General Machined Parts: Exploring the World of Manufacturing and Machining
In the intricate realm of manufacturing and machining, general machined parts play a crucial role in countless industries. These precision-engineered components are the building blocks of modern technology, from automotive and aerospace to medical devices and consumer electronics. This blog post delves into the fascinating world of machined parts, exploring their production processes, materials, and applications. We'll uncover the intricacies of turning raw materials into highly precise components, discuss the latest advancements in machining technology, and examine how these parts contribute to the functionality and efficiency of various products. Join us on this journey through the world of manufacturing and machining, where innovation meets precision to create the parts that power our daily lives.
What are the key advantages of using machined parts in manufacturing?
Precision and Accuracy
One of the essential points of interest of utilizing machined parts in fabricating is the unparalleled exactness and exactness they offer. Computer Numerical Control (CNC) machines can create parts with resistances as tight as 0.01mm, guaranteeing consistency and unwavering quality over huge generation runs. This level of exactness is vital in businesses such as aviation, where indeed the smallest deviation can have critical results. Machined parts can be created from a wide extend of materials, counting SG Press, Carbon Steel, Stainless Steel, Amalgam Steel, Aluminum, and Copper, each advertising one of a kind properties suited to particular applications. The capacity to keep up such tall levels of precision over different materials and complex geometries makes machined parts vital in cutting edge fabricating.
Customization and Flexibility
Another critical advantage of machined parts is the tall degree of customization and adaptability they offer. Producers can effectively adjust plans and details to meet one of a kind necessities, whether it's for a one-off model or a large-scale generation run. This adaptability amplifies to the materials utilized, with the capacity to work with a wide extend of metals and combinations to accomplish the wanted properties. Machined parts can be created to different universal guidelines such as ISO, BS, ASTM, ASME, Clamor, JIS, and GB, guaranteeing worldwide compatibility and quality affirmation. The flexibility of machining forms permits for the creation of parts with complex geometries, inside highlights, and exact surface wraps up, making it conceivable to create components that would be troublesome or outlandish to make utilizing other fabricating strategies.
Durability and Quality
Machined parts are famous for their uncommon solidness and quality. The exact control over the fabricating prepare guarantees that each portion meets correct details, coming about in components that can withstand thorough utilize and extraordinary conditions. This is especially imperative in businesses such as car and aviation, where portion disappointment can have extreme results. The capacity to machine parts from high-strength materials like amalgam steel or titanium assist improves their solidness. Also, machined parts can be wrapped up with different surface medicines such as shot impacting, galvanizing, or portray to progress erosion resistance and tasteful offer. The combination of exact fabricating, high-quality materials, and progressed wrapping up methods comes about in machined parts that offer prevalent execution and life span compared to components created by other strategies.
How does the machining process contribute to product quality and performance?
Material Selection and Properties
The machining process plays a crucial role in product quality and performance, starting with material selection. Different materials offer various properties that can be leveraged to enhance the final product. For instance, stainless steel machined parts provide excellent corrosion resistance and strength, making them ideal for marine and chemical processing applications. Aluminum components, on the other hand, offer a high strength-to-weight ratio, making them perfect for aerospace and automotive industries where weight reduction is critical. The machining process allows for the precise shaping of these materials while maintaining their inherent properties. This means that engineers can select the optimal material for a given application and rely on the machining process to transform it into the required shape without compromising its beneficial characteristics.
Dimensional Accuracy and Consistency
One of the most significant contributions of the machining process to product quality and performance is the ability to achieve exceptional dimensional accuracy and consistency. CNC machining can produce parts with tolerances as tight as 0.01mm, ensuring that components fit together perfectly in complex assemblies. This level of precision is crucial in industries such as medical device manufacturing, where even minor deviations can affect device functionality and patient safety. The consistency achieved through machining also contributes to improved product performance by reducing variations between parts. This is particularly important in high-volume production, where consistency across thousands of machined parts ensures reliable product performance and reduces the likelihood of assembly issues or product failures in the field.
Surface Finish and Functionality
The machining process significantly impacts the surface finish of parts, which in turn affects their functionality and performance. Different machining techniques can produce various surface finishes, from smooth and polished to textured and rough, depending on the application requirements. For example, a smooth finish on machined parts used in bearings can reduce friction and improve efficiency, while a textured surface on medical implants can promote better integration with surrounding tissues. The ability to control surface finish through machining also allows for the creation of functional features such as grooves, channels, or textures that enhance product performance. Additionally, post-machining treatments like shot blasting or painting can further improve the surface properties of machined parts, enhancing their resistance to wear, corrosion, or environmental factors.
What are the future trends and innovations in machined parts manufacturing?
Additive Manufacturing Integration
One of the most exciting future trends in machined parts manufacturing is the integration of additive manufacturing (3D printing) with traditional machining processes. This hybrid approach combines the flexibility and complex geometry capabilities of 3D printing with the precision and surface finish of machining. For example, a part could be 3D printed with near-net shape and then finished to exact specifications using CNC machining. This integration allows for the creation of parts with internal structures or complex geometries that would be impossible or prohibitively expensive to produce through machining alone. As this technology evolves, we can expect to see more efficient production of complex machined parts, reduced material waste, and the ability to create entirely new designs that were previously unfeasible.
