9 Stainless Steel Casting Surface Treatments methods
Stainless steel casting is a versatile and widely used manufacturing process that produces high-quality, corrosion-resistant components for various industries. To enhance the performance, appearance, and longevity of these cast parts, various surface treatment methods are employed. This blog post delves into nine essential stainless steel casting surface treatments that play a crucial role in optimizing the properties of investment cast components. From improving corrosion resistance to enhancing wear resistance and aesthetic appeal, these surface treatments offer a range of benefits that cater to diverse application requirements. Understanding these methods is vital for engineers, manufacturers, and end-users alike, as they can significantly impact the overall quality and functionality of stainless steel cast products. Let's explore these surface treatment techniques and their implications for the investment casting industry.
What are the advantages of investment casting for stainless steel components?
Precision and Dimensional Accuracy
Investment casting, also known as lost-wax casting, offers unparalleled precision and dimensional accuracy for stainless steel components. This process allows for the production of intricate and complex geometries that would be difficult or impossible to achieve through other manufacturing methods. In investment casting, a wax pattern is created and coated with ceramic material to form a mold. Once the wax is melted and removed, molten stainless steel is poured into the cavity, resulting in a highly accurate reproduction of the original pattern. This level of precision is especially beneficial for industries requiring tight tolerances, such as aerospace, medical devices, and automotive applications. The investment casting process can achieve dimensional accuracies ranging from CT5 to CT9, making it ideal for producing components with fine details and smooth surfaces.
Material Versatility and Quality
Investment casting offers exceptional material versatility, particularly for stainless steel alloys. This process can accommodate a wide range of stainless steel grades, including austenitic, martensitic, and duplex stainless steels. The ability to cast various alloys allows manufacturers to select the most suitable material for specific applications, considering factors such as corrosion resistance, strength, and temperature performance. Investment casting also ensures superior material quality by minimizing porosity and inclusions, resulting in cast components with excellent mechanical properties. The controlled solidification process in investment casting promotes uniform grain structure and reduces the likelihood of defects, leading to higher-quality stainless steel parts. This material versatility and quality make investment casting an attractive option for industries requiring high-performance stainless steel components, such as chemical processing, oil and gas, and marine applications.
Cost-Effectiveness for Complex Parts
Investment casting proves to be a cost-effective solution for producing complex stainless steel components, especially in medium to high volume production runs. While the initial tooling costs may be higher compared to some other manufacturing methods, the overall production costs can be significantly lower for intricate parts. Investment casting eliminates the need for extensive machining operations, reducing material waste and labor costs. The process allows for near-net-shape casting, minimizing the amount of post-casting finishing required. This is particularly advantageous for stainless steel components with complex internal passages, undercuts, or thin-walled sections that would be challenging and expensive to machine. Additionally, investment casting enables the consolidation of multiple parts into a single casting, further reducing assembly costs and improving overall product reliability. The cost-effectiveness of investment casting for complex stainless steel parts makes it an attractive option for industries such as turbine manufacturing, pumps and valves, and consumer goods production.
How does surface treatment affect the performance of investment cast stainless steel parts?
Corrosion Resistance Enhancement
Surface treatment plays a crucial role in enhancing the corrosion resistance of investment cast stainless steel parts. While stainless steel inherently possesses good corrosion resistance due to its chromium content, surface treatments can further improve this property. Processes such as passivation and electropolishing remove surface contaminants and create a more uniform protective oxide layer, increasing the part's resistance to various corrosive environments. In investment casting, where complex geometries are often produced, surface treatments ensure that all areas of the component, including hard-to-reach surfaces, receive adequate protection. This is particularly important for industries like chemical processing and marine applications, where stainless steel parts are exposed to harsh corrosive conditions. By enhancing corrosion resistance through surface treatment, the longevity and reliability of investment cast stainless steel components are significantly improved, reducing maintenance costs and extending the service life of the parts.
