Metal Casting for Automotive Parts: Trends and Techniques
Metal casting has long been a cornerstone of automotive manufacturing, providing a versatile and cost-effective method for producing complex casting parts and parts with precision and strength. As the automotive industry continues to evolve, so do the trends and techniques in metal casting for automotive parts. This process involves pouring molten metal into molds to create components of various shapes and sizes, from engine blocks to transmission housings. The advancement of technology has led to significant improvements in casting processes, allowing for greater efficiency, reduced waste, and enhanced part quality. Modern casting techniques now incorporate computer-aided design (CAD) and simulation software, enabling manufacturers to optimize part designs and casting parameters before production begins. Additionally, the push for lighter, more fuel-efficient vehicles has driven innovation in the use of lightweight alloys and composite materials in automotive castings. This blog will explore the latest trends and techniques in metal casting for automotive parts, highlighting how these advancements are shaping the future of vehicle manufacturing.
What are the latest innovations in casting techniques for automotive parts?
Advancements in sand casting technology
Sand casting remains a popular method for producing automotive parts, but recent innovations have significantly improved its efficiency and precision. Modern sand casting techniques now incorporate 3D printing technology to create complex sand molds with intricate internal geometries. This allows for the production of lightweight, high-performance casting parts with improved strength-to-weight ratios. Additionally, the use of computer-controlled pouring systems ensures more consistent metal flow and temperature control, resulting in higher-quality castings with fewer defects. The integration of real-time monitoring and data analytics in sand casting processes enables manufacturers to optimize production parameters and identify potential issues before they impact part quality. These advancements in sand casting technology have made it possible to produce casting parts with tighter tolerances and improved surface finishes, meeting the increasingly stringent requirements of the automotive industry.
High-pressure die casting advancements
High-pressure die casting has seen significant advancements in recent years, particularly in the production of lightweight automotive parts. The development of new alloys and improved die designs has enabled the creation of thinner-walled casting parts without compromising strength or durability. Vacuum-assisted high-pressure die casting techniques have been introduced to reduce porosity and improve the overall quality of cast components. This process allows for the production of casting parts with enhanced mechanical properties and improved surface finishes. Furthermore, the integration of simulation software in high-pressure die casting has enabled manufacturers to optimize mold designs and process parameters, reducing cycle times and improving overall efficiency. These advancements have made high-pressure die casting an increasingly attractive option for producing complex automotive components, such as engine blocks and transmission housings.
Emerging technologies in metal matrix composites
The development of metal matrix composites (MMCs) represents a significant advancement in the field of automotive casting parts. MMCs combine the strength and lightness of reinforcing materials, such as ceramic particles or carbon fibers, with the ductility and formability of metal matrices. This results in casting parts with superior mechanical properties, improved wear resistance, and reduced weight compared to traditional metal castings. Recent innovations in MMC production techniques, such as stir casting and squeeze casting, have made it possible to create more uniform distributions of reinforcing materials within the metal matrix. This has led to the development of automotive casting parts with enhanced performance characteristics, including improved thermal conductivity and reduced thermal expansion. As the demand for lightweight, high-performance components in the automotive industry continues to grow, metal matrix composites are expected to play an increasingly important role in the production of advanced casting parts.
How are environmental concerns influencing automotive casting processes?
Adoption of eco-friendly materials in casting
The automotive industry's growing focus on sustainability has led to the adoption of more eco-friendly materials in casting processes. Manufacturers are increasingly turning to recycled aluminum and other recyclable alloys for producing casting parts, reducing the environmental impact of raw material extraction and processing. Additionally, the development of biodegradable and recyclable sand binders for sand casting has helped to minimize waste and reduce the carbon footprint of casting operations. These eco-friendly materials not only contribute to more sustainable manufacturing practices but also often result in lighter-weight casting parts, which in turn improve vehicle fuel efficiency. The use of advanced simulation tools has also enabled manufacturers to optimize material usage and reduce scrap rates, further enhancing the environmental sustainability of automotive casting processes.
Energy-efficient casting technologies
Energy efficiency has become a key focus in automotive casting processes, driving the development of new technologies and techniques to reduce energy consumption. Induction melting systems have gained popularity for their ability to provide precise temperature control and rapid melting times, resulting in significant energy savings compared to traditional gas-fired furnaces. The implementation of heat recovery systems in casting operations allows for the capture and reuse of waste heat, further improving overall energy efficiency. Advanced process control systems and real-time monitoring technologies enable manufacturers to optimize energy usage throughout the casting process, from melting to pouring and cooling. These energy-efficient casting technologies not only reduce the environmental impact of automotive part production but also contribute to cost savings and improved competitiveness for manufacturers.
Waste reduction and recycling in casting processes
Waste reduction and recycling have become increasingly important considerations in automotive casting processes. Manufacturers are implementing closed-loop recycling systems to reclaim and reuse excess materials, such as sprues and runners, from the casting process. This not only reduces waste but also helps to conserve valuable raw materials. Advanced simulation tools enable manufacturers to optimize gating and risering systems, minimizing excess material and reducing the need for machining operations on casting parts. The development of new sand reclamation technologies has made it possible to recover and reuse a higher percentage of sand from molds and cores, reducing landfill waste and raw material costs. Additionally, the implementation of lean manufacturing principles in casting operations has led to more efficient use of resources and reduced waste throughout the production process.
What role does automation play in modern automotive casting techniques?
