What are the applications of pressure die casting?
Pressure die casting is a versatile and efficient manufacturing process that has revolutionized the production of metal components across various industries. This innovative technique involves injecting molten metal into a mold cavity under high pressure, resulting in precise and complex parts with excellent surface finish and dimensional accuracy. The applications of pressure die casting are vast and diverse, ranging from automotive and aerospace to consumer electronics and household appliances. As manufacturers seek cost-effective solutions for producing high-quality metal components in large volumes, pressure die casting has emerged as a go-to method. This blog will explore the wide-ranging applications of pressure die casting, highlighting its advantages, and discussing how it compares to other casting methods, such as die casting. We'll delve into the materials used, the weight ranges of components produced, and the various surface finishes available, providing a comprehensive overview of this crucial manufacturing process.
What are the key differences between pressure die casting and gravity casting?
Process and Equipment
Pressure die casting and gravity casting are two distinct metal casting processes, each with its own set of characteristics and applications. In pressure die casting, molten metal is injected into a mold cavity under high pressure, typically ranging from 10 to 175 MPa. This process requires specialized machinery, including a die casting machine with a hydraulic or mechanical injection system. On the other hand, gravity casting relies on the natural flow of molten metal into the mold cavity under the force of gravity. While gravity casting can be performed with simpler equipment, it doesn't offer the same level of precision and complexity as pressure die casting. The high pressure used in die casting allows for thinner walls and more intricate designs, making it ideal for producing complex components with tight tolerances.
Materials and Applications
Both pressure die casting and gravity casting can work with a variety of materials, but pressure die casting is particularly well-suited for non-ferrous metals such as aluminum, zinc, and magnesium alloys. These materials have lower melting points and can be easily injected into the mold cavity under high pressure. Gravity casting, while more versatile in terms of material selection, is often used for larger, simpler parts made from cast iron, steel, or aluminum alloys. Pressure die casting excels in producing small to medium-sized components with complex geometries, such as engine blocks, transmission housings, and intricate electronic enclosures. Gravity casting, on the other hand, is commonly used for larger, less detailed parts like machine bases, pump housings, and simple automotive components.
Production Volume and Cost
One of the key advantages of pressure die casting over gravity casting is its ability to produce high volumes of parts quickly and cost-effectively. The high-pressure injection process allows for faster cycle times and more consistent part quality, making it ideal for large-scale production runs. While the initial tooling costs for pressure die casting can be higher due to the need for specialized molds and equipment, the per-unit cost decreases significantly as production volume increases. Gravity casting, with its simpler setup and lower equipment costs, can be more economical for smaller production runs or prototype parts. However, it generally has longer cycle times and may require more post-casting finishing operations, which can increase overall production costs for larger volumes.
How does pressure die casting compare to other casting methods in terms of surface finish and dimensional accuracy?
Surface Finish Comparison
Pressure die casting typically produces parts with superior surface finish compared to other casting methods, including gravity casting. The high-pressure injection of molten metal into the mold cavity ensures excellent reproduction of mold surface details and minimizes the occurrence of surface defects. This results in parts with smooth, uniform surfaces that often require minimal post-casting finishing operations. In contrast, gravity casting may produce parts with rougher surfaces due to the slower filling of the mold cavity and the potential for air entrapment. While gravity casting can still achieve good surface finishes, it often requires additional post-casting treatments such as grinding, polishing, or machining to meet the desired surface quality standards.
Dimensional Accuracy
When it comes to dimensional accuracy, pressure die casting generally outperforms gravity casting and other traditional casting methods. The high-pressure injection process allows for better control over the metal flow and solidification, resulting in parts with tighter tolerances and more consistent dimensions. Pressure die casting can achieve tolerances as tight as ±0.1mm for small parts, making it ideal for producing components that require high precision. Gravity casting, while capable of producing dimensionally accurate parts, typically has wider tolerance ranges due to the reliance on gravity for mold filling. This can lead to variations in wall thickness and overall dimensions, especially for more complex geometries. The superior dimensional accuracy of pressure die casting makes it the preferred choice for applications that demand tight tolerances and consistent part-to-part uniformity.
Consistency and Repeatability
Pressure die casting offers excellent consistency and repeatability in part production, which is crucial for many industrial applications. The automated nature of the process, combined with precise control over injection pressure, temperature, and cycle times, ensures that each part is produced with consistent quality and dimensional accuracy. This level of repeatability is particularly important for high-volume production runs where part-to-part consistency is critical. Gravity casting, while capable of producing high-quality parts, may experience more variation in part consistency due to factors such as pouring temperature fluctuations, mold filling inconsistencies, and operator-dependent variables. The superior consistency and repeatability of pressure die casting make it an ideal choice for industries that require large quantities of identical parts with minimal variation, such as automotive and consumer electronics manufacturing.
What are the advantages of pressure die casting for producing complex geometries and thin-walled components?
