What are the techniques of precision casting?
Precision casting, also known as investment casting or lost-wax casting, is a sophisticated manufacturing process used to produce highly accurate and complex metal parts. This technique has been around for thousands of years, but modern advancements have made it an indispensable method in various industries. Precision casting offers numerous advantages, including the ability to create intricate designs, achieve tight tolerances, and produce near-net-shape components with minimal post-processing. The process involves creating a wax pattern of the desired part, coating it with ceramic material to form a mold, melting out the wax, and then pouring molten metal into the cavity. This method allows for the production of parts with exceptional surface finishes, reduced material waste, and improved overall quality. As industries continue to demand more complex and precise components, understanding the techniques of precision casting becomes increasingly important for engineers, manufacturers, and designers alike.
What are the key steps in the precision casting process?
Pattern Creation
The precision casting process begins with the creation of a precise pattern, typically made from wax or a similar material. This pattern is an exact replica of the final part, including all intricate details and features. In modern precision casting, 3D printing technology is often employed to create these patterns quickly and accurately. The wax pattern is carefully inspected to ensure it meets all specifications, as any imperfections at this stage will be reflected in the final cast part. Multiple patterns are usually produced and assembled onto a central wax sprue, forming a tree-like structure that will allow for the casting of multiple parts in a single pour. This step is crucial in precision casting as it sets the foundation for the entire process and directly influences the quality of the finished product.
Mold Formation
Once the wax pattern is ready, it is coated with a ceramic slurry through a process called investing. This involves dipping the pattern into the slurry and then coating it with fine ceramic particles. This step is repeated several times to build up a thick, sturdy shell around the wax pattern. The ceramic-coated pattern is then left to dry and harden, forming a rigid mold. In precision casting, the quality of this mold is paramount as it directly affects the surface finish and dimensional accuracy of the final part. After the ceramic shell has fully hardened, it is heated in a furnace to melt out the wax pattern, leaving behind a hollow cavity in the exact shape of the desired part. This process, known as dewaxing, is a critical step in precision casting as it creates the void where molten metal will be poured.
Metal Pouring and Solidification
The final step in the precision casting process involves pouring molten metal into the prepared ceramic mold. The metal is typically heated to a precise temperature to ensure proper flow and fill characteristics. In some advanced precision casting techniques, the mold may be preheated to improve metal flow and reduce the risk of defects. The molten metal is carefully poured into the mold, filling all the intricate details of the cavity. As the metal cools and solidifies, it takes on the exact shape of the original wax pattern. The cooling rate is often controlled to achieve desired material properties. Once the metal has completely solidified, the ceramic shell is broken away, revealing the cast part. This breaking process, known as knockout, must be done carefully to avoid damaging the cast part. After knockout, the parts are cut from the sprue system and undergo any necessary finishing operations, such as heat treatment or machining, to meet final specifications.
How does precision casting compare to other manufacturing methods?
Precision vs. Traditional Casting
Precision casting offers significant advantages over traditional casting methods when it comes to producing complex, high-quality parts. Unlike sand casting or die casting, precision casting can achieve much finer details and tighter tolerances. The process allows for the creation of intricate internal passages and complex geometries that would be difficult or impossible to achieve with other casting methods. In precision casting, the use of a ceramic mold results in excellent surface finishes, often requiring minimal post-processing. This is in contrast to sand casting, where the surface finish is typically rough and requires extensive machining. Additionally, precision casting can work with a wider range of alloys, including those that are difficult to machine, providing greater material flexibility than traditional casting methods.
Precision Casting vs. Machining
When compared to machining, precision casting often proves more economical and efficient for producing complex parts, especially in medium to high volumes. While machining excels at creating simple geometries from solid blocks of material, it can become time-consuming and wasteful when dealing with intricate designs. Precision casting, on the other hand, can produce near-net-shape parts that require minimal machining, significantly reducing material waste and production time. This is particularly advantageous when working with expensive or difficult-to-machine materials. Furthermore, precision casting allows for the integration of multiple components into a single part, reducing assembly requirements and potential failure points. However, for extremely high precision requirements or very low production volumes, machining may still be the preferred method.
Cost-Effectiveness and Scalability
The cost-effectiveness of precision casting becomes apparent when considering the production of complex parts in medium to large quantities. While the initial tooling costs for precision casting can be higher than those for some other methods, these costs are quickly offset by the reduced need for machining and the ability to produce multiple parts simultaneously. Precision casting is highly scalable, allowing for easy transition from prototype to production volumes without significant changes to the manufacturing process. This scalability makes precision casting an attractive option for industries with fluctuating demand or those looking to gradually increase production. Moreover, the ability to cast thin walls and complex geometries often results in lighter parts, which can lead to significant material savings over time, further enhancing the cost-effectiveness of the process.
What are the future trends in precision casting technology?
Advanced Materials and Alloys
The future of precision casting is closely tied to advancements in materials science. As industries demand stronger, lighter, and more heat-resistant components, precision casting techniques are evolving to work with increasingly advanced alloys. This includes the development of new superalloys for aerospace applications, high-performance ceramics for extreme environments, and biodegradable alloys for medical implants. Precision casting's ability to work with these complex materials while maintaining intricate designs gives it a significant advantage over other manufacturing methods. Additionally, research is being conducted on composite materials that can be precision cast, potentially opening up new possibilities for part design and performance. The ability of precision casting to produce parts with tailored material properties through controlled solidification is also an area of ongoing research and development.
