What Is Machining and How Are Parts Made?
Machining is a crucial manufacturing process that transforms raw materials into precisely crafted machined parts and components used in various industries. This intricate process involves removing material from a workpiece using cutting tools and advanced machinery to achieve desired shapes, sizes, and specifications. Machining plays a vital role in producing parts for automobiles, aerospace, medical devices, and countless other applications. As technology advances, machining techniques continue to evolve, offering greater precision, efficiency, and complexity in part production. From traditional methods like turning and milling to cutting-edge computer-controlled systems, machining encompasses a wide range of processes that enable manufacturers to create components with exceptional accuracy and consistency. In this blog, we'll explore the world of machining, delving into its fundamental principles, various techniques, and the crucial role it plays in modern manufacturing.
What are the most common types of machining processes?
Turning: The art of rotational symmetry
Turning is a fundamental machining process that produces cylindrical parts with rotational symmetry. In this operation, the workpiece rotates while a cutting tool moves along its axis, removing material to create the desired shape. Turning is extensively used to manufacture machined parts such as shafts, pins, and various cylindrical components. The process allows for high precision in diameter control and surface finish, making it ideal for producing parts with tight tolerances. Lathes, both manual and CNC-controlled, are the primary machines used for turning operations. Materials commonly machined through turning include metals like steel, aluminum, and brass, as well as plastics and other materials. The versatility of turning makes it an essential process in industries ranging from automotive to aerospace, where precision cylindrical components are crucial.
Milling: Versatile material removal
Milling is a versatile machining process that uses rotary cutters to remove material from a workpiece, creating a wide variety of shapes and features. Unlike turning, milling can produce flat surfaces, contours, slots, and complex 3D geometries. Milling machines, both vertical and horizontal, are used to manufacture machined parts with high precision and repeatability. The process is particularly useful for creating components with multiple faces, pockets, and intricate details. CNC milling has revolutionized the industry, allowing for the production of highly complex parts with minimal human intervention. Materials suitable for milling include metals, plastics, and composites, making it a go-to process for industries such as automotive, aerospace, and electronics. The flexibility of milling enables manufacturers to produce a wide range of machined parts, from simple brackets to complex molds and dies.
Drilling: Creating precise holes
Drilling is a machining process used to create cylindrical holes in workpieces. While it may seem simple, precision drilling is crucial for many machined parts, ensuring proper fit and function in assemblies. Drilling can be performed on various machines, including drill presses, lathes, and milling machines. The process involves a rotating drill bit that cuts into the material, removing chips as it progresses deeper. Advanced drilling techniques, such as gun drilling and deep-hole drilling, allow for the creation of extremely long and precise holes. Materials ranging from soft plastics to hardened steels can be drilled, with appropriate tooling and cutting parameters. In the production of machined parts, drilling is often combined with other processes like turning or milling to create complete components. The ability to produce accurate holes is essential in industries such as automotive, where precise alignments and fastening points are critical for component assembly and performance.
How does CNC machining revolutionize part production?
Increased precision and repeatability
CNC (Computer Numerical Control) machining has revolutionized the production of machined parts by dramatically increasing precision and repeatability. Unlike manual machining, CNC systems use computer-controlled commands to guide cutting tools, ensuring consistent results across multiple parts. This level of precision is crucial for industries requiring tight tolerances, such as aerospace and medical device manufacturing. CNC machines can achieve accuracies down to 0.01mm, far surpassing what is possible with manual methods. The ability to produce identical parts time after time is a significant advantage, especially in high-volume production scenarios. CNC machining also allows for complex geometries that would be challenging or impossible to create manually. This precision extends to various materials, including SG Iron, Carbon Steel, Stainless steel, Alloy Steel, Aluminum, and Copper, enabling manufacturers to meet diverse customer requirements while maintaining high quality standards.
Enhanced efficiency and reduced waste
CNC machining significantly enhances efficiency in the production of machined parts while simultaneously reducing material waste. The automation inherent in CNC systems allows for continuous operation with minimal human intervention, leading to increased productivity and shorter lead times. Complex parts that might take hours or days to produce manually can be completed in a fraction of the time with CNC machining. This efficiency is particularly valuable when working with expensive materials or when rapid turnaround is required. Moreover, CNC machining's precision means less material is wasted due to errors or inconsistencies. The ability to optimize cutting paths and tool usage results in more efficient material utilization, which is especially important when working with costly alloys or large workpieces. For instance, when machining parts with dimensions up to 1200x800x600mm or diameters below 1000mm, CNC systems can calculate the most efficient cutting strategies, minimizing waste and maximizing output.
Flexibility in design and production
CNC machining offers unparalleled flexibility in both design and production of machined parts. Engineers and designers can create complex 3D models using CAD software, which can be directly translated into machine instructions. This seamless digital workflow allows for rapid prototyping and iterative design improvements without the need for extensive retooling. The flexibility extends to production as well, enabling manufacturers to quickly switch between different part designs or make adjustments to existing ones with minimal downtime. This adaptability is crucial in industries with rapidly changing requirements or those producing a wide variety of parts. CNC machining can accommodate a broad range of materials and specifications, from small components weighing as little as 0.2 kg to larger parts up to 200 kg. The ability to work with various material standards such as ISO, BS, ASTM, ASME, DIN, JIS, and GB ensures that machined parts meet diverse international requirements. Additionally, CNC systems can easily integrate secondary processes like shot blasting, galvanizing, or painting, providing a comprehensive solution for part production.
What are the key factors in selecting materials for machined parts?
