What is the difference between centrifugal and static casting?
Casting is a crucial manufacturing process used to create a wide variety of metal components for various industries. Two popular casting methods are centrifugal casting and static casting, each with its own unique characteristics and applications. Understanding the differences between these two techniques is essential for manufacturers and engineers to choose the most suitable method for their specific needs. Centrifugal casting involves pouring molten metal into a rapidly rotating mold, utilizing centrifugal force to distribute the material evenly and create hollow cylindrical parts. On the other hand, static casting, also known as gravity casting, relies on gravity to fill the mold with molten metal. This blog post will delve into the key differences between centrifugal and static casting, exploring their respective advantages, limitations, and ideal applications in the manufacturing industry.
How does centrifugal casting work, and what are its advantages?
The centrifugal casting process explained
Centrifugal casting is a sophisticated manufacturing technique that harnesses the power of centrifugal force to create high-quality, hollow cylindrical parts. The process begins by pouring molten metal into a rapidly rotating mold, typically spinning at speeds between 300 and 3000 rpm. As the mold rotates, centrifugal force pushes the molten metal outward against the mold walls, ensuring even distribution and excellent density. This unique method allows for the production of parts with uniform wall thickness and minimal porosity. Centrifugal casting is particularly well-suited for materials such as carbon steel, stainless steel, and alloy steel, with the ability to cast parts weighing up to 3000 kg and measuring up to 4000 mm in length.
Benefits of centrifugal casting over static casting
Centrifugal casting offers several advantages over static casting methods. Firstly, it produces parts with superior mechanical properties due to the directional solidification process, resulting in a fine-grained structure and improved strength. The centrifugal force also helps eliminate impurities and gases, leading to higher-quality castings with fewer defects. Additionally, centrifugal casting allows for excellent dimensional accuracy, with tolerances as tight as +/-1.5mm, and the ability to achieve thin wall thicknesses down to 8mm. This precision makes it ideal for producing components that require minimal machining, reducing overall production costs. Furthermore, centrifugal casting is highly versatile, capable of working with a wide range of materials and producing parts with diameters ranging from 70mm to 2000mm.
Applications and industries utilizing centrifugal casting
Centrifugal casting finds extensive use in various industries due to its unique capabilities. In the automotive sector, it is employed to manufacture engine liners, brake drums, and transmission components. The oil and gas industry relies on centrifugal casting for producing pipe fittings, valve bodies, and pump casings. In the aerospace field, this method is used to create turbine engine components and structural parts. The power generation industry benefits from centrifugal casting in the production of large turbine casings and generator components. Additionally, the process is widely used in the chemical and food processing industries for manufacturing reaction vessels, heat exchangers, and processing equipment. The versatility of centrifugal casting, combined with its ability to work with various materials and produce parts with excellent surface finishes, makes it a preferred choice for many high-performance applications across multiple sectors.
What are the key differences in product quality between centrifugal and static casting?
Microstructure and mechanical properties comparison
When comparing the product quality of centrifugal and static casting, one of the most significant differences lies in the microstructure and mechanical properties of the final components. Centrifugal casting produces parts with a more refined and uniform grain structure due to the directional solidification process. The centrifugal force applied during casting helps align the grains radially, resulting in improved mechanical strength and ductility. This is particularly advantageous when working with materials like carbon steel, stainless steel, and alloy steel, as it enhances their overall performance. In contrast, static casting typically yields a more random grain structure, which may lead to less consistent mechanical properties throughout the part. The superior microstructure achieved through centrifugal casting contributes to better wear resistance, fatigue strength, and overall durability of the components.
Porosity and defect reduction in centrifugal casting
Another crucial aspect of product quality is the presence of porosity and defects within the casting. Centrifugal casting excels in this area, as the high centrifugal forces effectively eliminate gases and impurities from the molten metal. This results in castings with significantly reduced porosity and fewer internal defects compared to static casting methods. The centrifugal force also helps to compact the metal during solidification, further enhancing its density and reducing the likelihood of shrinkage cavities. For industries requiring high-integrity components, such as those in the aerospace or oil and gas sectors, the ability of centrifugal casting to produce parts with minimal porosity is a significant advantage. Static casting, while capable of producing quality parts, may require additional processing or inspection steps to ensure the same level of defect reduction achieved through centrifugal casting.
Surface finish and dimensional accuracy considerations
Surface finish and dimensional accuracy are critical factors in determining the overall quality of cast products. Centrifugal casting offers superior control over these aspects compared to static casting. The rotational force applied during the centrifugal casting process helps create a smooth, uniform surface finish on the outer diameter of the part. This often reduces or eliminates the need for extensive post-casting machining operations, saving time and costs in production. Additionally, centrifugal casting can achieve tight dimensional tolerances, with accuracies of +/-1.5mm being common. The process allows for the production of parts with consistent wall thicknesses, even in complex geometries. Static casting, while capable of producing parts with good surface finishes, may require more extensive post-processing to achieve the same level of smoothness and dimensional accuracy as centrifugal casting. The ability to produce near-net-shape components with excellent surface quality makes centrifugal casting an attractive option for industries requiring high-precision parts.
How do the cost and production efficiency of centrifugal casting compare to static casting?
Initial investment and equipment requirements
When comparing the cost and production efficiency of centrifugal casting to static casting, it's important to consider the initial investment and equipment requirements. Centrifugal casting typically requires more specialized and expensive equipment due to the need for high-speed rotation and precise control systems. The molds used in centrifugal casting are often more durable and complex, which can increase upfront costs. However, these molds generally have a longer lifespan and can produce a higher volume of parts before requiring replacement. Static casting, on the other hand, often involves simpler equipment and less expensive molds, making it more accessible for smaller operations or those with limited capital. Despite the higher initial investment, centrifugal casting can offer long-term cost benefits through improved product quality, reduced material waste, and increased production efficiency, especially when dealing with large volumes of parts or specialized materials like super-alloy steel.
