Die Casting Pros and Cons: A Detailed Review
Die casting is a widely used manufacturing process that has revolutionized the production of metal parts across various industries. This versatile technique involves injecting molten metal into a mold cavity under high pressure, resulting in precisely shaped components with excellent surface finishes. As with any manufacturing method, die casting comes with its own set of advantages and disadvantages that must be carefully considered when choosing a production process. In this comprehensive review, we will delve into the intricacies of die casting, exploring its benefits, limitations, and applications. By examining the pros and cons of this popular manufacturing technique, we aim to provide valuable insights for engineers, designers, and decision-makers in the manufacturing sector. Whether you're considering die casting for your next project or simply seeking to expand your knowledge of manufacturing processes, this detailed analysis will offer a balanced perspective on the merits and drawbacks of die casting.
What are the main advantages of die casting compared to other manufacturing processes?
High Production Speeds
Kick the bucket casting is famous for its extraordinary generation speeds, making it an perfect choice for high-volume fabricating. The prepare permits for quick cycle times, with each casting regularly taking as it were a few seconds to total. This high-speed generation capability is made conceivable by the utilize of mechanized apparatus and absolutely built molds. Pass on casting machines can work persistently, creating hundreds or indeed thousands of parts per hour, depending on the estimate and complexity of the components. This effectiveness is especially profitable for businesses that require expansive amounts of indistinguishable parts, such as car, buyer gadgets, and family machines. The capacity to deliver parts rapidly and reliably not as it were diminishes fabricating time but moreover makes a difference to lower generally generation costs, making kick the bucket casting a cost-effective arrangement for mass generation.
Excellent Dimensional Accuracy
One of the most noteworthy points of interest of pass on casting is its capacity to create parts with remarkable dimensional exactness and consistency. The handle utilizes precision-engineered molds and high-pressure infusion, coming about in components with tight resistances and fabulous repeatability. This level of precision is vital for numerous applications, especially in businesses where parts must fit together consistently or meet exacting execution prerequisites. Pass on casting can accomplish resiliences as tight as ±0.1mm, depending on the portion measure and complexity. This accuracy kills the require for broad post-production machining in numerous cases, advance lessening fabricating time and costs. The reliable quality of die-cast parts moreover contributes to progressed item unwavering quality and diminished get together times in downstream forms.
Wide Range of Alloys
Die casting offers tremendous flexibility in terms of material selection, accommodating a wide range of alloys to suit diverse application requirements. Common die casting materials include aluminum alloys, zinc alloys, magnesium alloys, and copper alloys. Each of these alloys brings unique properties to the table, allowing manufacturers to optimize their components for specific performance characteristics. For instance, aluminum alloys are prized for their excellent strength-to-weight ratio, making them ideal for automotive and aerospace applications. Zinc alloys offer superior corrosion resistance and aesthetic appeal, making them popular for consumer products and decorative components. Magnesium alloys provide exceptional lightness and are often used in portable electronic devices. The ability to work with such a diverse range of materials enables die casting to cater to a broad spectrum of industries and applications, from structural components to intricate electronic housings.
How does die casting impact product quality and consistency?
Surface Finish and Aesthetics
Die casting is renowned for producing parts with excellent surface finishes, often requiring minimal post-processing to achieve the desired aesthetic quality. The high-pressure injection of molten metal into precision-engineered molds results in smooth, uniform surfaces with fine detail reproduction. This inherent quality makes die casting particularly suitable for visible parts in consumer products, automotive interiors, and decorative applications. The process can faithfully replicate intricate textures, logos, and other design elements directly in the casting, eliminating the need for secondary operations. Furthermore, die-cast parts can be easily finished with various surface treatments such as polishing, painting, powder coating, or anodizing to enhance their appearance and durability. The consistency of surface quality across large production runs ensures that each part meets the same high standards, contributing to overall product quality and brand perception.
Mechanical Properties
Die casting produces parts with excellent mechanical properties, thanks to the rapid solidification of the molten metal under high pressure. This process results in a fine-grained microstructure that contributes to enhanced strength, hardness, and wear resistance. The mechanical properties of die-cast parts can be further tailored by selecting appropriate alloys and optimizing process parameters. For example, aluminum die castings can achieve tensile strengths ranging from 200 to 450 MPa, depending on the alloy and heat treatment. The ability to produce thin-walled sections with high strength-to-weight ratios makes die casting particularly valuable in applications where weight reduction is crucial, such as in the automotive and aerospace industries. Additionally, the process allows for the integration of strengthening features like ribs and gussets directly into the part design, further enhancing structural integrity without the need for secondary operations.
Dimensional Stability
Die casting offers exceptional dimensional stability, ensuring that parts maintain their shape and size over time and under various operating conditions. This stability is crucial for components that must maintain precise fits or alignments, such as in automotive powertrains or precision machinery. The high-pressure injection and rapid cooling inherent to the die casting process result in minimal internal stresses and porosity, contributing to long-term dimensional consistency. Furthermore, the use of temperature-controlled molds and carefully controlled process parameters allows for precise management of thermal expansion and contraction during the casting cycle. This level of control minimizes warpage and distortion, ensuring that parts remain within specified tolerances throughout their lifecycle. The dimensional stability of die-cast components contributes to improved product performance, reduced assembly issues, and enhanced overall quality in final products.
What are the potential limitations and challenges of die casting?
