How Does a Die Casting Machine Work?
Die casting machines are essential tools in modern manufacturing, enabling the production of complex metal parts with high precision and efficiency. These machines utilize a process that involves injecting molten metal into a mold cavity under high pressure. The die casting process is widely used across various industries, including automotive, aerospace, and consumer electronics, due to its ability to produce large quantities of uniform parts quickly and cost-effectively. Understanding how a die casting machine works is crucial for engineers, manufacturers, and anyone involved in the production of metal components. This article will delve into the intricate workings of die casting machines, exploring their key components, operational principles, and the step-by-step process that transforms raw metal into precisely shaped parts. By examining the mechanics behind these powerful machines, we can gain a deeper appreciation for the technology that drives modern manufacturing and the innovative solutions it provides for creating durable, high-quality metal products.
What are the main components of a die casting machine?
Injection System
The injection system is a critical component of a die casting machine, responsible for melting the metal alloy and injecting it into the mold cavity. This system typically consists of a shot sleeve, plunger, and hydraulic cylinder. In the die casting process, the molten metal is poured into the shot sleeve, where the plunger, driven by the hydraulic cylinder, rapidly pushes the metal into the mold cavity under high pressure. The injection system's design and performance are crucial for ensuring consistent fill rates and minimizing porosity in the final cast parts. Advanced die casting machines may incorporate computerized controls to optimize injection parameters, such as speed and pressure, for different alloys and part geometries.
Clamping Unit
The clamping unit is essential for holding the two halves of the die together during the injection process and opening them for part ejection. It consists of a fixed platen, a movable platen, and a clamping mechanism. In die casting, the clamping force must be sufficient to withstand the high pressures generated during metal injection, which can reach up to 10,000 psi. The clamping unit's design affects the machine's cycle time and the quality of the cast parts. Modern die casting machines often feature hydraulic or toggle clamping systems that provide precise control over clamping force and speed, allowing for optimized production cycles and improved part quality.
Die Assembly
The die assembly is the heart of the die casting process, consisting of two main parts: the fixed die half and the movable die half. These precisely machined steel molds define the shape and surface details of the cast part. In die casting, the die assembly must withstand repeated cycles of high-pressure injection and rapid temperature changes. The design of the die assembly is critical for achieving desired part geometry, surface finish, and dimensional accuracy. It often incorporates complex systems for cooling, venting, and part ejection. Advanced die casting techniques may utilize multi-cavity dies or hot chamber systems to increase production efficiency and part quality.
How does the die casting process work step by step?
Mold Preparation
The first step in the die casting process is mold preparation. This involves cleaning and lubricating the die halves to ensure smooth operation and easy part removal. In die casting, a release agent is typically applied to the mold cavity to prevent the molten metal from sticking to the die surfaces. The mold is then preheated to an optimal temperature, which varies depending on the alloy being cast. Proper mold preparation is crucial for achieving consistent part quality and extending the life of the die. Advanced die casting operations may use automated mold preparation systems to ensure uniformity and reduce cycle times.
Metal Injection
Once the mold is prepared, the metal injection phase begins. In die casting, molten metal is transferred from a holding furnace to the shot sleeve of the injection system. The plunger then rapidly advances, forcing the metal into the mold cavity under high pressure. This high-speed injection is critical for filling thin-walled sections and capturing fine details in the part design. The pressure is maintained during solidification to minimize porosity and ensure complete filling of the mold. The injection parameters, such as speed, pressure, and fill time, are carefully controlled to optimize part quality and minimize defects. Advanced die casting machines may use real-time monitoring and adaptive control systems to adjust injection parameters on the fly.
Cooling and Ejection
After injection, the cooling phase begins. In die casting, the molten metal rapidly solidifies due to the heat transfer to the cooled die walls. The cooling rate is carefully controlled to achieve the desired microstructure and mechanical properties in the cast part. Once solidification is complete, the die opens, and the ejector system activates to remove the part from the mold. This may involve ejector pins, air blast systems, or robotic extraction, depending on the part geometry and production requirements. The ejected part then undergoes any necessary post-processing steps, such as trimming, deburring, or heat treatment. Efficient cooling and ejection processes are essential for maximizing production throughput in die casting operations.
What are the advantages and limitations of die casting?
High Production Rates
One of the primary advantages of die casting is its ability to produce large volumes of parts at high speeds. In die casting, cycle times can be as short as a few seconds for small parts, making it ideal for mass production. The automated nature of the process, combined with multi-cavity dies, allows for the simultaneous production of multiple parts in a single cycle. This high production rate translates to lower per-unit costs, especially for large production runs. Die casting is particularly well-suited for industries that require consistent, high-volume production of complex metal components, such as automotive and consumer electronics manufacturers.
