What to Consider in Metal Casting Design?
Metal casting design is a critical aspect of manufacturing that requires careful consideration and planning. When designing parts for metal casting, engineers and designers must take into account various factors to ensure the final product meets quality standards, performs as intended, and can be produced efficiently. The process of metal casting involves pouring molten metal into a mold, allowing it to solidify, and then removing the solidified part. This versatile manufacturing method can produce complex shapes and structures that would be difficult or impossible to achieve through other means. However, successful casting design requires a deep understanding of material properties, casting processes, and design principles. In this blog, we'll explore key considerations in metal casting design, focusing on how these factors impact the production of high-quality casting parts and the overall success of the manufacturing process.
What are the key factors to consider when designing casting parts?
Material Selection
Choosing the right material for casting parts is crucial to the success of the final product. The material selected impacts not only the physical properties of the part but also the casting process itself. When considering materials for casting parts, factors such as strength, durability, weight, corrosion resistance, and thermal properties must be taken into account. Common materials for casting parts include various grades of iron, steel, aluminum, and copper alloys. Each material has its own unique characteristics that affect how it behaves during the casting process and in the final application. For example, aluminum alloys are often chosen for their lightweight properties and excellent corrosion resistance, making them ideal for automotive and aerospace applications. On the other hand, cast iron is known for its excellent wear resistance and ability to dampen vibration, making it suitable for machinery components.
Part Geometry
The geometry of casting parts plays a significant role in the success of the casting process and the quality of the final product. When designing casting parts, it's essential to consider factors such as wall thickness, draft angles, and the overall complexity of the part. Uniform wall thickness is crucial for even cooling and solidification, which helps prevent defects such as warping or internal stresses. Draft angles are necessary to facilitate the removal of the part from the mold without damage. Complex geometries may require the use of cores or special mold designs to achieve the desired shape. Additionally, designers must consider how the part's geometry will affect the flow of molten metal during the casting process. Sharp corners or sudden changes in thickness can lead to turbulence or incomplete filling of the mold, resulting in defects in the casting parts.
Casting Process Selection
Selecting the appropriate casting process is crucial for producing high-quality casting parts efficiently and cost-effectively. Different casting processes have their own strengths and limitations, and the choice depends on factors such as the material being cast, the complexity of the part, production volume, and desired surface finish. Common casting processes include sand casting, investment casting, die casting, and centrifugal casting. For example, sand casting is versatile and suitable for producing large, complex parts in a wide range of materials, but it may have limitations in terms of surface finish and dimensional accuracy. Investment casting, on the other hand, can produce parts with excellent surface finish and tight tolerances but is generally more expensive and better suited for smaller, intricate components. Die casting offers high production rates and excellent dimensional accuracy but is limited to non-ferrous metals and has higher tooling costs. Choosing the right process for casting parts ensures optimal results in terms of quality, cost, and production efficiency.
How does the design of casting parts affect their performance and quality?
Structural Integrity
The design of casting parts has a significant impact on their structural integrity, which is crucial for ensuring the part can withstand the loads and stresses it will experience during use. When designing casting parts, engineers must consider factors such as stress distribution, load-bearing capacity, and potential failure modes. The shape and thickness of various sections of the part should be optimized to provide adequate strength while minimizing weight and material use. Features such as ribs, gussets, and fillets can be incorporated into the design to reinforce critical areas and improve overall structural integrity. Additionally, the orientation of the part during casting can affect its mechanical properties, as the solidification process can lead to variations in grain structure and strength. Proper design considerations for structural integrity not only improve the performance and reliability of casting parts but also help prevent premature failure and extend the lifespan of the components.
Surface Finish
The surface finish of casting parts is an important aspect of their overall quality and can significantly impact their performance and appearance. The design of casting parts plays a crucial role in determining the achievable surface finish. Factors such as part geometry, material selection, and casting process all influence the final surface quality. Complex geometries with deep recesses or sharp corners can be challenging to achieve a smooth surface finish, especially in processes like sand casting. The choice of material also affects surface finish, as some materials are more prone to surface defects or require special treatments to achieve the desired finish. The casting process itself has a significant impact on surface finish, with processes like investment casting generally producing smoother surfaces compared to sand casting. Designers must consider the required surface finish for the casting parts early in the design process and select appropriate materials and processes to achieve the desired results.
Dimensional Accuracy
Achieving and maintaining dimensional accuracy is crucial for the quality and functionality of casting parts. The design of casting parts directly influences the ability to achieve tight tolerances and consistent dimensions. Factors such as shrinkage during solidification, warping due to uneven cooling, and draft angles for mold removal all need to be considered when designing for dimensional accuracy. The complexity of the part geometry can also impact dimensional accuracy, with simpler shapes generally being easier to produce within tight tolerances. The choice of casting process plays a significant role in dimensional accuracy, with some processes like die casting offering better control over final dimensions compared to sand casting. Designers must work closely with foundry experts to understand the capabilities and limitations of different casting processes and materials in terms of achievable tolerances. Proper consideration of these factors during the design phase helps ensure that casting parts meet the required dimensional specifications, reducing the need for costly post-casting machining operations and improving overall part quality and performance.
What are the best practices for optimizing casting parts design for manufacturability?
