Which Casting Process Is Right for Your Parts?
When it comes to manufacturing metal components, selecting the right casting process is crucial for achieving optimal quality, efficiency, and cost-effectiveness. The choice of casting method can significantly impact the final product's properties, production time, and overall expenses. With various casting techniques available, such as sand casting, gravity casting, and centrifugal casting, it's essential to understand the strengths and limitations of each process to make an informed decision. This blog post will explore different casting methods, their applications, and the factors to consider when choosing the most suitable process for your specific casting parts and parts. By the end of this article, you'll have a better understanding of how to select the ideal casting technique that aligns with your project requirements, ensuring superior results and maximizing the value of your manufacturing efforts.
What Are the Key Differences Between Sand Casting and Investment Casting?
Process Overview
Sand casting and investment casting are two popular methods for producing metal parts, each with its unique characteristics. Sand casting involves creating a mold using compacted sand, into which molten metal is poured. This process is versatile and cost-effective, making it suitable for a wide range of casting parts, from small components to large machinery parts. On the other hand, investment casting, also known as lost-wax casting, utilizes a wax pattern that is coated with ceramic material to create a precise mold. This method is ideal for producing complex, high-precision parts with excellent surface finishes. Both processes have their strengths and are chosen based on the specific requirements of the casting parts being manufactured.
Material Considerations
The choice between sand casting and investment casting often depends on the material properties required for the final casting parts. Sand casting is compatible with a wide range of metals, including iron, steel, aluminum, and copper alloys. This versatility makes it an excellent choice for producing various casting parts across different industries. Investment casting, while more limited in terms of material options, excels in working with high-temperature alloys, stainless steel, and other materials that require intricate details and smooth surfaces. The investment casting process allows for better control over the material's grain structure, resulting in improved mechanical properties for certain casting parts that demand high performance in challenging environments.
Cost and Production Volume
When considering the economics of producing casting parts, sand casting and investment casting offer different advantages depending on the production volume and part complexity. Sand casting generally has lower tooling costs and is more economical for large parts or small to medium production runs. This makes it an attractive option for prototyping or producing a limited number of casting parts. Investment casting, while having higher initial tooling costs, becomes more cost-effective for higher volume production of small to medium-sized parts with complex geometries. The superior surface finish and tighter tolerances achieved through investment casting can also reduce the need for secondary machining operations, potentially lowering overall production costs for certain types of casting parts.
How Does Gravity Casting Compare to Pressure Die Casting?
Process Mechanics
Gravity casting and pressure die casting are two distinct methods used to produce metal casting parts, each with its own set of advantages. Gravity casting relies on the natural force of gravity to fill the mold with molten metal, resulting in a relatively simple and cost-effective process for producing casting parts. This method is particularly suitable for large components or those with thick walls. Pressure die casting, on the other hand, uses high pressure to inject molten metal into a steel mold at high speed. This process is ideal for creating complex, thin-walled casting parts with excellent dimensional accuracy and smooth surface finishes. The choice between these two methods often depends on the specific requirements of the casting parts, including size, complexity, and production volume.
Production Efficiency
When it comes to production efficiency, gravity casting and pressure die casting offer different benefits for manufacturing casting parts. Gravity casting typically has lower tooling costs and is more flexible in terms of mold design, making it suitable for small to medium production runs or for casting parts that require frequent design changes. However, the cycle time for gravity casting can be longer, which may limit its efficiency for high-volume production. Pressure die casting, in contrast, excels in high-volume production scenarios, with faster cycle times and the ability to produce multiple casting parts in a single shot. This makes pressure die casting particularly efficient for industries requiring large quantities of small to medium-sized components with consistent quality.
Quality and Finish
The quality and finish of casting parts produced by gravity casting and pressure die casting can vary significantly. Gravity casting generally produces parts with good mechanical properties and can accommodate a wide range of alloys. However, the surface finish may require additional post-processing, and the method may not be suitable for parts with very thin walls or intricate details. Pressure die casting, on the other hand, is known for producing casting parts with excellent surface finishes, tight tolerances, and the ability to create complex geometries with thin walls. The high pressure used in this process also results in a denser microstructure, which can improve the mechanical properties of the casting parts. When selecting between these two methods, it's essential to consider the specific quality requirements and surface finish needs of your casting parts to ensure the best results for your application.
What Factors Should Be Considered When Choosing Between Centrifugal Casting and Static Casting?
Part Geometry
When deciding between centrifugal casting and static casting for producing casting parts, the geometry of the desired component plays a crucial role. Centrifugal casting is particularly well-suited for cylindrical or tubular casting parts, such as pipes, bushings, and rings. The centrifugal force generated during the process helps distribute the molten metal evenly along the mold walls, resulting in a uniform thickness and dense structure. This method is ideal for parts with symmetrical cross-sections and can produce components with excellent concentricity. Static casting, on the other hand, offers more flexibility in terms of part geometry and can be used to create casting parts with complex shapes, undercuts, and varying wall thicknesses. When evaluating which process to use, consider the overall shape and features of your casting parts to determine which method will yield the best results.