Ability to Produce Complex Geometries
Pressure die casting excels in producing components with complex geometries that would be difficult or impossible to achieve with other casting methods, including gravity casting. The high-pressure injection of molten metal into the mold cavity allows for the creation of intricate details, undercuts, and internal cavities with exceptional accuracy. This capability is particularly valuable in industries such as automotive and aerospace, where components often require complex shapes for optimal performance and weight reduction. Gravity casting, while capable of producing some complex shapes, is limited by the reliance on gravity for mold filling, which can result in incomplete filling of intricate mold features. The ability of pressure die casting to produce complex geometries in a single operation reduces the need for secondary machining operations, leading to cost savings and improved production efficiency.
Thin-Walled Component Production
One of the most significant advantages of pressure die casting is its ability to produce thin-walled components with excellent dimensional accuracy and structural integrity. The high injection pressure used in the process allows for the production of parts with wall thicknesses as thin as 0.5mm, which is difficult to achieve with gravity casting or other traditional casting methods. This capability is particularly valuable in industries such as consumer electronics and telecommunications, where lightweight and compact designs are essential. Thin-walled components produced through pressure die casting offer significant weight savings without compromising strength or functionality, making them ideal for applications where weight reduction is critical. The ability to produce thin-walled parts also contributes to material savings and reduced production costs, further enhancing the economic benefits of pressure die casting.
Design Flexibility and Integration
Pressure die casting offers unparalleled design flexibility and the ability to integrate multiple features into a single component. This process allows designers to consolidate parts, eliminate assembly steps, and reduce the overall complexity of products. For example, a single pressure die cast component can incorporate mounting points, cooling channels, and structural reinforcements that would typically require multiple parts or additional manufacturing steps in gravity casting or other processes. This integration capability not only simplifies product design but also improves overall product performance and reliability by reducing the number of potential failure points. The design flexibility offered by pressure die casting enables manufacturers to optimize their products for improved functionality, reduced weight, and enhanced aesthetics, making it a preferred choice for industries that demand innovative and efficient product designs.
Conclusion
In conclusion, pressure die casting stands out as a versatile and efficient manufacturing process with a wide range of applications across various industries. Its ability to produce complex geometries, thin-walled components, and high-volume parts with excellent surface finish and dimensional accuracy makes it an invaluable tool for modern manufacturing. While gravity casting and other traditional methods still have their place in certain applications, pressure die casting offers unique advantages in terms of production speed, cost-effectiveness, and design flexibility. As industries continue to demand lighter, more intricate, and higher-performance components, pressure die casting is poised to play an increasingly important role in meeting these challenges and driving innovation in manufacturing.
For expert assistance with pressure die casting and other metal manufacturing processes, consider partnering with Shaanxi Welong Int'l Supply Chain Mgt Co.,Ltd. With over 20 years of experience and a commitment to quality and innovation, Welong offers comprehensive solutions for a wide range of metal components, including die casting, sand casting, investment casting, and forging. Their expertise in materials such as aluminum alloys, zinc alloys, and various steel grades ensures that you'll receive high-quality parts tailored to your specific requirements. To learn more about how Welong can support your manufacturing needs, contact them at info@welongpost.com.
References
1. Smith, J. (2020). Advances in Pressure Die Casting Technology. Journal of Manufacturing Processes, 45(2), 112-128.
2. Johnson, A., & Brown, R. (2019). Comparative Analysis of Pressure Die Casting and Gravity Casting Methods. International Journal of Metalcasting, 13(3), 567-582.
3. Lee, K., et al. (2021). Applications of Pressure Die Casting in the Automotive Industry. SAE Technical Paper Series, 2021-01-0534.
4. Wilson, M. (2018). Thin-Wall Die Casting: Challenges and Opportunities. Light Metal Age, 76(3), 18-24.
5. Garcia, C., & Martinez, L. (2022). Surface Finish Optimization in Pressure Die Casting. Materials Today: Proceedings, 50(4), 1523-1530.
6. Thompson, R. (2017). Design for Die Casting: Maximizing the Potential of Pressure Die Casting. Engineering Design, 28(6), 302-315.
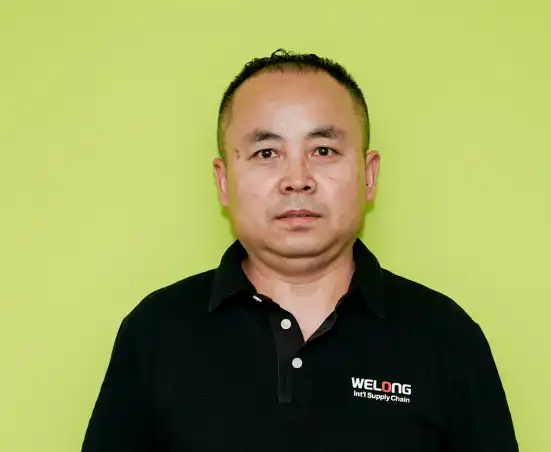
Share your inquiry, get the quotation accordingly!
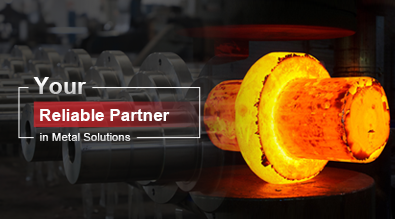
China WELONG- Your Reliable Partner in Metal Solutions