Design for Ease of Mold Making
Optimizing the design of casting parts for ease of mold making is crucial for improving manufacturability and reducing production costs. When designing casting parts, it's important to consider how the mold will be created and how the part will be removed from the mold. Simple, straight-pull designs are generally easier and less expensive to produce than those requiring complex core assemblies or multi-part molds. Incorporating appropriate draft angles into the design facilitates easier part removal and reduces the risk of damage during the demolding process. Avoiding undercuts or creating them in a way that allows for simple core placement can significantly simplify mold design. Additionally, considering the parting line location early in the design process can help optimize the mold design and improve the overall quality of the casting parts. By focusing on designs that are easy to mold, manufacturers can reduce tooling costs, improve production efficiency, and ultimately produce higher quality casting parts.
Minimizing Post-Casting Operations
Reducing the need for extensive post-casting operations is a key consideration in optimizing the design of casting parts for manufacturability. Post-casting operations such as machining, grinding, and polishing can significantly increase production time and costs. By designing casting parts with near-net shape capabilities, manufacturers can minimize these secondary operations. This involves careful consideration of part geometry, tolerance requirements, and surface finish specifications during the design phase. Incorporating features such as machining allowances where necessary, while keeping them to a minimum, can help balance the need for post-casting operations with overall production efficiency. Additionally, designing casting parts with self-locating features or datum points can simplify subsequent machining operations when they are required. Consideration should also be given to the orientation of the part during casting to optimize surface finish and reduce the need for post-casting surface treatments. By minimizing post-casting operations through thoughtful design, manufacturers can reduce production costs and lead times for casting parts.
Material Flow and Solidification Analysis
Conducting thorough material flow and solidification analysis is essential for optimizing the design of casting parts and ensuring successful production. Advanced simulation software allows designers to model the casting process, predicting how the molten metal will flow through the mold and solidify. This analysis can reveal potential issues such as incomplete filling, porosity, or hot spots that could lead to defects in the casting parts. By identifying these problems early in the design phase, engineers can make necessary adjustments to part geometry, gating systems, or process parameters to improve castability. Solidification analysis is particularly important for identifying areas prone to shrinkage defects, allowing designers to optimize wall thicknesses and add feed paths where necessary. Additionally, this type of analysis can help in determining the optimal orientation of the part during casting to ensure even cooling and minimize internal stresses. By leveraging material flow and solidification analysis in the design process, manufacturers can significantly improve the quality and consistency of their casting parts while reducing development time and production costs.
Conclusion
In conclusion, successful metal casting design requires a comprehensive approach that considers multiple factors. From material selection and part geometry to the choice of casting process and design for manufacturability, each aspect plays a crucial role in producing high-quality casting parts. By carefully considering these elements and leveraging advanced tools like simulation software, designers and engineers can optimize their designs for both performance and production efficiency. As the field of metal casting continues to evolve with new technologies and materials, staying informed about best practices and innovative approaches will be key to creating successful casting designs that meet the demanding requirements of modern industries.
Shaanxi Welong Int'l Supply Chain Mgt Co.,Ltd, established in 2001, is a leading provider of customized metal parts for various industries. With certifications including ISO 9001:2015 and API-7-1, we specialize in forging, sand casting, investment casting, centrifugal casting, and machining. Our expertise covers a wide range of materials, including iron cast, steel, stainless steel, aluminum, copper, zinc, and various alloys. Our experienced team of engineers helps optimize production processes, control quality, and ensure timely delivery worldwide. With a track record of serving over 100 customers across Europe, North America, Asia, and Oceania, we strive to be a leader in the international supply chain, driving China's intelligent manufacturing to global prominence. For inquiries, please contact us at info@welongpost.com.
References
1. Campbell, J. (2015). Complete Casting Handbook: Metal Casting Processes, Metallurgy, Techniques and Design. Butterworth-Heinemann.
2. Beeley, P. (2001). Foundry Technology. Butterworth-Heinemann.
3. ASM International. (2008). ASM Handbook, Volume 15: Casting. ASM International.
4. Ravi, B. (2005). Metal Casting: Computer-Aided Design and Analysis. PHI Learning Pvt. Ltd.
5. Chastain, S. D. (2004). Metal Casting: A Sand Casting Manual for the Small Foundry. Stephen Chastain.
6. Brown, J. R. (1999). Foseco Ferrous Foundryman's Handbook. Butterworth-Heinemann.
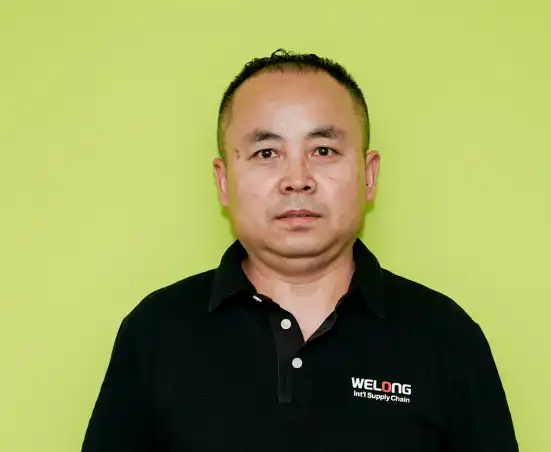
Share your inquiry, get the quotation accordingly!
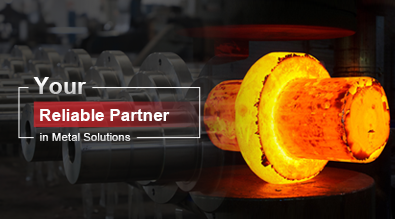
China WELONG- Your Reliable Partner in Metal Solutions