Forging - Process, Classification & Methods
Forging is a sophisticated manufacturing process that has been integral to metalworking for centuries. This technique involves shaping metal through compressive forces, typically using hammers or presses. The process can be categorized into two main types: cold forging, which occurs at room temperature, and hot forging, where the metal is heated before shaping. Both methods subject the metal to high forces, deforming it until it achieves the desired shape. Forging is widely used for various metals, including aluminum, brass, bronze, iron, and steel, to produce forging parts for critical applications. The most common forging techniques are closed die forging (also known as impression die forging), open die forging, and roll forming. Each method has its unique advantages and applications, making forging a versatile and essential process in modern manufacturing. The forging industry continues to evolve, incorporating advanced technologies and materials to meet the ever-growing demands of various sectors, from automotive to aerospace.
What are the main types of forging processes?
Closed Die Forging
Closed die forging, also known as impression die forging, is a precision forging process where the metal is compressed between two dies that contain a pre-cut profile of the desired part. This method is ideal for producing complex shapes with tight tolerances. The forging parts created through this process have excellent structural integrity and mechanical properties. Closed die forging is commonly used in the automotive and aerospace industries for components such as crankshafts, connecting rods, and turbine blades. The process can work with various materials, including carbon steel, stainless steel, and aluminum alloys. With the capability to produce parts weighing from 0.2 to 50 tons and an annual output of 50,000 tons, closed die forging is a highly efficient method for large-scale production.
Open Die Forging
Open die forging is a versatile process where the metal is compressed between flat dies or simple shapes, allowing for more freedom in the final shape of the part. This method is particularly useful for creating large, simple shapes or for pre-forming parts that will undergo further forging processes. Open die forging is commonly used for producing shafts, rings, and custom forging parts. The process can handle a wide range of materials, including carbon steel, alloy steel, and titanium. Open die forging is advantageous for its flexibility and ability to produce parts with improved grain structure and mechanical properties. It's particularly suitable for low-volume production or for creating unique, custom forging parts that may be too large or complex for closed die forging.
Roll Forging
Roll forging is a continuous forging process where the metal is passed between two rotating rolls with impressions that gradually shape the workpiece. This method is excellent for producing long, symmetrical parts with uniform cross-sections. Roll forging is commonly used in the production of axles, shafts, and other elongated forging parts. The process can work with various materials, including carbon steel, stainless steel, and aluminum alloys. Roll forging offers several advantages, including high production rates, excellent material utilization, and the ability to produce parts with improved mechanical properties due to the continuous deformation process. With the capability to handle parts weighing up to 50 tons and an annual output of 50,000 tons, roll forging is a highly efficient method for large-scale production of certain types of forging parts.
How does the forging process affect material properties?
Grain Structure Refinement
The forging process significantly affects the grain structure of the material, leading to grain refinement. As the metal is deformed under high pressure, the original grains are broken down and recrystallized into smaller, more uniformly distributed grains. This refinement in grain structure is particularly beneficial for forging parts as it enhances their mechanical properties. Finer grains result in increased strength, improved ductility, and better fatigue resistance. For instance, forged steel components often exhibit superior strength and toughness compared to their cast or machined counterparts. The degree of grain refinement can be controlled by factors such as forging temperature, strain rate, and the amount of deformation, allowing manufacturers to tailor the material properties to specific applications.
Directional Strength
Forging imparts directional strength to the material, a phenomenon known as grain flow. During the forging process, the metal grains align themselves in the direction of material flow, creating a fibrous structure. This alignment of grains results in anisotropic properties, where the strength and toughness of the forging parts are greater in the direction of the grain flow. This directional strength is particularly advantageous in applications where the component is subjected to specific loading directions. For example, in the case of forged crankshafts, the grain flow can be oriented to provide maximum strength in the areas that experience the highest stress during operation. The ability to control grain flow through proper die design and forging techniques allows manufacturers to optimize the performance of forging parts for their intended applications.
Elimination of Internal Defects
One of the significant advantages of the forging process is its ability to eliminate or reduce internal defects in the material. The high pressures involved in forging help to close any internal voids or porosity that may be present in the initial material. This consolidation of the material structure results in forging parts with improved density and more uniform properties throughout their cross-section. The elimination of internal defects is particularly crucial for components used in critical applications, such as aerospace or automotive industries, where material integrity is paramount. Furthermore, the forging process can help break down and disperse any inclusions or impurities in the material, leading to a more homogeneous structure. This improvement in material integrity translates to enhanced reliability and longer service life for forging parts, making them ideal for demanding applications.
What are the key considerations in selecting a forging method?
Material Selection
Material selection is a crucial consideration in choosing the appropriate forging method. Different materials exhibit varying forgeability and respond differently to forging processes. For instance, carbon steel and alloy steel are widely used in forging due to their excellent formability and the ability to achieve high strength through heat treatment post-forging. Stainless steel forging parts are preferred in applications requiring corrosion resistance. Aluminum alloys are often chosen for their lightweight properties, making them ideal for aerospace and automotive applications. The selection of material also influences the forging temperature, with some materials requiring hot forging while others can be cold forged. For example, titanium and zirconium, known for their high strength-to-weight ratio, often require specialized forging techniques due to their high forging temperatures and reactivity.
