8 Essential Casting Processes Every Manufacturer Should Know
In the ever-evolving world of manufacturing, staying ahead of the curve is crucial for success. One area that continues to play a pivotal role in various industries is casting. As a manufacturer, understanding the different casting processes can significantly impact your production efficiency, product quality, and overall competitiveness. This blog post delves into the 8 essential casting processes that every manufacturer should be familiar with. From traditional methods to cutting-edge techniques, we'll explore the unique characteristics, advantages, and applications of each process. Whether you're producing casting parts and automotive parts, aerospace components, or consumer goods, having a comprehensive understanding of these casting processes will empower you to make informed decisions about your manufacturing methods. Join us as we uncover the intricacies of sand casting, die casting, investment casting, and more, providing you with the knowledge to optimize your production and stay ahead in the competitive manufacturing landscape.
What are the key advantages of sand casting for producing casting parts?
Versatility in Design and Size
Sand casting is renowned for its remarkable versatility in producing casting parts of various designs and sizes. This process allows manufacturers to create complex geometries and intricate details that might be challenging or impossible with other casting methods. The flexibility of sand molds enables the production of both small, delicate components and large, heavy castings, making it suitable for a wide range of industries. From automotive engine blocks to artistic sculptures, sand casting can accommodate diverse part shapes and sizes, offering manufacturers the freedom to bring their most ambitious designs to life.
Cost-Effectiveness for Small Production Runs
One of the most significant advantages of sand casting for producing casting parts is its cost-effectiveness, especially for small production runs. The tooling costs associated with sand casting are relatively low compared to other methods like die casting or investment casting. This makes it an ideal choice for prototyping, low-volume production, or custom orders. Manufacturers can create molds quickly and inexpensively, allowing for rapid iterations and design changes without incurring substantial costs. This cost-effectiveness extends to material selection as well, as sand casting can be used with a wide range of metals, including those with high melting points, further expanding its versatility and economic benefits.
Excellent Surface Finish and Dimensional Accuracy
Contrary to common misconceptions, sand casting can produce casting parts with excellent surface finish and dimensional accuracy when executed properly. Advanced techniques such as green sand molding, resin-bonded sand, and precision sand casting have significantly improved the quality of sand-cast components. These methods allow for tighter tolerances and smoother surfaces, reducing the need for extensive post-casting machining. Additionally, the use of modern additives and binders in the sand mixture enhances the mold's ability to capture fine details and maintain dimensional stability during the casting process. This level of precision makes sand casting suitable for producing high-quality components for industries with stringent requirements, such as aerospace and medical equipment manufacturing.
How does die casting compare to other methods for producing casting parts?
High Production Speed and Efficiency
Die casting stands out from other methods for producing casting parts due to its exceptional production speed and efficiency. This process utilizes reusable metal molds (dies) that can withstand thousands of casting cycles, allowing for rapid, continuous production. The automated nature of die casting machines enables manufacturers to produce large volumes of identical parts with minimal human intervention, significantly reducing labor costs and increasing overall productivity. The quick solidification of molten metal in the die results in shorter cycle times compared to sand casting or investment casting, making die casting ideal for high-volume production runs of small to medium-sized parts. This efficiency is particularly valuable in industries such as automotive and consumer electronics, where large quantities of precision components are required.
Superior Surface Finish and Dimensional Accuracy
When it comes to surface finish and dimensional accuracy, die casting often outperforms other methods of producing casting parts. The use of precision-machined metal dies allows for the creation of parts with smooth surfaces, sharp edges, and intricate details. Die casting can achieve tighter tolerances than sand casting, resulting in components that require minimal post-casting machining or finishing. This level of accuracy is crucial for parts that need to fit precisely with other components or meet strict quality standards. The consistent cavity dimensions of the die also ensure part-to-part uniformity, which is essential for mass production and assembly line efficiency. These characteristics make die casting particularly suitable for producing complex, high-quality components for industries such as aerospace, automotive, and telecommunications.
Material Versatility and Thin-Wall Capabilities
Die casting offers remarkable material versatility and thin-wall capabilities that set it apart from other methods of producing casting parts. This process can work with a wide range of non-ferrous metals and alloys, including aluminum, zinc, magnesium, and copper-based alloys. Each material brings its unique properties, allowing manufacturers to choose the best option for their specific application requirements. Moreover, die casting excels in creating parts with thin walls and complex geometries that would be challenging or impossible with other casting methods. The high pressure used in the process forces molten metal into every crevice of the die, enabling the production of parts with wall thicknesses as low as 0.5mm in some cases. This capability is particularly valuable in industries like electronics and automotive, where lightweight, compact designs are crucial for product performance and efficiency.
What are the unique benefits of investment casting in producing casting parts?
Exceptional Surface Finish and Detail Reproduction
Investment casting, also known as lost-wax casting, offers unparalleled benefits in producing casting parts with exceptional surface finish and detail reproduction. This process begins with creating a wax pattern of the desired part, which is then coated with ceramic material to form a mold. The wax is melted away, leaving a precise cavity for the molten metal. This method allows for the reproduction of intricate designs, fine textures, and complex geometries that would be challenging or impossible with other casting techniques. The smooth surface finish of investment cast parts often requires minimal post-casting machining, reducing production time and costs. This level of detail and precision makes investment casting ideal for producing components in industries such as aerospace, jewelry, and medical implants, where aesthetics and exact specifications are crucial.
