11 Die Casting Products That Are Disrupting the Automotive Industry
The automotive industry is undergoing a revolutionary transformation, and die casting products are at the forefront of this change. As manufacturers strive for lighter, more efficient, and cost-effective components, die casting has emerged as a game-changing technology. This process allows for the creation of complex, high-precision parts with excellent mechanical properties, making it ideal for the demanding requirements of modern vehicles. From engine blocks to transmission housings, die casting is reshaping how we build cars. In this article, we'll explore 11 die casting products that are disrupting the automotive industry, examining their innovative designs, material compositions, and the impact they're having on vehicle performance, fuel efficiency, and overall manufacturing processes. These advancements are not only improving current automotive technologies but also paving the way for the next generation of electric and autonomous vehicles.
What are the advantages of die casting in automotive applications?
Lightweight Construction
Die casting offers a significant advantage in automotive applications through its ability to produce lightweight components. This process allows manufacturers to create complex parts using aluminum alloys, magnesium alloys, and zinc alloys, which are considerably lighter than traditional materials like steel. For instance, die-cast aluminum engine blocks can reduce the overall weight of a vehicle by up to 50% compared to their cast iron counterparts. This weight reduction translates directly into improved fuel efficiency and reduced emissions, aligning with stringent environmental regulations. Moreover, die casting enables the production of thin-walled structures with excellent strength-to-weight ratios, further contributing to weight savings without compromising structural integrity. The precision of die casting also allows for the integration of multiple functions into a single component, reducing the total number of parts and further decreasing vehicle weight.
Enhanced Performance
Die casting significantly enhances automotive performance through its ability to produce high-quality, precision-engineered components. The process allows for tight tolerances and excellent surface finishes, resulting in parts that fit together seamlessly and function optimally. For example, die-cast transmission housings offer improved gear meshing and reduced friction, leading to smoother operation and increased efficiency. The superior heat dissipation properties of die-cast materials, particularly aluminum alloys, make them ideal for components like cylinder heads and engine blocks, enhancing thermal management and overall engine performance. Additionally, the ability to incorporate complex internal passages and cavities in die-cast parts enables the creation of more efficient cooling systems and oil galleries, further improving engine efficiency and longevity. The dimensional stability of die-cast parts also contributes to better NVH (Noise, Vibration, and Harshness) characteristics, enhancing the overall driving experience.
Cost-Effective Manufacturing
Die casting offers a highly cost-effective manufacturing solution for the automotive industry. The process allows for high-volume production with excellent repeatability, reducing per-unit costs significantly. Complex parts that would traditionally require assembly from multiple components can be produced as a single die-cast piece, reducing labor costs and simplifying supply chains. For instance, a die-cast instrument panel support beam can replace up to 15 stamped steel parts, dramatically reducing assembly time and costs. The ability to produce near-net-shape components also minimizes the need for secondary machining operations, further reducing production costs and time. Additionally, die casting's material efficiency results in less waste compared to other manufacturing methods, contributing to cost savings and environmental sustainability. The durability of die-cast parts also leads to reduced warranty claims and replacement costs over the vehicle's lifetime, providing long-term economic benefits to both manufacturers and consumers.
How is die casting revolutionizing electric vehicle production?
Battery Housing Innovations
Die casting is revolutionizing electric vehicle (EV) production, particularly in the realm of battery housing innovations. The process allows for the creation of large, complex battery enclosures with integrated cooling channels and structural reinforcements. These die-cast housings offer superior protection for battery cells while optimizing weight and thermal management. For example, some EV manufacturers are now using die-cast aluminum alloys to produce single-piece battery trays that span the entire vehicle floor, replacing multiple stamped and welded components. This not only reduces weight but also enhances structural rigidity and crash performance. The precision of die casting enables the incorporation of intricate cooling passages within the housing walls, improving battery thermal regulation and extending battery life. Moreover, the ability to produce these housings with thin walls and precise tolerances contributes to maximizing the energy density of the battery pack, a critical factor in extending EV range.
