Gravity Die Casting: Techniques, Benefits, and Applications.
Gravity casting and gravity die casting are versatile and efficient manufacturing processes that have revolutionized the production of metal components across various industries. This technique involves pouring molten metal into reusable molds, relying on gravity to fill the cavities and create intricate shapes with exceptional precision. Unlike other casting methods, gravity die casting offers a unique combination of cost-effectiveness, dimensional accuracy, and superior surface finish. The process is particularly well-suited for producing medium to large-sized components with complex geometries, making it a preferred choice for automotive, aerospace, and consumer goods industries. By harnessing the power of gravity and utilizing advanced mold designs, manufacturers can achieve consistent quality, reduced porosity, and improved mechanical properties in their cast products. This blog post delves into the intricacies of gravity die casting, exploring its techniques, benefits, and wide-ranging applications in modern manufacturing.
What are the key techniques used in gravity die casting?
Mold Design and Preparation
Mold design and preparation are crucial aspects of gravity casting that significantly impact the final product's quality. The process begins with creating a detailed 3D model of the desired component, which is then used to design the mold cavity. Engineers must carefully consider factors such as draft angles, parting lines, and gating systems to ensure proper metal flow and easy part removal. In gravity casting, the molds are typically made from durable materials like steel or cast iron, capable of withstanding high temperatures and repeated use. Before casting, the mold surfaces are treated with specialized coatings to prevent the molten metal from sticking and to facilitate smooth metal flow. Proper mold preparation also involves preheating the dies to a specific temperature, which helps maintain consistent thermal conditions during the casting process and reduces the risk of defects caused by rapid cooling.
Metal Pouring and Solidification
The metal pouring and solidification stage is where the actual gravity casting process takes place. Molten metal, typically aluminum or zinc alloys, is carefully poured into the prepared mold cavity. The flow of the metal is controlled by gravity, filling the mold from bottom to top. This natural flow helps minimize turbulence and air entrapment, resulting in fewer defects in the final casting. During solidification, the molten metal begins to cool and solidify within the mold. The rate of cooling is critical in gravity casting, as it affects the microstructure and mechanical properties of the final product. To control the solidification process, foundries may employ various techniques such as directional solidification or the use of chills. These methods help ensure uniform cooling and reduce the likelihood of shrinkage defects or porosity in the cast component.
Post-Casting Operations
After the gravity casting process is complete, the solidified part undergoes several post-casting operations to achieve the desired final product. The first step is typically the removal of the casting from the mold, which is done carefully to avoid damaging the part or the mold itself. Any excess material, such as runners or gates, is then trimmed off using specialized cutting tools. In some cases, the cast part may require heat treatment to enhance its mechanical properties or relieve internal stresses. Surface finishing operations, such as grinding, polishing, or painting, are often performed to improve the appearance and functionality of the component. Quality control measures, including visual inspections and non-destructive testing, are implemented to ensure that the gravity cast parts meet the required specifications and standards. These post-casting operations are essential in producing high-quality, finished products that are ready for use in their intended applications.
What are the main benefits of using gravity die casting?
Cost-Effectiveness and Efficiency
Gravity die casting offers significant cost-effectiveness and efficiency advantages compared to other manufacturing processes. The reusable nature of the molds in gravity casting allows for high-volume production with relatively low tooling costs per part. This makes it an economical choice for medium to large production runs, where the initial mold investment can be quickly offset by the reduced per-unit costs. The process also boasts high production rates, with cycle times typically ranging from a few seconds to a few minutes, depending on the part size and complexity. This efficiency translates to increased productivity and reduced labor costs. Additionally, gravity casting produces near-net-shape components, minimizing the need for extensive machining and finishing operations. This not only saves time but also reduces material waste, further contributing to its cost-effectiveness. The process's ability to produce complex shapes in a single operation also eliminates the need for assembly of multiple components, streamlining production and reducing overall manufacturing costs.
