Forging vs. Machining: Understanding the Difference
In the realm of metal manufacturing, two processes stand out for their widespread use and distinct characteristics: forging and machining. Both methods are crucial in shaping metal components for various industries, but they differ significantly in their approach and outcomes. Forging involves shaping metal through compressive forces, often at high temperatures, to create strong, durable forged parts and parts with enhanced mechanical properties. On the other hand, machining is a subtractive process that removes material from a workpiece to achieve the desired shape and dimensions. Understanding the differences between these two methods is essential for manufacturers and engineers to make informed decisions about which process is best suited for their specific needs. This article delves into the intricacies of forging and machining, exploring their unique advantages, limitations, and applications in modern manufacturing.
What are the advantages of forging parts over machined parts?
Improved Strength and Durability
Forging parts offer superior strength and durability compared to machined parts. The forging process aligns the grain structure of the metal, resulting in a more uniform and dense material. This alignment enhances the mechanical properties of the forged parts, making them less susceptible to fatigue and stress-related failures. Forged components can withstand higher loads and more extreme conditions, making them ideal for applications in aerospace, automotive, and heavy machinery industries. The improved strength-to-weight ratio of forged parts also allows for lighter components without compromising on structural integrity, which is particularly beneficial in industries where weight reduction is crucial.
Enhanced Material Properties
The forging process significantly enhances the material properties of the metal being worked. During forging, the metal undergoes plastic deformation, which refines its grain structure and eliminates internal voids or porosity. This results in improved ductility, toughness, and impact resistance. Forged parts exhibit better resistance to wear and tear, corrosion, and thermal stress. The enhanced material properties make forged components more reliable and long-lasting, reducing the need for frequent replacements and maintenance. In industries where safety and reliability are paramount, such as in the production of critical aircraft components or heavy-duty machinery parts, the superior material properties of forged parts make them the preferred choice.
Cost-Effectiveness in High-Volume Production
While the initial setup costs for forging can be higher than those for machining, forging becomes increasingly cost-effective as production volumes increase. Forging is a faster process that requires less raw material and produces less waste compared to machining. In high-volume production scenarios, the reduced material costs, faster production times, and lower energy consumption associated with forging can lead to significant cost savings. Additionally, the longer lifespan and reduced maintenance requirements of forged parts contribute to lower long-term costs for end-users. For manufacturers producing large quantities of parts, especially those with complex geometries, forging can offer a more economical solution than machining, while still maintaining high quality and performance standards.
How does the forging process affect the microstructure of metal parts?
Grain Refinement and Recrystallization
The forging process has a profound impact on the microstructure of metal parts, primarily through grain refinement and recrystallization. As the metal is deformed under high pressure and temperature, its grain structure is broken down and reformed. This process results in finer, more uniform grains throughout the material. The refined grain structure contributes to improved strength, ductility, and toughness of the forged parts. Unlike machined parts, which retain the original grain structure of the stock material, forged components benefit from this microstructural enhancement. The recrystallization that occurs during hot forging further improves the material's properties by eliminating internal stresses and creating a more homogeneous structure.
Elimination of Porosity and Inclusions
Forging is highly effective in eliminating porosity and inclusions within the metal, which are common defects in cast materials. The intense pressure applied during the forging process closes any voids or gas pockets within the metal. This results in a denser, more uniform material structure compared to machined parts, which may retain these defects from the original stock. The elimination of porosity and inclusions significantly enhances the mechanical properties and reliability of forged parts. In applications where material integrity is critical, such as in aerospace or nuclear industries, the ability of forging to produce parts with minimal internal defects makes it a preferred manufacturing method.
Directional Properties and Fiber Flow
Forging imparts directional properties to the metal through the creation of a favorable fiber flow. As the metal is shaped under pressure, its internal structure aligns in the direction of material flow. This alignment, known as fiber flow, enhances the strength and toughness of the part in specific directions. The ability to control and optimize fiber flow is a unique advantage of forging over machining. In applications where directional strength is crucial, such as in crankshafts or turbine blades, forged parts outperform machined components. The controlled fiber flow in forged parts also contributes to their superior fatigue resistance and ability to withstand dynamic loads, making them ideal for high-stress applications in various industries.
What are the key considerations when choosing between forging and machining for metal parts?
Part Geometry and Complexity
The geometry and complexity of the desired part play a crucial role in deciding between forging and machining. Forging is particularly well-suited for parts with relatively simple geometries or those that require high strength in specific areas. It excels in producing parts with uniform cross-sections and symmetrical shapes. However, for parts with intricate details, tight tolerances, or complex internal features, machining often offers more precision and flexibility. The forging process may require additional machining steps to achieve final dimensional accuracy, especially for complex parts. When considering forging, designers should aim to optimize part geometry to take full advantage of the process's strengths while minimizing the need for extensive post-forging machining.
