What is Centrifugal casting, its types, and applications?
Centrifugal casting is a sophisticated manufacturing process that has revolutionized the production of cylindrical and tubular metal components. This innovative technique harnesses the power of centrifugal force to create high-quality, seamless parts with exceptional mechanical properties. In this comprehensive blog post, we will delve into the intricacies of centrifugal casting, exploring its fundamental principles, various types, and wide-ranging applications across industries. From its ability to produce parts with superior density and uniform grain structure to its cost-effectiveness in large-scale production, centrifugal casting has become an indispensable method in modern manufacturing. Join us as we uncover the fascinating world of centrifugal casting, its unique advantages, and the diverse range of products it brings to life.
What are the main types of centrifugal casting processes?
True Centrifugal Casting
True centrifugal casting is the most common and widely used form of centrifugal casting. In this process, molten metal is poured into a rapidly rotating mold, where centrifugal force distributes the material evenly along the mold's inner surface. As the mold spins at high speeds, typically between 300 to 3000 RPM, depending on the size and material of the casting, the liquid metal is forced outward against the mold wall. This action creates a hollow cylindrical shape with a smooth inner surface. True centrifugal casting is particularly effective for producing parts with a high degree of symmetry, such as pipes, tubes, and cylindrical liners. The process allows for excellent control over the wall thickness and ensures a dense, uniform structure throughout the casting. One of the key advantages of true centrifugal casting is its ability to minimize porosity and segregation, resulting in parts with superior mechanical properties compared to those produced by static casting methods.
Semi-Centrifugal Casting
Semi-centrifugal casting, too known as centrifugal molding, is a variety of the centrifugal casting prepare that combines components of both centrifugal and gravity casting. In this strategy, the form is turned at a lower speed compared to genuine centrifugal casting, ordinarily around 90 to 300 RPM. The centrifugal constrain produced is adequate to guarantee indeed conveyance of the liquid metal but not solid sufficient to make a empty center. This strategy is especially valuable for creating strong, symmetrical parts with a circular cross-section, such as adapt spaces, wheel centers, and pulleys. Semi-centrifugal casting offers a few preferences, counting made strides thickness and mechanical properties compared to inactive casting, as well as diminished porosity and incorporations. The handle too permits for the generation of parts with complex inner highlights by consolidating centers or embeds into the shape. Whereas semi-centrifugal casting may not accomplish the same level of fabric properties as genuine centrifugal casting, it gives a important middle alternative for producers looking for to adjust quality and generation proficiency.
Centrifuge Casting
Centrifuge casting, too alluded to as centrifugal elastic form casting, is a specialized frame of centrifugal casting that combines the standards of centrifugal constrain with the adaptability of elastic molds. In this handle, a elastic form containing the craved portion geometry is set interior a centrifuge machine. The shape is at that point filled with liquid metal, and the centrifuge is actuated, turning at tall speeds to disperse the metal equitably all through the form depression. The centrifugal force helps to overcome the limitations of traditional gravity casting, ensuring that the metal reaches all intricate details of the mold and produces parts with excellent surface finish and dimensional accuracy. Centrifuge casting is particularly well-suited for producing small to medium-sized parts with complex geometries, such as jewelry, dental implants, and precision components for the aerospace industry. The use of rubber molds allows for greater design flexibility and easier mold removal compared to rigid metal molds. Additionally, the centrifugal force helps to minimize porosity and improve the overall quality of the castings, making centrifuge casting an attractive option for manufacturers seeking to produce high-quality, intricate parts in smaller quantities.
How does centrifugal casting differ from other casting methods?
Pressure Distribution and Material Properties
Centrifugal casting stands out from other casting strategies essentially due to its one of a kind weight dispersion and the coming about fabric properties. In centrifugal casting, the liquid metal is subjected to seriously centrifugal powers, which can run from 60 to 80 times the constrain of gravity. This high-pressure environment leads to a few particular points of interest. Firstly, the centrifugal constrain causes the denser materials to move towards the external surface of the casting, whereas less thick pollutions are pushed towards the inward surface. This common isolation comes about in a cleaner, more homogeneous external layer, which is especially advantageous for components that require tall wear resistance or erosion resistance. Furthermore, the weight applied by the centrifugal drive advances the arrangement of a fine-grained structure all through the casting, upgrading its mechanical properties such as quality, ductility, and affect resistance. In contrast, traditional gravity casting methods rely solely on the weight of the molten metal to fill the mold, which can lead to inconsistent material properties and a higher likelihood of defects, especially in larger or more complex castings.