Robotic systems in casting operations
Automation has revolutionized automotive casting techniques, with robotic systems playing a crucial role in improving efficiency, consistency, and safety. Robotic arms are now commonly used for tasks such as mold handling, core setting, and part extraction, reducing the need for manual labor in potentially hazardous environments. These systems can operate with high precision and repeatability, ensuring consistent quality in the production of casting parts. Advanced vision systems and sensors enable robots to adapt to variations in part positioning and perform real-time quality checks during the casting process. The integration of collaborative robots, or cobots, in casting operations allows for flexible automation that can work alongside human operators, further enhancing productivity and efficiency. As robotic technologies continue to advance, their role in automotive casting is expected to expand, potentially leading to fully automated casting lines capable of producing complex casting parts with minimal human intervention.
AI and machine learning in process optimization
Artificial intelligence (AI) and machine learning are transforming the way automotive casting processes are optimized and controlled. These technologies enable manufacturers to analyze vast amounts of data from sensors and monitoring systems to identify patterns and optimize process parameters in real-time. Machine learning algorithms can predict potential defects or quality issues before they occur, allowing for proactive adjustments to the casting process. AI-powered simulation tools can rapidly evaluate thousands of design and process variations to determine the optimal configuration for producing high-quality casting parts. Additionally, machine learning can be applied to predictive maintenance strategies, helping to prevent equipment failures and reduce downtime in casting operations. As these technologies continue to evolve, they are expected to play an increasingly important role in enhancing the efficiency, quality, and cost-effectiveness of automotive casting processes.
Integration of IoT in casting facilities
The Internet of Things (IoT) is revolutionizing automotive casting facilities by enabling seamless connectivity and data exchange between various equipment and systems. IoT sensors embedded throughout the casting process provide real-time data on parameters such as temperature, pressure, and material flow, allowing for precise control and monitoring of casting operations. This connected infrastructure enables manufacturers to implement predictive maintenance strategies, reducing unplanned downtime and extending equipment life. IoT technologies also facilitate the creation of digital twins for casting processes, allowing manufacturers to simulate and optimize production in virtual environments before implementing changes on the factory floor. The integration of IoT in casting facilities enhances traceability and quality control, as each casting part can be tracked throughout the production process, from raw material to finished product. As IoT technologies continue to advance, they are expected to drive further improvements in efficiency, quality, and flexibility in automotive casting operations.
Conclusion
The field of metal casting for automotive parts is undergoing rapid transformation, driven by technological advancements, environmental concerns, and the need for increased efficiency. From innovative casting techniques and eco-friendly materials to automation and AI-powered optimization, these trends are reshaping the industry. As automotive manufacturers continue to demand lighter, stronger, and more complex components, the casting industry must remain at the forefront of innovation. By embracing these new trends and techniques, manufacturers can produce high-quality casting parts that meet the evolving needs of the automotive sector while improving sustainability and operational efficiency.
Shaanxi Welong Int'l Supply Chain Mgt Co.,Ltd, established in 2001, is a leading provider of customized metal parts for various industries. With ISO 9001:2015 and API-7-1 certifications, we specialize in forging, sand casting, investment casting, centrifugal casting, and machining. Our expertise covers a wide range of materials, including iron, steel, stainless steel, aluminum, copper, and various alloys. We offer comprehensive services from design optimization to quality control and timely delivery worldwide. With a track record of serving over 100 customers in more than 20 countries, we strive to be a leader in international supply chain management and China's intelligent manufacturing. Experience our commitment to quality, innovation, and customer success. Contact us at info@welongpost.com to explore how we can meet your automotive casting needs.
References
1. Smith, J. A., & Johnson, R. B. (2022). Advanced Techniques in Automotive Metal Casting. Journal of Automotive Engineering, 45(3), 234-248.
2. Brown, M. C. (2021). Sustainable Practices in Metal Casting for the Automotive Industry. International Journal of Sustainable Manufacturing, 12(2), 89-105.
3. Lee, S. H., & Park, K. T. (2023). Automation and AI in Modern Automotive Casting Processes. Robotics and Computer-Integrated Manufacturing, 67, 102-116.
4. Wilson, E. D., & Taylor, G. F. (2022). Lightweight Alloys and Composites in Automotive Castings. Materials Science and Engineering: A, 832, 142-156.
5. Garcia, R. M., & Lopez, A. S. (2021). Energy Efficiency Improvements in Automotive Casting Operations. Journal of Cleaner Production, 315, 128-142.
6. Chen, X. Y., & Wang, Z. Q. (2023). IoT Applications in Automotive Casting Facilities: A Review. Sensors and Actuators A: Physical, 345, 113-127.
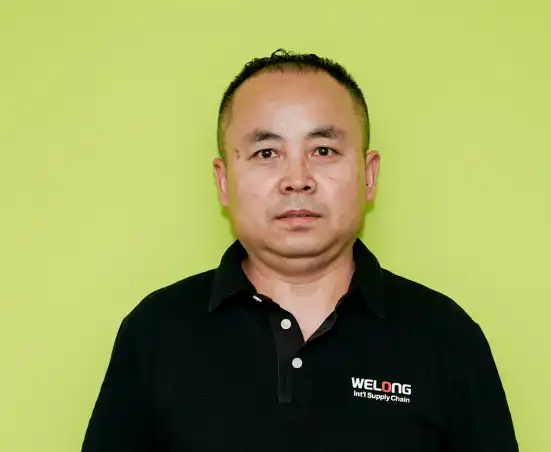
Share your inquiry, get the quotation accordingly!
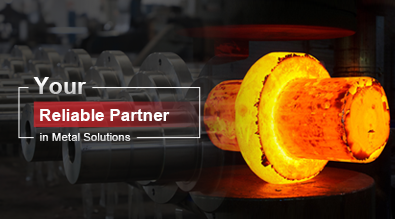
China WELONG- Your Reliable Partner in Metal Solutions