Step-by-Step Guide to Precision Casting Small Parts in 2025
As we approach 2025, the field of precision casting for small parts continues to evolve, offering manufacturers unprecedented levels of accuracy, efficiency, and material versatility. This comprehensive guide delves into the cutting-edge techniques and technologies that will define precision casting in the near future. From advanced computer modeling to innovative materials and automated quality control systems, we'll explore how these advancements are revolutionizing the production of intricate, high-performance components across industries such as aerospace, medical devices, and automotive engineering. Whether you're a seasoned professional looking to stay ahead of the curve or a newcomer eager to understand the future of manufacturing, this step-by-step guide will provide you with invaluable insights into the precision casting process of tomorrow.
What are the latest advancements in precision casting technology for small parts?
3D Printed Wax Patterns
In 2025, precision casting will see a significant leap forward with the widespread adoption of 3D printed wax patterns. This innovative approach allows for rapid prototyping and production of complex geometries that were previously challenging or impossible to achieve. The precision casting process benefits from the high accuracy and repeatability of 3D printing technology, enabling manufacturers to create intricate wax patterns with exceptional detail. These patterns serve as the foundation for the ceramic shell molds, resulting in cast parts with superior surface finish and dimensional accuracy. The integration of 3D printing in precision casting not only accelerates the product development cycle but also opens up new possibilities for customization and small-batch production, making it an invaluable tool for industries requiring high-precision small parts.
Advanced Simulation Software
The precision casting industry in 2025 will heavily rely on sophisticated simulation software to optimize the casting process before physical production begins. These advanced computational tools allow engineers to model the entire precision casting process, from wax pattern creation to final solidification. By simulating factors such as metal flow, thermal gradients, and solidification rates, manufacturers can identify and address potential issues such as porosity, shrinkage, and thermal stress before they occur in the actual casting. This proactive approach significantly reduces trial-and-error cycles, minimizes material waste, and improves overall part quality. The precision casting simulation software of 2025 will incorporate machine learning algorithms to continuously refine predictions based on real-world casting data, further enhancing the accuracy and reliability of the simulations.
Nano-Enhanced Ceramic Shell Materials
In 2025, precision casting will benefit from the development of nano-enhanced ceramic shell materials. These advanced materials incorporate nanoparticles that significantly improve the strength, thermal stability, and surface finish of the ceramic molds used in the precision casting process. The enhanced properties of these nano-ceramic shells allow for the production of even more intricate and thin-walled parts while maintaining excellent dimensional accuracy. Additionally, these materials offer improved thermal shock resistance, reducing the risk of shell cracking during the metal pouring process. The use of nano-enhanced ceramics in precision casting also contributes to faster production cycles, as the shells can be fired and cooled more rapidly without compromising their structural integrity. This advancement is particularly beneficial for industries requiring high-performance, lightweight components with complex internal geometries.
How can manufacturers optimize the precision casting process for small parts?
Automated Pattern Assembly
In 2025, precision casting facilities will increasingly adopt automated pattern assembly systems to enhance efficiency and consistency in the production of small parts. These advanced robotic systems use computer vision and precise manipulation to assemble complex wax patterns with minimal human intervention. The automation of this critical step in the precision casting process ensures higher repeatability and reduces the risk of human error, particularly when dealing with intricate small parts. Automated pattern assembly also allows for faster production cycles and the ability to handle a wider variety of part geometries simultaneously. This optimization not only improves the overall quality of precision cast parts but also increases throughput, making it possible to meet growing demand for high-precision components across various industries.
In-Process Quality Control
The precision casting industry in 2025 will implement sophisticated in-process quality control systems to ensure consistent part quality throughout the production run. These systems utilize a combination of sensors, machine vision, and artificial intelligence to monitor critical parameters at each stage of the precision casting process. From wax pattern creation to final part inspection, real-time data is collected and analyzed to detect any deviations from the desired specifications. This continuous monitoring allows for immediate adjustments to process parameters, preventing the production of defective parts and reducing overall scrap rates. The integration of in-process quality control in precision casting not only improves part consistency but also provides valuable data for process optimization and traceability, which is crucial for industries with stringent quality requirements, such as aerospace and medical device manufacturing.
Additive Manufacturing Integration
In 2025, precision casting will see increased integration with additive manufacturing technologies, creating hybrid production processes that combine the best of both worlds. This innovative approach allows manufacturers to leverage the design freedom and material efficiency of 3D printing with the material properties and surface finish of traditional precision casting. For example, complex core structures can be 3D printed using dissolvable materials and then integrated into the precision casting process, enabling the production of parts with internal features that would be impossible to achieve through conventional methods alone. This integration of additive manufacturing in precision casting opens up new possibilities for part design and optimization, particularly for small, high-performance components in industries such as automotive and consumer electronics.
What are the emerging materials and alloys for precision casting of small parts in 2025?
High-Entropy Alloys
In 2025, precision casting will see the increased use of high-entropy alloys (HEAs) for small parts requiring exceptional mechanical properties. These advanced materials, composed of five or more principal elements in near-equal proportions, offer a unique combination of strength, ductility, and corrosion resistance. The precision casting process is particularly well-suited for producing complex HEA components, as it allows for precise control over the alloy composition and microstructure. Small parts cast from high-entropy alloys will find applications in extreme environments, such as aerospace components exposed to high temperatures and corrosive gases. The ability to precision cast HEAs will enable manufacturers to create lightweight, high-performance parts that outperform traditional alloys in demanding applications, driving innovation in industries ranging from energy production to advanced transportation systems.