Material properties and performance requirements
Selecting the right material for machined parts is crucial to ensure optimal performance and longevity. The choice depends on various factors, including the part's intended function, operating environment, and specific performance requirements. For instance, SG Iron offers excellent ductility and impact resistance, making it suitable for parts subject to dynamic loads. Carbon Steel provides high strength and good machinability, ideal for structural components. Stainless steel is preferred for its corrosion resistance and is widely used in food processing and medical equipment. Alloy Steel offers enhanced properties like improved strength or heat resistance, crucial for specialized applications. Aluminum is valued for its light weight and good thermal conductivity, often used in aerospace and automotive industries. Copper, with its excellent electrical and thermal conductivity, is essential for electrical components. The selection process must consider factors such as tensile strength, hardness, thermal properties, and chemical resistance to ensure the machined parts meet the specific demands of their intended application.
Machinability and cost considerations
Machinability is a critical factor in material selection for machined parts, directly impacting production efficiency and cost. Materials with good machinability, such as certain grades of aluminum and mild steel, allow for faster cutting speeds, longer tool life, and better surface finishes. This translates to reduced machining time and lower production costs. However, harder materials like some stainless steels or titanium alloys, while offering superior properties, may require specialized tooling and slower machining speeds, increasing production costs. The balance between material properties and machinability often involves trade-offs. For instance, a more expensive, easily machinable material might be more cost-effective in the long run due to reduced machining time and tool wear. Cost considerations also extend to material availability and form (e.g., bar stock, plate, or casting). The weight range of 0.2 - 200 kgs for machined parts suggests a need for materials that can be efficiently processed in various sizes and shapes. Additionally, the ability to achieve a machining precision of 0.01mm may influence material choice, as some materials are more conducive to high-precision machining than others.
Surface finish and post-processing requirements
The surface finish of machined parts plays a crucial role in their functionality and aesthetic appeal. Different materials respond differently to machining processes, affecting the achievable surface finish. For instance, aluminum generally allows for excellent surface finishes, while some grades of stainless steel may require additional finishing steps to achieve the desired smoothness. The choice of material must align with the required surface finish, which can range from rough to mirror-like depending on the application. Post-processing requirements also influence material selection. Some machined parts may need additional treatments such as shot blasting for improved surface texture, galvanizing for corrosion protection, or painting for aesthetic or functional purposes. The material must be compatible with these secondary processes. For example, certain alloys may not be suitable for galvanizing, limiting their use in applications requiring this treatment. The ability to achieve specific surface finishes and accommodate post-processing is particularly important for parts with critical dimensions, such as those up to 1200x800x600mm or with diameters below 1000mm. The material's response to these processes can significantly impact the final quality and functionality of the machined parts.
Conclusion
Machining is a fundamental manufacturing process that continues to evolve with technological advancements. From traditional turning and milling to sophisticated CNC systems, machining enables the production of precise, complex parts essential for numerous industries. The selection of appropriate materials, consideration of machining processes, and understanding of post-processing requirements are crucial for creating high-quality machined parts. As manufacturing demands grow more complex, the importance of precision machining in producing components that meet strict specifications and performance requirements cannot be overstated. The future of machining lies in further integration of digital technologies, advanced materials, and innovative processes to meet the ever-increasing demands of modern industry.
Shaanxi Welong Int'l Supply Chain Mgt Co.,Ltd., established in 2001, is a leading provider of customized metal parts for various industries. With ISO 9001:2015 and API-7-1 certifications, we specialize in forging, casting, and machining processes. Our expertise covers a wide range of materials, including iron, steel, aluminum, and alloys. We offer comprehensive services from design optimization to quality control and timely delivery worldwide. With a track record of serving over 100 customers across Europe, North America, and Asia, we are committed to being a leader in international supply chain management. Our focus on innovation, quality, and customer satisfaction positions us at the forefront of China's intelligent manufacturing revolution. For superior machined parts and exceptional service, contact us at info@welongpost.com.
References
1. Smith, J. (2020). Advanced Machining Processes: Principles and Applications. Industrial Press.
2. Johnson, A. & Williams, B. (2019). CNC Machining Handbook: Building, Programming, and Implementation. McGraw-Hill Education.
3. Brown, C. (2018). Modern Manufacturing Processes. Wiley.
4. Davis, R. (2021). Materials Science in Manufacturing. Elsevier.
5. Thompson, L. (2017). Precision Machining Technology. Cengage Learning.
6. Anderson, P. (2022). The Future of Machining: Trends and Innovations. Journal of Manufacturing Technology, 45(3), 178-195.
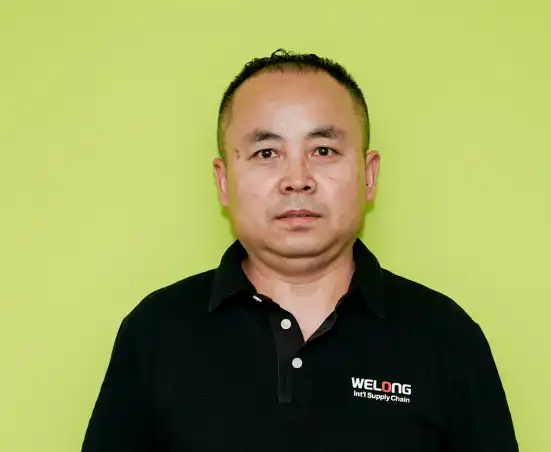
Share your inquiry, get the quotation accordingly!
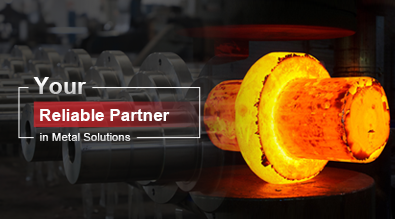
China WELONG- Your Reliable Partner in Metal Solutions