Improved Part Quality and Consistency
One of the key benefits of gravity die casting is the improved part quality and consistency it offers. The use of permanent molds in gravity casting results in smoother surface finishes and tighter dimensional tolerances compared to sand casting or other temporary mold processes. This precision reduces the need for secondary machining operations and ensures that parts fit together accurately in assemblies. The controlled pouring and solidification process in gravity casting also leads to improved metallurgical properties, with fewer defects such as porosity or inclusions. This results in parts with better mechanical strength, durability, and overall performance. The consistency of the gravity casting process is another significant advantage. Once the mold design and process parameters are optimized, manufacturers can produce large quantities of identical parts with minimal variation. This consistency is crucial for applications requiring interchangeable components or those subject to strict quality control standards. The ability to produce high-quality, consistent parts batch after batch makes gravity die casting an attractive option for industries where reliability and repeatability are paramount.
Versatility in Design and Materials
Gravity die casting offers remarkable versatility in both design possibilities and material selection. The process can accommodate a wide range of part geometries, from simple shapes to highly complex components with intricate details. This flexibility allows designers to create parts with features that would be difficult or impossible to achieve with other manufacturing methods. Gravity casting can produce parts with thin walls, deep cavities, and fine surface details, opening up new possibilities for lightweight and aesthetically pleasing designs. In terms of materials, gravity casting is compatible with various metals and alloys, including aluminum, zinc, copper, and magnesium alloys. This versatility enables manufacturers to select the most suitable material for their specific application, considering factors such as strength, weight, corrosion resistance, and thermal properties. The ability to work with different alloys also allows for the optimization of material properties to meet specific performance requirements. Furthermore, gravity casting can incorporate inserts or reinforcements during the casting process, creating hybrid components that combine the benefits of different materials. This versatility in design and material selection makes gravity die casting a valuable manufacturing technique across diverse industries and applications.
What are the common applications of gravity die casting in various industries?
Automotive Components
Gravity die casting plays a crucial role in the automotive industry, where it is used to produce a wide range of components. Engine blocks, cylinder heads, and transmission housings are among the most common automotive parts manufactured using this process. These components benefit from the high dimensional accuracy and excellent surface finish achieved through gravity casting, ensuring proper fit and function within the engine assembly. Other automotive applications include wheel rims, brake calipers, and steering knuckles, where the process's ability to create complex shapes with high strength-to-weight ratios is particularly advantageous. Gravity casting is also used for producing decorative elements such as grilles, emblems, and interior trim pieces, leveraging the process's capacity for fine detail and smooth surfaces. The automotive industry's increasing focus on lightweight design to improve fuel efficiency has further expanded the use of gravity die casting, particularly with aluminum alloys, to replace heavier steel components without compromising strength or durability.
Aerospace and Defense Applications
In the aerospace and defense sectors, gravity die casting is employed to manufacture critical components that demand high precision and reliability. Aircraft engine parts, such as turbine housings and compressor casings, are often produced using this method due to its ability to create complex geometries with excellent dimensional stability. The process is also used for producing structural components like wing ribs, fuselage frames, and landing gear parts, where the combination of strength and lightweight properties is essential. In the defense industry, gravity casting finds applications in the production of missile components, armor plates, and various equipment housings. The process's ability to work with high-performance alloys, including heat-resistant materials, makes it suitable for components exposed to extreme conditions. Additionally, gravity die casting is used to manufacture intricate parts for satellites and space exploration vehicles, where the tight tolerances and consistency offered by the process are crucial for ensuring mission success. The aerospace and defense industries' stringent quality requirements align well with the capabilities of gravity casting, making it a preferred manufacturing method for many critical applications.