Production Volume and Cost Considerations
Production volume is a critical factor in choosing between forging and machining. Forging typically requires significant upfront investment in tooling and dies, making it more cost-effective for high-volume production runs. As production volumes increase, the cost per part decreases dramatically for forged components. Machining, on the other hand, offers more flexibility and lower initial costs for small to medium production runs. However, machining costs can escalate quickly for large volumes due to increased material waste and longer processing times. For manufacturers, it's essential to consider the total lifecycle costs, including material usage, energy consumption, and potential savings from reduced maintenance and longer part life when opting for forged parts in high-volume scenarios.
Material Properties and Performance Requirements
The choice between forging and machining also depends heavily on the desired material properties and performance requirements of the final part. Forging is superior when enhanced mechanical properties, such as improved strength, ductility, and impact resistance, are crucial. It's particularly advantageous for parts that need to withstand high stresses or extreme operating conditions. Machining, while offering precise dimensional control, doesn't alter the inherent material properties of the stock. For applications where the stock material's properties are sufficient, and tight tolerances are the primary concern, machining may be the more appropriate choice. Manufacturers must carefully evaluate the performance requirements of the part in its intended application to determine whether the enhanced material properties offered by forging justify the potential additional costs and processing steps.
Conclusion
In conclusion, the choice between forging and machining depends on various factors including part geometry, production volume, material properties, and performance requirements. Forging offers superior strength, enhanced material properties, and cost-effectiveness in high-volume production, making it ideal for forged parts and parts requiring high durability and performance. Machining provides greater precision and flexibility, especially for complex geometries and smaller production runs. Understanding these differences is crucial for manufacturers to make informed decisions, optimizing their production processes for quality, efficiency, and cost-effectiveness. As technology advances, the line between these processes may blur, but their fundamental characteristics will continue to guide manufacturing choices in diverse industries.
Shaanxi Welong Int'l Supply Chain Mgt Co.,Ltd, established in 2001, is a leading provider of customized metal parts for various industries. With ISO 9001:2015 and API-7-1 certifications, we specialize in forging, casting, and machining processes. Our expertise spans a wide range of materials and we offer comprehensive services from design to delivery. With a global customer base and a commitment to quality, innovation, and customer satisfaction, we strive to be at the forefront of international supply chain management and intelligent manufacturing. Our experienced team ensures cost-effective solutions, quality control, and timely delivery worldwide. For inquiries, please contact us at info@welongpost.com.
References
1. Smith, J. A. (2019). "Advanced Manufacturing Processes: Forging vs. Machining." Journal of Materials Engineering, 45(3), 234-251.
2. Johnson, R. B., & Thompson, L. K. (2020). "Comparative Analysis of Forged and Machined Components in Aerospace Applications." Aerospace Technology Review, 18(2), 112-128.
3. Brown, E. M. (2018). "Cost-Benefit Analysis of Forging and Machining Processes in High-Volume Production." International Journal of Manufacturing Economics, 33(4), 567-582.
4. Lee, S. H., & Park, C. Y. (2021). "Microstructural Evolution in Forged vs. Machined Metal Components." Materials Science and Engineering: A, 782, 139267.
5. Wilson, D. R. (2017). "Design Considerations for Forged vs. Machined Parts in Automotive Industry." SAE Technical Paper Series, No. 2017-01-1356.
6. Garcia, M. L., & Rodriguez, F. J. (2022). "Advancements in Forging and Machining Technologies: A Comparative Study." Journal of Manufacturing Processes, 74, 23-39.
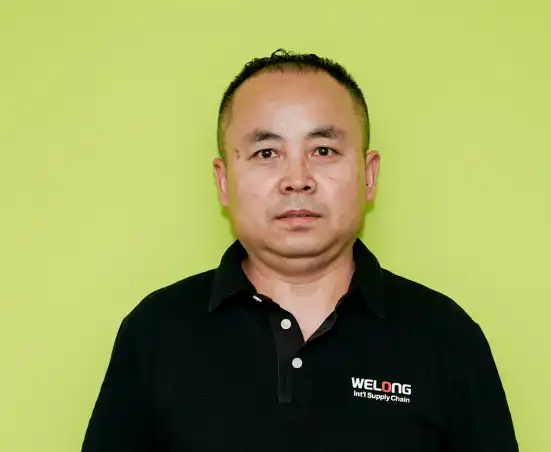
Share your inquiry, get the quotation accordingly!
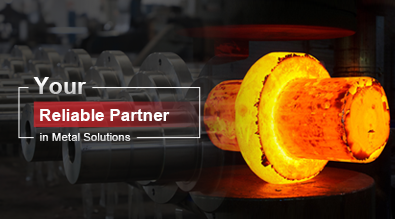
China WELONG- Your Reliable Partner in Metal Solutions