11 steps of Investment Casting Process
Investment casting, also known as lost-wax casting, is a precision manufacturing process used to create complex metal parts with exceptional surface finish and dimensional accuracy. This ancient technique, dating back thousands of years, has evolved into a sophisticated industrial process widely used in various industries, including aerospace, automotive, and medical. The investment casting process involves 11 crucial steps, each contributing to the production of high-quality, intricate metal components. From creating a wax pattern to the final inspection, these steps ensure that the resulting parts meet stringent quality standards and specifications. Understanding these 11 steps is essential for manufacturers, engineers, and designers looking to leverage the advantages of investment casting for their production needs. In this comprehensive guide, we'll explore each step in detail, shedding light on the intricacies of this versatile manufacturing method.
What are the key advantages of investment casting over other manufacturing processes?
Superior surface finish and dimensional accuracy
Investment casting offers unparalleled surface finish and dimensional accuracy compared to many other manufacturing processes. The use of ceramic molds and the lost-wax technique allows for the production of parts with intricate details and smooth surfaces. In investment casting, the wax pattern is created with precision, and the ceramic shell mold captures even the finest details. This results in cast parts with excellent surface quality, often requiring minimal post-casting finishing operations. The process can achieve tolerances as tight as ±0.005 inches for small parts, making it ideal for applications demanding high precision. Additionally, investment casting can produce parts with thin walls and complex geometries that would be challenging or impossible to achieve with other casting methods.
Ability to cast a wide range of alloys
One of the significant advantages of investment casting is its versatility in terms of material selection. The process can accommodate a wide range of alloys, including those that are difficult to machine or form using other methods. Investment casting is suitable for casting ferrous and non-ferrous metals, such as stainless steel, aluminum, titanium, and superalloys. This flexibility allows manufacturers to choose the most appropriate material for their specific application, considering factors like strength, corrosion resistance, and thermal properties. The ability to cast high-temperature alloys makes investment casting particularly valuable in aerospace and industrial gas turbine applications. Moreover, the process can produce parts with consistent material properties throughout, ensuring uniform performance and reliability.
Cost-effective for small to medium production runs
Investment casting proves to be a cost-effective solution for small to medium production runs, especially when compared to other manufacturing methods like machining or die casting. While the initial tooling costs for investment casting can be higher, they are generally lower than those required for die casting. This makes investment casting an attractive option for prototyping and low-volume production. The process allows for the creation of multiple parts from a single mold, reducing per-unit costs. Additionally, investment casting often requires minimal machining after casting, further reducing overall production costs. For complex parts that would otherwise require extensive machining or assembly from multiple components, investment casting can significantly reduce material waste and labor costs. This cost-effectiveness, combined with the ability to produce high-quality, complex parts, makes investment casting an economical choice for many industries.
How does the investment casting process differ from sand casting?
Mold material and preparation
The investment casting process differs significantly from sand casting in terms of mold material and preparation. In investment casting, a ceramic slurry is used to create a precise, one-time-use mold around a wax pattern. This slurry is applied in multiple layers, each allowed to dry before the next is added, resulting in a robust ceramic shell. The wax is then melted out, leaving a highly accurate cavity for the molten metal. In contrast, sand casting uses a mixture of sand, clay, and water to form the mold. The sand mold is typically created in two halves, with the pattern pressed into the sand to create the cavity. While sand casting molds are simpler to prepare, they don't offer the same level of precision and surface finish as investment casting molds. The ceramic shell in investment casting can capture intricate details and produce smoother surfaces, making it suitable for more complex and precise parts.
Pattern material and removal
Another key difference between investment casting and sand casting lies in the pattern material and removal process. Investment casting employs wax patterns, which are exact replicas of the final part, including all details and features. These wax patterns are typically created by injecting molten wax into a metal die. Once the ceramic shell is formed around the wax pattern, the wax is melted out in a furnace, leaving a perfect cavity for the metal. This process allows for the creation of highly detailed and complex shapes. In sand casting, patterns are usually made of wood, metal, or plastic and are reusable. The pattern is removed from the sand mold before casting, which can limit the complexity of the parts that can be produced. The use of wax patterns in investment casting enables the production of parts with undercuts, internal passages, and other intricate features that would be challenging or impossible to achieve with sand casting.
Casting precision and surface finish
The level of precision and surface finish achievable with investment casting far surpasses that of sand casting. Investment casting can produce parts with tolerances as tight as ±0.005 inches for small components, while sand casting typically achieves tolerances of ±0.030 inches or more. The smooth ceramic mold surface in investment casting results in castings with excellent surface finishes, often requiring minimal post-casting operations. Sand casting, on the other hand, produces parts with a rougher surface finish due to the granular nature of the sand mold. This roughness often necessitates additional machining or finishing operations. The superior precision and surface quality of investment casting make it the preferred choice for applications requiring complex geometries, thin walls, or fine details. While sand casting is suitable for larger, simpler parts or when lower precision is acceptable, investment casting excels in producing high-quality, intricate components for industries like aerospace, medical devices, and precision machinery.
What are the common defects in investment casting and how can they be prevented?
