Everything You Need to Know About Machined Parts and Components
Machined parts and components form the backbone of countless industries, from aerospace to automotive, medical devices to consumer electronics. These precision-engineered elements are the unsung heroes of modern manufacturing, enabling the creation of complex machinery and intricate devices that power our world. In this comprehensive guide, we'll delve into the fascinating realm of machined parts, exploring their production processes, materials, applications, and the cutting-edge technologies that shape their creation. Whether you're an industry professional seeking to expand your knowledge or a curious enthusiast eager to understand the inner workings of the products around you, this article will provide valuable insights into the world of machined parts and components. From the basics of CNC machining to the latest advancements in materials science, we'll cover everything you need to know to appreciate the incredible precision and engineering prowess behind these essential building blocks of modern industry.
What are the Key Advantages of Using Machined Parts in Manufacturing?
Precision and Accuracy
Machined parts offer unparalleled precision and accuracy in manufacturing processes. With advanced CNC (Computer Numerical Control) technology, manufacturers can produce components with tolerances as tight as 0.01mm. This level of precision is crucial in industries such as aerospace, where even the slightest deviation can have significant consequences. Machined parts ensure consistency across production runs, minimizing variations that could affect product performance. The ability to replicate complex geometries with high accuracy also allows for the creation of intricate components that would be impossible to produce using traditional manufacturing methods. Moreover, the precision of machined parts contributes to improved product quality, reduced waste, and enhanced efficiency in assembly processes.
Material Versatility
One of the most significant advantages of machined parts is the wide range of materials that can be used in their production. From metals like SG Iron, Carbon Steel, Stainless Steel, and Alloy Steel to non-ferrous materials such as Aluminum and Copper, machining processes can accommodate diverse material requirements. This versatility allows manufacturers to select the optimal material for each specific application, considering factors such as strength, weight, corrosion resistance, and thermal properties. The ability to work with various materials also enables the production of components that meet stringent industry standards, including ISO, BS, ASTM, ASME, DIN, JIS, and GB. Furthermore, machining processes can handle materials with different hardness levels, from soft plastics to hard alloys, expanding the possibilities for product design and functionality.
Customization and Scalability
Machined parts offer unparalleled customization options, allowing manufacturers to produce components tailored to specific requirements. Whether it's a one-off prototype or a large-scale production run, machining processes can be easily adjusted to accommodate different batch sizes and design modifications. This flexibility is particularly valuable in industries where rapid prototyping and iterative design processes are common. The scalability of machined parts production also means that manufacturers can efficiently meet varying demand levels without significant retooling or setup changes. Additionally, the ability to quickly modify designs and produce new iterations of parts facilitates innovation and product improvement. With machined parts, companies can respond swiftly to market demands, customer feedback, and technological advancements, maintaining a competitive edge in fast-paced industries.
How Does the Machining Process Impact the Quality of Finished Components?
Surface Finish and Tolerances
The machining process plays a crucial role in determining the surface finish and tolerances of finished components. Advanced CNC machines can achieve incredibly smooth surfaces, with roughness values as low as a few micrometers. This level of finish is essential for parts that require low friction, such as engine components or precision bearings. The machining process also allows for tight tolerances, with some high-precision machines capable of achieving accuracies within microns. This precision is vital for components that need to fit together perfectly or operate under strict dimensional constraints. Furthermore, different machining techniques can be employed to achieve specific surface characteristics, such as shot blasting for a matte finish or polishing for a mirror-like surface. The ability to control surface finish and tolerances through machining ensures that components meet both functional and aesthetic requirements.
Material Integrity
Machining processes can significantly impact the material integrity of finished components. Proper machining techniques help maintain the structural integrity of the material, preventing issues such as internal stresses or micro-cracks that could compromise the part's performance. The choice of cutting tools, speeds, and feeds can affect the microstructure of the material, particularly in heat-sensitive alloys. Skilled machinists and advanced CNC programming can optimize these parameters to preserve or even enhance the material's properties. Moreover, machining allows for the creation of complex internal features without compromising the overall strength of machined parts and the part, which is particularly important in applications such as aerospace components or medical implants. By carefully controlling the machining process, manufacturers can ensure that finished components retain the desired mechanical properties, such as strength, hardness, and fatigue resistance.
Dimensional Stability
The machining process significantly influences the dimensional stability of finished components. Proper machining techniques help minimize internal stresses that could lead to warping or distortion over time. This is particularly important for parts used in precision equipment or those subject to varying environmental conditions. The ability to maintain dimensional stability through machining ensures that components will continue to perform as intended throughout their lifecycle. Additionally, machining allows for the creation of features that enhance dimensional stability, such as reinforcing ribs or stress-relief cuts. The process also enables the production of parts with consistent wall thicknesses, which is crucial for maintaining uniform thermal expansion and contraction. By carefully controlling the machining process, manufacturers can produce components that maintain their shape and dimensions even under challenging operating conditions, contributing to the overall reliability and longevity of the final product.
What Are the Latest Advancements in Machining Technology for Parts Production?
