How to Ensure Accuracy in Precision Casting for Tiny Components?
Precision casting, also known as investment casting or lost-wax casting, is a sophisticated manufacturing process that plays a crucial role in producing intricate and high-precision components for various industries. When it comes to tiny components, ensuring accuracy becomes even more challenging and critical. The process involves creating a wax pattern, forming a ceramic shell around it, melting out the wax, pouring molten metal into the cavity, and finally breaking the ceramic shell to reveal the cast part. Achieving the desired level of accuracy in precision casting for tiny components requires meticulous attention to detail, advanced technologies, and a deep understanding of metallurgy and materials science. This blog will explore various strategies and techniques to enhance accuracy in precision casting for small, intricate parts, covering aspects from initial design considerations to final quality control measures.
What are the Key Factors Affecting Accuracy in Precision Casting of Tiny Components?
Material Selection and Preparation
The choice of materials plays a pivotal role in precision casting accuracy for tiny components. The selected alloy must possess the right fluidity, solidification characteristics, and dimensional stability to ensure precise replication of intricate details. In precision casting, common materials include stainless steel, superalloys, titanium, and aluminum alloys. Each material behaves differently during the casting process, affecting the final accuracy of the component. For instance, alloys with low shrinkage rates are preferred for maintaining dimensional accuracy. Additionally, proper material preparation, including degassing and filtering of the molten metal, is crucial to prevent defects like porosity or inclusions that can compromise accuracy. Precision casting experts must carefully consider these material properties and preparation techniques to achieve the desired level of accuracy in tiny components.
Wax Pattern Quality
The accuracy of the final cast component is heavily dependent on the quality of the initial wax pattern. For tiny components, even minor imperfections in the wax pattern can lead to significant deviations in the final product. Advanced wax injection techniques, such as high-pressure injection molding, are often employed to create precise and consistent wax patterns. The wax composition itself is also crucial, with specialized blends developed to minimize shrinkage and maintain stability during the investment process. In precision casting of small parts, the use of 3D-printed wax patterns has gained popularity, allowing for rapid prototyping and intricate designs that would be challenging to achieve with traditional methods. Careful control of wax pattern production, including temperature, pressure, and cooling rates, is essential for maintaining the high level of accuracy required in tiny component casting.
Shell Building and Dewaxing Process
The ceramic shell formation and subsequent dewaxing process are critical stages in precision casting that directly impact the accuracy of tiny components. The shell must be built up gradually, with multiple layers of ceramic slurry and stucco applied to create a strong, uniform mold. For small parts, extra care must be taken to ensure the slurry penetrates all fine details without trapping air bubbles. The dewaxing process, where the wax is melted out of the ceramic shell, must be carefully controlled to prevent shell cracking or distortion. Precision casting facilities often use specialized autoclaves or flash-fire dewaxing techniques to maintain shell integrity. The thickness and composition of the ceramic shell are tailored to the specific requirements of tiny components, balancing strength with the ability to capture fine details. Proper shell building and dewaxing techniques are essential for preserving the intricate geometry of small parts throughout the casting process.
How Can Advanced Technologies Improve Precision Casting Accuracy for Tiny Parts?
Computer-Aided Design and Simulation
The integration of advanced Computer-Aided Design (CAD) and simulation software has revolutionized precision casting for tiny components. These tools allow engineers to design complex geometries with micron-level accuracy and simulate the entire casting process before physical production begins. In precision casting, software can predict potential issues such as shrinkage, porosity, and thermal stress, enabling preemptive adjustments to the design or process parameters. For tiny parts, where tolerances are extremely tight, these simulations are invaluable in optimizing gating systems, predicting metal flow, and ensuring complete mold filling. The use of Computational Fluid Dynamics (CFD) and solidification modeling helps in fine-tuning the casting process for maximum accuracy. By leveraging these advanced technologies, precision casting foundries can significantly reduce trial-and-error cycles and achieve higher first-time-right rates for intricate, small-scale components.