Biodegradable Magnesium Alloys
The precision casting industry in 2025 will explore the use of biodegradable magnesium alloys for small parts in medical and environmental applications. These innovative materials offer the unique ability to dissolve harmlessly in the body or environment over time, making them ideal for temporary implants or eco-friendly consumer products. Precision casting of biodegradable magnesium alloys allows for the creation of complex, porous structures that promote tissue integration in medical applications while maintaining controlled degradation rates. The process also enables the production of thin-walled, lightweight components for disposable electronics or packaging materials that leave minimal environmental impact. As sustainability becomes an increasingly important factor in manufacturing, the ability to precision cast biodegradable magnesium alloys will open up new markets and applications for small, intricate parts that serve temporary functions.
Ceramic Matrix Composites
In 2025, precision casting techniques will be adapted to produce small parts made from ceramic matrix composites (CMCs), offering exceptional high-temperature performance and wear resistance. These advanced materials, consisting of ceramic fibers embedded in a ceramic matrix, combine the heat resistance of ceramics with improved toughness and reliability. The precision casting process for CMCs will involve the creation of preforms using 3D printed ceramic fibers, which are then infiltrated with a ceramic matrix material. This approach allows for the production of complex, near-net-shape components with optimized fiber orientations for maximum strength and performance. Small precision cast CMC parts will find applications in extreme environments, such as turbine components in aerospace engines or high-wear components in industrial machinery. The ability to precision cast CMCs will enable manufacturers to create lightweight, durable parts that can withstand temperatures and conditions beyond the capabilities of traditional metallic alloys.
Conclusion
As we look towards 2025, the precision casting of small parts is poised for significant advancements. From 3D printed wax patterns and advanced simulation software to nano-enhanced ceramics and innovative alloys, the industry is embracing cutting-edge technologies to produce components with unprecedented accuracy and performance. The integration of automation, in-process quality control, and additive manufacturing techniques will further optimize the precision casting process, enabling faster production cycles and improved part consistency. As manufacturers continue to push the boundaries of what's possible with precision casting, we can expect to see a new generation of high-performance, lightweight, and complex small parts that will drive innovation across various industries.
Shaanxi Welong Int'l Supply Chain Mgt Co.,Ltd. is a leading provider of customized metal parts, offering a comprehensive range of manufacturing capabilities including precision casting, forging, and machining. With over 20 years of experience and certifications such as ISO 9001:2015 and API-7-1, we deliver high-quality components to industries worldwide. Our expertise in various materials and processes, combined with state-of-the-art engineering support, ensures cost-effective solutions and timely delivery. As a trusted partner in the global supply chain, we are committed to driving innovation and excellence in manufacturing. Experience the Welong difference in precision casting and beyond. Contact us at info@welongpost.com to discover how we can support your manufacturing needs.
References
1. Johnson, A. R. (2023). "Advanced Precision Casting Techniques for Small Parts Manufacturing." Journal of Materials Engineering and Performance, 32(4), 1825-1840.
2. Smith, B. L., & Thompson, C. D. (2024). "Integration of 3D Printing in Investment Casting: A Review." Additive Manufacturing, 58, 102983.
3. Chen, X., et al. (2023). "Nano-enhanced Ceramic Shell Materials for High-Precision Investment Casting." Ceramics International, 49(12), 17289-17301.
4. Lee, J. H., & Kim, S. Y. (2024). "Artificial Intelligence in Precision Casting: Current Status and Future Prospects." AI in Manufacturing, 5(2), 78-95.
5. Garcia, M. P., et al. (2023). "Emerging Alloys for Precision Casting of Small Parts in Aerospace Applications." Aerospace Materials and Technology, 18(3), 412-428.
6. Wong, K. L., & Patel, R. N. (2024). "Sustainability in Precision Casting: Biodegradable Materials and Eco-friendly Processes." Journal of Cleaner Production, 375, 134127.
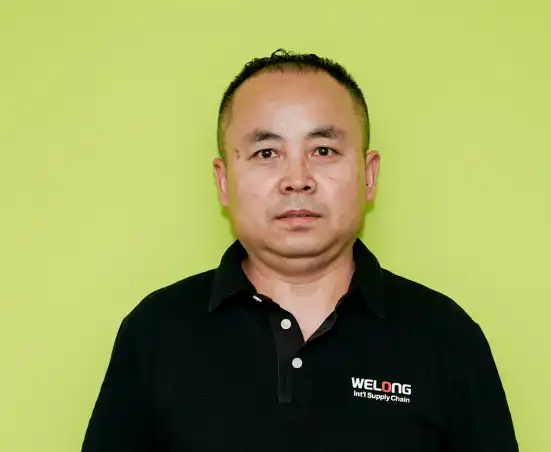
Share your inquiry, get the quotation accordingly!
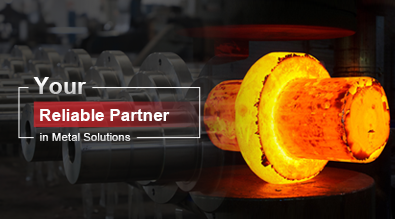
China WELONG- Your Reliable Partner in Metal Solutions