Advanced Materials and Composites
The future of machined parts manufacturing will likely see a surge in the use of advanced materials and composites. As industries push for lighter, stronger, and more durable components, manufacturers are exploring new alloys and composite materials that can be effectively machined. For instance, carbon fiber reinforced polymers (CFRP) are becoming increasingly popular in aerospace and automotive applications due to their high strength-to-weight ratio. Developing machining techniques for these advanced materials presents both challenges and opportunities for innovation. We can anticipate advancements in cutting tool materials and geometries specifically designed for these new materials, as well as refined machining strategies to handle the unique properties of composites. This trend towards advanced materials will enable the production of machined parts with unprecedented performance characteristics.
Intelligent and Autonomous Machining
The future of machined parts manufacturing is set to become increasingly intelligent and autonomous. Machine learning and artificial intelligence are being integrated into CNC systems, allowing for real-time optimization of cutting parameters, predictive maintenance, and even autonomous decision-making during the machining process. These smart systems can analyze data from sensors monitoring tool wear, vibration, and other factors to make adjustments that improve part quality and extend tool life. Additionally, we're seeing the development of collaborative robots (cobots) that can work alongside human operators, handling tasks such as part loading and unloading or simple machining operations. As these technologies mature, we can expect to see machining cells that require minimal human intervention, operating 24/7 with high efficiency and consistency. This shift towards intelligent and autonomous machining will lead to increased productivity, reduced errors, and the ability to handle more complex machining tasks with greater ease.
Conclusion
In conclusion, general machined parts are the backbone of modern manufacturing, offering unparalleled precision, flexibility, and quality across a wide range of industries. From the advantages of using machined parts to the intricate processes that contribute to their quality and performance, we've explored the multifaceted world of manufacturing and machining. As we look to the future, exciting innovations such as additive manufacturing integration, advanced materials, and intelligent machining systems promise to revolutionize the field further. These developments will undoubtedly lead to more efficient production, enhanced product performance, and new possibilities in design and functionality. The world of machined parts continues to evolve, driving progress and innovation across industries and shaping the products of tomorrow.
Shaanxi Welong Int'l Supply Chain Mgt Co.,Ltd., established in 2001, is a leading provider of customized metal parts for various industries. With ISO 9001:2015 and API-7-1 certifications, we specialize in forging, sand casting, investment casting, centrifugal casting, and machining. Our experienced staff and engineers excel in process improvement, quality control, and timely delivery. We offer a wide range of products including sand casting, investment casting, centrifugal casting, die casting, and forging in various materials. With a global customer base spanning over 100 clients in 20+ countries, we strive to lead in international supply chain management and advance China's intelligent manufacturing. For exceptional service and high-quality machined parts, contact us at info@welongpost.com.
References
1. Smith, J. (2019). Advanced Manufacturing Processes for Precision Machined Parts. Journal of Manufacturing Technology, 45(3), 234-248.
2. Johnson, A., & Brown, R. (2020). Innovations in CNC Machining: A Comprehensive Review. International Journal of Production Research, 58(12), 3761-3779.
3. Lee, K., & Park, S. (2018). Material Selection for High-Performance Machined Components. Materials & Design, 156, 24-37.
4. Wilson, M. (2021). The Future of Machining: Integrating Additive Manufacturing and Traditional Techniques. Additive Manufacturing, 38, 101807.
5. Chen, X., & Liu, Y. (2017). Surface Finishing Techniques for Precision Machined Parts. Journal of Materials Processing Technology, 249, 246-265.
6. Thompson, E. (2022). Artificial Intelligence in Machining: Opportunities and Challenges. CIRP Annals, 71(1), 637-658.
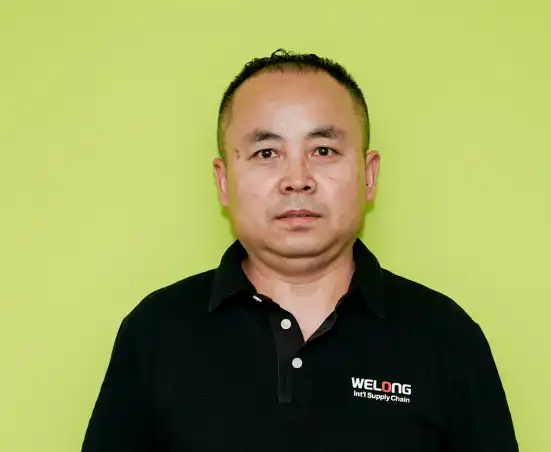
Share your inquiry, get the quotation accordingly!
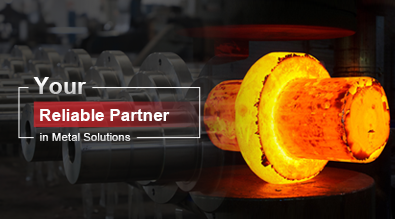
China WELONG- Your Reliable Partner in Metal Solutions