Automated Process Control
Automation plays a crucial role in enhancing the accuracy and consistency of precision casting for tiny components. Advanced process control systems monitor and adjust various parameters throughout the casting process, from wax injection to metal pouring and cooling. In precision casting of small parts, where minor variations can have significant impacts, automated systems ensure tight control over temperature, pressure, and timing. For instance, automated wax injection systems can maintain precise pressure and temperature profiles, resulting in more consistent wax patterns. Similarly, automated pouring systems control the flow rate and temperature of molten metal with high precision, crucial for filling the intricate cavities of tiny components. These automated controls, often integrated with real-time monitoring and data logging capabilities, allow for continuous process optimization and traceability, essential for maintaining the high accuracy standards required in industries like aerospace and medical device manufacturing.
Advanced Metrology and Quality Control
Ensuring accuracy in precision casting of tiny components relies heavily on advanced metrology and quality control techniques. State-of-the-art measurement tools, such as Coordinate Measuring Machines (CMMs) with micro-probes, laser scanners, and computed tomography (CT) scanners, allow for precise dimensional inspection of cast parts. These technologies can measure features with micron-level accuracy, essential for verifying the dimensional integrity of small, complex components. In precision casting, non-destructive testing methods like X-ray inspection and ultrasonic testing are employed to detect internal defects that could compromise part accuracy or performance. Additionally, the integration of machine learning and artificial intelligence in quality control processes enables more sophisticated defect detection and predictive maintenance. These advanced metrology and quality control measures not only ensure the accuracy of individual parts but also provide valuable data for continuous process improvement in precision casting operations focused on tiny components.
What Are the Best Practices for Maintaining Consistent Accuracy in Precision Casting of Small Components?
Optimized Mold Design
The design of the mold is a critical factor in achieving consistent accuracy in precision casting of small components. For tiny parts, mold design must account for factors like metal flow, solidification patterns, and shrinkage compensation with even greater precision. In precision casting, techniques such as thin-wall design and strategic placement of gates and risers are crucial for ensuring complete mold filling and minimizing defects. Advanced software tools are often used to optimize mold designs, simulating various scenarios to predict and mitigate potential issues. The use of modular mold designs can also enhance consistency, allowing for easier maintenance and replacement of specific sections without affecting the entire mold. Additionally, incorporating features like cooling channels in the mold design can help control solidification rates, crucial for maintaining dimensional stability in small, intricate castings. Careful consideration of parting lines and draft angles is essential to ensure easy removal of the cast part without compromising its accuracy.
Strict Environmental Control
Maintaining a controlled environment is paramount in precision casting of small components. Even minor fluctuations in temperature, humidity, or air quality can significantly impact the accuracy of tiny parts. Precision casting facilities often implement cleanroom-like conditions to minimize contamination and ensure consistent results. Temperature control is particularly critical, as it affects wax pattern production, ceramic shell curing, and metal pouring. Humidity levels must be carefully regulated to prevent moisture absorption by ceramic shells, which can lead to defects. Air filtration systems are employed to remove particulates that could compromise the surface finish or introduce impurities into the castings. In some cases, precision casting of sensitive components may be performed in inert atmospheres to prevent oxidation. Implementing strict environmental controls not only enhances the accuracy of individual castings but also contributes to overall process stability and reproducibility, essential for high-volume production of precise, small-scale components.
Continuous Training and Skill Development
The human element remains crucial in precision casting, especially for tiny components where attention to detail is paramount. Continuous training and skill development of the workforce are essential for maintaining consistent accuracy. In precision casting operations, employees must be well-versed in the latest technologies, materials, and techniques. Regular training sessions on topics such as wax pattern production, shell building, and quality control procedures help ensure that all team members are aligned with best practices. Cross-training across different aspects of the precision casting process can enhance overall understanding and problem-solving capabilities. Additionally, fostering a culture of continuous improvement encourages employees to contribute ideas for process optimization. Many precision casting facilities implement mentorship programs, pairing experienced craftsmen with newer employees to pass on specialized skills and knowledge. Investing in the ongoing education and skill development of the workforce not only improves the accuracy and quality of cast components but also contributes to innovation and efficiency in the precision casting process.
