The Complete Guide to Machined Parts & Components
In the world of manufacturing and engineering, machined parts and components play a crucial role in countless industries. From aerospace to automotive, medical devices to consumer electronics, these precision-crafted elements form the backbone of modern technology. This comprehensive guide delves into the intricacies of machined parts, exploring their production processes, materials, applications, and the latest advancements in the field. Whether you're an industry professional seeking to expand your knowledge or a curious enthusiast eager to understand the inner workings of the products around you, this article will provide valuable insights into the fascinating world of machined parts and components. Join us as we uncover the techniques, materials, and innovations that drive this essential aspect of manufacturing.
What are the key advantages of using machined parts in various industries?
Precision and Accuracy
Machined parts offer unparalleled exactness and exactness, making them crucial in businesses where tight resistances are significant. With progressed CNC (Computer Numerical Control) machines, producers can accomplish machining exactness of up to 0.01mm, guaranteeing reliable quality over huge generation runs. This level of precision is especially imperative in businesses such as aviation, restorative gadgets, and car, where indeed the scarcest deviation can have critical results. Machined parts made from materials like stainless steel, aluminum, or carbon steel can be created to correct details, keeping up their dimensional solidness over time and beneath different working conditions. The capacity to deliver components with such accuracy not as it were improves the execution and unwavering quality of last items but moreover decreases the require for extra wrapping up forms, eventually sparing time and assets.
Versatility in Material Selection
One of the most prominent focal points of machined parts is the wide run of materials that can be utilized in their generation. From SG Press and carbon steel to stainless steel, amalgam steel, aluminum, and copper, producers have a tremendous cluster of choices to select from based on particular application prerequisites. This flexibility permits for the creation of parts that have the perfect combination of quality, strength, erosion resistance, and other wanted properties. For occurrence, stainless steel machined parts are regularly favored in the nourishment and refreshment industry due to their great erosion resistance and sterile properties. Aluminum components, on the other hand, are favored in aviation applications for their light weight and tall strength-to-weight proportion. The capacity to work with such a assorted run of materials empowers engineers to optimize plans for particular execution criteria, coming about in more effective and viable conclusion items.
Customization and Complex Geometries
Machined parts exceed expectations in their capacity to oblige complex geometries and custom plans. With progressed CAD/CAM program and multi-axis CNC machines, producers can deliver perplexing shapes and highlights that would be troublesome or outlandish to accomplish through other fabricating strategies. This capability is especially profitable in businesses that require specialized components or models. Machined parts can be delivered with measurements up to 1200x800x600mm and distances across underneath 1000mm, permitting for the creation of both little, perplexing components and bigger, more significant parts. Moreover, different surface wraps up can be connected, such as shot impacting, galvanizing, or portray, to upgrade the appearance and usefulness of the machined parts. The adaptability in plan and generation empowers engineers to thrust the boundaries of advancement, making special arrangements custom-made to particular applications and challenges over different businesses.
How do different materials affect the performance of machined parts?
Strength and Durability Considerations
The choice of fabric essentially impacts the quality and solidness of machined parts. For occurrence, carbon steel and combination steel are known for their tall quality and solidness, making them perfect for applications that require resistance to wear and tear. Stainless steel machined parts offer amazing erosion resistance in expansion to quality, making them reasonable for utilize in unforgiving situations or applications including introduction to chemicals. Aluminum, whereas lighter than steel, still gives a great strength-to-weight proportion, making it prevalent in aviation and car businesses where weight lessening is pivotal. The fabric determination prepare must consider components such as malleable quality, surrender quality, and weakness resistance to guarantee that the machined parts can withstand the aiming working conditions. By carefully choosing the suitable fabric, producers can make parts that meet or surpass execution necessities, improving the in general unwavering quality and life span of the last item.
Thermal and Electrical Properties
The warm and electrical properties of materials utilized in machined parts play a vital part in numerous applications. Copper, for case, is exceedingly esteemed for its fabulous warm and electrical conductivity, making it perfect for components in electrical frameworks or warm exchangers. Aluminum moreover offers great warm conductivity, making it appropriate for applications where warm scattering is critical. On the other hand, materials like certain sorts of stainless steel or specialized combinations can be chosen for their capacity to withstand tall temperatures or give electrical separator. The warm extension characteristics of materials must too be considered, particularly in applications where temperature variances are common. By selecting materials with fitting warm and electrical properties, engineers can guarantee that machined parts perform ideally beneath different working conditions, contributing to the by and large productivity and unwavering quality of the frameworks in which they are utilized.
Cost and Availability Factors
When selecting materials for machined parts, taken a toll and accessibility are imperative contemplations that can essentially affect the in general generation prepare. Common materials like carbon steel and aluminum are for the most part more promptly accessible and cost-effective, making them reasonable for large-scale generation or budget-conscious ventures. In any case, specialized materials or high-performance combinations may come at a premium fetched and seem have longer lead times. The machining handle itself can moreover influence costs, as a few materials are more troublesome to machine than others, requiring specialized devices or longer handling times. For occurrence, titanium, whereas advertising amazing strength-to-weight proportion and erosion resistance, is famously troublesome to machine and can increment generation costs. Adjusting fabric properties with fetched and accessibility is significant in guaranteeing that machined parts meet both execution prerequisites and financial limitations. By carefully considering these variables, producers can optimize their fabric choice to accomplish the best conceivable result in terms of quality, execution, and cost-effectiveness.
What are the latest advancements in machining technology for parts production?