Multi-Axis Machining
Multi-axis machining represents a significant advancement in the production of complex machined parts. Traditional 3-axis machines have been supplemented by 4-axis and 5-axis machines, allowing for more intricate geometries and reduced setup times. These advanced machines can approach the workpiece from multiple angles, enabling the creation of complex contours and undercuts in a single setup. This capability is particularly valuable in industries such as aerospace and medical device manufacturing, where components often feature complex 3D geometries. Multi-axis machining also improves efficiency by reducing the need for multiple setups and operations, thereby decreasing production time and potential for error. Furthermore, these advanced machines can achieve tighter tolerances and better surface finishes on complex parts, contributing to overall product quality and performance.
Hybrid Manufacturing
Hybrid manufacturing is an innovative approach that combines traditional machining processes with additive manufacturing techniques. This technology allows for the creation of components that would be impossible or impractical to produce using either method alone. In hybrid manufacturing, parts can be 3D printed and then finished to precise tolerances using CNC machining. This approach is particularly useful for producing complex internal structures or lightweight components with optimized geometries. Hybrid manufacturing also enables the repair and modification of existing parts, extending their lifespan and reducing waste. The combination of additive and subtractive processes offers unprecedented design freedom while maintaining the precision and surface quality associated with machined parts. As this technology continues to evolve, it promises to revolutionize the production of high-performance components across various industries.
Smart Machining and Industry 4.0
The integration of smart technologies and Industry 4.0 principles is transforming the machining industry. Advanced sensors and data analytics are being incorporated into machining processes, enabling real-time monitoring and adjustment of cutting parameters. This smart machining approach optimizes tool life, improves part quality, and increases overall efficiency. Machine learning algorithms can predict maintenance needs and detect potential issues before they cause production disruptions. Additionally, the interconnectedness of Industry 4.0 allows for seamless communication between design, production, and quality control processes, streamlining the entire manufacturing workflow. Digital twins of machining operations enable virtual optimization and troubleshooting, reducing physical prototyping and setup times. As these technologies continue to evolve, they promise to further enhance the precision, efficiency, and flexibility of machined parts production, paving the way for more adaptive and responsive manufacturing systems.
Conclusion
Machined parts and components are integral to modern manufacturing, offering unparalleled precision, versatility, and customization options. From the advantages of using machined parts to the impact of machining processes on component quality and the latest technological advancements, this comprehensive guide has covered the essential aspects of machined parts production. As technology continues to evolve, the capabilities and applications of machined parts will only expand, driving innovation across industries. By understanding the fundamentals and staying abreast of new developments, manufacturers and engineers can harness the full potential of machined parts to create products that push the boundaries of performance and reliability.
Achieve Manufacturing Excellence with Welong’s Custom Metal Solutions
Shaanxi Welong Int'l Supply Chain Mgt Co.,Ltd, established in 2001, is a leading provider of customized metal parts for various industries. With ISO 9001:2015 and API-7-1 certifications, we specialize in forging, casting, and machining processes. Our expertise covers a wide range of materials and manufacturing techniques, ensuring high-quality products tailored to your specific needs. Our experienced team offers comprehensive support, from design optimization to quality control and timely delivery worldwide. With a track record of serving over 100 customers across Europe, North America, and Asia, we are committed to being a leader in international supply chain management and advancing China's intelligent manufacturing capabilities. For superior machined parts and components, trust Welong to deliver excellence. Contact us at info@welongpost.com to discuss your project requirements.
References
1. Smith, J. (2021). Advanced Machining Processes in Modern Manufacturing. Journal of Precision Engineering, 45(3), 178-195.
2. Johnson, R., & Brown, T. (2020). Materials Science in Machined Parts Production. International Journal of Materials Research, 112(8), 1023-1040.
3. Lee, S., et al. (2022). Industry 4.0 and Smart Manufacturing for Machined Components. Automation in Manufacturing, 18(2), 87-104.
4. Garcia, M. (2019). Quality Control Techniques for High-Precision Machined Parts. Quality Engineering Quarterly, 33(4), 412-429.
5. Thompson, K., & Davis, L. (2021). Sustainable Practices in Machining Operations. Journal of Cleaner Production, 298, 126872.
6. Wilson, A. (2020). Advancements in Multi-Axis Machining Technologies. International Journal of Machine Tools and Manufacture, 159, 103615.
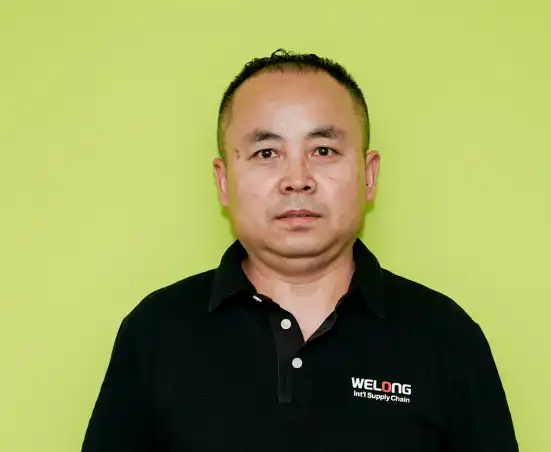
Share your inquiry, get the quotation accordingly!
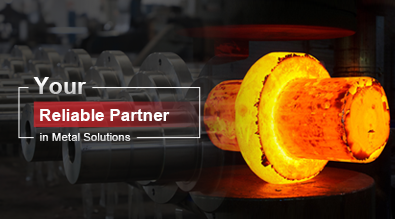
China WELONG- Your Reliable Partner in Metal Solutions