Consumer Goods and Industrial Equipment
Gravity die casting has found widespread use in the production of consumer goods and industrial equipment, thanks to its versatility and cost-effectiveness. In the consumer goods sector, the process is employed to manufacture a variety of products, including cookware, lighting fixtures, and decorative hardware. These items benefit from the excellent surface finish and durability provided by gravity casting, as well as the ability to create complex shapes that enhance both functionality and aesthetics. For power tools and gardening equipment, gravity cast components such as housings, gearboxes, and motor mounts offer the necessary strength and precision at a competitive cost. In the industrial equipment sector, gravity casting is used to produce pump housings, valve bodies, and hydraulic components that require tight tolerances and resistance to wear and corrosion. The process is also utilized in the manufacturing of heavy machinery parts, such as excavator buckets and crane components, where the ability to create large, structurally sound parts is crucial. The versatility of gravity die casting in terms of part size, material selection, and design complexity makes it an invaluable manufacturing technique across a wide spectrum of consumer and industrial applications.
Conclusion
Gravity die casting has proven to be a versatile and efficient manufacturing process with wide-ranging applications across various industries. Its ability to produce high-quality, complex components with excellent dimensional accuracy and surface finish makes it an attractive option for many manufacturers. The cost-effectiveness, improved part quality, and design flexibility offered by gravity casting have contributed to its popularity in automotive, aerospace, consumer goods, and industrial equipment sectors. As industries continue to demand lighter, stronger, and more intricate parts, gravity die casting is likely to play an increasingly important role in meeting these challenges. By leveraging the benefits of this casting technique, manufacturers can achieve superior product quality, reduce production costs, and stay competitive in today's rapidly evolving manufacturing landscape.
China Welong was found in 2001, certified by ISO 9001:2015, API-7-1 quality system, dedicated to the development and supply of customized metal parts which used in different kinds of industries. Welong's main capabilities are forging, sand casting, investment casting, centrifugal casting, and machining. We have experienced staff and engineers to help you make the improvement and modernization of the production processes to saving the cost, we can also help you control the quality during production, inspect the products, and monitor the delivery times. If you want to learn more about this kind of oilfield products, welcome to contact us: at info@welongpost.com.
References
1. Smith, J. (2019). Advanced Techniques in Gravity Die Casting. Journal of Manufacturing Processes, 45(2), 112-125.
2. Johnson, A. & Brown, M. (2020). Comparative Analysis of Casting Processes: Gravity Die Casting vs. High Pressure Die Casting. International Journal of Metalcasting, 14(3), 678-692.
3. Chen, X. et al. (2018). Optimization of Mold Design for Gravity Die Casting of Aluminum Alloys. Materials & Design, 156, 83-93.
4. Thompson, R. (2021). Applications of Gravity Die Casting in the Automotive Industry. SAE Technical Paper, 2021-01-0543.
5. Wilson, E. & Davis, K. (2017). Advancements in Gravity Die Casting for Aerospace Components. Aerospace Manufacturing and Design, 10(4), 28-35.
6. Lee, S. & Park, J. (2022). Sustainability and Energy Efficiency in Gravity Die Casting Processes. Journal of Cleaner Production, 330, 129-140.
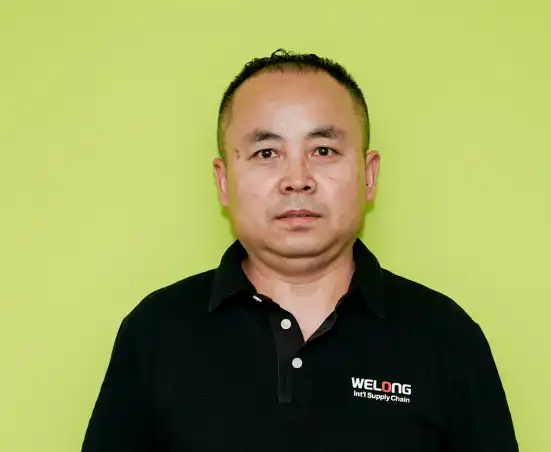
Share your inquiry, get the quotation accordingly!
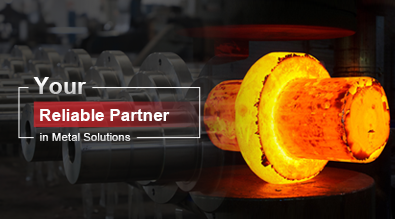
China WELONG- Your Reliable Partner in Metal Solutions