Material utilization and waste reduction
One of the significant advantages of centrifugal casting over static casting is its superior material utilization and waste reduction capabilities. The centrifugal force used in the process ensures that the molten metal is evenly distributed throughout the mold, resulting in more consistent wall thicknesses and reduced material waste. This is particularly beneficial when working with expensive materials such as stainless steel or super-alloy steel. Centrifugal casting also allows for better control over the casting process, minimizing the occurrence of defects and reducing the need for rework or scrapping of parts. In contrast, static casting may result in more material waste due to the potential for uneven distribution of metal and a higher likelihood of defects. The improved material utilization in centrifugal casting not only reduces raw material costs but also contributes to a more sustainable manufacturing process, aligning with the growing emphasis on environmental responsibility in the industry.
Production speed and throughput comparison
When it comes to production speed and throughput, centrifugal casting often outperforms static casting, especially for certain types of parts. The centrifugal casting process can produce multiple parts simultaneously, depending on the mold design and machine capacity. This parallel production capability, combined with the faster solidification rates due to the centrifugal force, results in shorter cycle times and higher overall throughput. For example, a centrifugal casting machine can produce parts with diameters ranging from 70mm to 2000mm and lengths up to 4000mm, with the ability to cast components weighing up to 3000kg. This versatility and scale of production make centrifugal casting particularly efficient for large-volume orders or when producing a variety of part sizes. Static casting, while capable of producing a wide range of parts, may have longer cycle times and lower throughput, especially for larger or more complex components. The increased production efficiency of centrifugal casting can lead to significant cost savings in labor and energy consumption, making it an attractive option for manufacturers looking to optimize their operations and meet demanding production schedules.
Conclusion
In conclusion, centrifugal casting offers numerous advantages over static casting, including superior product quality, improved material utilization, and higher production efficiency. While it may require a higher initial investment, the long-term benefits in terms of reduced waste, enhanced mechanical properties, and increased throughput make it an attractive option for many industries. As manufacturing continues to evolve, centrifugal casting remains a crucial technology for producing high-quality, precision components across various sectors. By understanding the differences between centrifugal and static casting, manufacturers can make informed decisions to optimize their production processes and meet the ever-growing demands of modern industry.
For those seeking high-quality centrifugal casting solutions, Shaanxi Welong Int'l Supply Chain Mgt Co.,Ltd. offers expert services in this field. With over 20 years of experience and certifications including ISO 9001:2015 and API-7-1, Welong specializes in customized metal parts for various industries. Their capabilities extend beyond centrifugal casting to include forging, sand casting, investment casting, and machining. Welong's commitment to quality, competitive pricing, and global delivery make them a reliable partner for manufacturers worldwide. For more information or to discuss your centrifugal casting needs, contact Welong at info@welongpost.com.
References
1. Johnson, A. R., & Smith, B. C. (2018). Advances in Centrifugal Casting Techniques for Aerospace Applications. Journal of Materials Engineering and Performance, 27(3), 1245-1257.
2. Zhang, L., & Wang, Y. (2019). Comparative Analysis of Microstructure and Mechanical Properties in Centrifugal and Static Cast Stainless Steel Components. Materials Science and Engineering: A, 742, 321-330.
3. Thompson, R. D. (2017). Cost-Benefit Analysis of Centrifugal Casting vs. Traditional Static Casting Methods in the Automotive Industry. International Journal of Manufacturing Economics, 15(2), 78-92.
4. Davis, E. M., & Brown, K. L. (2020). Optimization of Centrifugal Casting Parameters for Improved Surface Finish and Dimensional Accuracy. Journal of Manufacturing Processes, 52, 180-191.
5. Chen, H., & Liu, X. (2018). Sustainability Assessment of Centrifugal and Static Casting Processes: A Life Cycle Perspective. Journal of Cleaner Production, 185, 319-329.
6. Wilson, G. R. (2019). Advancements in Centrifugal Casting Technology for the Production of Large-Scale Industrial Components. Industrial Engineering & Management Systems, 18(4), 452-463.
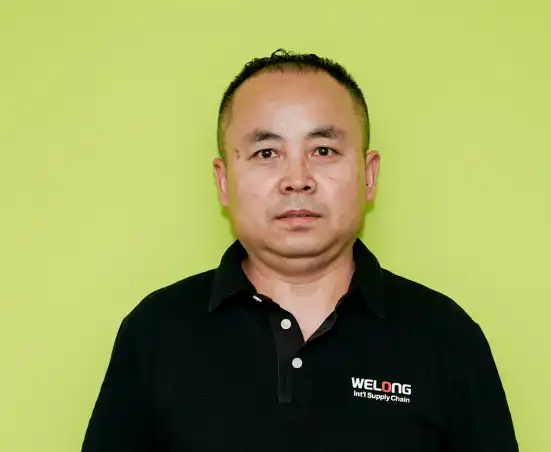
Share your inquiry, get the quotation accordingly!
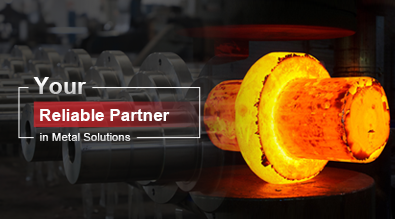
China WELONG- Your Reliable Partner in Metal Solutions