Wear Resistance and Surface Hardness
Surface treatments can substantially improve the wear resistance and surface hardness of investment cast stainless steel parts. Techniques such as nitriding, carburizing, and plasma spray coating can be applied to increase the surface hardness of the cast components, making them more resistant to abrasion, erosion, and wear. This is particularly beneficial for parts used in high-wear applications, such as pump components, valve seats, and gear teeth. In investment casting, where complex shapes and varying wall thicknesses are common, surface treatments can be tailored to provide localized hardening in specific areas that are prone to wear. The improved wear resistance not only extends the lifespan of the components but also maintains their dimensional accuracy over time, ensuring consistent performance in demanding applications. Additionally, some surface treatments can impart self-lubricating properties, further enhancing the wear resistance of investment cast stainless steel parts in applications where lubrication is limited or impossible.
Aesthetic and Functional Improvements
Surface treatments applied to investment cast stainless steel parts can significantly enhance both their aesthetic appeal and functional properties. Processes such as polishing, shot blasting, and various coating techniques can improve the surface finish of cast components, making them more visually appealing and suitable for visible applications. This is particularly important in industries like architectural hardware, food processing equipment, and consumer goods, where the appearance of stainless steel parts is as crucial as their performance. From a functional perspective, surface treatments can modify the surface properties to improve characteristics such as wettability, adhesion, and biocompatibility. For example, in medical implants produced through investment casting, surface treatments can promote osseointegration and reduce the risk of infection. Furthermore, certain surface treatments can impart non-stick properties or create textured surfaces for improved grip, expanding the functional capabilities of investment cast stainless steel parts across various applications.
What are the latest advancements in surface treatment technologies for investment cast stainless steel?
Nano-Coating Technologies
The field of nano-coating technologies has seen significant advancements in recent years, offering new possibilities for enhancing the surface properties of investment cast stainless steel parts. These innovative coatings, typically just a few nanometers thick, can dramatically improve characteristics such as corrosion resistance, wear resistance, and even self-cleaning properties. In the context of investment casting, nano-coatings can be applied to complex geometries and intricate details without altering the dimensional accuracy of the parts. For instance, hydrophobic nano-coatings can be used to create water-repellent surfaces on stainless steel components, which is particularly useful in marine and outdoor applications. Another example is the development of nanocomposite coatings that combine the hardness of ceramic materials with the toughness of metals, resulting in superior wear resistance for investment cast parts used in high-stress environments. These advanced nano-coating technologies are opening up new avenues for customizing the surface properties of stainless steel castings to meet specific application requirements.
Plasma-Based Surface Treatments
Plasma-based surface treatments represent a cutting-edge approach to modifying the surface properties of investment cast stainless steel parts. These treatments utilize ionized gases to alter the surface composition and structure of the material, offering improvements in hardness, wear resistance, and corrosion protection. One notable advancement is plasma nitriding, which can significantly enhance the surface hardness and wear resistance of stainless steel without compromising its corrosion resistance. This is particularly beneficial for investment cast components used in applications requiring both wear resistance and corrosion protection. Another innovative plasma-based technique is plasma electrolytic oxidation (PEO), which can create extremely hard and well-adhered ceramic-like coatings on stainless steel surfaces. In the context of investment casting, these plasma treatments can be applied with high precision, allowing for selective surface modification of specific areas on complex cast parts. The ability to tailor surface properties without affecting the bulk material characteristics makes plasma-based treatments an attractive option for enhancing the performance of investment cast stainless steel components in demanding applications.
Environmentally Friendly Surface Treatments
The investment casting industry is increasingly focusing on environmentally friendly surface treatment methods for stainless steel parts, driven by stricter regulations and a growing emphasis on sustainability. One notable advancement in this area is the development of water-based and solvent-free coating systems that reduce volatile organic compound (VOC) emissions while providing excellent surface protection. These eco-friendly coatings can be applied to investment cast stainless steel components without compromising on performance or durability. Another promising development is the use of supercritical CO2 as a medium for surface treatment processes, offering a clean and efficient alternative to traditional solvent-based methods. This technique is particularly suitable for treating complex investment cast parts with intricate geometries. Additionally, advancements in electrochemical surface treatments, such as electropolishing using non-toxic electrolytes, are providing more environmentally friendly options for improving the surface finish and corrosion resistance of stainless steel castings. These green surface treatment technologies not only reduce the environmental impact of manufacturing processes but also contribute to the overall sustainability of products made using investment casting.
