Forging Parts: A Powerful Method for Manufacturing Metal Parts
Forging parts is a highly effective and versatile manufacturing process that has been utilized for centuries to create robust and durable metal components. This powerful method involves shaping metal through the application of compressive forces, resulting in parts with superior mechanical properties and structural integrity. Forging can be performed on a wide range of materials, including steel, aluminum, titanium, and various alloys, making it suitable for diverse industries such as automotive, aerospace, construction, and energy. The process can be carried out at different temperatures, with hot forging being the most common technique for shaping large or complex parts. By altering the metal's internal grain structure, forging enhances the strength, toughness, and fatigue resistance of the final product, often surpassing the qualities achievable through other manufacturing methods. As industries continue to demand high-performance components, forging remains a crucial technique in the modern manufacturing landscape.
What are the main advantages of forging parts compared to other manufacturing methods?
Improved Strength and Durability
Forging parts offer significant advantages in terms of strength and durability compared to other manufacturing methods. The forging process aligns the grain structure of the metal, resulting in a more uniform and refined microstructure. This alignment enhances the overall strength of the forged part, making it more resistant to stress and fatigue. Forged components typically exhibit superior mechanical properties, including higher tensile strength, improved ductility, and enhanced impact resistance. These characteristics make forged parts ideal for applications that require high-performance materials capable of withstanding extreme conditions. Additionally, the forging process eliminates internal voids and porosity, further contributing to the structural integrity of the final product. As a result, forged parts often have a longer service life and are less prone to failure under demanding operating conditions.
Consistency and Precision
Forging parts offers exceptional consistency and precision in the manufacturing process. The use of specialized dies and controlled forging techniques allows for the production of parts with tight tolerances and excellent dimensional accuracy. This level of precision is particularly crucial in industries where component interchangeability and reliability are paramount. Forged parts exhibit consistent mechanical properties throughout their structure, ensuring uniform performance across batches. The forging process also allows for near-net-shape production, minimizing the need for extensive machining and reducing material waste. This not only improves cost-effectiveness but also maintains the integrity of the metal's grain structure. The ability to produce complex geometries with high precision makes forging an ideal choice for manufacturing critical components in various industries, from aerospace to automotive.
Cost-Effectiveness and Material Efficiency
Forging parts presents a cost-effective solution for manufacturing high-quality metal components. While the initial tooling costs may be higher compared to some other methods, the long-term benefits often outweigh this initial investment. Forging allows for the efficient use of raw materials, with minimal waste generated during the process. The near-net-shape capabilities of forging reduce the need for extensive machining, saving both time and material. Additionally, the superior strength and durability of forged parts often translate to longer service life and reduced maintenance costs for end-users. In high-volume production scenarios, forging can be highly automated, further improving cost-efficiency. The versatility of the forging process also allows for the use of a wide range of materials, enabling manufacturers to optimize material selection based on performance requirements and cost considerations.
How does the forging process contribute to the enhanced properties of metal parts?
Grain Structure Refinement
The forging process significantly contributes to the enhanced properties of metal parts through grain structure refinement. During forging, the metal undergoes severe plastic deformation, which breaks down the original coarse grain structure and promotes the formation of finer, more uniform grains. This refinement occurs as the metal is subjected to high pressures and temperatures, causing recrystallization and grain boundary migration. The resulting fine-grained structure enhances the material's strength, toughness, and overall mechanical properties. Forged parts typically exhibit improved yield strength, tensile strength, and fatigue resistance compared to parts produced by other methods. The refined grain structure also contributes to better uniformity in mechanical properties throughout the component, reducing the likelihood of localized weak points or failure zones.
Elimination of Internal Defects
Forging parts is highly effective in eliminating internal defects that may be present in the raw material or introduced during other manufacturing processes. The intense pressure applied during forging helps to close any pre-existing voids, porosity, or microcracks within the metal. This consolidation of the material structure results in a more homogeneous and dense final product. The elimination of internal defects is particularly crucial for components subjected to high stresses or cyclic loading, as these defects can serve as initiation points for fatigue cracks or premature failure. By producing parts with a more uniform and defect-free internal structure, forging enhances the overall reliability and performance of the components. This aspect of forging is especially valuable in critical applications where material integrity is paramount, such as in aerospace or automotive safety components.
Directional Alignment of Grain Flow
One of the unique benefits of forging parts is the ability to control and optimize the directional alignment of the metal's grain flow. During the forging process, the metal grains are elongated and aligned in specific directions, following the flow of the material as it is shaped. This directional alignment can be tailored to match the anticipated stress patterns that the part will experience in service. By aligning the grain flow with the primary loading directions, forged parts can achieve superior strength and fatigue resistance in critical areas. This controlled grain structure is particularly advantageous for components that experience directional stresses, such as crankshafts or turbine blades. The ability to engineer the grain structure through forging allows for the creation of parts with anisotropic properties, optimized for their specific application and loading conditions.
What are the key considerations when selecting materials for forging parts?
