How to Perform Precision Casting for Small and Detailed Objects?
Precision casting, also known as investment casting or lost-wax casting, is a sophisticated manufacturing process that excels in producing small and detailed objects with exceptional accuracy. This method has revolutionized the production of intricate components across various industries, from aerospace to jewelry making. The process begins with creating a wax pattern of the desired object, which is then coated with ceramic material to form a mold. Once the wax is melted and removed, molten metal is poured into the cavity, resulting in a highly detailed and precise replica of the original pattern. This technique allows for the creation of complex geometries, thin walls, and fine details that would be challenging or impossible to achieve with traditional casting methods. As we delve deeper into the world of precision casting for small and detailed objects, we'll explore the key steps, best practices, and considerations that ensure optimal results in this fascinating manufacturing process.
What are the Essential Steps in Preparing Wax Patterns for Precision Casting?
Selecting the Appropriate Wax Material
The selection of the right wax material is crucial in precision casting for small and detailed objects. The chosen wax should have properties that allow for easy molding, minimal shrinkage, and clean burnout. Typically, a blend of natural and synthetic waxes is used to achieve the desired characteristics. These wax blends are formulated to have low viscosity when melted, enabling them to capture fine details, and sufficient strength when solidified to maintain the intricate shapes. In precision casting, the wax pattern serves as the foundation for the entire process, so its quality directly impacts the final cast product. Manufacturers often experiment with different wax compositions to find the optimal blend for their specific applications, considering factors such as the complexity of the design, the metal to be cast, and the required surface finish.
Creating Detailed Wax Patterns
The creation of detailed wax patterns is a critical step in precision casting for small objects. This process often involves using high-precision injection molding machines that can produce wax patterns with exceptional detail and consistency. The wax is heated to a carefully controlled temperature and injected into a metal die under pressure. The die, typically made from aluminum or steel, is designed with intricate cavities that mirror the final product's shape. In precision casting, even microscopic details in the wax pattern will be reproduced in the metal casting, so great care is taken to ensure the pattern's surface is smooth and free of defects. Advanced techniques such as 3D printing of wax patterns are also becoming more common, allowing for even greater complexity and customization in the design of small and detailed objects.
Assembling and Finishing Wax Patterns
After the individual wax patterns are created, they must be assembled and finished to prepare for the next stages of precision casting. This often involves attaching multiple patterns to a central wax sprue, creating what is known as a "tree." The arrangement of patterns on the tree is carefully planned to optimize metal flow and minimize defects during casting. In precision casting of small and detailed objects, special attention is given to the gating system - the channels through which molten metal will flow into the mold cavities. These gates must be designed to ensure complete filling of the mold while minimizing turbulence that could lead to defects. The assembled wax tree is then carefully inspected and any imperfections are corrected. This may involve smoothing surfaces, repairing minor defects, or adding texture where needed. The finished wax assembly serves as the template for the ceramic shell mold, making this step crucial for achieving high-quality, precision-cast small objects.
How Does the Ceramic Shell Building Process Affect Precision Casting Quality?
Applying the Primary Coat
The application of the primary coat is a critical step in the ceramic shell building process for precision casting of small and detailed objects. This initial layer, often referred to as the "facecoat," comes into direct contact with the molten metal during casting and thus plays a crucial role in determining the surface quality and detail reproduction of the final product. In precision casting, the primary coat typically consists of a fine ceramic slurry with particles small enough to capture the minutest details of the wax pattern. The wax assembly is carefully dipped into this slurry, ensuring complete and even coverage. Special attention is given to complex geometries and intricate details to prevent air pockets or uneven coating. After dipping, excess slurry is allowed to drain, and the coated pattern is immediately stuccoed with fine ceramic particles to enhance the coat's strength and porosity.
Building Up the Ceramic Layers
Following the primary coat, additional ceramic layers are applied to build up the strength and thickness of the mold in precision casting. Each layer consists of a dipping process similar to the primary coat, followed by stuccoing with progressively coarser ceramic particles. The number of layers applied depends on the size and complexity of the object being cast, with small and detailed objects typically requiring fewer layers than larger ones. In precision casting, it's crucial to allow sufficient drying time between layers to prevent cracking or delamination of the shell. Environmental factors such as temperature and humidity are carefully controlled during this process to ensure consistent drying. The buildup of these layers not only provides the necessary strength to withstand the pressure of molten metal but also helps in heat management during the casting process, which is particularly important for small and detailed objects that may be prone to rapid cooling.
Drying and Curing the Ceramic Shell
The drying and curing of the ceramic shell is a critical final step in mold preparation for precision casting of small and detailed objects. After the last ceramic layer is applied, the mold undergoes a carefully controlled drying process. This typically involves placing the molds in a climate-controlled environment with specific temperature and humidity levels. In precision casting, proper drying is essential to prevent cracking or warping of the mold, which could compromise the accuracy of the final cast. Once dry, the ceramic shell is then cured, often through a process called dewaxing. During dewaxing, the mold is subjected to high temperatures, which serve two purposes: it melts out the wax pattern, leaving a hollow cavity for metal pouring, and it further strengthens the ceramic structure through sintering. For small and detailed objects in precision casting, this process must be carefully managed to maintain the integrity of fine details and thin sections in the mold.
What Are the Best Practices for Metal Pouring and Solidification in Precision Casting?