Material Properties
The choice between centrifugal casting and static casting can significantly impact the material properties of the resulting casting parts. Centrifugal casting is known for producing parts with superior mechanical properties due to the directional solidification that occurs during the process. This method can result in a finer grain structure, reduced porosity, and improved material density, which are particularly beneficial for casting parts that require high strength and wear resistance. Static casting, while capable of producing parts with good mechanical properties, may not achieve the same level of material refinement as centrifugal casting. However, static casting offers more flexibility in terms of alloy selection and can be used with a wider range of materials, including those that may be challenging to use in centrifugal casting. When selecting between these methods, consider the specific material requirements of your casting parts and how they align with the strengths of each process.
Production Volume and Cost
Production volume and cost considerations play a significant role in choosing between centrifugal casting and static casting for manufacturing casting parts. Centrifugal casting typically requires specialized equipment and tooling, which can result in higher initial setup costs. However, this method becomes more cost-effective for large production runs of cylindrical or tubular casting parts, as it offers faster cycle times and reduced material waste. Static casting, such as sand casting or investment casting, generally has lower tooling costs and is more economical for smaller production runs or when producing a variety of different casting parts. The choice between these methods often depends on the expected production volume, the complexity of the parts, and the overall project budget. By carefully evaluating these factors, manufacturers can select the most cost-effective and efficient process for producing their specific casting parts.
Conclusion
Selecting the right casting process for your parts is a critical decision that impacts quality, efficiency, and cost-effectiveness. By understanding the strengths and limitations of various casting methods, such as sand casting, investment casting, gravity casting, pressure die casting, and centrifugal casting, manufacturers can make informed choices tailored to their specific needs. Factors such as part geometry, material properties, production volume, and cost considerations all play crucial roles in determining the most suitable casting technique. By carefully evaluating these factors and aligning them with project requirements, manufacturers can optimize their production processes and achieve superior results in their casting parts.
Power Your Projects with Welong’s Precision Casting & Forging Solutions
Shaanxi Welong Int'l Supply Chain Mgt Co.,Ltd. is a leading provider of customized metal parts for various industries. With over 20 years of experience and certifications including ISO 9001:2015 and API-7-1, we specialize in forging, sand casting, investment casting, centrifugal casting, and machining. Our expertise covers a wide range of materials and processes, ensuring high-quality products tailored to our customers' needs. We offer comprehensive support, from design and production to quality control and timely delivery worldwide. Our commitment to excellence, competitive pricing, and outstanding service has earned us a global customer base across more than 100 clients. Choose Welong for innovative solutions and reliable partnerships in metal casting and manufacturing. Contact us at info@welongpost.com to discover how we can contribute to your project's success.
References
1. Campbell, J. (2015). Complete Casting Handbook: Metal Casting Processes, Techniques and Design. Butterworth-Heinemann.
2. Beeley, P. R. (2001). Foundry Technology. Butterworth-Heinemann.
3. Brown, J. R. (1999). Foseco Ferrous Foundryman's Handbook. Butterworth-Heinemann.
4. Kalpakjian, S., & Schmid, S. R. (2014). Manufacturing Engineering and Technology. Pearson.
5. ASM International. (2008). ASM Handbook, Volume 15: Casting. ASM International.
6. Groover, M. P. (2010). Fundamentals of Modern Manufacturing: Materials, Processes, and Systems. John Wiley & Sons.
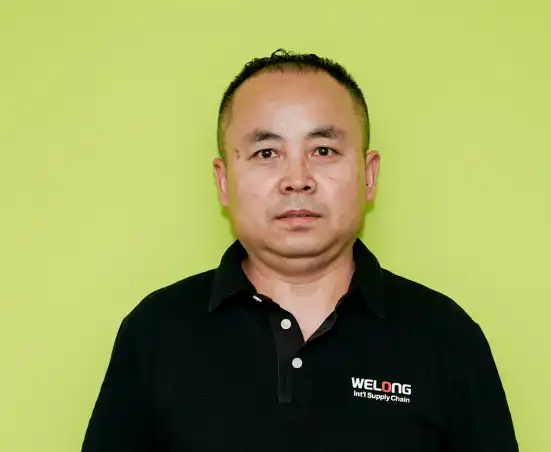
Share your inquiry, get the quotation accordingly!
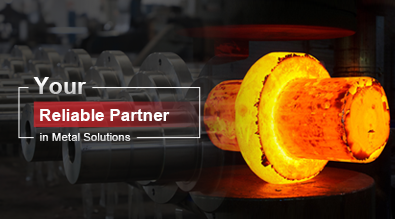
China WELONG- Your Reliable Partner in Metal Solutions