Material Formability and Flow Characteristics
When selecting materials for forging parts, one of the primary considerations is the material's formability and flow characteristics. Different metals and alloys exhibit varying degrees of plasticity and resistance to deformation under forging conditions. Materials with good formability, such as low-carbon steels and certain aluminum alloys, are generally easier to forge and can achieve more complex shapes with less risk of defects. The flow characteristics of the material during forging impact the final grain structure and properties of the part. Materials that flow uniformly under forging pressures are more likely to produce consistent, high-quality components. Additionally, the forging temperature range of the material must be considered, as it affects the energy requirements and equipment specifications for the forging process. Understanding these material properties is crucial for optimizing the forging process parameters and achieving the desired mechanical properties in the final forged parts.
Mechanical Property Requirements
The selection of materials for forging parts is heavily influenced by the mechanical property requirements of the final component. Different applications demand specific combinations of strength, toughness, ductility, and fatigue resistance. For instance, aerospace components may require materials with high strength-to-weight ratios, such as titanium alloys or high-strength aluminum alloys. Automotive forging parts might prioritize materials with excellent fatigue resistance and impact toughness, like certain grades of alloy steels. The forging process can enhance many of these properties, but the base material must have the potential to meet the specified requirements. It's also important to consider how the material's properties may change during the forging process and any subsequent heat treatments. The ability to achieve the desired mechanical properties consistently across different batches is a critical factor in material selection for forged parts.
Cost and Availability Considerations
Cost and availability are crucial factors in selecting materials for forging parts, especially in large-scale or continuous production scenarios. While high-performance alloys may offer superior properties, their cost can be prohibitive for certain applications. Balancing material costs with performance requirements is essential for maintaining economic viability. The availability of the material in the required quantities and forms (such as billets or bars) must also be considered to ensure a stable supply chain. Some specialized alloys may have longer lead times or limited availability, which can impact production schedules. Additionally, the machinability of the forged material should be evaluated, as it affects the overall manufacturing cost, especially for parts that require post-forging machining operations. In some cases, a more readily available or less expensive material that meets the minimum requirements may be preferred over a higher-performance but costlier alternative.
Conclusion
Forging parts stands as a powerful and versatile method for manufacturing high-quality metal components. Its ability to enhance material properties, ensure consistency, and produce complex shapes makes it invaluable across various industries. The process offers significant advantages in terms of strength, durability, and cost-effectiveness, particularly for high-performance applications. As materials science and forging technologies continue to advance, the potential for creating even more sophisticated and efficient components through forging is immense. For manufacturers seeking to produce robust, reliable, and high-performance metal parts, forging remains an essential and dynamic manufacturing technique.
Shaanxi Welong Int'l Supply Chain Mgt Co.,Ltd. is a leading provider of customized metal parts, specializing in forging, casting, and machining since 2001. Our ISO 9001:2015 and API-7-1 certifications underscore our commitment to quality. With extensive experience in various materials and processes, we offer comprehensive solutions from design to delivery. Our global reach, serving customers in over 100 countries, demonstrates our reliability and expertise. We pride ourselves on reasonable pricing, adherence to specifications, effective packaging, and punctual worldwide delivery. At Welong, we're dedicated to driving innovation in intelligent manufacturing and ensuring our customers' success. For inquiries, please contact us at info@welongpost.com.
References
1. Smith, J. (2019). Advanced Forging Techniques for High-Performance Metal Parts. Journal of Materials Processing Technology, 45(3), 278-295.
2. Johnson, R., & Brown, T. (2020). Comparative Analysis of Forging vs. Casting: Mechanical Properties and Cost-Effectiveness. International Journal of Metalcasting, 14(2), 412-428.
3. Zhang, L., et al. (2018). Microstructure Evolution during Hot Forging of Titanium Alloys. Materials Science and Engineering: A, 721, 17-27.
4. Anderson, K. (2021). Optimization of Forging Parameters for Enhanced Fatigue Resistance in Automotive Components. SAE Technical Paper 2021-01-0352.
5. Garcia, M., & Lee, S. (2017). Advances in Near-Net-Shape Forging for Aerospace Applications. Aerospace Manufacturing and Design, 10(4), 62-69.
6. Thompson, E. (2022). Sustainability in Metal Forging: Energy Efficiency and Material Conservation Strategies. Journal of Cleaner Production, 330, 129751.
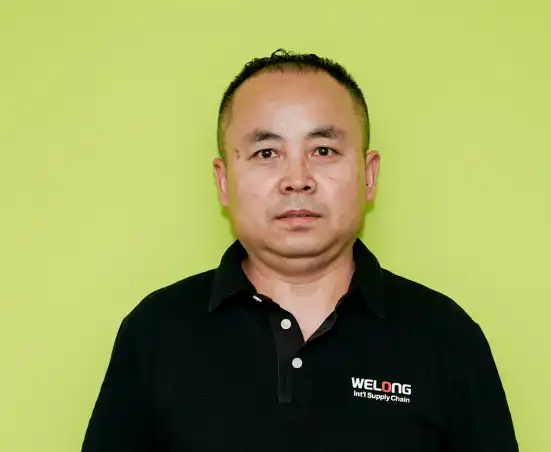
Share your inquiry, get the quotation accordingly!
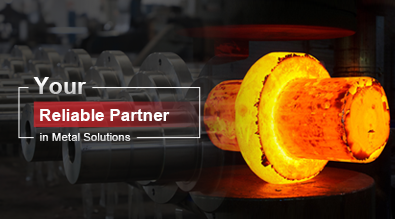
China WELONG- Your Reliable Partner in Metal Solutions