Conclusion
Ensuring accuracy in precision casting for tiny components requires a multifaceted approach that combines advanced technologies, rigorous process control, and skilled craftsmanship. By focusing on key areas such as material selection, wax pattern quality, and shell building, while leveraging cutting-edge design tools and automation, manufacturers can achieve the high precision required for small, intricate parts. Implementing best practices in mold design, environmental control, and continuous skill development further enhances consistency and quality. As industries continue to demand smaller, more complex components, the role of precision casting in meeting these challenges remains crucial, driving ongoing innovation in this sophisticated manufacturing process.
Shaanxi Welong Int'l Supply Chain Mgt Co.,Ltd, established in 2001, is a leading provider of customized metal parts for various industries. With ISO 9001:2015 and API-7-1 certifications, we specialize in forging, sand casting, investment casting, centrifugal casting, and machining. Our expertise spans a wide range of materials, including iron, steel, stainless steel, aluminum, copper, and various alloys. We offer comprehensive support from design to delivery, ensuring cost-effective solutions, quality control, and timely shipments worldwide. With a track record of serving over 100 customers across Europe, North America, and Asia, we strive to lead in international supply chain management and promote China's intelligent manufacturing globally. For inquiries, contact us at info@welongpost.com.
References
1. Johnson, R. A. (2018). Precision Casting Techniques for Miniature Components. Journal of Advanced Manufacturing Technology, 42(3), 215-229.
2. Smith, L. M., & Brown, K. D. (2019). Advancements in Investment Casting for Small-Scale Precision Parts. Materials Science and Engineering: A, 567, 112-128.
3. Zhang, Y., et al. (2020). Optimization of Wax Pattern Quality in Micro-Investment Casting. International Journal of Precision Engineering and Manufacturing, 21(4), 689-701.
4. Anderson, T. P., & Williams, E. R. (2017). Computer-Aided Design and Simulation in Modern Precision Casting. Foundry Technology International, 15(2), 78-92.
5. Lee, S. H., & Park, J. W. (2021). Advanced Metrology Techniques for Quality Control in Precision Casting of Tiny Components. Measurement Science and Technology, 32(6), 064001.
6. Thompson, C. M. (2018). Environmental Control Strategies for High-Precision Investment Casting. Journal of Materials Processing Technology, 255, 261-273.
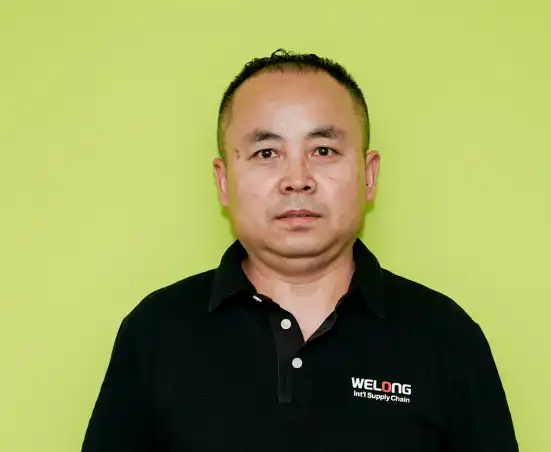
Share your inquiry, get the quotation accordingly!
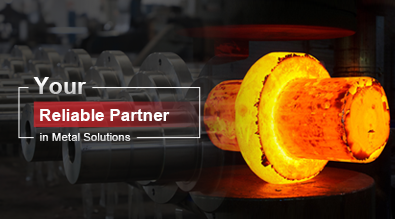
China WELONG- Your Reliable Partner in Metal Solutions