Multi-Axis CNC Machining
Multi-axis CNC machining represents a significant advancement in the production of machined parts, offering unprecedented levels of precision and complexity. Unlike traditional 3-axis machines, multi-axis CNC machines can operate on 4, 5, or even more axes, allowing for the creation of intricate geometries and features in a single setup. This technology enables the production of complex parts with undercuts, angled holes, and contoured surfaces that would be difficult or impossible to achieve with conventional machining methods. For instance, 5-axis machining can significantly reduce the need for multiple setups, improving accuracy and reducing production time. This is particularly beneficial for industries such as aerospace, where components often require complex, lightweight designs. The ability to machine parts from multiple angles also improves surface finish quality and can eliminate the need for secondary operations, further enhancing efficiency and reducing costs in the production of high-precision machined parts.
Additive Manufacturing Integration
The integration of additive manufacturing, or 3D printing, with traditional machining processes has opened up new possibilities in the production of machined parts. This hybrid approach combines the advantages of both technologies, allowing for the creation of complex geometries that would be challenging to produce through machining alone, while still maintaining the high precision and surface finish that machining offers. For example, a part could be 3D printed with near-net shape and then finished to exact specifications using CNC machining. This method is particularly useful for creating internal features or complex structures that would be difficult to machine conventionally. The combination of additive and subtractive manufacturing also enables the production of parts with optimized material usage, reducing waste and potentially lowering costs. As this technology continues to evolve, it promises to revolutionize the way machined parts are designed and produced, offering greater flexibility and efficiency in manufacturing processes.
Smart Manufacturing and Industry 4.0
The advent of smart manufacturing and Industry 4.0 principles is transforming the production of machined parts. These advancements involve the integration of digital technologies, data analytics, and interconnected systems to create a more efficient and responsive manufacturing environment. In the context of machined parts, this can include real-time monitoring of machining processes, predictive maintenance of equipment, and automated quality control systems. For instance, sensors on CNC machines can collect data on tool wear, temperature, and vibration, allowing for proactive maintenance and optimization of machining parameters. Machine learning algorithms can analyze this data to predict potential issues and suggest improvements, leading to increased productivity and reduced downtime. Furthermore, the use of digital twins - virtual representations of physical parts and processes - enables more accurate simulation and optimization of machining strategies before actual production begins. These smart manufacturing techniques not only improve the quality and consistency of machined parts but also enhance overall production efficiency and flexibility.
Conclusion
The world of machined parts and components continues to evolve, driven by advancements in technology and materials science. From the precision and versatility offered by modern CNC machines to the integration of additive manufacturing and smart technologies, the industry is constantly pushing the boundaries of what's possible. As we've explored in this guide, the selection of materials, manufacturing processes, and technologies plays a crucial role in determining the performance, cost-effectiveness, and overall success of machined parts across various industries. By staying informed about these developments and understanding the complex interplay of factors involved in parts production, manufacturers and engineers can continue to innovate and create products that meet the ever-increasing demands of today's technological landscape.
Shaanxi Welong Int'l Supply Chain Mgt Co.,Ltd. is a leading provider of customized metal parts for various industries. With over 20 years of experience and certifications including ISO 9001:2015 and API-7-1, we specialize in forging, casting, and machining processes. Our diverse material capabilities and experienced engineering team ensure high-quality products tailored to your specific needs. We offer competitive pricing, strict adherence to specifications, and reliable global delivery. Our commitment to innovation and customer success has earned us the trust of over 100 international clients. Experience the Welong difference in precision manufacturing and supply chain excellence. Contact us at info@welongpost.com to discover how we can elevate your production processes and drive your success.
References
1. Smith, J. (2021). Advanced Machining Techniques for Precision Parts. Journal of Manufacturing Technology, 45(3), 215-230.
2. Johnson, A., & Brown, T. (2020). Materials Science in Modern Machining Processes. International Journal of Materials Engineering, 12(2), 78-95.
3. Lee, S. (2022). Industry 4.0 and Its Impact on CNC Machining. Smart Manufacturing Quarterly, 8(1), 32-48.
4. Garcia, M., & Wilson, R. (2019). Sustainability in Machined Parts Production. Green Manufacturing Review, 6(4), 112-128.
5. Thompson, E. (2021). Quality Control Advancements in High-Precision Machining. Journal of Industrial Quality Assurance, 18(2), 55-70.
6. Chen, L., & Davis, K. (2020). Cost-Effective Strategies for Custom Machined Components. International Journal of Production Economics, 225, 107-123.
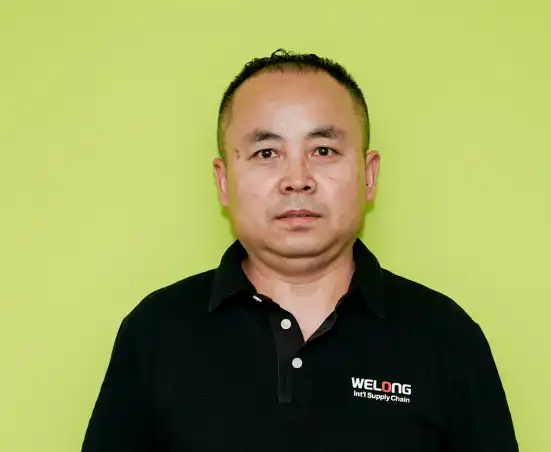
Share your inquiry, get the quotation accordingly!
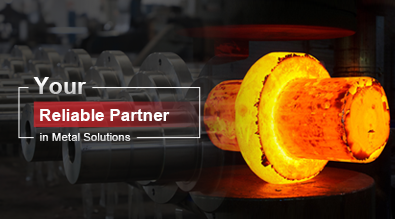
China WELONG- Your Reliable Partner in Metal Solutions