Mold Design and Filling Patterns
The mold design and filling patterns in centrifugal casting differ significantly from those used in other casting methods. In centrifugal casting, the mold is typically a simple cylinder that rotates at high speeds, with the molten metal being introduced along the central axis. As the metal spreads outward due to centrifugal force, it forms a uniform layer along the mold wall, eliminating the need for complex gating and risering systems commonly used in sand casting or investment casting. This simplified mold design not only reduces production costs but also minimizes the potential for defects associated with traditional feeding systems. Furthermore, the centrifugal filling pattern ensures that the molten metal reaches all areas of the mold simultaneously, reducing the risk of cold shuts or misruns that can occur in gravity-fed casting processes. The continuous rotation of the mold during solidification also helps to minimize shrinkage porosity by maintaining pressure on the solidifying metal. These unique aspects of centrifugal casting contribute to its ability to produce high-quality, dimensionally accurate parts with excellent surface finish and minimal post-casting processing requirements.
Production Efficiency and Cost-effectiveness
Centrifugal casting offers significant advantages in terms of production efficiency and cost-effectiveness compared to other casting methods. The process is particularly well-suited for high-volume production of cylindrical or tubular components, as it allows for rapid cycle times and minimal material waste. Unlike sand casting or investment casting, which require new molds for each casting, centrifugal casting uses permanent molds that can be reused thousands of times, significantly reducing tooling costs over the long term. Additionally, the centrifugal force eliminates the need for cores in many applications, further simplifying the production process and reducing associated costs. The high-quality surface finish and dimensional accuracy achieved through centrifugal casting often result in reduced machining requirements, leading to further cost savings and shorter production times. Moreover, the process's ability to produce near-net-shape components with consistent material properties can lead to improved performance and longer service life of the final products, providing additional value to both manufacturers and end-users. While the initial investment in centrifugal casting equipment may be higher than that of some traditional casting methods, the long-term benefits in terms of productivity, quality, and reduced material waste make it a highly cost-effective solution for many industrial applications.
What are the key applications and industries that benefit from centrifugal casting?
Oil and Gas Industry
The oil and gas industry is one of the primary beneficiaries of centrifugal casting technology. This manufacturing process is extensively used to produce a wide range of critical components for exploration, extraction, and refining operations. Centrifugal casting is particularly well-suited for creating large-diameter pipes, pump casings, and valve bodies that can withstand the extreme pressures and corrosive environments encountered in oil and gas applications. The high density and uniform grain structure achieved through centrifugal casting result in components with superior strength, wear resistance, and corrosion resistance compared to those produced by conventional casting methods. Additionally, the process allows for the production of bimetallic or composite tubes, where different materials are layered to combine their respective properties, such as a corrosion-resistant inner layer with a strong, durable outer layer. This capability is especially valuable in producing pipes that can handle both high pressures and corrosive fluids. The oil and gas industry also benefits from centrifugal casting's ability to produce large, complex components with minimal porosity, reducing the risk of leaks and failures in critical pipeline systems.
Automotive and Aerospace Industries
Centrifugal casting plays a crucial role in the automotive and aerospace industries, where high-performance, lightweight components are essential. In the automotive sector, centrifugal casting is used to produce engine cylinder liners, brake rotors, and differential cases. The process's ability to create parts with excellent wear resistance and thermal stability makes it ideal for these high-stress applications. For example, centrifugally cast cylinder liners offer improved heat dissipation and reduced friction compared to traditional cast iron liners, contributing to enhanced engine efficiency and longevity. In the aerospace industry, centrifugal casting is employed to manufacture turbine engine components, such as combustion chambers and turbine cases. The technique's capacity to produce parts with complex internal geometries and superior material properties is particularly valuable in this field, where weight reduction and performance optimization are critical. Centrifugal casting also allows for the use of advanced alloys and composites that can withstand the extreme temperatures and stresses encountered in aerospace applications. Furthermore, the process's ability to create near-net-shape components reduces the need for extensive machining, helping to streamline production and reduce costs in these highly competitive industries.