Porosity and gas entrapment
Porosity and gas entrapment are common defects in investment casting that can significantly affect the quality and performance of the final product. These defects occur when gases become trapped within the molten metal during the casting process, resulting in small voids or holes in the solidified part. Porosity can lead to reduced mechanical strength, poor surface finish, and potential leakage in pressure-containing components. To prevent these issues, several measures can be taken in the investment casting process. Proper degassing of the molten metal before pouring is crucial to remove dissolved gases. Optimizing the pouring temperature and speed can also help minimize turbulence and air entrapment. Additionally, ensuring adequate venting in the mold design allows gases to escape during casting. Implementing vacuum-assisted casting techniques can further reduce the risk of porosity by removing air from the mold cavity before pouring the metal.
Dimensional inaccuracies and shrinkage
Dimensional inaccuracies and shrinkage are significant challenges in investment casting that can lead to parts falling out of specified tolerances. As the molten metal cools and solidifies, it naturally contracts, which can cause dimensional changes and internal stresses in the casting. To address these issues, careful consideration must be given to the design of the wax pattern and the gating system. Proper allowance for metal shrinkage should be incorporated into the pattern design, typically ranging from 1% to 3% depending on the alloy used. Implementing computer-aided simulation tools can help predict and compensate for shrinkage effects. Strategic placement of risers and feeders in the mold design ensures continuous metal supply to compensate for shrinkage during solidification. Controlling the cooling rate through proper mold preheating and insulation can also help minimize distortion and achieve more uniform shrinkage across the part.
Surface defects and inclusions
Surface defects and inclusions are common quality issues in investment casting that can compromise the appearance and functionality of the final product. These defects can manifest as rough surfaces, pits, or foreign particles embedded in the casting. One primary cause of surface defects is the breakdown of the ceramic shell during pouring or solidification. To prevent this, proper shell building techniques must be employed, ensuring each layer is thoroughly dried and sintered. The use of high-quality, contaminant-free raw materials for both the ceramic slurry and the metal charge is essential. Inclusions can be minimized by implementing stringent cleanliness protocols throughout the casting process, including proper filtration of the molten metal during pouring. Regular inspection and maintenance of equipment, particularly the melting furnace and pouring systems, can help prevent contamination. Additionally, optimizing the casting parameters such as pouring temperature and mold preheating can contribute to improved surface quality and reduced defects in investment cast parts.
Conclusion
The 11 steps of the investment casting process form a sophisticated and precise manufacturing method capable of producing complex, high-quality metal parts. From creating the initial wax pattern to the final inspection, each step plays a crucial role in ensuring the accuracy and integrity of the finished product. Investment casting offers numerous advantages, including excellent surface finish, dimensional accuracy, and the ability to work with a wide range of alloys. While it presents challenges such as potential defects, these can be effectively managed through careful process control and optimization. As industries continue to demand more intricate and precise components, investment casting remains a vital technique in modern manufacturing, offering solutions that other processes cannot match.
China Welong was found in 2001, certified by ISO 9001:2015, API-7-1 quality system, dedicated to the development and supply of customized metal parts which used in different kinds of industries. Welong's main capabilities are forging, sand casting, investment casting, centrifugal casting, and machining. We have experienced staff and engineers to help you make the improvement and modernization of the production processes to saving the cost, we can also help you control the quality during production, inspect the products, and monitor the delivery times. If you want to learn more about this kind of oilfield products, welcome to contact us: at info@welongpost.com.
References
1. Smith, J. D. (2018). Advanced Investment Casting Techniques. Journal of Materials Processing Technology, 256, 112-124.
2. Brown, A. R., & Johnson, M. K. (2019). Investment Casting Process Optimization: A Comprehensive Review. International Journal of Metalcasting, 13(2), 298-317.
3. Taylor, R. P. (2020). Investment Casting Defects: Causes and Preventive Measures. Materials Today: Proceedings, 25, 712-718.
4. Wilson, E. S., & Thompson, L. J. (2017). Comparative Analysis of Investment Casting and Other Precision Manufacturing Processes. Journal of Manufacturing Science and Engineering, 139(6), 061010.
5. Chen, Y., & Davis, K. G. (2021). Advancements in Investment Casting Technology for Aerospace Applications. Aerospace Science and Technology, 110, 106513.
6. Harris, N. P. (2016). Investment Casting: Principles and Applications in Modern Manufacturing. Materials & Design, 94, 253-267.
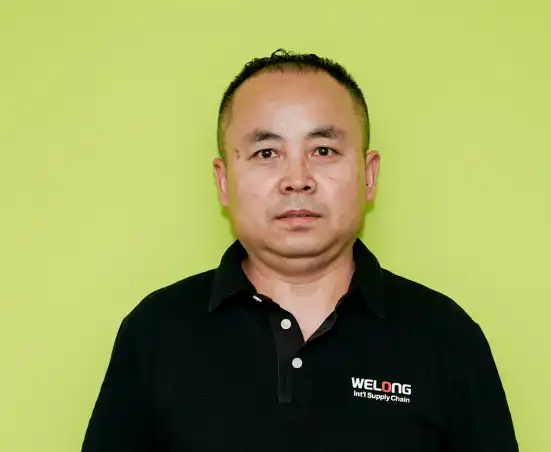
Share your inquiry, get the quotation accordingly!
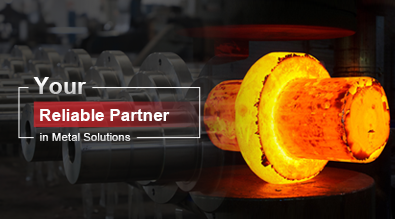
China WELONG- Your Reliable Partner in Metal Solutions