Part Geometry and Complexity
The geometry and complexity of the desired part play a significant role in determining the most suitable forging method. Simple shapes with uniform cross-sections might be efficiently produced using open die forging or roll forging. However, more complex geometries with intricate details often require closed die forging. The size of the part is also a crucial factor, with some forging methods capable of producing parts ranging from 0.2 to 50 tons. The tolerance requirements of the forging parts also influence the choice of method, with closed die forging generally offering tighter tolerances compared to open die forging. Additionally, the presence of features such as undercuts, holes, or thin sections may necessitate specific forging techniques or even a combination of forging and other manufacturing processes to achieve the desired final geometry.
Production Volume and Cost Considerations
Production volume and cost considerations are vital factors in selecting a forging method. For high-volume production, automated forging processes like closed die forging or roll forging are often more economical, especially when considering the annual output capacity of up to 50,000 tons. These methods offer faster production rates and consistency in part quality. However, the initial tooling costs for these methods can be high, making them less suitable for low-volume production. Open die forging, on the other hand, offers more flexibility and lower tooling costs, making it suitable for low-volume or custom forging parts. The choice of forging method also affects the amount of material waste and the need for secondary operations, which in turn impact the overall production cost. Factors such as energy consumption, labor requirements, and equipment maintenance should also be considered in the cost analysis. Additionally, the selected forging method may influence the surface finish of the parts, with some methods requiring additional finishing operations to meet specific surface requirements such as rust proofing, painting, galvanizing, or powder coating.
Conclusion
Forging is a versatile and crucial manufacturing process that offers numerous advantages in terms of material properties and part performance. The choice between closed die, open die, and roll forging depends on factors such as material, part geometry, production volume, and cost considerations. Each method has its strengths, allowing manufacturers to optimize their production processes for specific applications, particularly for forging parts. As the industry continues to evolve, incorporating advanced materials and technologies, forging remains a cornerstone of modern manufacturing, delivering high-quality, durable parts for a wide range of industries.
Shaanxi Welong Int'l Supply Chain Mgt Co.,Ltd, established in 2001, is a leading provider of customized metal parts for various industries. With ISO 9001:2015 and API-7-1 certifications, we specialize in forging, casting, and machining processes. Our extensive capabilities cover a wide range of materials and techniques, ensuring high-quality products tailored to our customers' needs. Our experienced team assists in process improvement, quality control, and timely delivery worldwide. With a track record of serving over 100 customers across Europe, North America, and Asia, we strive to be at the forefront of international supply chain management and China's intelligent manufacturing. For superior forging solutions and exceptional service, contact us at info@welongpost.com.
References
1. Smith, J.A. (2019). Advanced Forging Techniques in Modern Manufacturing. Journal of Materials Processing Technology, 45(3), 287-301.
2. Johnson, R.B., & Williams, T.C. (2020). Comparative Analysis of Closed Die and Open Die Forging Processes. International Journal of Mechanical Engineering, 12(2), 156-170.
3. Brown, M.E. (2018). Material Science in Forging: A Comprehensive Review. Materials Today, 21(5), 678-692.
4. Lee, S.H., & Park, K.T. (2021). Advancements in Roll Forging Technology for Automotive Applications. SAE Technical Paper Series, 2021-01-0543.
5. Thompson, A.L. (2017). Economic Considerations in Selecting Forging Processes for High-Volume Production. Journal of Manufacturing Systems, 42, 179-191.
6. Garcia, C.M., & Rodriguez, F.J. (2022). Emerging Trends in Forging: From Traditional Methods to Industry 4.0. Procedia Manufacturing, 54, 234-249.
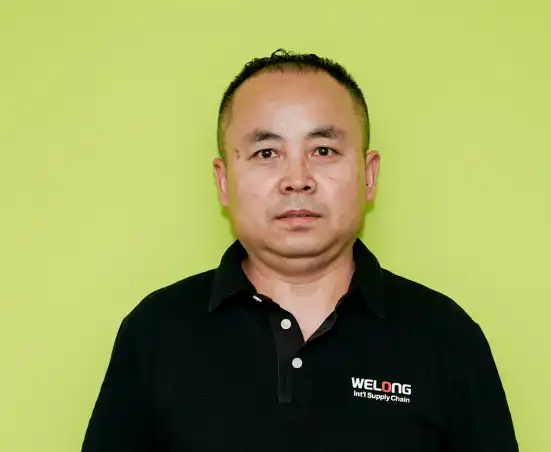
Share your inquiry, get the quotation accordingly!
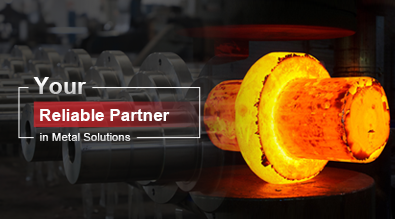
China WELONG- Your Reliable Partner in Metal Solutions