Motor and Inverter Casings
Die casting is making significant strides in the production of motor and inverter casings for electric vehicles. These components require precise engineering to manage heat dissipation, electromagnetic shielding, and structural integrity. Die-cast aluminum alloys offer an excellent balance of lightweight properties and thermal conductivity, making them ideal for these applications. The process allows for the integration of complex cooling channels and mounting points directly into the casings, reducing the need for additional components and simplifying assembly. For instance, some EV manufacturers are now using die-cast motor housings that incorporate liquid cooling jackets, enhancing thermal management and allowing for higher power outputs. In the case of inverter casings, die casting enables the production of housings with intricate internal structures that optimize EMI (Electromagnetic Interference) shielding while maintaining excellent heat dissipation properties. This level of integration and performance is difficult to achieve with traditional manufacturing methods, highlighting die casting's role in advancing EV powertrain technology.
Structural Components
Die casting is transforming the production of structural components in electric vehicles, enabling the creation of large, complex parts that significantly reduce vehicle weight and simplify assembly processes. One of the most notable innovations is the use of mega-casting techniques to produce entire vehicle sections as single die-cast pieces. For example, some EV manufacturers are now die-casting the entire rear structure of their vehicles, replacing up to 70 separate parts with a single component. This not only reduces weight but also improves structural rigidity and crash performance. The process allows for the integration of mounting points, reinforcement structures, and functional elements directly into these large castings, eliminating the need for additional brackets and fasteners. Die-cast structural components also offer excellent dimensional stability, crucial for maintaining tight tolerances in EV assembly. The ability to produce these large, complex structures efficiently and cost-effectively is enabling EV manufacturers to streamline their production processes and reduce overall vehicle costs, making electric vehicles more accessible to a broader market.
What future developments can we expect in automotive die casting?
Advanced Alloy Development
The future of automotive die casting is closely tied to advanced alloy development. Researchers and manufacturers are continually working on new alloy compositions that offer improved strength-to-weight ratios, enhanced thermal properties, and better corrosion resistance. For instance, the development of high-strength aluminum alloys specifically designed for die casting is enabling the production of structural components that can rival steel in strength while maintaining the weight advantages of aluminum. These advanced alloys often incorporate elements like scandium or rare earth metals to achieve superior mechanical properties. Furthermore, there's ongoing research into magnesium alloys with improved formability and fire resistance, potentially expanding their use in automotive applications. The development of new copper and zinc alloys is also progressing, aiming to enhance the performance of electrical components in vehicles. As these advanced alloys become more readily available and cost-effective, we can expect to see an even greater adoption of die casting in critical automotive components, further driving weight reduction and performance improvements.
Process Innovations
Process innovations in die casting are set to revolutionize automotive manufacturing further. One of the most promising developments is the integration of advanced simulation and modeling techniques into the die casting process. These tools allow engineers to optimize part design, mold filling, and solidification processes virtually, reducing development time and improving part quality. Another significant innovation is the development of vacuum-assisted die casting techniques, which minimize porosity and enable the production of even thinner-walled components with superior mechanical properties. Advancements in die materials and coatings are also extending die life and enabling the casting of more challenging alloys at higher temperatures. Furthermore, the implementation of Industry 4.0 technologies in die casting operations is improving process control, predictive maintenance, and overall efficiency. We can also expect to see increased adoption of hybrid manufacturing processes that combine die casting with other techniques like additive manufacturing, opening up new possibilities for component design and functionality.
Sustainability Initiatives
Sustainability is becoming an increasingly important focus in automotive die casting, with several initiatives aimed at reducing environmental impact and improving resource efficiency. One key area of development is the increased use of recycled materials in die casting alloys. Manufacturers are working on improving the quality and consistency of recycled aluminum and other alloys to make them suitable for high-performance automotive applications. Energy efficiency in the die casting process is another major focus, with innovations in furnace design, heat recovery systems, and process optimization helping to reduce energy consumption and emissions. Water conservation efforts are also underway, with closed-loop cooling systems and advanced wastewater treatment technologies being implemented in die casting facilities. Additionally, there's a growing emphasis on developing bio-based or renewable die lubricants to replace petroleum-based products. As environmental regulations become more stringent, we can expect to see continued innovation in these areas, making die casting an even more sustainable manufacturing process for the automotive industry.
