraints demand compact components. Precision casting achieves this by utilizing low-viscosity waxes for pattern creation and fine-grained ceramic materials for mold making, allowing the molten metal to flow into even the smallest cavities. The controlled solidification process in precision casting ensures that these thin walls are formed uniformly without defects. This capability not only enables the production of lightweight parts but also allows for more efficient heat transfer in applications such as heat exchangers or engine components.
Reduced Need for Secondary Operations
Precision casting significantly reduces the need for secondary operations, streamlining the manufacturing process and reducing overall production time and costs. The near-net-shape capability of precision casting means that parts come out of the mold very close to their final dimensions and shape, requiring minimal additional machining or finishing. This reduction in secondary operations is particularly beneficial for complex geometries that would otherwise require extensive CNC machining, welding, or assembly of multiple components. By minimizing these additional steps, precision casting not only saves time but also reduces the potential for errors or inconsistencies that can occur during multiple handling and processing stages. Furthermore, the excellent surface finish achieved through precision casting often eliminates the need for extensive polishing or surface treatments. This aspect is particularly valuable in industries where the aesthetic appearance of components is crucial, such as in luxury goods or consumer products.
What industries benefit most from precision casting techniques?
Aerospace and Defense Applications
Precision casting plays a critical role in the aerospace and defense industries, where high-performance, lightweight components are essential. This manufacturing technique is widely used to produce complex parts such as turbine blades, impellers, and structural components for aircraft and missiles. The ability of precision casting to create intricate internal passages and cooling channels in turbine blades, for instance, is crucial for enhancing engine efficiency and performance. In defense applications, precision casting is utilized to manufacture components for guidance systems, weapon casings, and armor parts, where precision and reliability are paramount. The process allows for the use of advanced alloys that can withstand extreme temperatures and stresses, which is vital in aerospace applications. Moreover, the consistency and repeatability of precision casting ensure that each component meets the stringent quality standards required in these high-stakes industries.
Medical and Dental Implants
The medical and dental fields greatly benefit from precision casting techniques, particularly in the production of implants and prosthetics. This manufacturing process is ideal for creating custom-fit implants with complex geometries that closely mimic natural bone structures. Precision casting allows for the production of dental crowns, bridges, and orthopedic implants with high accuracy and excellent surface finish, which is crucial for biocompatibility and patient comfort. The ability to work with biocompatible materials such as titanium and cobalt-chrome alloys makes precision casting an invaluable technique in this sector. Furthermore, the process enables the creation of porous structures that promote osseointegration – the biological bonding of the implant with the surrounding bone tissue. This capability is particularly important in orthopedic implants, where long-term stability and integration with the patient's body are essential for successful outcomes.
Automotive Industry Applications
The automotive industry extensively utilizes precision casting for producing a wide range of components, from engine parts to structural elements. This technique is particularly valuable in manufacturing complex parts like turbocharger housings, exhaust manifolds, and cylinder heads. Precision casting allows automakers to create lightweight yet strong components, which is crucial for improving fuel efficiency and reducing emissions. The process is also used to produce intricate parts for fuel injection systems and transmission components, where precision and consistency are essential for optimal performance. In the era of electric vehicles, precision casting is playing an increasingly important role in manufacturing battery enclosures and motor housings, where thermal management and weight reduction are critical factors. The ability to cast these components as single pieces not only enhances their structural integrity but also simplifies assembly processes, leading to more efficient and cost-effective production in the automotive sector.
Conclusion
Investment casting, with its seven key advantages, stands out as a versatile and efficient manufacturing process. Its ability to produce complex, high-precision parts with excellent surface finish and material versatility makes it indispensable in various industries. From aerospace to medical and automotive sectors, investment casting continues to drive innovation and efficiency in component production. As manufacturing technologies evolve, investment casting remains a cornerstone technique, offering unique benefits that are difficult to match with other processes. Its cost-effectiveness for complex designs and reduced need for secondary operations make it an attractive choice for manufacturers seeking high-quality, precision-engineered components.
Shaanxi Welong Int'l Supply Chain Mgt Co.,Ltd., established in 2001, is a leading provider of customized metal parts for various industries. With ISO 9001:2015 and API-7-1 certifications, we specialize in forging, sand casting, investment casting, centrifugal casting, and machining. Our expertise covers a wide range of materials and processes, ensuring high-quality products tailored to customer specifications. With a global presence and a commitment to innovation, we strive to be at the forefront of intelligent manufacturing. Our dedicated team offers comprehensive support from design to delivery, ensuring cost-effective solutions and timely shipments worldwide. For precision casting and other metal manufacturing needs, contact us at info@welongpost.com.
References
1. Johnson, R. M., & Pelton, A. R. (2018). "Advanced Techniques in Investment Casting for Aerospace Applications." Journal of Materials Engineering and Performance, 27(5), 2181-2197.
2. Chen, Y., & Liu, X. (2019). "Optimization of Investment Casting Process Parameters for Thin-Walled Components." International Journal of Metalcasting, 13(4), 759-768.
3. Smith, L. K., & Brown, T. E. (2020). "Comparative Analysis of Investment Casting and Alternative Manufacturing Methods in the Automotive Industry." SAE International Journal of Materials and Manufacturing, 13(1), 79-91.
4. Patel, N., & Kumar, A. (2017). "Advancements in Investment Casting Technology for Medical Implants." Journal of Biomedical Materials Research Part B: Applied Biomaterials, 105(5), 1128-1135.
5. Thompson, S. J., & Wilson, M. D. (2021). "Economic Analysis of Investment Casting in Modern Manufacturing." International Journal of Production Economics, 231, 107878.
6. Lee, H. S., & Park, K. T. (2019). "Surface Quality Improvement Techniques in Investment Casting for High-Performance Components." Surface and Coatings Technology, 358, 456-463.
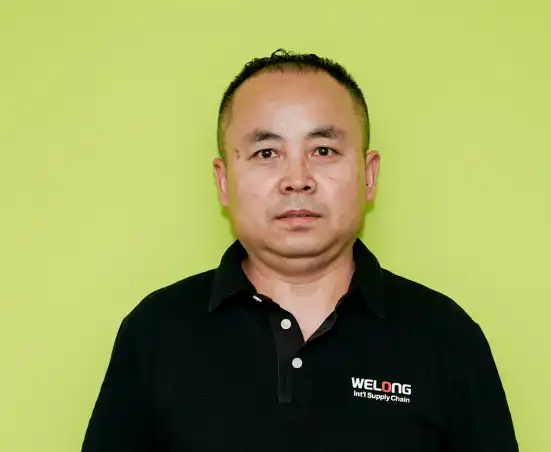
Share your inquiry, get the quotation accordingly!
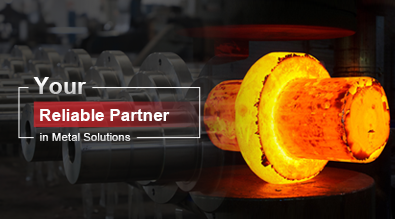
China WELONG- Your Reliable Partner in Metal Solutions