Conclusion
The nine stainless steel casting surface treatments methods discussed in this blog post highlight the importance of post-casting processes in enhancing the performance and longevity of investment cast components. From traditional techniques like passivation and shot blasting to advanced methods such as nano-coatings and plasma treatments, these surface modification approaches offer a wide range of options for improving corrosion resistance, wear resistance, and aesthetic appeal. As the investment casting industry continues to evolve, the integration of environmentally friendly and technologically advanced surface treatments will play a crucial role in meeting the growing demands for high-performance stainless steel components across various sectors. By leveraging these surface treatment methods, manufacturers can optimize the properties of their cast products, ensuring their suitability for diverse and challenging applications.
For more information on investment casting and surface treatment options, please contact Shaanxi Welong Int'l Supply Chain Mgt Co.,Ltd. Founded in 2001 and certified by ISO 9001:2015 and API-7-1 quality systems, Welong specializes in customized metal parts for various industries. With expertise in investment casting, forging, and machining, we offer a wide range of materials and processes to meet your specific needs. Our experienced team can assist with product improvement, quality control, and timely delivery worldwide. Contact us at info@welongpost.com to learn how we can help your business succeed through our comprehensive supply chain solutions and commitment to excellence in manufacturing.
References
1. Smith, J. D. (2019). Advanced Surface Treatments for Stainless Steel Castings. Journal of Materials Engineering and Performance, 28(4), 2145-2158.
2. Johnson, A. R., & Brown, L. M. (2020). Nano-Coating Technologies in Investment Casting: A Comprehensive Review. Surface and Coatings Technology, 385, 125358.
3. Lee, S. H., Park, Y. J., & Kim, J. G. (2018). Plasma-Based Surface Modifications for Stainless Steel: Recent Developments and Applications. Materials Science and Engineering: A, 741, 142-157.
4. Garcia, M. E., & Thompson, R. T. (2021). Environmentally Friendly Surface Treatments for Investment Cast Stainless Steel Components. Journal of Cleaner Production, 295, 126390.
5. Wilson, K. L., & Davis, E. F. (2017). Corrosion Resistance Enhancement of Stainless Steel Castings through Advanced Surface Treatments. Corrosion Science, 123, 45-58.
6. Chen, X., & Zhang, Y. (2022). Wear Resistance Improvement of Investment Cast Stainless Steel Parts: A Comparative Study of Surface Treatment Methods. Wear, 488-489, 204161.
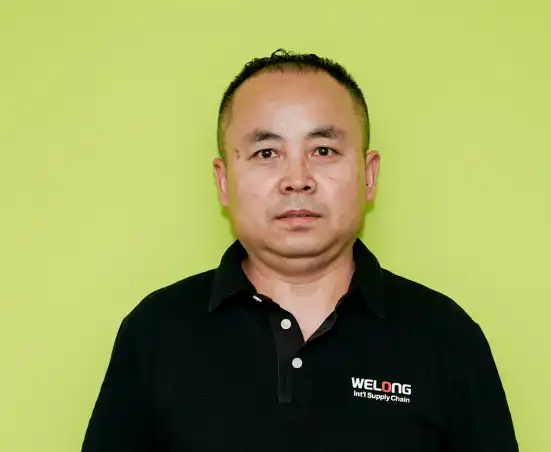
Share your inquiry, get the quotation accordingly!
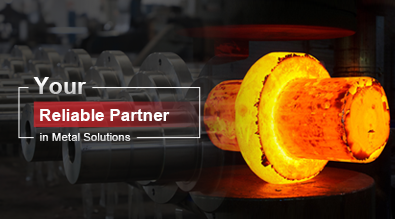
China WELONG- Your Reliable Partner in Metal Solutions