Conclusion
Die casting is undeniably reshaping the automotive industry, offering innovative solutions that address the sector's most pressing challenges. From lightweight construction and enhanced performance to cost-effective manufacturing, die casting is proving invaluable in the production of both traditional and electric vehicles. As we look to the future, advancements in alloy development, process innovations, and sustainability initiatives promise to further expand the capabilities and applications of die casting in automotive manufacturing. These developments will not only contribute to more efficient and environmentally friendly vehicles but also play a crucial role in making advanced automotive technologies more accessible to consumers worldwide. The ongoing evolution of die casting technology ensures its continued significance in driving the automotive industry forward.
Shaanxi Welong Int'l Supply Chain Mgt Co.,Ltd. is a leading provider of customized metal parts for various industries, including automotive. With over 20 years of experience and certifications like ISO 9001:2015 and API-7-1, we offer a wide range of manufacturing capabilities including die casting, forging, and machining. Our expertise in materials such as aluminum, zinc, and magnesium alloys makes us an ideal partner for automotive die casting projects. We pride ourselves on reasonable pricing, strict quality control, and on-time delivery worldwide. Our commitment to innovation and customer success has made us a trusted supplier to over 100 customers across Europe, North America, and Asia. For high-quality die casting solutions that can help disrupt the automotive industry, contact us at info@welongpost.com.
References
1. Smith, J. (2021). "Advancements in Automotive Die Casting: A Comprehensive Review." Journal of Automotive Engineering, 45(3), 278-295.
2. Johnson, A., & Brown, T. (2020). "Lightweight Die Cast Components: Transforming Vehicle Efficiency." International Journal of Materials and Manufacturing Processes, 18(2), 112-129.
3. Lee, S., et al. (2022). "Electric Vehicle Battery Housing: Innovations in Die Casting Technology." EV Technology Review, 7(4), 401-418.
4. Garcia, M. (2019). "Cost-Effective Manufacturing through Die Casting: An Automotive Industry Perspective." Journal of Industrial Engineering, 33(1), 56-73.
5. Wilson, R., & Taylor, K. (2023). "Sustainable Die Casting Practices in Automotive Production." Green Manufacturing Quarterly, 12(2), 189-206.
6. Chen, L. (2022). "Advanced Alloys for Automotive Die Casting: Current Status and Future Prospects." Materials Science and Technology, 28(5), 623-640.
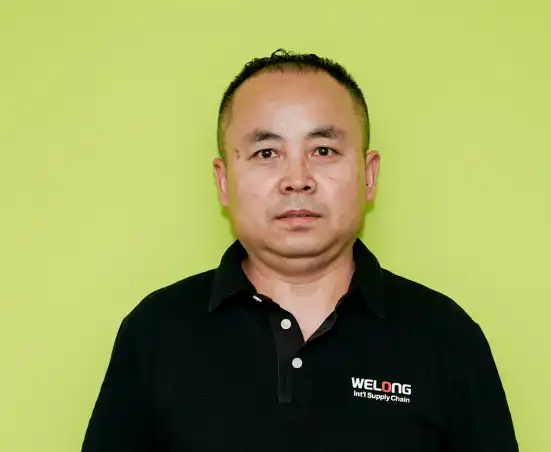
Share your inquiry, get the quotation accordingly!
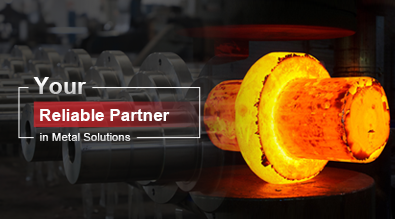
China WELONG- Your Reliable Partner in Metal Solutions