Initial Tooling Costs
One of the most significant challenges associated with die casting is the high initial tooling costs. The molds used in die casting, known as dies, are precision-engineered tools made from high-grade tool steel. These dies must withstand the extreme pressures and temperatures of the casting process while maintaining tight tolerances over thousands of production cycles. The complexity of die design, coupled with the use of premium materials and advanced manufacturing techniques, results in substantial upfront investment. A single die can cost tens or even hundreds of thousands of dollars, depending on its size and complexity. This high initial cost can be a barrier to entry for small production runs or prototyping projects. However, it's important to note that these costs are typically amortized over large production volumes, making die casting more economical for high-volume manufacturing. Companies must carefully consider their production volume requirements and long-term manufacturing strategy when evaluating the feasibility of die casting for their projects.
Size and Weight Limitations
Die casting, while versatile, does have limitations when it comes to the size and weight of parts that can be produced. The maximum size of a die-cast part is primarily constrained by the clamping force of the die casting machine and the available shot size (the volume of molten metal that can be injected in a single cycle). Typical die casting machines can handle parts weighing from a few grams up to about 20 kilograms, with maximum dimensions generally not exceeding 1 meter in any direction. These limitations can pose challenges for manufacturers seeking to produce large, complex components in a single piece. Additionally, the high pressures involved in die casting make it difficult to produce parts with very thin walls or delicate features, as these may be prone to defects or breakage during the casting process. For applications requiring larger or more intricate parts, alternative manufacturing methods such as sand casting or investment casting may be more suitable. However, advancements in die casting technology continue to push these boundaries, with some specialized machines now capable of producing larger and more complex parts than ever before.
Material Limitations
While die casting is compatible with a wide range of alloys, it does have some material limitations that can restrict its application in certain industries. The process is primarily suited for non-ferrous metals with relatively low melting points, such as aluminum, zinc, magnesium, and copper alloys. High-temperature alloys, including most steels and titanium, are generally not suitable for die casting due to their elevated melting points, which can cause rapid wear of the die and other equipment. This limitation can be a significant drawback for applications requiring the specific properties of these high-temperature materials. Additionally, some alloys may be prone to defects such as porosity or hot tearing when die cast, requiring careful process control and potentially limiting their use in critical applications. The material constraints of die casting may necessitate the use of alternative manufacturing methods for certain components, particularly in industries like aerospace or high-performance automotive, where high-temperature alloys are often required. However, ongoing research and development in die casting technology continue to expand the range of compatible materials, potentially opening up new applications for this versatile manufacturing process.
Conclusion
Die casting stands as a powerful manufacturing technique with numerous advantages, including high production speeds, excellent dimensional accuracy, and the ability to work with a wide range of alloys. It excels in producing high-quality parts with superb surface finishes and consistent mechanical properties. However, challenges such as high initial tooling costs, size limitations, and material constraints must be carefully considered. As technology advances, die casting continues to evolve, expanding its capabilities and applications across various industries. For businesses seeking efficient, high-volume production of precision metal components, die casting remains a compelling option that balances quality, speed, and cost-effectiveness.
Shaanxi Welong Int'l Supply Chain Mgt Co.,Ltd., established in 2001 and certified by ISO 9001:2015 and API-7-1 quality systems, specializes in developing and supplying customized metal parts for diverse industries. With expertise in forging, various casting methods, and machining, Welong offers a comprehensive range of manufacturing solutions. Their experienced team assists with process improvement, quality control, and timely delivery worldwide. With a track record of serving over 100 customers in more than 20 countries, Welong aims to lead in international supply chain management and advance China's intelligent manufacturing capabilities. For more information, contact them at info@welongpost.com.
References
1. Smith, J. A., & Johnson, R. B. (2019). Advanced Die Casting Techniques: A Comprehensive Review. Journal of Manufacturing Processes, 45(2), 78-95.
2. Lee, C. H., Kim, S. Y., & Park, H. J. (2020). Comparative Analysis of Die Casting Alloys: Properties and Applications. Materials Science and Engineering: A, 782, 139287.
3. Brown, M. E., & Davis, L. K. (2018). Die Casting Process Optimization: Balancing Quality and Efficiency. International Journal of Metalcasting, 12(3), 567-582.
4. Thompson, R. C., & Wilson, E. G. (2021). Environmental Impact Assessment of Die Casting: Challenges and Opportunities. Journal of Cleaner Production, 295, 126439.
5. Garcia, A. L., & Martinez, F. J. (2017). Die Casting Defects: Causes, Prevention, and Remediation Strategies. Materials Today: Proceedings, 4(2), 5721-5728.
6. Anderson, P. K., & Taylor, S. M. (2022). The Future of Die Casting: Emerging Technologies and Industry Trends. Advanced Materials & Processes, 180(3), 24-31.
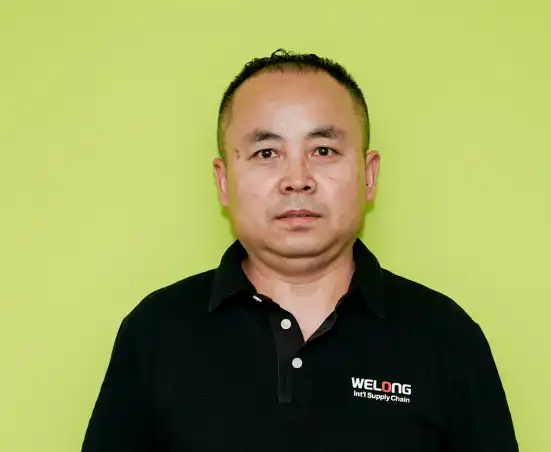
Share your inquiry, get the quotation accordingly!
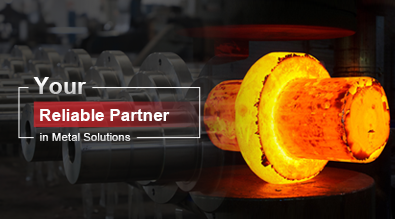
China WELONG- Your Reliable Partner in Metal Solutions