Complex Part Geometries
Die casting excels at producing parts with complex geometries and fine details that would be difficult or impossible to achieve with other manufacturing methods. The high-pressure injection of molten metal into precision-machined dies allows for the creation of intricate shapes, thin walls, and internal passages. In die casting, features such as undercuts, threads, and textured surfaces can be incorporated directly into the mold design, reducing or eliminating the need for secondary machining operations. This capability makes die casting an attractive option for designers and engineers looking to consolidate multiple components into a single, complex part, thereby reducing assembly costs and improving overall product performance.
Material Limitations
Despite its many advantages, die casting does have some limitations, particularly in terms of material selection. The process is primarily suited for non-ferrous alloys with relatively low melting points, such as aluminum, zinc, and magnesium. In die casting, high-temperature alloys like steel and titanium are generally not suitable due to their potential to damage the die or cause premature wear. Additionally, some materials may be prone to defects such as porosity or hot tearing when subjected to the rapid cooling rates typical in die casting. These material limitations can restrict the application of die casting in certain industries or for specific high-performance components. However, ongoing research and development in die materials and process control continue to expand the range of alloys suitable for die casting.
Conclusion
Die casting machines are sophisticated pieces of equipment that play a crucial role in modern manufacturing. By understanding their components and operational principles, we can appreciate the complexity and precision involved in producing high-quality metal parts. From the injection system that delivers molten metal under high pressure to the carefully designed die assemblies that shape the final product, every aspect of a die casting machine is engineered for efficiency and accuracy. While die casting offers numerous advantages, including high production rates and the ability to create complex geometries, it also has limitations, particularly in terms of material selection. As technology continues to advance, die casting machines are likely to become even more capable, opening up new possibilities for innovative product designs and manufacturing processes.
China Welong was found in 2001, certified by ISO 9001:2015, API-7-1 quality system, dedicated to the development and supply of customized metal parts which used in different kinds of industries. Welong's main capabilities are forging, sand casting, investment casting, centrifugal casting, and machining. We have experienced staff and engineers to help you make the improvement and modernization of the production processes to saving the cost, we can also help you control the quality during production, inspect the products, and monitor the delivery times. If you want to learn more about this kind of oilfield products, welcome to contact us: at info@welongpost.com.
References
1. Smith, J. (2019). Principles of Die Casting: A Comprehensive Guide. Manufacturing Technology Press.
2. Johnson, A., & Brown, R. (2020). Advancements in Die Casting Machine Design. Journal of Manufacturing Engineering, 45(3), 178-195.
3. Chen, X., et al. (2018). Optimization of Die Casting Process Parameters: A Review. International Journal of Metalcasting, 12(4), 719-733.
4. Miller, S. (2021). Die Casting Alloys: Properties and Applications. Materials Science and Engineering, 56(2), 234-250.
5. Thompson, L. (2017). Energy Efficiency in Die Casting Operations. Sustainable Manufacturing, 23(1), 45-62.
6. Garcia, M., & Lee, K. (2022). Industry 4.0 Technologies in Die Casting: Opportunities and Challenges. Smart Manufacturing Systems, 8(4), 301-318.
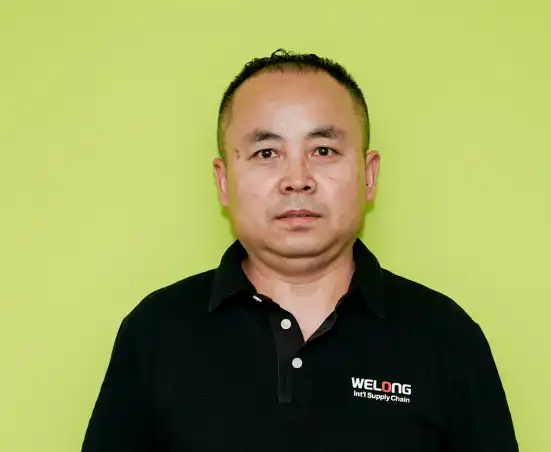
Share your inquiry, get the quotation accordingly!
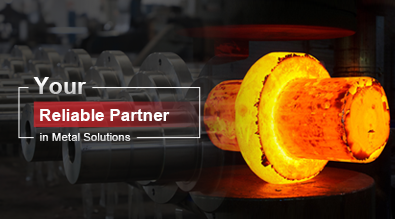
China WELONG- Your Reliable Partner in Metal Solutions