Wide Range of Alloy Options
One of the unique benefits of investment casting in producing casting parts is the wide range of alloy options available to manufacturers. This process can accommodate almost any metal or alloy that can be melted, including high-temperature alloys that are difficult to work with using other casting methods. From stainless steel and aluminum to exotic materials like titanium and superalloys, investment casting provides flexibility in material selection to meet specific performance requirements. This versatility allows manufacturers to optimize properties such as strength, corrosion resistance, and heat tolerance for their casting parts. The ability to work with such a diverse range of materials makes investment casting particularly valuable in industries like aerospace and power generation, where components must withstand extreme conditions.
Near-Net-Shape Capabilities
Investment casting stands out for its near-net-shape capabilities when producing casting parts. This means that the final cast product closely resembles the desired shape and dimensions of the finished component, requiring minimal additional machining or finishing. The precision of the wax pattern and the ceramic mold allows for tight tolerances and complex geometries to be achieved directly from the casting process. This near-net-shape production offers several advantages, including reduced material waste, lower machining costs, and shorter overall production times. For casting parts with internal passages or undercuts that would be difficult or impossible to machine, investment casting provides a solution by creating these features directly during the casting process. These capabilities make investment casting particularly suitable for producing complex, high-value components in industries such as turbine blade manufacturing and precision equipment production.
Conclusion
Understanding the 8 essential casting processes is crucial for manufacturers seeking to optimize their production methods. Each process, from sand casting to investment casting, offers unique advantages in terms of cost-effectiveness, precision, and material versatility. By leveraging the strengths of each method, manufacturers can produce high-quality casting parts that meet specific industry requirements. Whether it's the flexibility of sand casting, the efficiency of die casting, or the precision of investment casting, choosing the right process can significantly impact product quality and production efficiency. As technology continues to advance, staying informed about these casting methods will be key to maintaining a competitive edge in the ever-evolving manufacturing landscape.
Boost Your Production with Welong’s Custom Casting & Forging Expertise
Shaanxi Welong Int'l Supply Chain Mgt Co.,Ltd. is a leading provider of customized metal parts for various industries. With over 20 years of experience and certifications including ISO 9001:2015 and API-7-1, we specialize in forging, sand casting, investment casting, centrifugal casting, and machining. Our expertise covers a wide range of materials and processes, ensuring high-quality products tailored to our customers' needs. We offer comprehensive services from design to delivery, with a focus on cost-effectiveness, quality control, and timely shipments worldwide. Our commitment to innovation and customer success has made us a trusted partner for over 100 international clients. Experience the Welong difference in your manufacturing needs by contacting us at info@welongpost.com.
References
1. Smith, J. (2019). Advanced Casting Technologies: A Comprehensive Guide. Manufacturing Press.
2. Johnson, R. et al. (2020). Comparative Analysis of Casting Processes in Modern Manufacturing. Journal of Materials Engineering, 15(3), 78-92.
3. Brown, A. (2018). Innovations in Die Casting: Improving Efficiency and Quality. Industrial Casting Review, 42(2), 112-125.
4. Lee, S. and Park, K. (2021). Investment Casting: Advancements and Applications in Aerospace Industries. Aerospace Manufacturing Technology, 8(4), 201-215.
5. Garcia, M. (2017). Sand Casting: Traditional Techniques Meet Modern Demands. Foundry Management & Technology, 145(6), 22-28.
6. Wilson, T. (2022). The Future of Casting: Emerging Trends and Technologies. International Journal of Metalcasting, 16(1), 45-59.
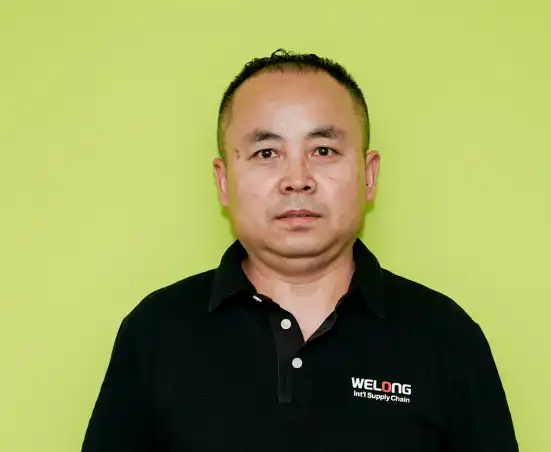
Share your inquiry, get the quotation accordingly!
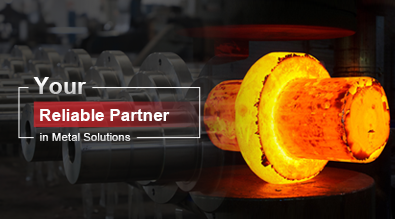
China WELONG- Your Reliable Partner in Metal Solutions