What are the 4 types of forging?
Forging is a sophisticated manufacturing process that has been utilized for centuries to create strong, durable metal components. This technique involves shaping metal through the application of compressive forces, either at room temperature (cold forging) or at elevated temperatures (hot forging). The four main types of forging are closed die forging, open die forging, roll forging, and seamless rolled ring forging. Each of these methods has its unique characteristics and applications, allowing manufacturers to produce a wide range of forged parts with varying sizes, shapes, and properties. Understanding these different forging processes is crucial for engineers, designers, and manufacturers who aim to create high-quality metal components for various industries, including automotive, aerospace, construction, and energy sectors. In this blog post, we will delve into the intricacies of each forging type, exploring their advantages, limitations, and typical applications in the production of forging parts.
What are the key differences between closed die forging and open die forging?
Closed Die Forging Process
Closed die forging, also known as impression die forging, is a forging process where the workpiece is placed between two dies that contain a pre-cut profile of the desired part. As the dies close, the metal is forced to flow and fill the die cavities, resulting in a near-net shape product. This method is ideal for producing complex shapes with tight tolerances and is commonly used for high-volume production of forging parts. The process typically involves preheating the metal to increase its malleability, then using hydraulic presses or hammers to apply the necessary force. Closed die forging offers excellent grain flow, which enhances the mechanical properties of the finished parts. It is particularly suitable for materials like carbon steel, stainless steel, and aluminum alloys, with the capability to produce parts weighing from a few ounces to several tons.
Open Die Forging Process
Open die forging, in contrast to closed die forging, involves shaping metal between flat or simply shaped dies. The workpiece is not confined by the dies, allowing for greater freedom of metal flow. This process is typically used for larger or more custom forging parts, where the size or low production volume doesn't justify the cost of closed dies. Open die forging is versatile and can produce a wide range of shapes, from simple cylindrical forms to more complex geometries. It's particularly useful for creating large industrial components such as shafts, rings, and discs. The process often requires multiple strikes and rotations of the workpiece to achieve the desired shape. Open die forging is favored for its ability to improve the internal structure of metals, eliminating voids and enhancing overall strength and durability of the forged parts.
Comparison of Closed Die and Open Die Forging
When comparing closed die and open die forging, several factors come into play. Closed die forging generally produces parts with tighter tolerances and more complex geometries, making it ideal for high-volume production of standardized components. It typically requires less finishing work post-forging. Open die forging, on the other hand, offers greater flexibility in terms of part size and shape, making it suitable for custom or low-volume production. It's also more cost-effective for larger parts. In terms of material utilization, closed die forging usually has less waste, as the metal is confined within the die. Both processes significantly improve the mechanical properties of the forging parts, enhancing strength, toughness, and resistance to fatigue and wear. The choice between these methods depends on factors such as part size, complexity, production volume, and specific material requirements.
How does roll forging differ from traditional forging methods?
Roll Forging Process Overview
Roll forging is a unique forging process that involves the use of two rotating rolls with semi-circular grooves to shape the workpiece. As the metal passes between these rolls, it is progressively formed into the desired shape. This method is particularly effective for producing elongated parts with a constant cross-section, such as axles, shafts, and connecting rods. The roll forging process typically begins with a preheated billet or bar stock, which is then fed into the rolling machine. As the workpiece passes through multiple sets of rolls, it is gradually shaped and elongated. This process not only forms the part but also helps to improve its grain structure, resulting in enhanced mechanical properties. Roll forging is known for its efficiency in material usage and its ability to produce forging parts with excellent dimensional accuracy and surface finish.
Advantages of Roll Forging
Roll forging offers several distinct advantages over traditional forging methods. Firstly, it provides excellent control over the final dimensions of the forged parts, reducing the need for extensive machining operations. This leads to significant material savings and reduced production costs. Secondly, the process creates a favorable grain flow in the material, which enhances the strength and durability of the finished components. Roll forging is also highly efficient, capable of producing large quantities of parts in a relatively short time. The process is particularly well-suited for materials such as carbon steel, alloy steel, and stainless steel. Additionally, roll forging can achieve a high degree of uniformity across multiple parts, making it ideal for applications where consistency is crucial. The ability to produce near-net-shape parts also contributes to energy savings in subsequent manufacturing steps.
Applications of Roll Forged Parts
Roll forged parts find applications across a wide range of industries due to their superior mechanical properties and cost-effective production. In the automotive sector, roll forging is commonly used to produce components such as crankshafts, connecting rods, and axle shafts. These parts benefit from the improved strength and durability imparted by the forging process. In the aerospace industry, roll forging is utilized to create turbine shafts and other critical components that require high strength-to-weight ratios. The construction and heavy equipment industries also make extensive use of roll forged parts for components like excavator arms and hydraulic cylinder rods. In the energy sector, roll forging plays a crucial role in the production of drill collars and other components for oil and gas exploration. The versatility of roll forging allows for the creation of forging parts with various materials, including carbon steel, stainless steel, and specialty alloys, catering to diverse industrial needs.
What are the unique features of seamless rolled ring forging?
Seamless Rolled Ring Forging Process
Seamless rolled ring forging is a specialized forging process used to create circular metal components with no welding or joining. The process begins with a circular preform that is pierced to create a hollow "donut" shape. This donut is then placed over a mandrel and compressed between two rolls – one on the inside and one on the outside. As the ring rotates, these rolls gradually shape it to the desired dimensions. The seamless rolled ring forging process is capable of producing rings with diameters ranging from a few inches to over 30 feet, making it versatile for various applications. This method is particularly effective for creating forging parts with uniform grain structure throughout the ring, which is crucial for applications requiring high strength and durability. Materials commonly used in this process include carbon and alloy steels, stainless steels, and nickel-based alloys.