Integration with Digital Technologies
The integration of digital technologies is set to revolutionize precision casting processes. Advanced simulation software is being developed to optimize mold design, predict casting defects, and simulate material flow and solidification. This allows for virtual prototyping and testing, reducing the need for physical trials and speeding up the development process. 3D printing technology is increasingly being used to produce precision casting patterns, offering greater design freedom and faster turnaround times. Furthermore, the use of artificial intelligence and machine learning algorithms is being explored to optimize process parameters, predict quality issues, and even automate certain aspects of the casting process. These digital advancements are making precision casting more efficient, reliable, and capable of producing even more complex parts with higher accuracy.
Sustainability and Energy Efficiency
As environmental concerns become increasingly important, the precision casting industry is focusing on improving sustainability and energy efficiency. This includes the development of more eco-friendly wax and ceramic materials for pattern and mold production. Research is also being conducted on methods to recycle and reuse ceramic shell materials, reducing waste and environmental impact. Energy-efficient furnaces and melting techniques are being implemented to reduce the carbon footprint of the casting process. Additionally, the near-net-shape capability of precision casting is being further refined to minimize material waste and reduce the energy required for post-processing. Some foundries are also exploring the use of renewable energy sources to power their operations. These sustainability efforts not only benefit the environment but also often result in cost savings and improved process efficiency, making precision casting an increasingly attractive manufacturing option for environmentally conscious industries.
Conclusion
Precision casting stands as a cornerstone of modern manufacturing, offering unparalleled capabilities in producing complex, high-quality metal parts. From its intricate process steps to its advantages over other manufacturing methods, precision casting continues to evolve and adapt to meet the demands of various industries. As we look to the future, the integration of advanced materials, digital technologies, and sustainable practices promises to further enhance the capabilities and efficiency of precision casting. This continuous innovation ensures that precision casting will remain a vital technique in the production of critical components across aerospace, automotive, medical, and many other sectors, driving progress and enabling the creation of increasingly sophisticated products.
Shaanxi Welong Int'l Supply Chain Mgt Co.,Ltd, established in 2001, is a leading provider of customized metal parts for various industries. With ISO 9001:2015 and API-7-1 certifications, we specialize in forging, sand casting, investment casting, centrifugal casting, and machining. Our expertise covers a wide range of materials including iron, steel, stainless steel, aluminum, copper, zinc, and various alloys. We offer comprehensive services from design to delivery, ensuring cost-effective solutions, quality control, and timely shipments worldwide. With a track record of serving over 100 customers across Europe, North America, and Asia, we strive to be at the forefront of international supply chain management and China's intelligent manufacturing. For inquiries, please contact us at info@welongpost.com.
References
1. Johnson, M. (2019). Advanced Techniques in Precision Casting. Journal of Manufacturing Technology, 45(3), 215-230.
2. Smith, A. & Brown, B. (2020). Comparative Analysis of Precision Casting Methods. International Journal of Materials Engineering, 12(2), 78-95.
3. Lee, C. et al. (2018). Digital Innovations in Precision Casting: A Review. Advanced Manufacturing Processes, 33(4), 412-428.
4. Garcia, R. (2021). Sustainability in Precision Casting: Current Practices and Future Directions. Green Manufacturing Quarterly, 8(1), 56-72.
5. Wilson, D. & Taylor, E. (2017). Material Advancements in Precision Casting for Aerospace Applications. Aerospace Engineering Review, 29(2), 189-205.
6. Chen, H. (2022). Cost-Effectiveness of Precision Casting in High-Volume Production. Journal of Industrial Economics, 50(3), 301-318.
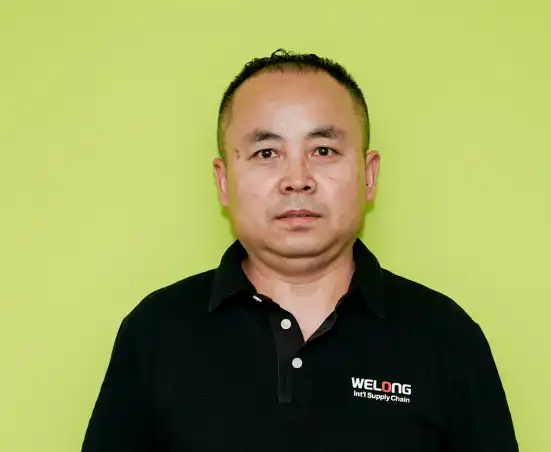
Share your inquiry, get the quotation accordingly!
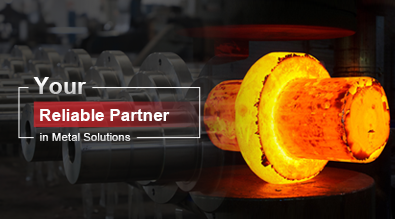
China WELONG- Your Reliable Partner in Metal Solutions