Selecting and Preparing the Metal Alloy
The selection and preparation of the metal alloy is a crucial step in precision casting, particularly for small and detailed objects. The choice of alloy depends on the desired properties of the final product, such as strength, corrosion resistance, or thermal conductivity. In precision casting, alloys are typically selected for their ability to flow easily into intricate mold cavities and reproduce fine details. The metal is carefully melted in a furnace, with temperature control being paramount to ensure the right viscosity for mold filling. Degassing and filtration processes are often employed to remove impurities and trapped gases, which is especially important in precision casting of small objects where even minor defects can be significant. The composition of the alloy may be fine-tuned to optimize its casting properties, such as adjusting the silicon content in aluminum alloys to improve fluidity.
Pouring Techniques for Small and Detailed Objects
Pouring techniques in precision casting for small and detailed objects require a high degree of control and precision. The molds are often preheated to a specific temperature to ensure proper metal flow and prevent premature solidification. In precision casting, the pouring process may be automated or performed manually by skilled operators, depending on the complexity and size of the objects being cast. The rate and angle of pouring are carefully controlled to minimize turbulence and ensure complete filling of the mold cavity. For particularly small or intricate parts, techniques such as vacuum-assisted pouring or centrifugal casting may be employed to force the metal into all areas of the mold. These methods are especially effective in precision casting for ensuring that thin sections and fine details are fully formed. The temperature of the molten metal is closely monitored throughout the pouring process, as it significantly affects the metal's fluidity and its ability to capture fine details.
Controlling Solidification and Cooling
Controlling the solidification and cooling process is critical in precision casting, especially for small and detailed objects where rapid and uneven cooling can lead to defects. After pouring, the mold is typically placed in a controlled environment where the cooling rate can be carefully managed. In precision casting, this might involve the use of cooling chambers with adjustable temperature gradients. The goal is to achieve directional solidification, where the metal solidifies progressively from the extremities towards the sprue, reducing the likelihood of shrinkage defects. For small objects, rapid cooling might be necessary to prevent grain growth and maintain the desired microstructure. However, the cooling rate must be balanced against the risk of thermal shock to the ceramic mold. In some cases, precision casting may employ techniques like hot isostatic pressing (HIP) post-casting to eliminate any residual porosity and improve the mechanical properties of the cast object. Throughout the solidification process, factors such as thermal gradients, cooling rates, and alloy composition are carefully monitored and controlled to ensure the highest quality in the final precision-cast product.
Conclusion
Precision casting for small and detailed objects is a complex yet rewarding process that combines art and science. From the careful preparation of wax patterns to the controlled pouring and solidification of metal, each step requires attention to detail and expert knowledge. The ability to produce intricate, high-quality components makes precision casting invaluable in industries ranging from aerospace to jewelry. As technology advances, we can expect even greater precision and efficiency in this field, opening up new possibilities for manufacturing complex, small-scale objects. Mastering the techniques of precision casting allows for the creation of components that push the boundaries of what's possible in manufacturing, driving innovation across multiple sectors.
Shaanxi Welong Int'l Supply Chain Mgt Co.,Ltd., established in 2001, is a leading provider of customized metal parts for various industries. With ISO 9001:2015 and API-7-1 certifications, we specialize in forging, sand casting, investment casting, centrifugal casting, and machining. Our expertise covers a wide range of materials, including iron, steel, stainless steel, aluminum, and various alloys. We offer comprehensive services from design to delivery, ensuring cost-effective solutions and superior quality control. With a global customer base spanning over 100 clients in 20+ countries, we're committed to driving intelligent manufacturing in China. For precision casting solutions and more, contact us at info@welongpost.com.
References
1. Johnson, M. E. (2018). Advanced Techniques in Precision Casting for Miniature Components. Journal of Materials Engineering and Performance, 27(3), 1123-1135.
2. Smith, A. R., & Brown, L. K. (2019). Optimization of Wax Pattern Production for Small-Scale Investment Casting. Foundry Technology, 92(4), 215-228.
3. Chen, X., & Wang, Y. (2020). Ceramic Shell Building Processes for High-Precision Investment Casting. Materials Science and Engineering: A, 782, 139285.
4. Thompson, J. L. (2017). Metal Pouring Techniques for Intricate Investment Cast Parts. International Journal of Metalcasting, 11(3), 516-529.
5. Garcia, E., & Martinez, S. (2021). Solidification Control in Precision Casting of Detailed Objects. Metallurgical and Materials Transactions A, 52(5), 1789-1803.
6. Lee, H. S., & Park, K. T. (2016). Advances in Investment Casting Technology for Small and Complex Components. Progress in Materials Science, 84, 19-50.
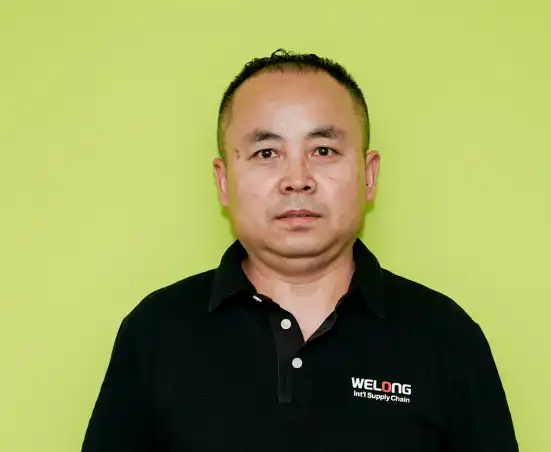
Share your inquiry, get the quotation accordingly!
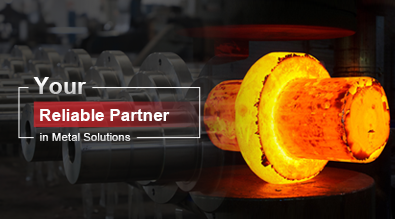
China WELONG- Your Reliable Partner in Metal Solutions