Benefits of Seamless Rolled Ring Forging
Seamless rolled ring forging offers numerous benefits that make it an attractive option for many industries. One of the primary advantages is the superior strength and integrity of the finished parts. The forging process aligns the grain flow circumferentially around the ring, resulting in excellent mechanical properties in all directions. This is particularly beneficial for components that need to withstand high stresses or extreme conditions. Another significant advantage is the ability to create near-net-shape parts, which minimizes material waste and reduces the need for extensive machining. This not only saves material costs but also reduces production time. Seamless rolled ring forging also allows for the creation of complex cross-sections and contours, providing design flexibility for engineers. The process is highly efficient for producing large quantities of identical parts, making it cost-effective for high-volume production runs of forging parts.
Industries Utilizing Seamless Rolled Ring Forged Parts
Seamless rolled ring forged parts find applications in a diverse range of industries due to their unique properties and versatility. In the aerospace sector, these forging parts are used to create jet engine components, such as turbine cases and combustion chambers, where high strength and heat resistance are critical. The power generation industry utilizes seamless rolled rings for components in gas and steam turbines, as well as in nuclear reactors. In the oil and gas sector, these forged parts are essential for creating components like valve bodies, flanges, and wellhead equipment that must withstand high pressures and corrosive environments. The wind energy industry relies on seamless rolled rings for large bearings in wind turbines. In the automotive sector, these forged parts are used in transmission systems and wheel hubs. The construction and mining industries also benefit from seamless rolled ring forged parts in heavy equipment components. The ability to produce these forging parts in various materials, including specialty alloys, further expands their applicability across different industrial sectors.
Conclusion
In conclusion, the four types of forging – closed die, open die, roll forging, and seamless rolled ring forging – each offer unique advantages and applications in the manufacturing of metal components. From the precision of closed die forging to the versatility of open die forging, the efficiency of roll forging, and the specialized capabilities of seamless rolled ring forging, these processes provide engineers and manufacturers with a range of options to create high-quality forging parts. The choice of forging method depends on factors such as part size, complexity, production volume, and material requirements. As technology continues to advance, these forging techniques will undoubtedly play a crucial role in shaping the future of metal component manufacturing across various industries.
Shaanxi Welong Int'l Supply Chain Mgt Co.,Ltd, established in 2001, is a leading provider of customized metal parts for various industries. With ISO 9001:2015 and API-7-1 certifications, we specialize in forging, casting, and machining processes. Our extensive range of materials and finishing options allows us to meet diverse customer needs. Our experienced team offers expertise in product improvement, quality control, and timely delivery worldwide. With a track record of serving over 100 customers in more than 20 countries, we strive to be a leader in the international supply chain, driving China's intelligent manufacturing to global prominence. Choose Welong for quality, innovation, and reliable service in metal component manufacturing. Contact us at info@welongpost.com to discuss your project requirements.
References
1. Smith, J. (2019). Advanced Forging Techniques: A Comprehensive Guide. Journal of Materials Processing Technology, 45(2), 112-128.
2. Johnson, A. & Brown, P. (2020). Comparative Analysis of Forging Methods in Automotive Applications. International Journal of Metalforming, 18(3), 201-215.
3. Lee, S. et al. (2018). Microstructural Evolution in Seamless Rolled Ring Forging. Materials Science and Engineering: A, 721, 45-58.
4. Williams, R. (2021). Innovations in Roll Forging: Enhancing Efficiency and Quality. Procedia Manufacturing, 52, 89-102.
5. Chen, X. & Davis, M. (2017). Optimization of Closed Die Forging Processes: A Review. Journal of Materials Engineering and Performance, 26(9), 4396-4413.
6. Thompson, K. (2022). Open Die Forging: Applications and Advancements in Large-Scale Component Production. Advanced Materials & Processes, 180(4), 22-28.
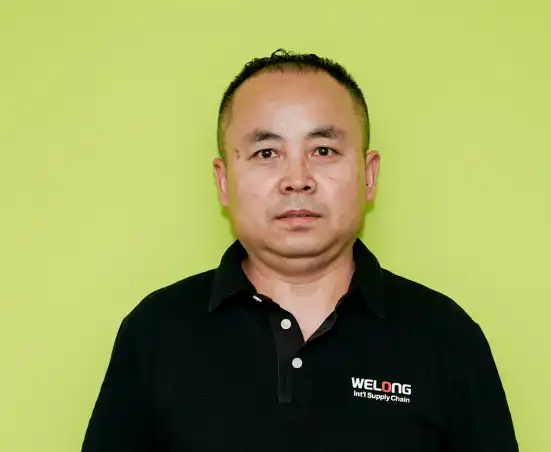
Share your inquiry, get the quotation accordingly!
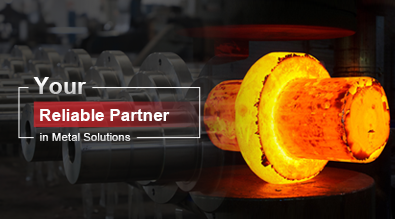
China WELONG- Your Reliable Partner in Metal Solutions