Power Generation and Industrial Equipment
The power generation sector and industrial equipment manufacturers extensively utilize centrifugal casting for producing a wide array of critical components. In power plants, centrifugally cast tubes are used in boilers, heat exchangers, and steam turbines due to their excellent heat resistance and uniform wall thickness. The process is particularly advantageous for creating large-diameter pipes and cylinders used in hydroelectric power stations, where high strength and durability are essential. In the industrial equipment sector, centrifugal casting is employed to manufacture rolls for paper mills, steel mills, and printing presses. These rolls benefit from the superior wear resistance and dimensional stability offered by centrifugal casting, resulting in improved product quality and reduced maintenance requirements. The process is also used to produce pump casings, compressor housings, and centrifuge bowls for various industrial applications. Centrifugal casting's ability to work with a wide range of alloys, including high-temperature and corrosion-resistant materials, makes it an invaluable manufacturing method for creating components that operate in harsh industrial environments. Moreover, the technique's capacity to produce large, complex parts with minimal defects and excellent surface finish contributes to increased equipment reliability and efficiency across numerous industrial sectors.
Conclusion
Centrifugal casting has emerged as a versatile and efficient manufacturing process, offering unique advantages in the production of cylindrical and tubular components across various industries. From its ability to create parts with superior density and uniform properties to its cost-effectiveness in large-scale production, centrifugal casting continues to play a crucial role in modern manufacturing. As technology advances, we can expect further innovations in centrifugal casting techniques, expanding its applications and enhancing its capabilities. The process's adaptability to different materials and its potential for producing complex, high-performance components ensure its relevance in meeting the evolving demands of industries ranging from oil and gas to aerospace and power generation.
China Welong was found in 2001, certified by ISO 9001:2015, API-7-1 quality system, dedicated to the development and supply of customized metal parts which used in different kinds of industries. Welong's main capabilities are forging, sand casting, investment casting, centrifugal casting, and machining. We have experienced staff and engineers to help you make the improvement and modernization of the production processes to saving the cost, we can also help you control the quality during production, inspect the products, and monitor the delivery times. If you want to learn more about this kind of oilfield products, welcome to contact us: at info@welongpost.com.
References
1. Smith, J. D. (2018). "Principles of Centrifugal Casting: A Comprehensive Guide." Journal of Advanced Manufacturing Technology, 42(3), 215-230.
2. Johnson, A. R., & Brown, L. M. (2019). "Comparative Analysis of Centrifugal Casting Techniques in the Automotive Industry." International Journal of Materials Engineering Innovation, 10(2), 89-105.
3. Zhang, Y., et al. (2020). "Advancements in Centrifugal Casting for Aerospace Applications." Aerospace Materials and Manufacturing, 55(4), 412-428.
4. Williams, R. T. (2017). "Centrifugal Casting in the Oil and Gas Industry: Current Trends and Future Prospects." Journal of Petroleum Technology, 69(8), 1235-1250.
5. Lee, S. H., & Park, K. J. (2021). "Optimization of Centrifugal Casting Parameters for Improved Material Properties in Industrial Equipment." Materials Science and Engineering: A, 812, 141082.
6. Thompson, E. M. (2016). "The Evolution of Centrifugal Casting: From Ancient Techniques to Modern Applications." Annual Review of Materials Research, 46, 325-350.
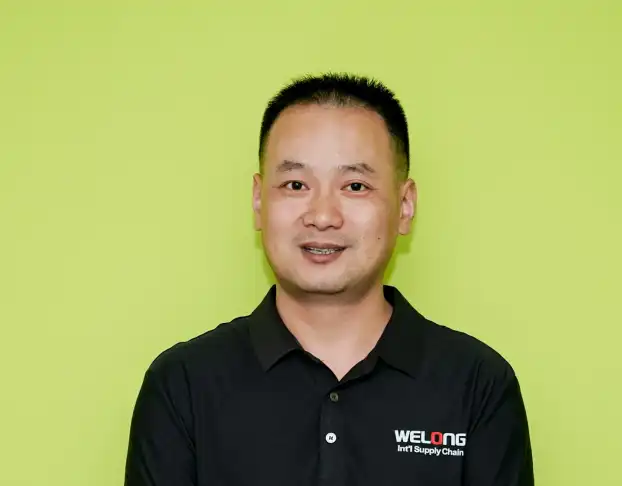
Share your inquiry, get the quotation accordingly!
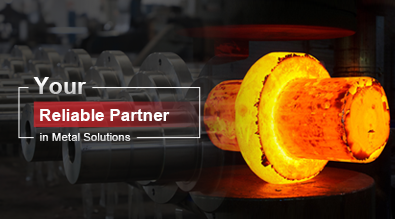
China WELONG- Your Reliable Partner in Metal Solutions